The collision repair industry is at the cusp of a revolution, with one of the most exciting developments being the advent of 3D printing technology. Additive manufacturing (AM) can assist in increasing the volume, reducing the cost, and shortening the cycle time of repairs.
This innovative approach to producing auto repair parts is transforming the landscape of automotive repairs and customization. As companies specialize in producing high-quality, OEM-compatible repair parts using sophisticated digital supply chains, the future of automotive repairs looks promising. Among the parts possible with 3D printing are tabs, made from the same material of such parts as headlight bases and capable of replacing missing or broken headlight tabs that form the entire frame of the base and can’t be bought separately.
However, this bright future brings with it the need for a crucial development: the establishment of industry-wide standards for 3D-printed parts and materials used in the collision repair process.
The necessity for standardization primarily stems from the need to ensure the quality and compatibility of 3D printed parts. In the absence of such standards, there is a significant risk of variability in part quality, which can lead to safety concerns and compatibility issues with existing automotive systems. Standardizing the production process and material quality would ensure that all 3D printed parts meet the stringent requirements of the automotive industry, similar to those expected from traditional manufacturing methods.
Another critical aspect is consumer safety and confidence. The automotive industry is inherently linked to the safety of its end-users. Vehicles repaired with subpar or untested parts pose a significant risk. Standardized regulations would ensure that all 3D printed parts undergo rigorous testing and quality control, similar to their traditionally manufactured counterparts. This would not only safeguard the users but also bolster consumer confidence in using 3D printed parts for repairs, including specific components like headlight tabs.
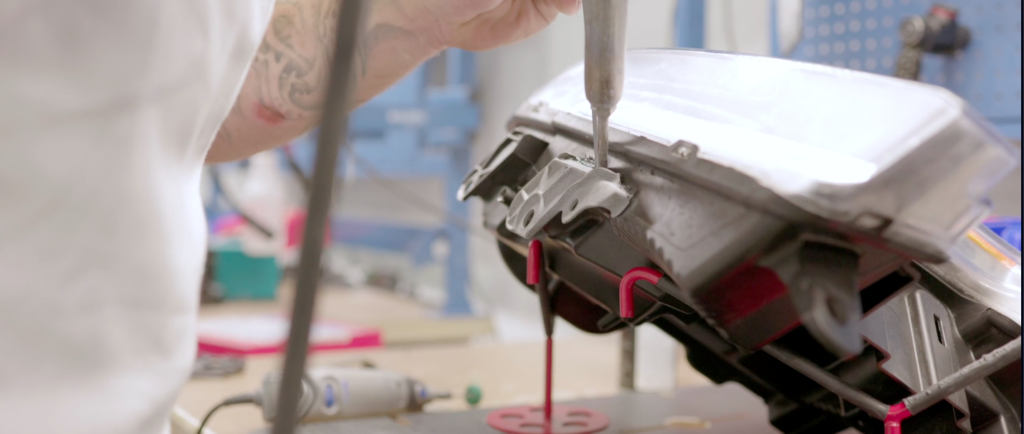
3D printed headlight tabs.
Having standards also reduces the risk of unethical operators using low-grade printers and materials to print automotive collision parts sold as standalone or used in the repair of a damaged part such as a headlight. This creates unknown risks to the collision shop, who may unknowingly purchase these poor-quality 3D printed components. These substandard parts are set to fail, causing added costs to the entire supply chain of the claim, from the insurers, the OEM to the collision shop, and frustrating the customer.
The urgency of standards and compliance in the auto repair industry, with the need to meet OEM compatibility, is such that it will be left to 3D printing providers from the industry to promote their work and products that comply to some level of standardization providing the industry and its customer being repair shops or part reconditioners the confidence and assurance needed.
Far from stifling innovation, standards can provide a structured framework within which creative and technological advancements can thrive. This structured approach to innovation ensures that new developments in 3D printing are both groundbreaking and safe, fostering growth while maintaining high industry standards.
Environmental sustainability is another area where standardization can have a profound impact. 3D printing offers a more eco-friendly approach to part manufacturing, potentially leading to more repairs rather than replacements with new parts. With reduced waste production and lower carbon emissions, standardizing the materials and methods used can ensure that these environmental benefits are consistently achieved across all 3D printed products.
As the collision repair industry continues to embrace 3D printing technology, the establishment of comprehensive standards for parts and materials is not just beneficial but essential. These standards will guarantee quality, ensure safety, facilitate regulatory compliance, encourage innovation, streamline the supply chain, and maximize environmental benefits. As the industry evolves, the implementation of such standards will be key to safeguarding the interests of all stakeholders, from manufacturers to end consumers, paving the way for a safer, more efficient, and sustainable future in automotive repairs
Subscribe to Our Email Newsletter
Stay up-to-date on all the latest news from the 3D printing industry and receive information and offers from third party vendors.
Print Services
Upload your 3D Models and get them printed quickly and efficiently.
You May Also Like
U.S. Navy Lab Uses 3D Printing to Reduce Tooling Lead Time By Over 90%
The F-35 Lightning II Joint Program Office (JPO), responsible for life-cycle management of the key fifth-generation joint strike fighter (JSF) system used by the U.S., its allies, and its partners,...
Etsy Design Rule Change Reduces Selection of 3D Printed Goods
Online marketplace Etsy has implemented a rule change requiring all 3D printed goods on the site to be original designs. The update to the site’s Creativity Standards states, ¨Items produced using...
Honeywell Qualifies 6K Additive’s Nickel 718 for 3D Printed Aerospace & Defense Parts
6K Additive is renowned for manufacturing sustainable additive manufacturing (AM) powder, and offers a wide portfolio of premium metal and alloy powders that include titanium, copper, stainless steel, and nickel,...
MetalWorm Sells WAAM Systems to Research Institutes in Brazil and Malaysia
Turkish WAAM firm MetalWorm has sold a system in Malaysia and another in Brazil. This is an excellent example of a few emerging trends in additive. Firstly, WAAM was experimented...