In the spring of 2023, one of the world’s only organizations dedicated to the auto collision repair industry, the International Bodyshop Industry Symposium (IBIS) Worldwide, launched a project called the 3D Printing in Auto Repair Task Force. Although initiatives like this seem to be launched on a weekly basis these days, when I posted about the group’s formation back in May, I was struck by the organization’s highly influential list of participants, as well as the breadth of experience that was put together.
The panel was established in order to create consensus on the most urgent issues surrounding 3D printed auto spares, from all relevant areas of the collision industry supply chain. As such, the industry experts involved ranged from auto giants to major additive manufacturing (AM) original equipment manufacturers (OEMs) to auto parts recyclers.
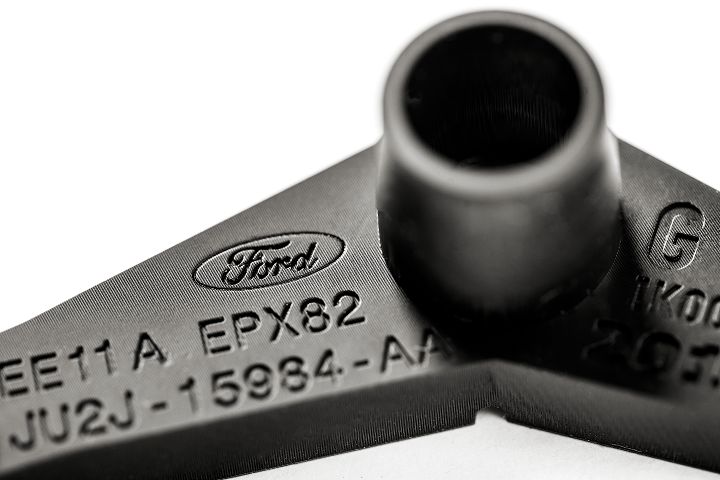
In October 2023, the 3D Printing in Auto Repair Task Force issued its final report, but, as that report explained, the plan is for the task force’s findings to serve as a jumping-off point for the creation of a more permanent body. The head of the 3D Printing in Auto Repair Task Force, Harold Sears — formerly the head of AM at Ford Motor Company — explained to me what form the organization may take in the near future, and filled me in on what his work on the task force taught him about the landscape for 3D printed auto spares.
“I was involved with 3D printing for 29 years of my 32 years at Ford,” Sears began. “I think that experience gives me an appreciation of the quality requirements for the auto industry, an appreciation of the testing and validation that auto components have to go through, and the need for them to sustain their quality and integrity. And that means integrity over time, too — it’s not just a matter of a part being printed and it passes its initial test. Once it’s on the vehicle, you have to keep track of how the part stands up to years of exposure to the environment and regular wear.”
Along those lines, one of the key purposes of the task force was to ensure that the experts involved were as up-to-date as possible on the latest activities driving the use of AM in auto repair globally:
As the final report notes, “Our findings were derived from referrals, personal dialogues, media sources, conference engagements, and meticulous physical inspections of parts. Additionally, we procured components from various outlets, including online platforms and industry suppliers. Furthermore, our task force visited prominent entities such as IBIS Global, HP’s Barcelona Facility, Thatcham Research, ADAC Automotive, Carhart Products, Boyd Group, and I-CAR, where we gleaned invaluable insights and explored potential collaborations to advance our objectives.”
Image courtesy of 3D Printing in Auto Repair Task Force
Sears noted that he was more than a little concerned by the (lack of) quality of the parts the task force ordered online. The most critical thing to keep in mind is the inherent difference between 3D printed parts certified by auto giants and legitimate suppliers, and the anonymous spares that anyone with internet access can purchase:
“When you’re the OEM and you’re printing these parts, you know they were designed to be 3D printed, and you know that they’re going to be designed to meet the certain specifications that the application requires, etc. When you come at it from the angle of automotive repair, then, you have to be very mindful that many of the parts you’re trying to replace likely weren’t originally designed to be 3D printed. So, we have to meet the quality standards that the part was originally designed for, but we also can’t make the parts better than that — certainly, we can’t be worse, but in some cases, being “better” may be just as bad as being worse. Some parts are designed to break and yield at a certain point, so having a part that’s stronger may put the driver in a compromising situation. You really have to understand the original intent of the part before you can even consider whether to 3D print it, or not.”
And, while the problem of 3D printed parts that are too technically sound is certainly interesting to keep in mind down the road, Sears pointed out that, for the most part, the 3D printed spares the task force procured online were well below standard:
“I have some concerns when it comes to these substandard parts. For one thing, some of the parts we bought, we didn’t even know they were 3D printed until we got them. Then, when we received them, it was obvious that they were. As for the ones that we knew were 3D printed, the overwhelmingly poor quality reflects negatively on the auto industry in a variety of ways. First, it just reflects negatively on 3D printing. Second, it can reflect poorly on the OEM. I found some folks giving me comments like, ‘I had X brand of vehicle and I’ve had to repair it four times, I’m never going to buy one of these again.’ And it may have nothing to do with the OEM, but it affects the customer’s perception, anyway.”
This is where the next phase of the 3D Printing in Auto Repair Task Force comes in. In order to provide the sort of assurances Sears correctly argues are non-negotiable, a certification authority needs to be in place. Whether it’s private, public, or — as is most likely, in my opinion — a public-private hybrid, an institution needs to exist that has the expertise, legitimacy, and power to qualify the platforms and processes involved in 3D printing safe and reliable spare parts for the auto industry.
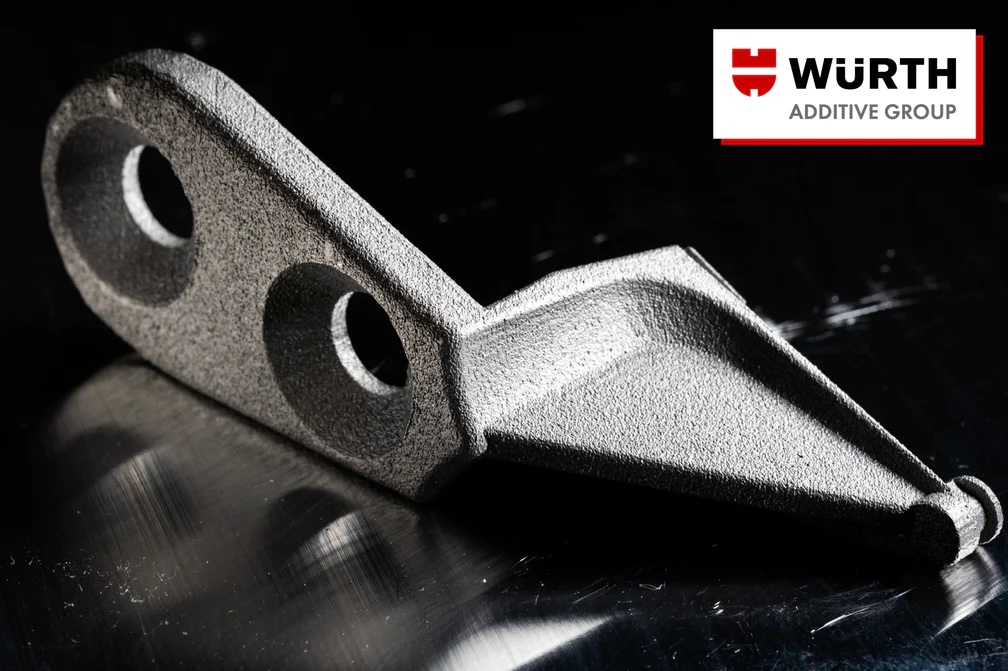
Those involved in the 3D Printing in Auto Repair Task Force not only have the advantage of having had a head start, but just as significantly, are already precisely the individuals who anyone starting a similar project would need to have input from in order to be successful at the task at-hand. One of the biggest tasks, for instance, will be how to best achieve digital quality control.
“Something that we’re talking about as we move this task force forward to its next phase is how do we go about doing that?” Sears said. “How do we certify and validate parts as 3D printable — and then, not only that they’re 3D printable, but how do we determine the best platforms and materials for each specific part? What’s ‘good enough,’ and who is deciding what’s good enough? I think the ability to digitally control that certification, and the distribution of the part file, is critical. And I think the technologies are there today — through blockchain, for example — that can allow us to control and license validated parts and processes. There are still going to be people who counterfeit parts, but the hope is that we can build some mechanism to where, if you put the counterfeit part next to the real certified part, trained professionals can tell the difference.”
Again, the key to building up the capacity to do that will depend upon the strength of the standards organization that emerges to qualify and deliver the relevant solutions.
“I would say the task force as we knew it and announced it has done its job. We’ve researched 3D printing’s role in the collision repair industry, we’ve identified many key issues, and we produced the final report — all of that was, in itself, quite an undertaking. Now, we’re in the early stages of putting together what will be more of a regulation or authority body, which can work with the 3D printing companies, companies in the relevant supply chains, and other related groups that are all connected to this collision repair industry to put the right processes in place and establish the necessary standards so the potential of AM can be opened up to the industry. I’m working right now to try to put the right team together that can establish this authority, for the best interest of both the 3D printing and collision repair industries,” Sears said.
“This is another not so easy task. Many people want to be involved, and that’s great, but maybe they aren’t always the right people to be involved. When you do something like this, it won’t be effective if it’s a group of 500 people. To pick the right group, it has to be the right size to be able to consider input, make decisions, and move things forward without constant arguing and months of not making any progress. So, that’s what we’re looking at right now, is putting the right team together to move us into the next phase.”
As I mentioned in a post about the potential for AM-centric digital supply chains to be deployed for quality control in the aerospace sector, the work of the 3D Printing in Auto Repair Task Force could align in many ways with the interests of other strategic sectors, including defense. As Sears aptly noted, it’s not easy to get the right people together, and that can be all the more difficult when trying to find consensus across the world’s most complex sectors. On the other hand, when the right problem comes along, it can be precisely the impetus necessary to spark new and unexpected collaborations.
Attendees of Additive Manufacturing Strategies (AMS) in New York City (February 6-8, 2024) can see 3D Printing in Auto Repair Task Force member Mario Dimovski speak on the AM for Mobility Panel.
Subscribe to Our Email Newsletter
Stay up-to-date on all the latest news from the 3D printing industry and receive information and offers from third party vendors.
Print Services
Upload your 3D Models and get them printed quickly and efficiently.
You May Also Like
3D Printing News Briefs, July 2, 2025: Copper Alloys, Defense Manufacturing, & More
We’re starting off with metals in today’s 3D Printing News Briefs, as Farsoon has unveiled a large-scale AM solution for copper alloys, and Meltio used its wire-laser metal solution to...
3DPOD 260: John Hart on VulcanForms, MIT, Desktop Metal and More
John Hart is a Professor at MIT; he´s also the director of the Laboratory for Manufacturing and Productivity as well as the director of the Center for Advanced Production Technologies....
3D Printing News Briefs, June 28, 2025: Defense Accelerator, Surgical Models, & More
In this weekend’s 3D Printing News Briefs, 3YOURMIND was selected to join an EU Defense Accelerator, and PTC has announced model-based definition (MBD) capabilities within Onshape. Finally, a study out...
EOS in India: AM’s Rising Star
EOS is doubling down on India. With a growing base of aerospace startups, new government policies, and a massive engineering workforce, India is quickly becoming one of the most important...