The U.S. Army Engineer Research and Development Center (ERDC), in collaboration with the University of Nevada, Reno and NASA, is advancing the field of additive construction (AC) through the development of “LEGO-like” 3D-printed concrete bricks. These modules are designed to be rapidly fabricated and assembled in the field, potentially transforming military infrastructure projects by enabling faster, more efficient construction in remote and conflict-prone areas.
This effort is part of the Automated Construction of Expeditionary Structures (ACES) program, which focuses on providing deployable 3D printing solutions for military operations. Using movable printers equipped with a printhead on a truss-based system, these printers can produce durable infrastructure components from locally sourced materials. The machines are compact enough to be transported within standard shipping containers and can be set up within hours, reducing the logistical burden on forward-operating bases.
In recent tests, the ERDC successfully constructed a small bridge using seven modular concrete segments, each printed and assembled on-site with post-tensioned cables. This achievement builds on earlier milestones, such as the 3D printing of a reinforced concrete bridge in 2019. At the time, the process required six days for assembly; now, structures of similar complexity can be completed in just one day. Professor Sherif Elfass, who oversees the project, highlighted how numerical modeling integrated with 3D printing optimizes the design and placement of segments, ensuring structural integrity under diverse conditions.
The potential applications extend beyond bridges. The U.S. Army Corps of Engineers envisions using this technology to construct barracks, barriers, culverts, vaults, and other critical structures. A notable example of this versatility was a barracks hut 3D-printed in 2017, which cut material needs by half and reduced manpower requirements by 62% compared to traditional plywood construction. These efficiencies align with the military’s broader goals of modernizing construction processes to address challenges such as material scarcity, labor shortages, and rising costs.
Earlier this year, 3DPrint.com spoke with Megan Kreiger, Portfolio Manager for AC at ERDC and a central figure in the development of AC technologies. Under her leadership, ERDC has pursued designs that prioritize field readiness and reliability. For instance, ACES printers avoid precision rails in favor of simpler, chain-and-sprocket mechanisms that are easier to repair with widely available parts. This approach ensures that printers remain operational in austere environments where access to spare parts and specialized tools is limited.
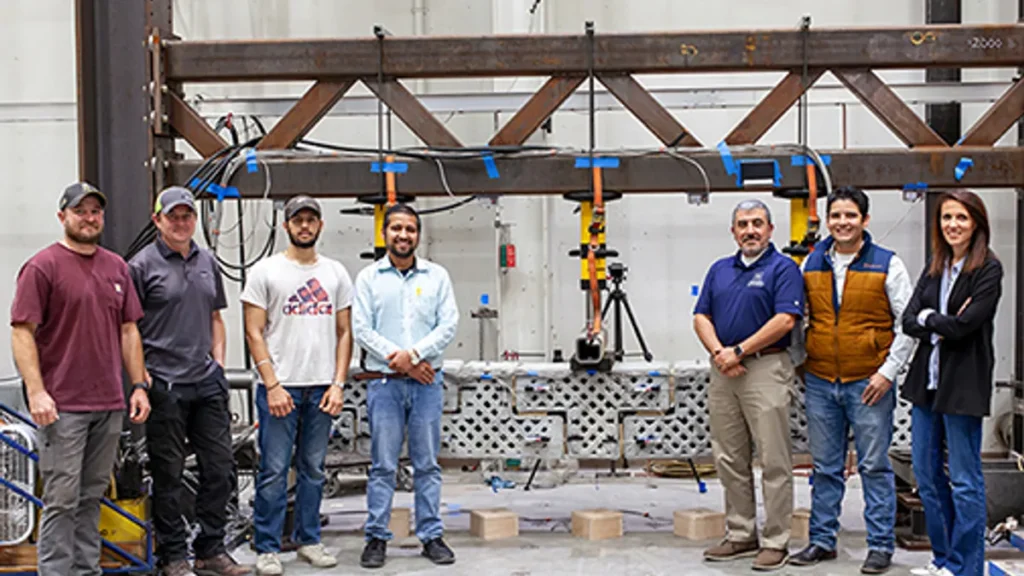
The research team testing 3D-printed bridge structures is (left to right), Todd Lyttle; Chad Lyttle; student researcher Saransh Beniwal; postdoctoral researcher Satish Paudel; Research Associate Professor Sherif Elfass; undergraduate researcher Allen Rivas; and team lead, Assistant Professor Floriana Petrone.
The ability to utilize local materials represents another significant advantage. For example, during a project in Guam, ERDC teams quickly adapted concrete mixtures using locally sourced aggregates, demonstrating the adaptability of the technology to varied geographies. This capability reduces the logistical challenges of transporting construction materials to remote locations, further enhancing the strategic value of AC. The dual-use nature of this research underscores its significance. While the immediate focus remains on military readiness, the broader adoption of AC technologies could pave the way for sustainable and cost-effective solutions to global infrastructure needs.
Subscribe to Our Email Newsletter
Stay up-to-date on all the latest news from the 3D printing industry and receive information and offers from third party vendors.
Print Services
Upload your 3D Models and get them printed quickly and efficiently.
You May Also Like
Metal Powder Supplier Elementum 3D Added to $46B Air Force Contract
Elementum 3D, a Colorado-based developer and supplier of metal powders used in additive manufacturing (AM), announced that the company has been added to the vendors list in the fourth on-ramp...
Ursa Major Lands $28.6M AFRL Deal for 3D Printed Draper Engine Flight Demo
The US Air Force Research Laboratory’s (AFRL’s) Rocket Propulsion Division at Edwards Air Force Base has awarded a $28.6 million contract to Ursa Major for follow-on work related to the...
3D Printing Financials: Rocket Lab’s Record-Breaking Year and Over 20 Launches Coming in 2025
Rocket Lab (Nasdaq: RKLB) closed 2024 with its best year yet. The company launched more rockets, signed more contracts, and expanded deeper into spacecraft and satellite production than ever before....
US Air Force Taps Beehive to Study 3D Printed Jet Engines
Propulsion 3D printing firm Beehive Industries secured a contract from the U.S. Air Force Life Cycle Management Center through SOSSEC. SOSSEC is a company that manages Other Transactions Authority (OTA)...