In a harsh, unforgiving environment, abundant design decisions, complicated manufacturing, and component integration are necessary for hot-fire testing of liquid rocket engines. Knowing that things can go wrong in milliseconds, the engine’s rumble and the test’s thrill can sometimes leave you forgetting to breathe. Although complex and challenging, the design process for rocket engines is usually not where significant issues arise.
Manufacturing and assembling components into a complex system involves significant time, costs, and skills to meet integration and performance requirements. Yet, the promise of Additive Manufacturing (AM) for propulsion applications is being demonstrated across the aerospace industry for critical parts and enabling rocket designs not previously possible. Cutting-edge techniques like AM are used to reduce part count, optimize weight, and allow for more complex parts geometry. AM significantly reduces manufacturing component costs and lead times. AM also allows for a much faster design-fail-fix cycle to develop and test early prototypes before moving into production.
NASA has a vital role to help solve some of the manufacturing challenges while improving rocket engine performance. One example of high risk and high reward development is NASA’s Game Changing Development Rapid Analysis and Manufacturing Propulsion Technology (RAMPT) project.
RAMPT engaged industry, commercial space, and academia to advance and integrate several AM and advanced manufacturing processes and prove these through hot-fire testing. The liquid rocket engine combustion chamber and nozzle are often manufactured from a single alloy using one of the many metal additive manufacturing processes. RAMPT explored new research to create enabling new alloys, multi-alloy AM components, and combining several of the metal AM processes for further optimization of AM designs. This philosophy drove the team to merge novel AM designs with other advanced manufacturing composite overwrap techniques to further reduce weight (Figure 1).
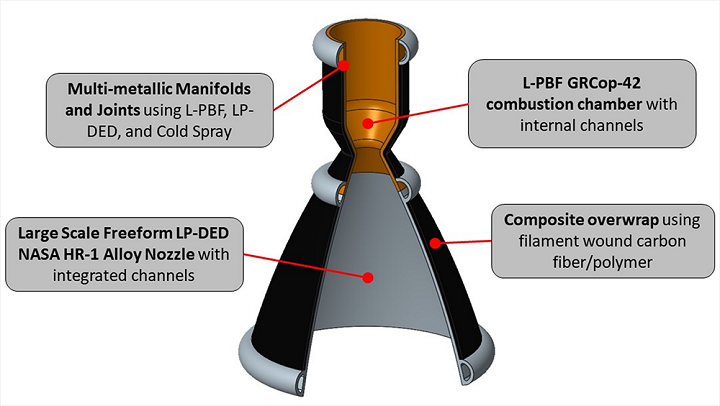
Figure 1. RAMPT concept using multi-alloy AM, large scale LP-DED, and composite overwrap integrated into a rocket engine thrust chamber assembly (NASA).
Scale was one of the challenges the RAMPT team matured. NASA along with industry partners advanced the laser powder directed energy deposition (LP-DED) AM process to demonstrate complex thin-wall internal channel geometry at scales greater than 1-meter in diameter. This was targeting the channel-cooled nozzle. The freeform LP-DED process allows for large-scale additive manufacturing – not constrained by the build box. In just 90 days the RAMPT project printed one of the largest AM nozzles NASA has produced by utilizing LP-DED, which included over 1,000 internal channels and measured 1.5 m (59 in) diameter and 1.8 m (72 in) tall (Figure 2). A full-scale RS-25 rocket engine nozzle liner was also developed under the RAMPT project with a 2.4 m (95 in) diameter and 2.8 m (111 in) height but did not include internal channels (Figure 2).

Figure 2. Large scale directed energy deposition nozzles. (Left) 1.5 m dia and 1.8 m height integral channel nozzle using NASA HR-1 alloy [NASA / RPMI]. (Right) 2.4 m dia and 2.8 m height liner using dual-head LP-DED with JBK-75 alloy (NASA / DM3D).
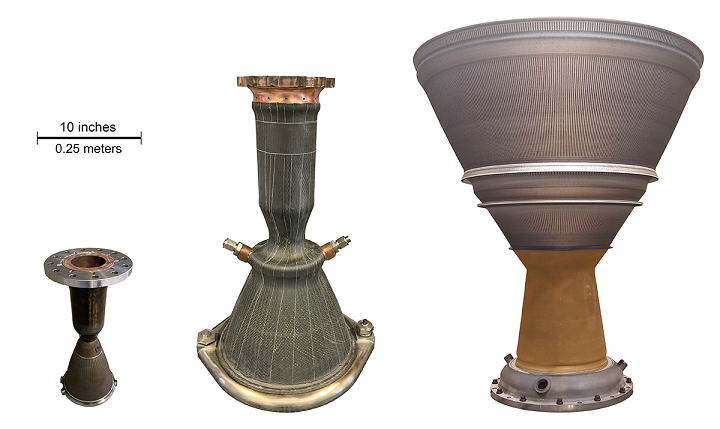
Figure 3. Various scales of composite overwrap multi-alloy and multi-process AM thrust chambers developed under the RAMPT project (NASA).
NASA has accumulated over 100,000 seconds of hot-fire testing on various AM parts and systems. This experience has helped NASA understand many of the challenges and limitations of AM and help establish standards for certification of AM components. To further advance the technology under the RAMPT project, 2,000 lbf (8.9 kN) and 7,000 lbf (31 kN) integrated thrust chambers were hot-fire tested at NASA’s Marshall Space Flight Center (MSFC) test stand 115 (Figure 4). Decouple (bolted) thrust chamber testing was also conducted at the 35,000 lbf (156 kN) to obtain data on the L-PBF GRCop-42 chamber and NASA HR-1 LP-DED integral channel nozzle (Figure 5). This testing proved out the challenges of the AM multi-alloys, combined AM processes, and composite overwrap and provided various lessons learned for industry infusion. Future testing will include a fully coupled 40,000 lbf (178 kN) at chamber pressures exceeding 1,400 psi (97 bar).
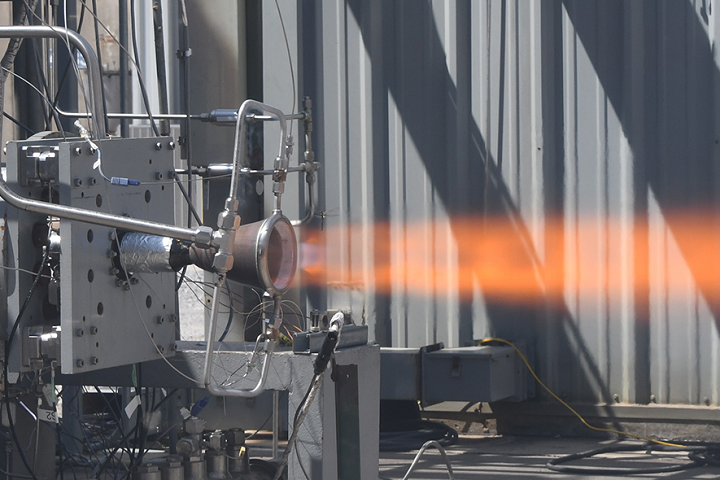
Figure 4. Hot-fire testing of a composite overwrap coupled GRCop-42 L-PBF chamber and LP-DED NASA HR-1 nozzle (NASA).
RAMPT utilized a multi-alloy, combined AM process approach along with complex composite applications and advanced AM simulation capabilities to develop large-scale, regeneratively-cooled liquid rocket engine technology. The RAMPT project reduced the design, analysis, fabrication, and assembly lifecycle lead times by over 50%. It also decreased part count by greater than 10x, reducing weight by more than 30% and increasing reliability. Additional RAMPT accomplishments included engaging the manufacturing community and facilitating the infusion of technology into the commercial industry through public-private partnerships to create a healthy supply chain. All data generated under the RAMPT project is available to industry partners.
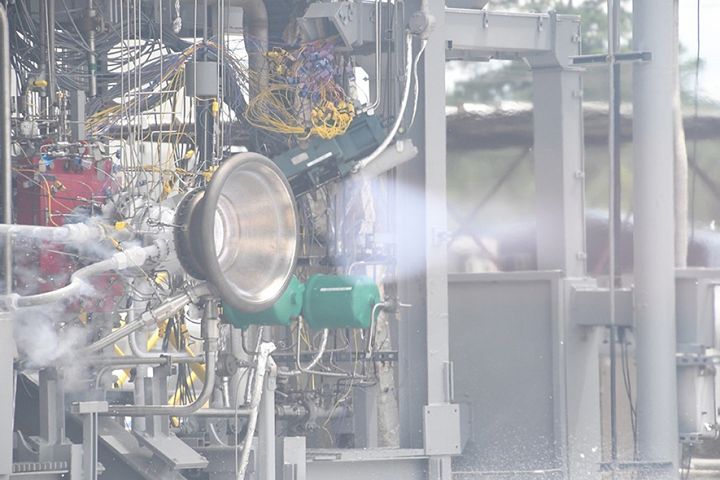
Figure 5. Hot-fire testing of a 35,000 lbf AM bimetallic GRCop-42 L-PBF/Inconel 625 LP-DED combustion chamber and LP-DED nozzle with integral channels (NASA).
NASA is participating at Additive Manufacturing Strategies, taking place in New York City from February 7-9, 2023. Paul Gradl, Principal Engineer, Subject Matter Expert, at NASA Marshall Space Flight Center (MSFC) will be taking part in Session 3, Talk 2: Metal AM for Rocket Engines: Successes and Failures, on February 8. Register for your ticket to attend here.
Subscribe to Our Email Newsletter
Stay up-to-date on all the latest news from the 3D printing industry and receive information and offers from third party vendors.
Print Services
Upload your 3D Models and get them printed quickly and efficiently.
You May Also Like
Reinventing Reindustrialization: Why NAVWAR Project Manager Spencer Koroly Invented a Made-in-America 3D Printer
It has become virtually impossible to regularly follow additive manufacturing (AM) industry news and not stumble across the term “defense industrial base” (DIB), a concept encompassing all the many diverse...
Inside The Barnes Global Advisors’ Vision for a Stronger AM Ecosystem
As additive manufacturing (AM) continues to revolutionize the industrial landscape, Pittsburgh-based consultancy The Barnes Global Advisors (TBGA) is helping shape what that future looks like. As the largest independent AM...
Ruggedized: How USMC Innovation Officer Matt Pine Navigates 3D Printing in the Military
Disclaimer: Matt Pine’s views are not the views of the Department of Defense nor the U.S. Marine Corps Throughout this decade thus far, the military’s adoption of additive manufacturing (AM)...
U.S. Congress Calls Out 3D Printing in Proposal for Commercial Reserve Manufacturing Network
Last week, the U.S. House of Representatives’ Appropriations Committee moved the FY 2026 defense bill forward to the House floor. Included in the legislation is a $131 million proposal for...