Move Methodically and Fix Things: Seurat CEO James DeMuth Shows How Metal 3D Printing is Remaking US Tech Landscape
A man stood with one leg on an e-scooter, the other on the pavement, as we both waited for the crosswalk light to change to the walk symbol. I glanced slightly to my left and couldn’t help but notice that the man looked like he didn’t have a care in the world, which I may have noticed because it so pronouncedly contrasted with my own state of mind, as I rushed from one interview to the next in 100° heat.
Then the man and I looked at each other at the same time, and I realized I’d met him the night before, and also that he was who I was on my way to interview: James DeMuth, CEO of Boston’s Seurat, a whole new kind of company in the metal additive manufacturing (AM) space. We were both in Austin for Formnext Forum’s first North American event, where Seurat had its first-ever AM trade show booth.
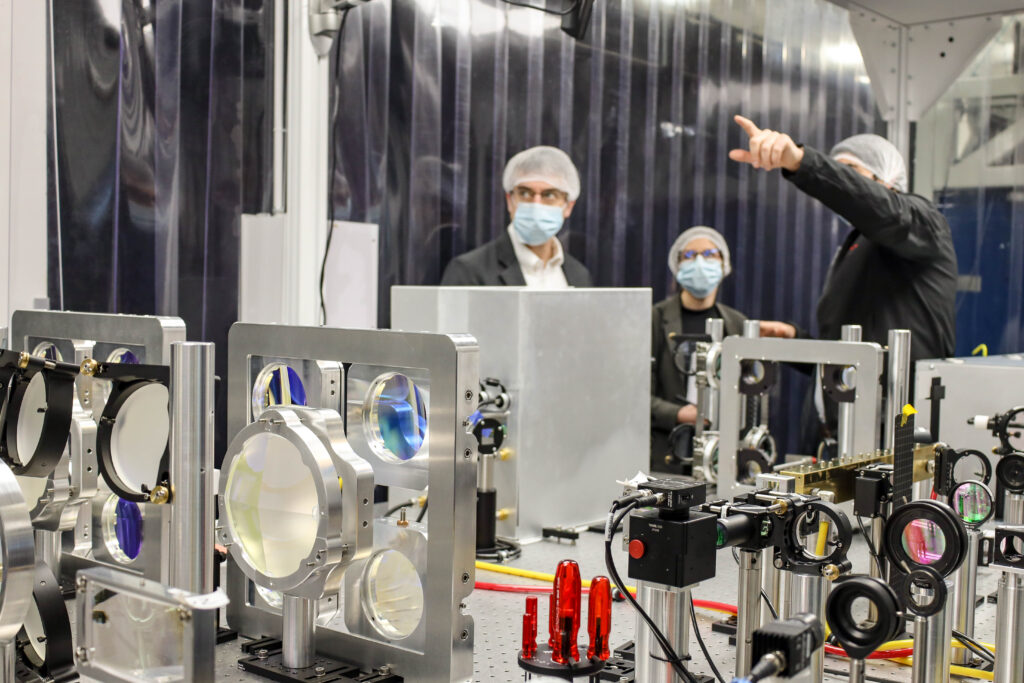
Seurat’s CEO and Co-Founder, James DeMuth, demonstrates how Seurat’s laser engines power, heat, and pattern in the Area Printing process.
“I guess neither of us is late,” DeMuth said with a grin, right as the traffic light gave us the go-ahead to cross. He rode the remaining few minutes to the Palmer Events Center at the slowest possible speed the e-scooter could travel, while I walked alongside him, kind of wishing that I, too, had an e-scooter.
James DeMuth is the kind of guy who would be very easy to not like, if only he weren’t so likable. It’s common to be dubious about youthful American entrepreneurs who rise to success quickly, attract big investments, and promise that they’re going to deliver unprecedented results. It can be satisfying to bet that something is too good to be true and then see your cynicism validated.
But while DeMuth might look the part of the Silicon Valley startup founders who have burned investors so many times in the last decade, he’s a new breed. For one thing, he didn’t emerge from some other startup, or drop out of college to start a business with his parents as the leads on his first funding round, etc. He earned his stripes in the R&D trenches, doing research on weapons stockpiles stewardship at the National Ignition Facility (NIF), part of the Department of Energy’s Lawrence Livermore National Laboratory (LLNL).
That is where DeMuth, who got his master’s in mechanical engineering at Stanford, gained experience (from 2010-2015) working with “192 of the world’s most energetic lasers,” which comprise a system at NIF that is “the size of three football fields.” He was part of a team working on a nuclear fusion project at LLNL, which is where DeMuth first encountered AM. Searching for a metal capable of handling the nearly 1100°F heat of the nuclear fusion process, the team found that powder bed fusion (PBF) AM was the best candidate.
From LLNL to Seurat
The problem was that, to build the LLNL fusion chamber, existing PBF processes at the time would’ve taken “200 years”, a reference point DeMuth cites frequently in explaining what Seurat’s key differentiators are. Interestingly, the alternative to PBF that DeMuth and his colleagues homed in on was being developed by another team at LLNL: the Optically Addressed Light Valve (OALV), which was first installed at the NIF in 2010. For five years, DeMuth helped develop an AM platform that could incorporate OALV.
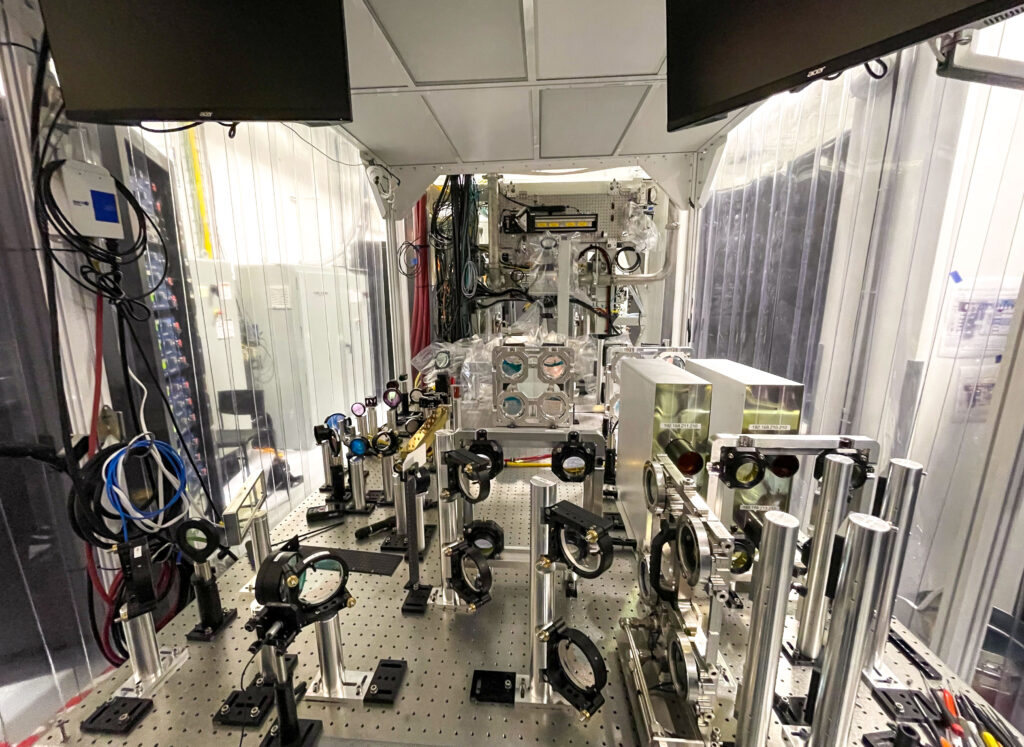
An optics array in Seurat’s new pilot factory conditions and routes the patterning laser system in the Area Printing process.
In 2015, DeMuth proved that the OALV platform could melt metal, met his co-founder, Erik Toomre, and officially started Seurat. In January 2016, Seurat secured the licensing for OALV from LLNL. This is the core technology underlying “area printing”, the large-scale, singularly high-speed metal AM technique that is wholly unique to Seurat:
“[Seurat builds] our own lasers,” DeMuth explained during his keynote presentation at Formnext Forum Austin, a conversation with Additive Manufacturing Media’s Peter Zelinski. “We then build our own [OALVs] — and use them to patterned our laser light, embedding a pattern into a high-powered pulse. That pulse is projected down onto the powder bed, which stamps an area of melted metal at a time. The way the LPBF process works today, you focus a laser to a spot, printing one pixel, or more accurately one voxel, at a time, and then you scan that laser around—you’re doing single-pixel printing. The way our process works takes a massively parallel approach to that, printing hundreds of thousands or millions of pixels per pulse, and then repeating that 40 times per second in our Gen-1 system.”
Seurat’s Business Model
Seurat’s biggest differentiator is what its incorporation of OALV enables, which is the potential to use AM for honest-to-goodness metal parts output at scale. This allows Seurat’s strategy to rest not on selling machines — something that, at least presently, it has no intentions of ever doing — but on selling parts. It is the established business model of the Tier 1 contract manufacturer, complete with long-term contracts and plans for a steadily decreasing cost-per-part, just completely reimagined in accordance with what the latest methodological advances make possible:
“Our machines are kind of the size of a double decker bus, so it’s a longer ramp cycle to get machines of that magnitude deployed. We’ve built the first one, and then it’s about another year after that until the second one rolls out, because you have a lot of examining what you’ve done, folding in changes, going from alpha version to beta version,” DeMuth told 3DPrint.com. “And then we look at trying to build one a quarter, and then one a month. And then from one a month, how do you get to X a month?”
As DeMuth went on to describe, the idea down the road isn’t just more machines, but more powerful machines:
“For right now, let’s say that the price point for parts we produce is between 200 and 300 dollars a kilo. Metal AM is typically 500 dollars a kilo or above. When we look at where we’re going, though, we’re looking at how do you get that price point down to something more like 20 to 30 dollars a kilo. The machines that are required to take you on that journey don’t get smaller; they get bigger, they get massively more productive. So, you’re looking at giant factories for mass production of parts. If you look at how big some of the giant machine shops in the world are, that have tens of thousands of CNCs operating, or giant casting houses, they’re gigantic facilities,” DeMuth said.
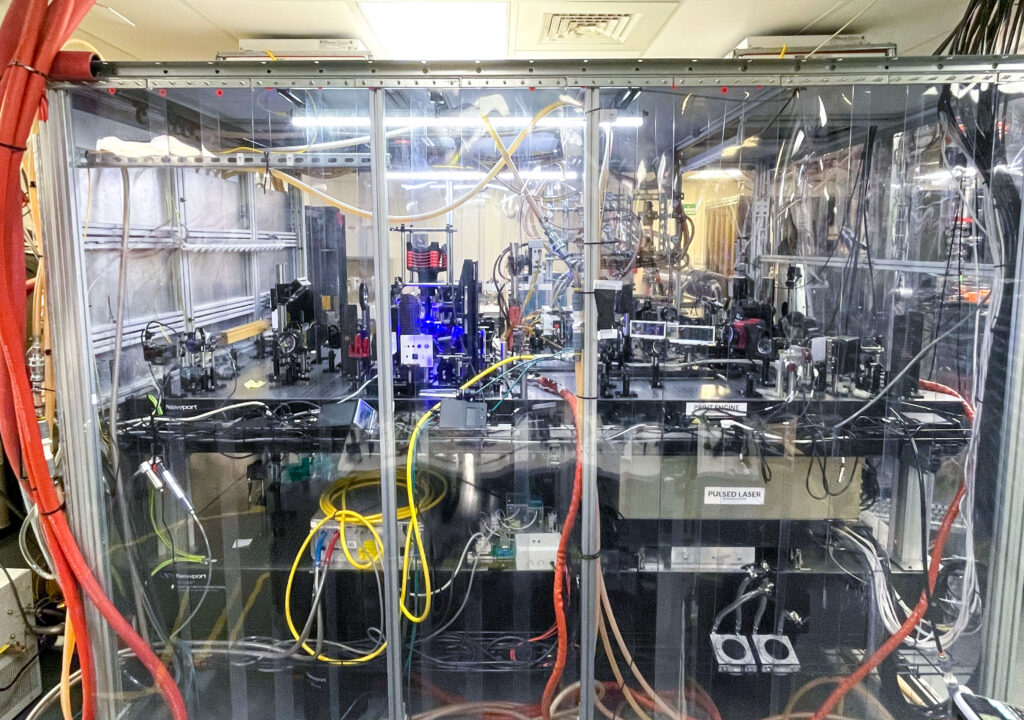
Prototype print engine and patterning lasers stationed in Seurat’s research lab. This system continues to validate parts for customers in Seurat’s Area Printing Program (APP)
Seurat’s Road Map
Seurat’s ambitions for growth will obviously require constantly expanding operating space, a trajectory that the company is already working towards:
“We signed the lease on [our pilot factory] in June 2021, and construction was done by January 2022. We were mostly finished building the alpha machine by the end of 2022, and then throughout 2023, it’s been debugging, commissioning, finding parts from vendors that were delivered that were wrong, getting them reworked. We got the first melt in June and now we’re essentially doing final commissioning. [Then we have] our manufacturing center,” DeMuth showed me, via video footage that Seurat had made available for attendees, “where we essentially do a whole bunch of subsystem builds. This is gearing up not just to do one system, but to eventually do one a month. And then this is another facility we have down the road, we just signed the lease on this. So, there’s a lot of build out work that has yet to happen, but they’ve already got a ton of clean room space…”
— this is where Seurat builds the lasers and OALVs, as mentioned above —
“…and they’re basically semiconductor devices, so we need to build them in clean rooms — we need a lot of space to build them, and a lot of equipment to build them.” When it comes to scaling machine deployments, incorporating all the machine, lasers, and light valve builds, Seurat will need a much bigger facility. “… And we’ve got an LOI [letter of intent] on a one-hundred-thousand-square-foot facility, which we’re earmarking for our first production factory.”
Building a Workforce
Five facilities in all so far that are either operational or on the fast-track to being operational, all within a short drive from each other in the Boston area. This is what the re-shoring of manufacturing looks like in practice. The next logical question is: where are you going to find the workers to fill all those facilities, not to mention all the ones that will ultimately have to be built to support Seurat’s ambitious expansion targets?
Seurat has been well aware for some time of how urgent the need for workforce development is, which is why the company announced a plan in the summer of 2022 to increase its workforce to 1,000 by the end of 2025. Right now, the company has 116 employees. DeMuth pointed out to me that, although the 1,000 number is just a benchmark, he’s confident that Seurat can get close to that in the next few years. Unsurprisingly, he expects that the key to its success on this front will be how quickly Seurat gets its production capacity up and running:
“When you look at the breakdown of what roles and employees we need to bring in en masse, it’s really about building the foundries,” DeMuth said. “The vast majority of people [we hire] will be either operating machines or essentially applications engineers to bring parts into the pipeline. The more parts you can bring in, the more customers you can get up to speed, those are essentially how you plant the seeds for future volume production.”
Since the Seurat platform is so unique relative to virtually all other AM systems currently on the market, the company has been in the fortunate position of not having to worry itself as much as the rest of the sector about the lack of available AM know-how in the workforce. This is a variable that’s going to be changing quickly because of what DeMuth pointed out about applications development being the key to growth:
“At a high level, we’re looking at bringing in folks who have experience and can hit the ground running. Five, maybe ten percent of our company has a background in AM. Most of the company is from semiconductor industry equipment building, machine building, or they’re from the biggest, baddest laser experts in the world. We’ve merged next-gen laser technology and optics technology with the relentless rigor of the semiconductor industry, which is how we get our machines built. The next step is where all the additive folks come in: operating the machines, getting the parts designed and fine-tuned for the area printing process. There’s a lot of training that we’ll have to do to bring people up to speed, and that’s part of the reason we’re at a show like this, is to bring in talent.”
With its headquarters in Boston, Seurat is also establishing a presence in one of the only cities in the US where a steady pipeline of AM workers is not an unreasonable thing to expect. The company’s hiring efforts should also be boosted by being named one of Boston’s best places to work by Boston Globe (in 2022) and builtin.com (in 2023).
But most of all, Seurat should attract attention from prospective employees by placing an emphasis on decarbonization in manufacturing supply chains: DeMuth’s aforementioned keynote presentation was entitled “How to Manufacture 25 Tons of Metal Per Year, Sustainably”. Since we live an era in which that very topic is one of the factors most responsible for making “reshoring” a household word, it’s hard to imagine that the company won’t find allies ready to help it fill its factories with new recruits:
“As high-volume manufacturers, we’re going to use a lot of power. A factory of our Gen-X machines in 2030, we’re nominally targeting a third of a gigawatt [Author’s note: a gigawatt is enough to power around 800,000 homes for a year]. When we’re looking at those scale levels, we’re going to want to co-deploy our part printing factories with power generation. If we’re doing that, let’s also make sure it’s a non-greenhouse gas emitting source in the process. …And if you can oversize the power plant deployment to bring green power to local communities in the process, it’ll be a win-win. There’s two things we’re focused on, one is net-zero, and the other is how can we just make our baseline manufacturing process better and better through relentless improvement. And we’re looking to tackle both of those simultaneously. That means working with our powder providers to make sure that they’re using clean energy sources to make their powder. And maybe we co-locate powder production with our machine production so we can use the same power source — that’s just one very simple way to check that box.”
There are so many moving pieces to pay attention to in order to bring manufacturing back to a scene — the US — that has, for decades, spent all of its energy spiriting it away. One thing you can give DeMuth credit for is that he is, at the very least, trying to keep his focus on all of it at once, while also making his moves as strategically as possible.
This is why, as much as he might seem to fit the mold of a tech CEO, James DeMuth is a novel addition to the world of US startup executives. Back when Meta was still Facebook, the company’s internal motto was “move fast and break things”, which later became the name of a book about Silicon Valley culture. I don’t know if Seurat has a motto, but if it does, I bet it’s something very different.
Images courtesy of Seurat.
Subscribe to Our Email Newsletter
Stay up-to-date on all the latest news from the 3D printing industry and receive information and offers from third party vendors.
Print Services
Upload your 3D Models and get them printed quickly and efficiently.
You May Also Like
The Dental Additive Manufacturing Market Could Nearly Double by 2033, According to AM Research
According to an AM Research report from 2024, the medical device industry, specifically in dentistry, prosthetics, and audiology, is expected to see significant growth as these segments continue to benefit from...
Heating Up: 3D Systems’ Scott Green Discusses 3D Printing’s Potential in the Data Center Industry
The relentless rise of NVIDIA, the steadily increasing pledges of major private and public investments in national infrastructure projects around the world, and the general cultural obsession with AI have...
AM Research Webinar Explores Continuum’s Sustainable Metal Additive Manufacturing Powders
Metal additive manufacturing (AM) powder supplier Continuum Powders is working to develop solutions that empower industries to reduce waste and optimize their resources. An independent life cycle assessment (LCA) of...
3D Printed Footwear Startup Koobz Lands $7.2M in Seed Round
California-based Koobz is focused on reshoring the U.S. footwear supply chain with advanced manufacturing processes, including 3D printing. The startup just announced that it has added $6 million to its...