On March 22, 2023 at 11:25 p.m. EST, Relativity Space successfully launched the world’s first 3D printed rocket, as a part of a flight test the company named “Good Luck, Have Fun,” or GLHF. The two-stage, 110-foot-tall Terran 1 rocket took off from Cape Canaveral Space Force Station’s Launch Complex 16 in Florida after previously calling off two previously launch attempts.
The Terran 1 was made using what has been labeled as the world’s largest metal 3D printer, Relativity’s robotic directed energy deposition (DED) system, Stargate. Altogether, the vehicle is made up of 85 percent 3D printed parts. 85 percent is a significant portion of 3D printed parts for any commercial product, let alone a rocket.
The event marks a milestone for Relativity Space, founded by Blue Origin alums Tim Ellis and Jordan Noone in 2016, as the company can now begin moving toward the launch of small payloads on the Terran 1, theoretically capable of delivering up to 2,756 pounds to low Earth orbit.
Failed Launches and Orbit
The successful launch was seven years in the making and comes after two recent setbacks. On March 8, the Terran 1 spent several hours standing at the launch pad, before the rocket’s first launch was scrubbed. After a second attempt on March 11, weather concerns and an issue with stage separation once again resulted in preventing lift off.
As detailed by our resident space 3D printing expert Vanesa Listek, failed launches are par for the course in this sector, namely as a result of weather conditions. Vanesa wrote:
“[I]n the past 30 years of missions lifting off from the Kennedy Space Center or Cape Canaveral Air Force Station, 48 percent of scrubs were due to bad weather conditions alone. For many rockets, the “no-go” decision also arises from technical issues that interfere with the launch, such as in central propulsion systems. This was the case for Terran 1…the truth is that plenty of takeoffs have been scrubbed. For example, in October 2020, back-to-back last-second launch scrubs by two SpaceX Falcon 9 rockets 36 hours apart led Elon Musk to undertake a “broad review” of launch operations in Florida to increase its launch rate. Then in 2021, Boeing’s second attempt at an uncrewed test flight of its new Starliner capsule to the International Space Station (ISS) was scrubbed due to an “unexpected valve” problem. And last year’s uncrewed Artemis 1 launch was postponed twice due to a liquid hydrogen leak. Indeed, the list goes on and on.”
In this case, the launch was successful, but the Terran 1 rocket was unable to reach orbit due to an “anomaly” on the second stage. As is the case with actual launches, failures in the space sector are a common occurrence, so much so that NASA’s Paul Gradl made failure the thesis of his presentation at Additive Manufacturing Strategies 2023 and that Space.com publishes an annual list of rocket failures.
In 2021, Astra Space’s Rocket 3 launch resulted in a devastating spin, while its 2022 Rocket 3.3 also failed. Though Blue Origin has had six successful flights for space tourists using its New Shepherd vehicle, an uncrewed mission with the same vehicle was not successful due to the failure of the BE-3 main engine. SpaceX has seen three of its Starship prototypes explode in flames, with Elon Musk only predicting a 50 percent chance of success for a launch this year. Despite the odds, the company is moving forward. Though Relativity space was unable to reach orbit, its launch represents an enormous success for the additive manufacturing (AM) industry, particularly for new space application.
3D Printing for New Space
The “3D Printing in Commercial Space: The AM Ecosystem in the Private Space Industry” report from SmarTech Analysis anticipates that the private new space sector will reach $2.1 billion by 2026. Relativity Space has already achieved $1.3 billion in funding from the likes of Mark Cuban and has reported a backlog of $1.65 billion in customer launch contracts, with each ride on the Terran 1 priced at $12 million apiece. However, some of these contracts are actually for payloads to be launched on the next rocket, the Terran R, a bigger (216-foot-tall), more powerful (44,000 pounds in payload) and reusable vehicle that Relativity Space plans to start flying as early as next year. Given the sheer value of the company, with AM as its backbone, $2.1 billion in revenues by 2026 already seems like an underestimate.
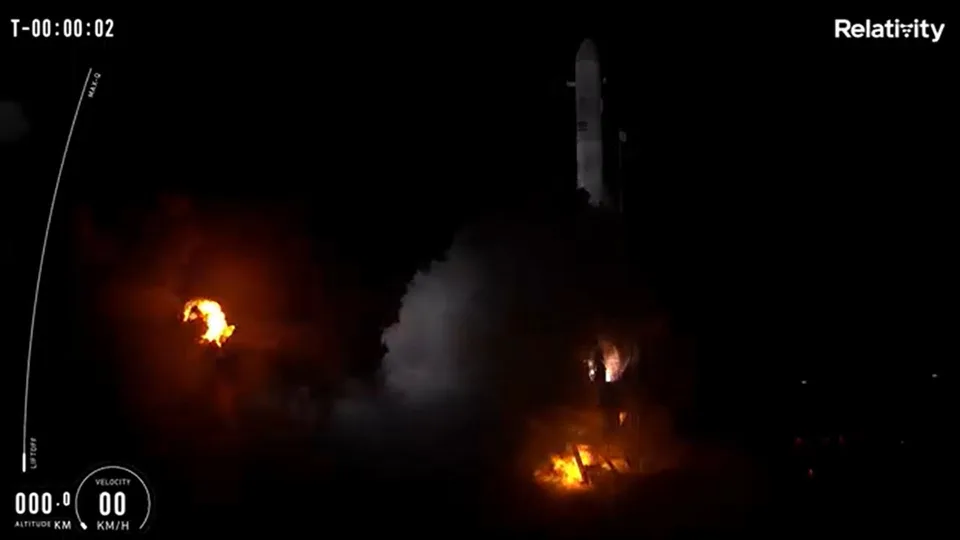
Relativity Space’s Terran 1 rocket lifts off.
Relativity is nowhere near the first in the space industry to rely on 3D printing. Long a staple of prototyping, research, and development, the use of AM slowly ramped up until reaching a seeming critical mass in which a slew of new space companies began adopting it for increasingly advanced applications. Rocket Lab (Nasdaq: RKLB) has launched 33 rockets with 3D printed engines, including most recently its first from U.S. soil. In fact, it is largely the demand from new space that has resulted in the release of increasingly large and productive laser powder bed fusion (LPBF) metal 3D printers, playing a key role in what we have dubbed the “laser wars.”
All of this points to the value of AM for space applications. As the best technology for producing low volumes of high-value parts in the fastest manner, 3D printing is the most cost effective process for building critical components for space. Nowhere else in society will you see a more perfect task for AM. As a result, the new space industry is booming largely thanks to the key role of 3D printing in producing critical components.
3D Printing Beyond Space
However, Relativity Space distinguishes itself not only in the sheer mass of 3D printing in its Terran 1 rocket, but also in its manufacturing approach. DED is uniquely suited for such large structures. SmarTech’s “DED and Large-Format Additive Manufacturing Markets: 2021-2030” report sees that specific AM segment hitting $739 million in revenues by 2026.

A long exposure view of Relativity Space’s Terran 1 taking off.
Just as everything else from space research trickles down into the rest of industrial society, Relativity Space’s technology will impact other sectors. From the jump, you can imagine anything that resembles a rocket in terms of shape, propulsion, and value to be 3D printed via DED—i.e., missiles. However, we’ll also see the technology applied to other large-scale metal structures and, because the startup has developed an automated production flow for its process, there’s more value than just big, metal things. Relativity Space has always had it in its roadmap to use its technology beyond space, so we can also envision submarine hulls and aircraft fuselages produced with Stargate and its future descendants.
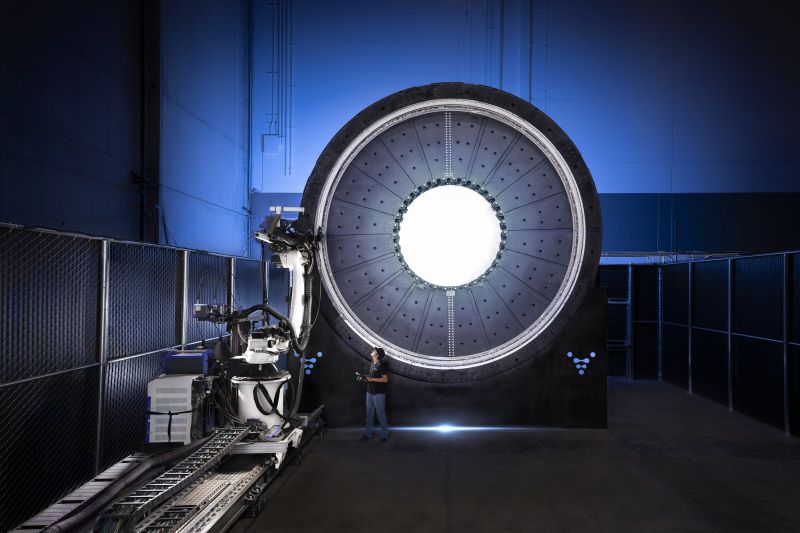
Relativity Space’s Stargate 4th Generation metal 3D printer moves horizontally instead of vertically, feeding multiple wires into a single print head. Image courtesy of Relativity Space.
For these reasons, not only will Relativity and new space be propelled by 3D printing, but so too will the AM sector and manufacturing at large.
Subscribe to Our Email Newsletter
Stay up-to-date on all the latest news from the 3D printing industry and receive information and offers from third party vendors.
Print Services
Upload your 3D Models and get them printed quickly and efficiently.
You May Also Like
Johns Hopkins University Researchers Develop HyFAM Technology
Two scientists from Johns Hopkins University, Nathan C. Brown and Jochen Mueller, have developed a hybrid manufacturing technology they call HyFam, or Hybrid Formative Additive Manufacturing. Their work on this technology...
3D Printing G-Code Gets an Upgrade: T-Code
Good old G-Code still manages many 3D printers, great and small. Just like the STL, it’s a standard that enables collaboration while also holding the additive manufacturing (AM) industry back....
AM Rewind: The Biggest News and Trends of 2024
After a sluggish 2023, driven by persistent inflation and geopolitical tensions, 2024 has seen some recovery. Economic growth climbed from about 2.8 percent in 2023 to a modest 3.2 percent...
Metal Wire 3D Printer OEM ValCUN Announces Plans for 2025 Expansion
ValCUN, a Belgian original equipment manufacturer (OEM) of wire-based metal additive manufacturing (AM) hardware, has announced that the company has entered the next phase of its growth trajectory, making key...