Bioengineering has significantly evolved in the last decade. Once again, scientists turned to 3D printed cardiac tissues to delve deeper into combating heart disease and tailoring treatments to the unique needs of individual patients. This ambition even extends to creating implantable tissues that might one day repair or replace damaged parts of a patient’s heart.
In a landmark study led by Harvard John A. Paulson School of Engineering and Applied Sciences (SEAS), researchers have developed a new method to 3D print structures that mimic the beating of a human heart. Thanks to a fiber-infused gel (FIG) ink that combines hydrogel infused with prefabricated gelatin fibers, they could precisely print 3D models of heart ventricles without needing additional support materials.
According to a paper published by the team in Nature Materials, during the 3D printing process, the fibers align in a way that helps heart cells (cardiomyocytes) to organize themselves in patterns similar to those found in actual heart tissues. As a result, the printed heart models exhibit properties similar to real hearts, like how they conduct electricity and contract. In the future, this technique could be further tweaked to create even more complex and functional heart models.
The significance of this work is that it introduces a novel way to 3D print heart tissue, getting closer to replicating the intricate structures and functions of real hearts. By adding gelatin fibers to the hydrogel, the team could create more detailed and accurate heart models. This has potential applications in medical research, drug testing, and possibly future treatments. According to the team, the method still has room for improvement, and further studies will try to enhance its capabilities, including introducing multiple cell types or better-mimicking blood vessels.
Suji Choi, a research associate at SEAS and the paper’s first author, noted the challenges they faced in striving to replicate organ structures for drug testing.
“People have been trying to replicate organ structures and functions to test drug safety and efficacy as a way of predicting what might happen in the clinical setting. But until now, 3D printing techniques alone have not been able to achieve physiologically-relevant alignment of cardiomyocytes, the cells responsible for transmitting electrical signals in a coordinated fashion to contract heart muscle,” explains Choi.
The pivotal moment came with the fusion of fibers into the printable ink, allowing the creation of intricate 3D shapes without external support.
“FIG ink is capable of flowing through the printing nozzle, but once the structure is printed, it maintains its 3D shape. Because of those properties, I found it’s possible to print a ventricle-like structure and other complex 3D shapes without using extra support materials or scaffolds,” says Choi.
The FIG ink’s origin was an intersection of ideas. Postdoctoral researcher Luke MacQueen suggested blending fibers created through a novel rotary jet spinning technique with the ink. This method, which is much better than the traditional electrospinning technique, preserves proteins that could otherwise degrade in electric fields.
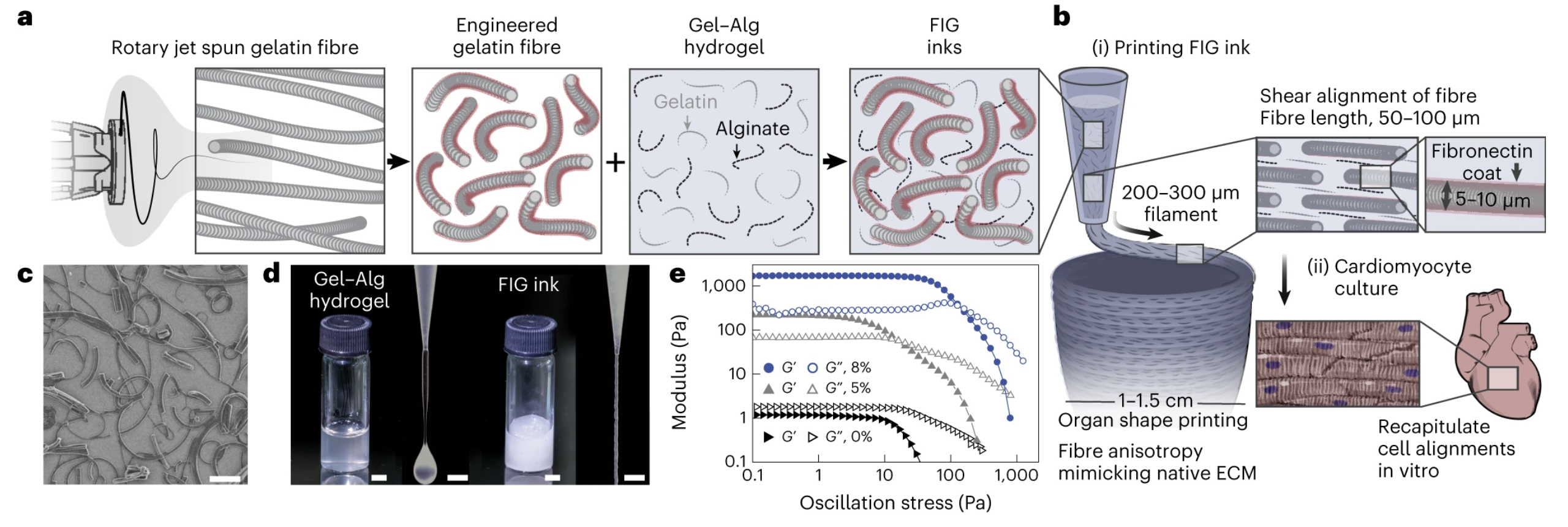
Schematic illustration of FIG ink components. Image courtesy of Harvard SEAS/Springer Nature/Nature Materials
During the ongoing experimentation, Choi discovered that when electrical stimulation was applied to these 3D printed structures, it resulted in a coordinated wave of contractions mimicking the rhythm of real heart ventricles. The team claims they immediately saw the potential of the technique became clear: ventricles capable of pumping between 5 and 20 times more fluid volume than previous models.
“We started this project to address some of the inadequacies in 3D printing of biological tissues.” says Kevin “Kit” Parker, senior author of the paper and Tarr Family Professor of Bioengineering and Applied Physics, head of the Disease Biophysics Group at SEAS. “When Luke developed this concept, the vision was to broaden the range of spatial scales that could be printed with 3D printers by dropping the bottom out of the lower limits, taking it down to the nanometer scale. The advantage of producing the fibers with rotary jet spinning rather than electrospinning is that we can use proteins that would otherwise be degraded by the electrical fields in electrospinning.”
Although the team acknowledges the prototype’s limitations, they see immense potential. In fact, efforts are already underway to engineer more lifelike heart tissues, and there’s optimism about using this method to construct more intricate cardiac structures like heart valves and dual-chambered mini hearts. In addition, Parker highlighted the group’s dedication to developing human tissues for regenerative therapies.
In recent years, there have been other noteworthy endeavors in this space. For instance, researchers from Tel Aviv University made waves in 2019 by 3D printing cardiac patches using a patient’s cells, achieving a complex structure complete with blood vessels and chambers. Similarly, a 2017 initiative from the University of Minnesota relied on a custom 3D printer to craft lifelike artificial heart models, showcasing the intricate anatomical details that can now be replicated. However, the new approach described by Harvard researchers is unique. With robust backing from numerous esteemed institutions on this project, including the National Science Foundation (NSF) and the National Institutes of Health (NIH), the future of bioengineering looks bright at Harvard SEAS.
Subscribe to Our Email Newsletter
Stay up-to-date on all the latest news from the 3D printing industry and receive information and offers from third party vendors.
You May Also Like
Model No. Deploys Titan Pellet 3D Printers for Sustainable Furniture Production
Over the years, many designers have tried to create 3D printed polymer furniture. Early pioneers like Janne Kyttanen, Materialise’s MGX, and Joris Laarman have led the way with 3D printed...
3D Printing News Unpeeled: Recycling PLA, More Efficient Atomizing
Filamentive hopes to recycle your PLA if you’re in the UK and order over £500 worth of filament. Their partner 3D Printing Waste (3DPW) will turn the PLA into injection...
Lighting the Way with Potato Starch: Sustainable Polish ECO Lamps Use 3D Printing
Lighting that meets the essence of nature: this is the reality brought to life by ECO Lamps, which introduces a fresh perspective to sustainable lighting design using potato starch. These...
3D Printing News Unpeeled: 3D Printed Construction Standard, Sand Wall & Self Heating Microfluidics
ISO/ASTM Standard 52939:2023 has been released and it sets standards for QA for 3D Printed polymer, composite and cement buildings. This is most welcome since 3D printed construction is a...