The famous rock ballad by the Scorpions, Winds of Change is my inspiration. I would change it to the “Gas Path of Change” but then that is really hard to lyricize to. We can rock out (and whistle) the intro together in person as I will be at the upcoming Additive Manufacturing Strategies in NYC where The Barnes Global Advisors is a sponsor this year. I will be moderating the panel on “Metals in AM” on behalf of Metal Powder Works. The panelists are Chris Eonta from Molyworks, Jamie Perozzi from 6K Additive, and Samantha Welch from Joby Aviation. We will explore where we are in powder production but also the requirements for powders where Sam will keep us all honest by representing the user and the originator of the requirements.
Our understanding of powders in AM is in its infancy. Today, we have one standard for characterizing powder, the Hall Flow, and most manufacturers treat it as a data point, not a pass or fail. We describe roundness as a binary – spherical or non-spherical when in reality, it is a continuum. AM powder bed system moves powder fine if you only need to cover a 250 mm2 surface, but it is not scalable. Imagine trying to plow a mound of powder big enough to cover a 1 m2 bed?!
Going from the macro sense down into the granular (pun intended) our understanding of powder particles, populations, and processing effects is still being studied at universities. As my oldest daughter started college this year, I made an analogy that made sense to me (figure 1).
When you meet a new person, they have a characteristic, just like a powder particle. The particle may be big or small, have satellites, or be 0.87 sphericity. A boy she meets may wear a ball cap, have cool clothes, and tell funny jokes.
When the same person is with a group of colleagues, their behavior likely changes to accommodate the population just as their presence alters the behavior of the population. With powder particles, small particles or fines can dominate the movement of the population.
Finally, those of us in AM often forget to look at the last piece – the process. We spend inordinate amounts of time getting powder into the bed, but the process imparts a force on the population. Truly ‘high flowing’ powder will then migrate away as the binder or laser (i.e. the process) in what we have seen as denudation or ballistic impact to the surface. Imagine the influence of the introduction of alcohol on our population of college students, changing their collective behavior together.
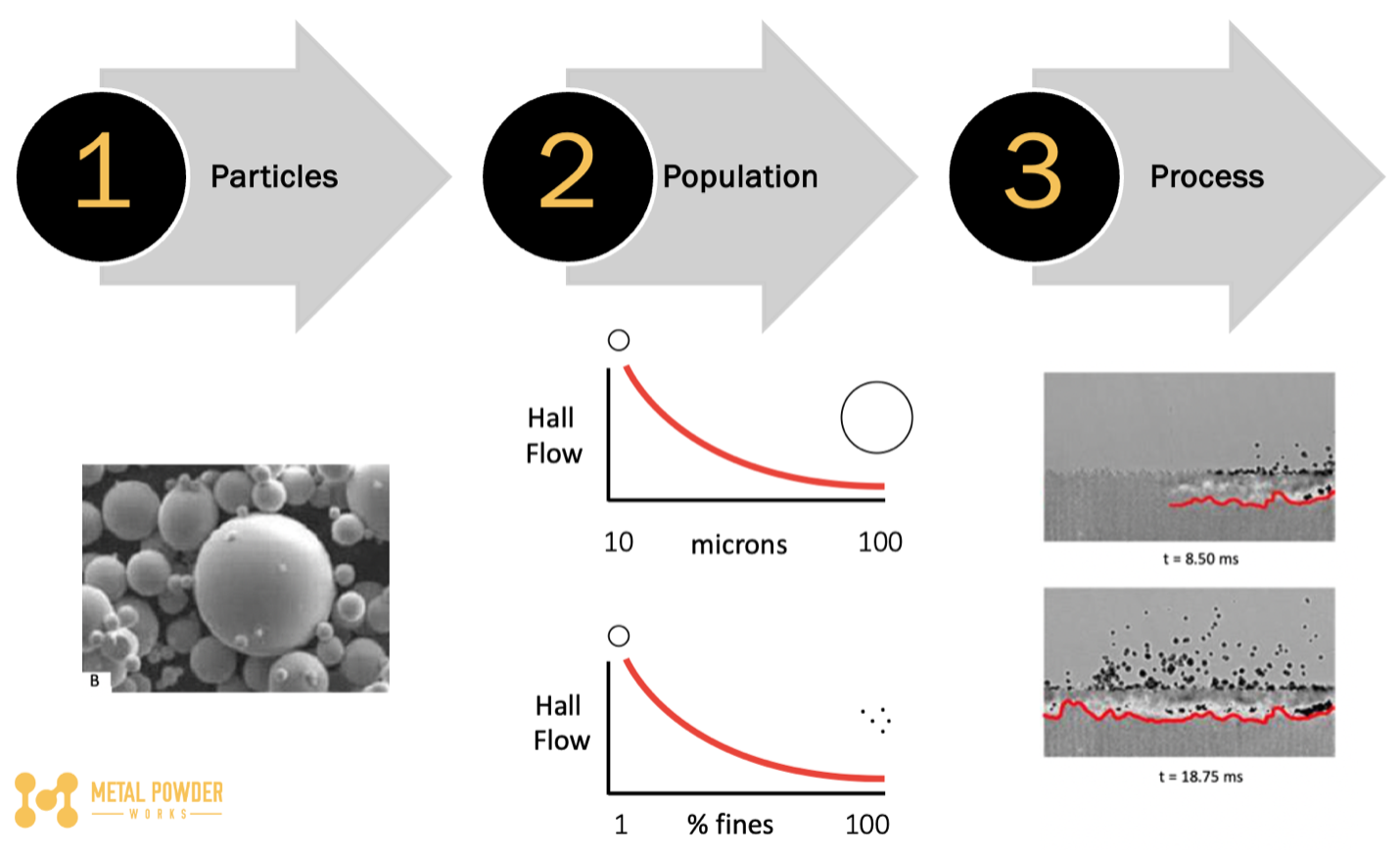
Figure 1.
We’re still in the early days of thinking about powders and the various AM processes. Our graphic (figure 2) shows the different requirements for powders by the various AM processes.
One steady comment that has come from my peers and colleagues in the manufacturing space is the need for consistency. 6K did a survey over the last year, and the need for consistency (and quality, which are essentially the same) is the biggest.
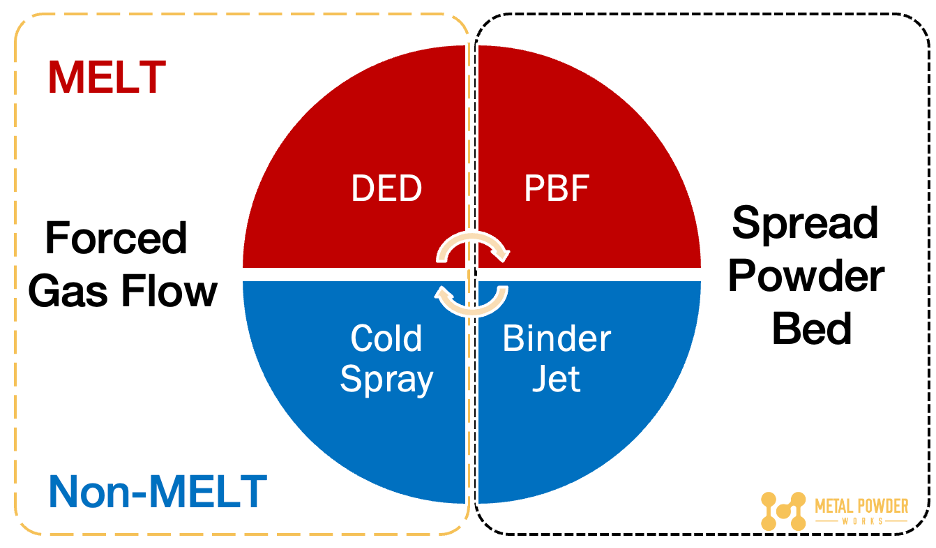
Figure 2.
Lastly, let’s be conscious of how we got here and the macroeconomics. Virtually all AM powders are gas or plasma atomized which yields a ‘rounder’ particle than water atomization but neither is very consistent. Water atomization makes up almost 95% of global powder production – it is more useful for making powders for the manufacturing processes that use it. Atomization does not have to be the only method for making AM powders, especially when you consider the range of requirements from being melted, to sintered, and/or deformed. The next time you get together with a population of your friends consider this: How will AM grow when it uses only 5% of global production capacity?
John Barnes, Founder of The Barnes Global Advisors and CEO of Metal Powder Works, will be participating at the upcoming Additive Manufacturing Strategies business summit in New York, February 6 to 8, 2024. Barnes will be moderating a panel on “Metals in AM” on behalf of Metal Powder Works. The Barnes Global Advisors will be hosting a workshop titled “Finding the Value in AM” on the third day of the event, as well.
Subscribe to Our Email Newsletter
Stay up-to-date on all the latest news from the 3D printing industry and receive information and offers from third party vendors.
You May Also Like
Model No. Deploys Titan Pellet 3D Printers for Sustainable Furniture Production
Over the years, many designers have tried to create 3D printed polymer furniture. Early pioneers like Janne Kyttanen, Materialise’s MGX, and Joris Laarman have led the way with 3D printed...
3D Printing News Unpeeled: Recycling PLA, More Efficient Atomizing
Filamentive hopes to recycle your PLA if you’re in the UK and order over £500 worth of filament. Their partner 3D Printing Waste (3DPW) will turn the PLA into injection...
Lighting the Way with Potato Starch: Sustainable Polish ECO Lamps Use 3D Printing
Lighting that meets the essence of nature: this is the reality brought to life by ECO Lamps, which introduces a fresh perspective to sustainable lighting design using potato starch. These...
3D Printing News Unpeeled: 3D Printed Construction Standard, Sand Wall & Self Heating Microfluidics
ISO/ASTM Standard 52939:2023 has been released and it sets standards for QA for 3D Printed polymer, composite and cement buildings. This is most welcome since 3D printed construction is a...