Inkbit, the Massachusetts-based original equipment manufacturer (OEM) of the Vista line of 3D printers, has launched a new material offering, TEPU 50A, at Formnext 2023 (November 7-10 in Frankfurt, Germany). Vista 3D printers leverage Inkbit’s multi-material and intelligent Vision Control Jetting (VCJ) technology. TEPU 50A, a thiol-ene polyurethane-based elastomer, is the second elastomer in Inkbit’s portfolio, after TEPU 30A (Vulcan Soft Elastomer 30). The selling point of TEPU 50A is that it is medium-soft, which enables customers to achieve highly functional prototyping for rubber-like components.
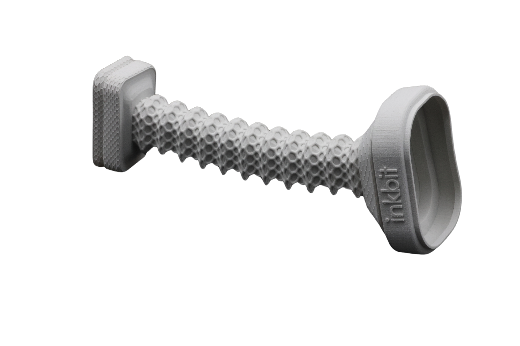
As Inkbit’s CEO, Davide Marini, told me in an interview about the product launch, TEPU 50A was specifically created to align with Inkbit’s users’ needs:
“We listened to customer feedback,” Marini said. “We had launched our first, 30A version of the material, which was met with a tremendous amount of enthusiasm. For the first time, it was possible to combine the rebound properties of an elastomer with very high resolution, fine features. But many of our customers remarked that the material would be even better if it were a little bit harder, so that’s what led us to develop TEPU 50A. One of the applications where we’ve seen a strong attraction is prototyping for automotive gaskets — there’s a very strong market pull here. Another area is the field of soft robotics, where customers are developing all sorts of grippers. An important point to emphasize is that our platform is a multi-material technology. So, when TEPU 50A is combined with a more rigid version, it lends itself to a number of applications for robotic grippers, and anything that has to do with gripping, in general. Another application where we’re seeing traction is in medical applications, especially wearables and prototyping for wearables. Finally, since the material feels very much like silicone, TEPU 50A is ideal for seals, gaskets, and generally anything that requires a soft, bouncy material that has good rebound, with high intricacy and geometric freedom.”
Silicone-like materials are not only in increasingly high demand for a diverse range of high-value sectors, they are also uniquely difficult to work with in a 3D printing context, which adds much to the business case for Inkbit’s platform. Enabling customers to effectively use a material like TEPU 50A for AM applications requires a deep background in that particular area of material science, a proficiency that few other companies can claim as their own:
“What differentiates Inkbit from other platforms is the vision system that is integrated inside the machine,” Marini explained. “It’s a contactless technology, so we don’t have the need for any type of mechanical planarization that would deform a soft structure. Another advantage that we have is that we use wax as a support material. So, we can create all sorts of very thin, intricate geometries with these materials. To the best of my knowledge, we created the first machine vision system that creates a 3D depth map in real time as part of the process. Other platforms may have used cameras, but not 3D computer vision systems.”
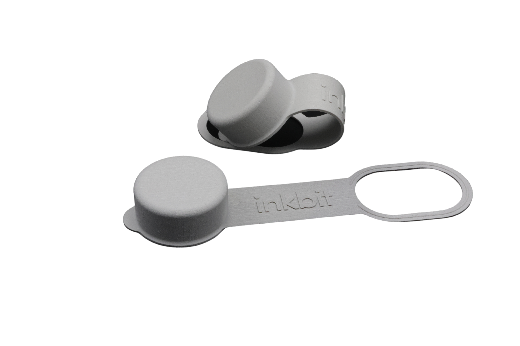
Although being so ahead of the curve has in some ways made the lead-up to commercialization more challenging than might’ve been the case with a more common underlying technology, it also seems to have allowed Inkbit to find equally innovative partners in other sectors, especially robotics:
“Robotics companies tend to be extremely innovative, and unafraid of new technologies,” said Marini. “They’re willing to try all sorts of new approaches. Also, in robotics, when you’re talking about volume production, you’re typically not talking about millions, you’re talking about maybe tens of thousands, or a hundred thousand max. Now, this is actually a volume that fits very well with 3D printing. Another thing I love about robotics companies is the concept of hardware/software co-development. In my opinion, this will become more and more prevalent across other industries, but I believe it was pioneered by the robotics industr. Let’s say I’m designing a robotic arm for some specific task. Typically what happens is there is an army of software developers that develop all the strategies and algorithms for controlling the arm’s movement. But software usually moves at an extremely fast pace compared to hardware. In an ideal world, what you want is to be able to change the geometry, change your hardware at the same speed as you’re changing your software so that the two can go together. With 3D printing, that problem can be solved, because you can rebuild your prototype every time you change your control algorithm. That’s what attracts robotics companies to 3D printing. They want to change the hardware at the speed of software.”
Of course, again, the potential to achieve that objective depends precisely on a company like Inkbit’s ability to negotiate between the needs of both software and hardware by cultivating the right material solution:
“Where our technology really shines is in prototyping fully functioning products, because we can print both rigid and soft structures at the same time. This advantage is quite substantial because it enables building structures that more closely resemble those created by nature. Often human inventions take their inspiration from nature. Inventors in aviation, for example, drew inspiration from the wings of birds. In the case of robotics, the most natural source of inspiration to turn to is the human hand. If you look at the most sophisticated naturally-occurring robots, such as our hands for example, they’re comprised of both rigid and soft structures. I think in order to advance the robotics field further, we need technologies like ours that provide a solution for multi-material manufacturing, as well as for prototyping and manufacturing on the same machine.”
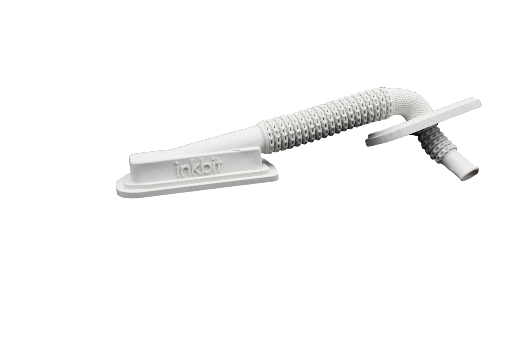
I finished up by asking if the development of new materials like TEPU 50A is the key to unlocking scale at this juncture in the AM sector’s history. Marini’s response was wholly unequivocal:
“It is absolutely the key, by far the most important aspect. I sometimes joke with my board of directors that we’re basically a materials company now, because the biggest challenge that we faced in the early years was ensuring our machine works reliably— our fantastic team of engineers and chemists kept their heads down, working to get the machine off the ground. Now the next chapter of our lives is how do we develop better and better materials all the way to production. My dream is to provide a platform that allows someone to have an idea in the morning while they’re drinking their coffee, that they can prototype it in the afternoon, and they can launch it to market the next week, all on the same machine.”
Subscribe to Our Email Newsletter
Stay up-to-date on all the latest news from the 3D printing industry and receive information and offers from third party vendors.
Print Services
Upload your 3D Models and get them printed quickly and efficiently.
You May Also Like
3D Printing News Briefs, July 2, 2025: Copper Alloys, Defense Manufacturing, & More
We’re starting off with metals in today’s 3D Printing News Briefs, as Farsoon has unveiled a large-scale AM solution for copper alloys, and Meltio used its wire-laser metal solution to...
Etsy Design Rule Change Reduces Selection of 3D Printed Goods
Online marketplace Etsy has implemented a rule change requiring all 3D printed goods on the site to be original designs. The update to the site’s Creativity Standards states, ¨Items produced using...
Siraya Tech Introduces New Elastomer 3D Printing Materials, Including Foaming TPU
California company Siraya Tech, founded in 2019 with a focus on material science, customer focus, and agility, develops high-quality 3D printing materials that meet the needs of creators, hobbyists, and...
3D Printing News Briefs, April 12, 2025: RAPID Roundup
The news from last week’s RAPID+TCT in Detroit just keeps on coming! That’s why today’s 3D Printing News Briefs is another RAPID Roundup of more exciting announcements from the trade...