In addition to Grid Logic, the most exciting firm presenting at RAPID + TCT 2022 was Quantica. This Berlin-based startup, previously covered here, showcased its new JetPack, a sort of development kit for exploring Quantica’s high-viscosity jetting technology. Because Quantica’s jetting heads have so many potential applications, the JetPack can enable customers to discover the proper pathway for their own use of the technology.
At RAPID, we caught up with the Quantica team, who discussed the new product, as well as the many use cases that high viscosity jetting enables. It was quickly apparent that the company has essentially redesigned the inkjet heads we see in so many additive processes—such as those from Stratasys and Mimaki—and improved them to process a much broader array of materials and fluids. Because it can print with resins 15 times more viscous than others on the market, it can not only produce full-color objects with a variety of stiffness/flexibility properties. It can do so with materials that are actually functional for uses beyond prototyping.
“You can start to put more materials into the fluids to get better properties and functionality,” Jason Remnant, Business Development Director for Quantica, told 3DPrint.com at RAPID + TCT. “So, if you want it to be more conductive, you can include more conductive materials like silver nanoparticles. If you want it to be more abrasion-resistant, you can add that. When we’ve looked at all the different types of properties that you want in 3d printing, if you move to high viscosity, everything becomes possible.”
One such application is the production of dental parts made from multiple off-the-shelf photopolymer resins. Typical vat photopolymerization processes can’t combine disparate materials within the same print job to create a single part, say a denture or model with gum- and teeth-like resins. As a result, the gums are fabricated in one print and the teeth in another. With inkjetting—and specifically with Quantica’s process—a full denture or model can be produced at once, with varying color tones and levels of flexibility.
“The whole point is that actually you want the teeth bit to be more robust and wearing, but you want the gums to be soft,” Remnant said. “So, there’s two different materials, but it would deposit them at the same time. With the existing process, they can make the gums and somewhere else than they make the teeth and then they paint the teeth, then they assemble in this long process. It takes weeks. Doing it this way [with Quantica], you shorten that whole supply chain down, take out a lot of cost, and you can get your dentures maybe the next day or the same day.”
Interestingly, the idea for Quantica didn’t come out of a PhD program or research institute, where we’re used to seeing high-tech startups born. Ben Hartkopp, Co-Founder & Chief Product Officer, told 3DPrint.com that the firm was born out of a basic desire to broaden the materials that can be jetted . After developing the technology for their own purposes, they realized that there was no other 3D printing process on the market capable of what they had achieved. At this point, Quantica’s printheads can eject materials at about 4,500 milli pascals per second at room temperature.
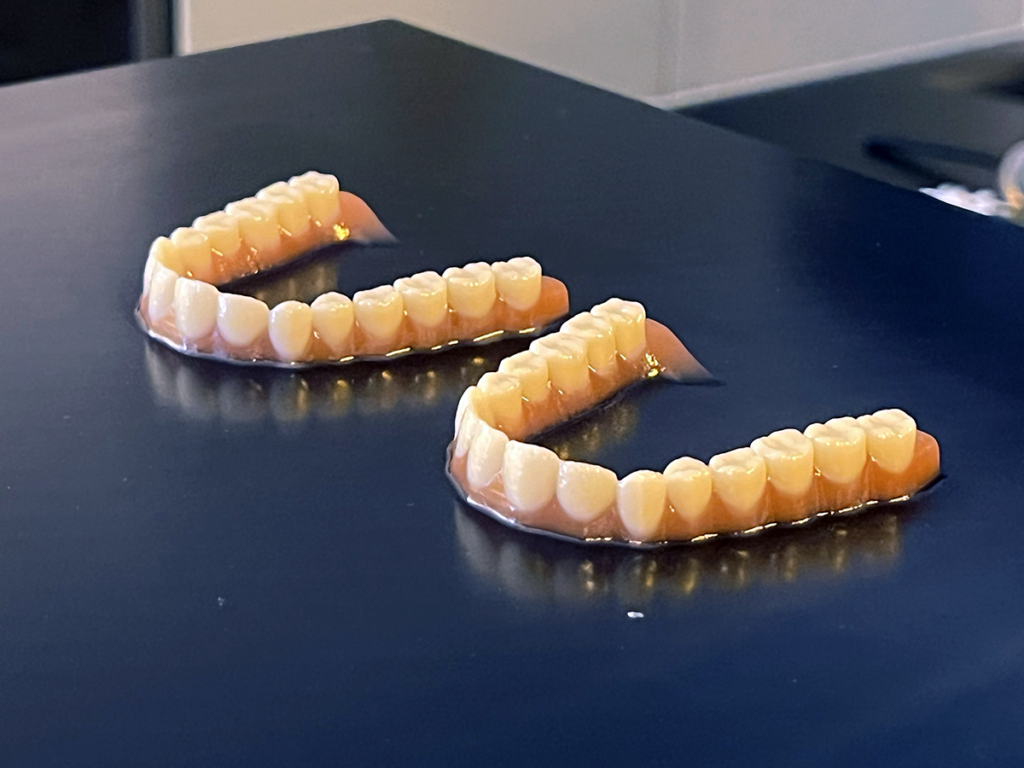
3D printed dentures made in a single process with multiple materials using Quantica’s printhead. Image courtesy of Quantica.
“We’re the first ones to be able to truly print multiple engineering-grade, end-use materials. We’re basically refining this process to be able to deliver true full-color aesthetics in dental and then expanding that to every market essentially,” Hartkopp said. “The exciting challenge that we are currently addressing is exploring which verticals to address first and finding the right material partners,” Hartkopp said.
That’s where the JetPack comes in. JetPack is said to “seamlessly” work with dropwatchers and print test stations so that users can select and validate materials and drive electronics compatibility with Quantica’s printheads. This, in turn, would lead to a new range of materials and printing systems to produce end products.
“It will help us accelerate getting into these markets because there are companies that want to start exploring this technology with their materials and their fluids. In many cases today, many of these markets that are trying to use inkjet have not succeeded properly. They’re doing bits and pieces, but they’ve struggled because they can’t get the right performance out of the fluid. They’re diluting the materials down to get it to work through inkjet technologies,” Remnant explained. “We’re removing that barrier and telling them they can go back to the type of materials they want to use. We have to tell people to go back to using the types of materials they want to use.”
So far, the Fraunhofer Institute for Manufacturing, Engineering, and Automation IPA has become one of the first research partners to use Quantica’s JetPack to develop photorealistic printed objects and applications. However, if you visit the company’s website, you can see that the applications are nearly limitless.
Users can feasibly deposit dielectric, conductive, ceramic, organic, metal materials and more—and not in separate print jobs. These materials can be combined. This means that 3D printed electronics are a possibility, as are organic tissues, or even a combination of both. The JetPack is just the first step in giving users access to Quantica’s high functionality, multi-material 3D printing technology, but they are currently developing a printer that will be announced later this year.
Subscribe to Our Email Newsletter
Stay up-to-date on all the latest news from the 3D printing industry and receive information and offers from third party vendors.
Print Services
Upload your 3D Models and get them printed quickly and efficiently.
You May Also Like
3D Printing News Briefs, July 2, 2025: Copper Alloys, Defense Manufacturing, & More
We’re starting off with metals in today’s 3D Printing News Briefs, as Farsoon has unveiled a large-scale AM solution for copper alloys, and Meltio used its wire-laser metal solution to...
Etsy Design Rule Change Reduces Selection of 3D Printed Goods
Online marketplace Etsy has implemented a rule change requiring all 3D printed goods on the site to be original designs. The update to the site’s Creativity Standards states, ¨Items produced using...
Siraya Tech Introduces New Elastomer 3D Printing Materials, Including Foaming TPU
California company Siraya Tech, founded in 2019 with a focus on material science, customer focus, and agility, develops high-quality 3D printing materials that meet the needs of creators, hobbyists, and...
3D Printing News Briefs, April 12, 2025: RAPID Roundup
The news from last week’s RAPID+TCT in Detroit just keeps on coming! That’s why today’s 3D Printing News Briefs is another RAPID Roundup of more exciting announcements from the trade...