Professor Christopher Tuck works at Nottingham University’s Centre for Additive Manufacturing. Unlike many researchers who focus on a single technology or specialize in mechanical engineering, Chris’s research is very diverse. He is interested in enabling additive technologies to flourish and be industrialized. His work encompasses binder jetting materials, inkjet, powder bed fusion (LPBF), polymers, metals, reducing the porosity of aluminum, mechanical properties of Ti64, manufacturing medicine through inkjet, and printing conductive components.
Through his work at contract 3D printing research firm Added Scientific and PU industrialization firm Reactive Fusion, he also engages in practical manufacturing projects. Active in ASTM F42 and the BSI on standards, Chris’s mission is to make 3D printing effective in manufacturing. We interviewed Chris about his mission at Nottingham.
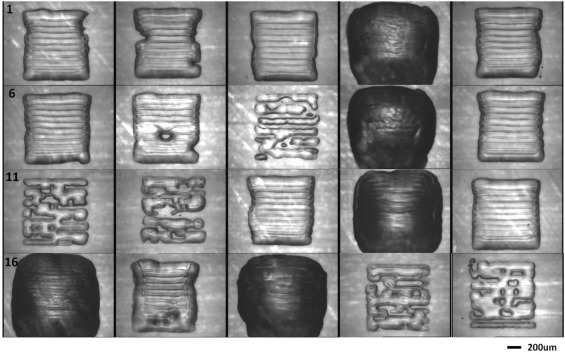
Experiments in material jetting simulation.
Our talk with Chris begins with standards. Chris discusses the importance of defining terminology, details, and further standards in medical and aerospace as significant milestones. He points out that the coordination of ASTM and ISO has expedited this process. However, he acknowledges that standards work is never done, especially in new applications.
We also discussed binder jet technology. With the recent hype, is it justified? Chris believes the technology has real scalability and can be cost-effective. He thinks more effort is needed to find the correct applications and niches to truly displace mainstream technologies at high volumes.
LPBF is also increasingly in the spotlight. Chris thinks that rather than focusing on adding more lasers, attention should be given to the productive rate of the technology. Control of melt pools and cooling are areas where he believes increased attention will lead to more repeatable production. He emphasizes the importance of mapping builds, finding failure modes, and reducing scrap rates. He is encouraged by developments in faster recoating as a practical path forward.
Lately Chris has been doing a lot of work on inkjet. Could that be a potential source of future AM technologies?
“Inkjet is the answer on several fronts, firstly, precision, second only to Vat polymerization, inkjet offers both precise droplet placements and small voxel size that if controlled can produce highly accurate and repeatable parts. Secondly, inkjet technology is inherently scalable in production, more heads equal more material laydown and we see the use of inkjet in other industries (ceramic tiles and printed electronics for example) where this scalability is exploited for mass manufacture. Finally, materials, anyone who has worked with inkjet knows that the viscosity limitations of inkjet printing heads have held back the performance of materials in these technologies, however with the advent of new heads, higher viscosity is becoming a real option, and this means the functionality of the materials and overall properties will get better. Given this, the ability to make truly multimaterial and multifunctional parts is becoming a reality. What’s still needed though is a system that people can access, modify, and develop.”
But inkjet is no panacea. Chris thinks that it is too difficult to develop new inkjet technologies at the moment. True democratization is currently difficult because the technologies are not easily accessible. Knowledge and access are restricted. Chris is focused on making multi-material parts using inkjet and other technologies. This approach has the potential to create truly revolutionary parts.
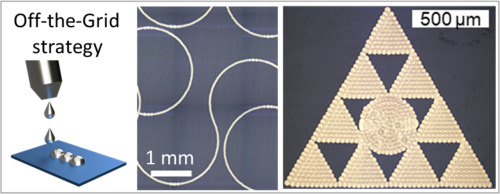
A better way to inkjet.
What about combinations of different technologies working together? It has been tried before but interest seems low in these types of combinations.
“I’m not sure to be honest, there is a lot to be said for combining technologies, for example we have recently developed a combined LPBF and Inkjet technology to modify material composition in metallic L-PBF. However, the fundamental thing is what do the different technologies offer to the final part should they be combined and how difficult the combination actually is? FDM and inkjet for example have similar deposition mechanisms, whereas Vat Polymerization and FDM may well be possible but where’s the added value? One way to think about this is that almost all the different processes have advantages either in material type or in scale up, and so taking advantage of those specific elements could be a driver, which is likely to be driven by product specific considerations.”
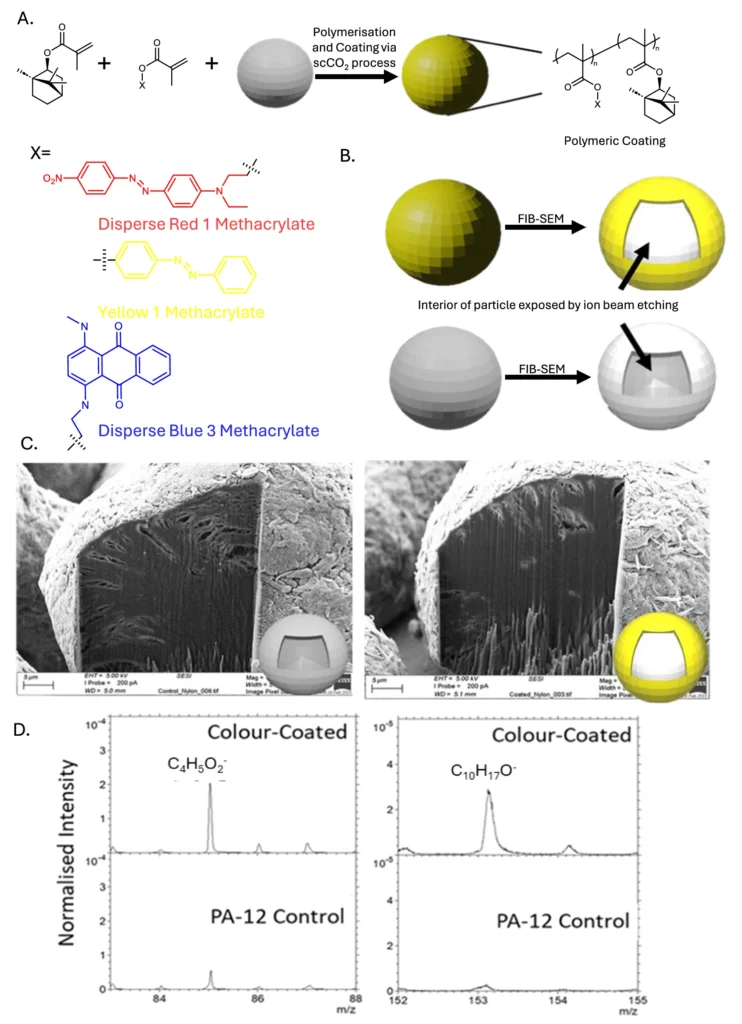
Coloring PBF parts.
That’s a good point. It’s not about the technology or whatever whizz-bang thing we’ve come up with. Chris is looking specifically for where these technologies would actually work. Product-specific and application-specific thinking will drive new adoptions, not just the inventions we make. This approach is far better than trying to shoehorn businesses and parts into predefined boxes. Specifically enhanced technologies and industrialized applications are where we can find real value for customers and the wider world.
Subscribe to Our Email Newsletter
Stay up-to-date on all the latest news from the 3D printing industry and receive information and offers from third party vendors.
Print Services
Upload your 3D Models and get them printed quickly and efficiently.
You May Also Like
Making 3D Printing Personal: How Faraz Faruqi Is Rethinking Digital Design at MIT CSAIL
What if your 3D printer could think more like an intelligent assistant, able to reason through a design idea, ask questions, and deliver something that works exactly the way the...
Reinventing Reindustrialization: Why NAVWAR Project Manager Spencer Koroly Invented a Made-in-America 3D Printer
It has become virtually impossible to regularly follow additive manufacturing (AM) industry news and not stumble across the term “defense industrial base” (DIB), a concept encompassing all the many diverse...
Heating Up: 3D Systems’ Scott Green Discusses 3D Printing’s Potential in the Data Center Industry
The relentless rise of NVIDIA, the steadily increasing pledges of major private and public investments in national infrastructure projects around the world, and the general cultural obsession with AI have...
Formlabs Teams Up with DMG MORI in Japan
In late June, Nick Graham, Chief Revenue Officer at Formlabs, announced on LinkedIn that the company had partnered with DMG MORI, one of the world’s leading machine tool companies, to...