Vienna, Austria-based Lithoz, which recently added to its ceramic 3D printing portfolio with the acquisition of German startup CerAMing, was one of many AM industry companies that attended formnext 2022 in Frankfurt a few weeks ago. While, last year, the ISO 9001-2015 certified ceramic 3D printer OEM demonstrated its compact entry-level CeraFab Lab L30 3D printer at the show, along with multimaterial parts 3D printed on its CeraFab Multi 2M30 LCM system, this year Lithoz premiered a new and improved medical ceramic material for 3D printed bone replacements.
LithaBone HA 480 is based on the natural mineral hydroxyapatite (HAp), which is the major element of human bone, along with calcium phosphate (CaP). Because of their low thermal conductivity, biocompatibility, and lighter intrinsic weight, ceramics are often used in the medical field for implants and devices, but certain ones are bioresorbable, meaning they can be resorbed by the body. This means that a second surgery—and all the inherent risks associated with opening up a person’s body again—is not necessary. This new material, developed through cooperation with users of the company’s previous bone graft substitute materials, can be used to 3D print patient-specific parts for bone replacements in both the medical and dental fields.
“Compared to LithaBone HA 400 it features much higher wall thicknesses and therefore a considerably better flexibility in geometries,” the Lithoz website states about LithaBone HA 480.
“Due to its similarity to the mineral components of bone, both LithaBone products have optimal biocompatibility and osteoconductivity. LithaBone is completely resorbed and replaced by native bone tissue, so that the implant does not need to be removed after the healing process is completed. This protects growing children in particular from additional painful procedures.”
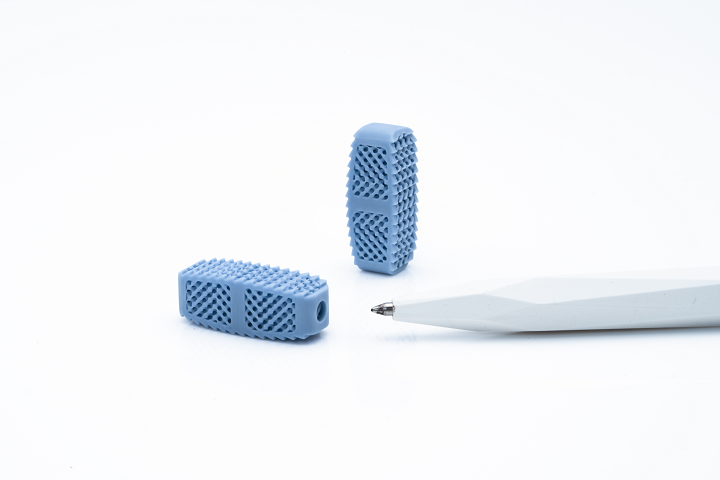
Transforaminal lumbar interbody fusion (TLIF) spinal cage 3D printed out of LithaBone HA 480 on the CeraFab S65 Medical 3D printer.
Lithoz wanted to improve its bioresorbable ceramic bone graft substitute material to make it more economically viable, as well as enable more effective 3D printed bone replacements, and the company says the new material had a great reception from visitors at formnext. That’s why it collaborated with users of its first ceramic bone substitute material to make this new one, taking their feedback to heart in specifying the development goals for LithaBone HA 480. German medical technology company KLS Martin has been using 3D printed bone substitute implants for several years, and is very impressed with the new ceramic material.
“We at KLS have been producing CMF implants for human use on our Lithoz CeraFab printer since 2015, with excellent results in terms of accuracy of fit, tolerability and healing success,” said Adem Aksu, the Director of Development Biomaterials at KLS Martin. “We already have had the chance to work with HA 480 and the results are outstanding: from mechanical properties over higher wall thickness to size and lattice structures, LithaBone HA 480 has convinced us of a considerable improvement compared to its predecessor.”
There are many bone structures in the body, which means that any ceramics used to replace bone must not only be biocompatible and resorbable, but also cover the entire range of bodily structures. The ceramic will dissolve inside the body, while bone will regrow alongside the substitute material’s guide structures, and the optimized design of the structure’s geometry is what makes or breaks an interaction between a bone substitute material and the adjacent human bone and tissues. If the geometry is there, you’re likely to achieve a clinical success, and luckily, 3D printing is great at delivering complex geometries.
Lithoz made several improvements to its original ceramic bone substitute material to develop the new LithaBone HA 480, including more possible geometries, better processability and mechanical properties, and a much higher wall thickness. The original LithaBone HA 400 had a previous maximum wall thickness of <1.6 mm, which has been increased to 10 mm with the new material, and required minimum wall thicknesses have been further decreased, which opens up more applications. Additionally, LithaBone HA 480 features what Lithoz calls a “ten-fold longer shelf life,” which means it can be more readily used for urgent surgeries.
Additional improvements include more precise imaging accuracy of fine structures. A major goal was to provide “a higher level of ultra-precise resolutions” and complex structures with the hydroxyapatite-based material, which goes along with the strengths of the company’s lithography-based ceramic manufacturing (LCM) technology. In addition to an improved depth of cure, LithaBone HA 480 has a decreased overpolymerization, which leads to a much more stable manufacturing process because there’s a simpler selection of build parameters. Finally, experienced users say that 3D printed parts made with the new LithaBone HA 480 ceramic are much easier and faster to clean. This improvement is due to a better binder composition, and helps save time during medical interventions.
3DPrint.com and SmarTech Analysis are hosting Additive Manufacturing Strategies in New York City on February 7-9, 2023. To learn more about 3D printing materials and the technology’s use in the medical field, and network with the industry’s most exciting leaders and companies, you can register for the event here.
Subscribe to Our Email Newsletter
Stay up-to-date on all the latest news from the 3D printing industry and receive information and offers from third party vendors.
Print Services
Upload your 3D Models and get them printed quickly and efficiently.
You May Also Like
3D Printing News Briefs, July 2, 2025: Copper Alloys, Defense Manufacturing, & More
We’re starting off with metals in today’s 3D Printing News Briefs, as Farsoon has unveiled a large-scale AM solution for copper alloys, and Meltio used its wire-laser metal solution to...
Etsy Design Rule Change Reduces Selection of 3D Printed Goods
Online marketplace Etsy has implemented a rule change requiring all 3D printed goods on the site to be original designs. The update to the site’s Creativity Standards states, ¨Items produced using...
Siraya Tech Introduces New Elastomer 3D Printing Materials, Including Foaming TPU
California company Siraya Tech, founded in 2019 with a focus on material science, customer focus, and agility, develops high-quality 3D printing materials that meet the needs of creators, hobbyists, and...
3D Printing News Briefs, April 12, 2025: RAPID Roundup
The news from last week’s RAPID+TCT in Detroit just keeps on coming! That’s why today’s 3D Printing News Briefs is another RAPID Roundup of more exciting announcements from the trade...