Early in 2021, a multidisciplinary team designed and tested the world’s first 3D printed rocket pad prototype for lunar missions. Built at a Texas Military Department location in Camp Swift, the project leveraged one of the most advanced technologies in additive construction to establish one of the building blocks for a sustainable off-Earth ecosystem. The meticulously designed pad resulted from months of hard work from a group of ten undergraduate students from U.S. colleges and universities who are part of NASA’s so-called Artemis Generation, the next group of explorers that will take part in the upcoming U.S.-led international human spaceflight program.
Together with experts from NASA, the Texas Military Department, and additive construction company ICON, the students took their Lunar PAD (Lunar Plume Alleviation Device) from concept to finished prototype. We take a deep dive into the creative process of one of the most innovative 3D printed constructions for space exploration with members of the student team behind the design and ICON’s rocket pad project lead and mechanical engineer Dana Wieland.
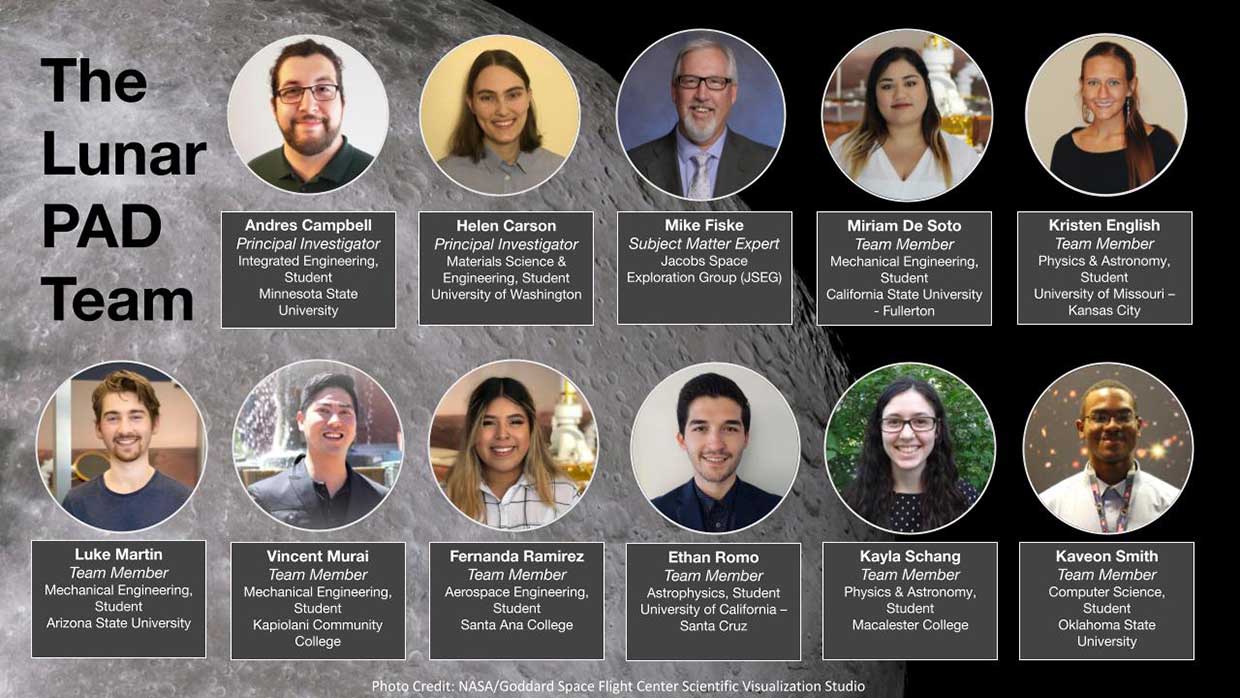
Conceived in 2019 by the students during a 12-week NASA training course called NASA Proposal Writing and Evaluation Experience (NPWEE), the rocket pad is one of the landing technologies that NASA anticipates will be needed for planned missions in the next decade, as spacecraft will attempt to land on the Moon. The team worked endlessly to tackle many technical design aspects over the past two years and won a competition. After a lot of research and talking with subject-matter experts, they used the $10,000 award to finalize the pad’s design, according to lead innovator Vincent Murai, who recently graduated as a mechanical engineer from the University of Hawaii.
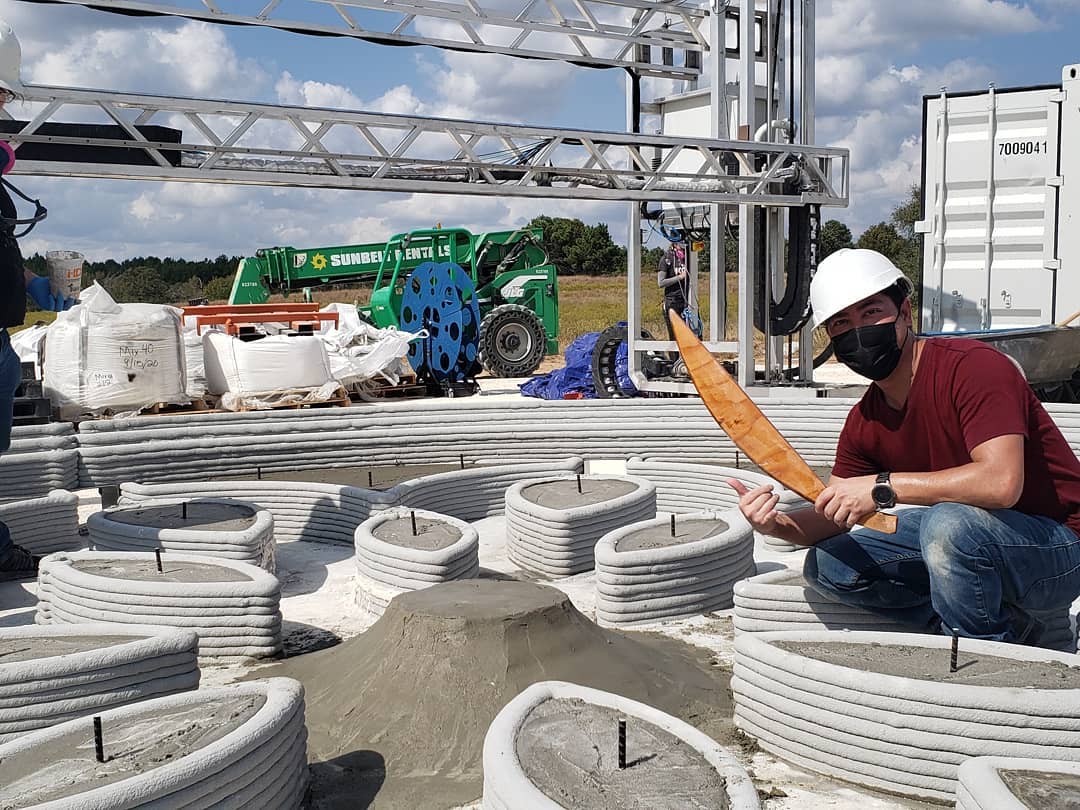
After the final design was chosen, ICON – a partner in NASA’s Artemis program – was selected to help them build a subscale prototype using cement-based material and a gantry print system. “A static fire test was then conducted on the Lunar PAD with an M3 Class rocket motor,” stated Murai. The design of the pad was unlike anything ICON had ever printed before. The firm worked with the student team to develop creative ways to execute all of the critical elements of the pad and weed out any details that would not contribute to the experiment’s overall success.
Wieland said 3D printing offered design freedom unseen in mainstream construction and building materials. 3D printed in October 2020, the Lunar PAD prototype is 20 feet in diameter and over 1.6 feet tall. A full-scale pad on the Moon would probably require roughly 100 meters in diameter, but, for that to happen, the students believe the project needs a much larger group of experts and budget.

For the prototype build, the team needed to ensure a particular exhaust flow behavior, specifically sending exhaust upward and outward and minimizing the amount of dust lofted during launch and landing. This is mainly because the design is unlike a normal landing pad, usually characterized by its flat or solid surface, as described by team member, physicist, and astronomer Kayla Schang from Macalester College in Minnesota. Instead, the PAD has space in the middle and some height, with openings in the surface that serve to diffuse the exhaust outwards as the craft is landing.
Like all current and future printing projects, ICON used a proprietary concrete formula called “lavacrete,” described as a “well understood, affordable, resilient material with a high thermal mass.” Wieland said the material used for the launch pad needed to be resilient because the prototype was created to replicate “what something similar might look like when 3D printing with materials found on the Moon.”
In fact, the team’s original design envisioned printing with a lunar regolith-based concrete. However, Schang said they had researched other materials closer to the Moon’s regolith, like sulfur concrete for 3D printing, as well as different binders that could be mixed with concrete aggregate to simulate an interplanetary material, such as magnesium oxide-based binders. Still, they were all deemed less suited to lay down or extrude through the nozzle.

For Andres Campbell, principal project investigator and senior engineering student at Minnesota State University, aside from the material requirements for the design and the type of additive manufacturing process needed to create it, one of the biggest challenges when pursuing the rocket pad concept was a lack of constraints. “Designing a pad for various potential landers that we still don’t know much about open the problem up quite a bit, leaving several variables to consider that are still largely unconstrained.”
After proving that the pad can withstand the strain, temperatures, and pressures of the flow dynamics, the team’s goal is to scale it to any size for future use on any planet, not just the Moon. Murai said NASA is pushing their project because they need this technology for the heart of the lunar mission. Most of the resources are going to the development of the human lander system (HLS) and commercial lunar payload platforms, he explained. In contrast, the resources for rocket pad designs are much more limited, which is disproportionate to their importance.
But no matter how many limitations they faced or how much research they required to come up with their final proposal, the students are proud that their design was the first successfully hot-fire-tested 3D printed rocket pad. According to Campbell, the fact that they are “breaking ground” with their innovative creation “adds a layer of mystery and challenge to what we are doing.” Mainly because there are no previous references to what this team is trying to do. Whether this project will reach the Moon someday is not entirely clear. For now, the students are analyzing the data from their work and continuing to do more tests, including an extreme temperature test and testing the properties of materials like regolith.
Hoping to use the knowledge gained from the construction process towards a full-scale design for the Moon, Mars, and beyond, the students said they are proud of their “footprint in the history of future space exploration.” Although they are eager to continue working on the project together, the team members are already moving on to graduate schools, jobs, and other projects. Still, they claim that having been part of this experience is very rewarding in and of itself, and more so knowing that someday, their proposal could become the foundation for automated, sustainable, and 3D printed landing technologies.
Subscribe to Our Email Newsletter
Stay up-to-date on all the latest news from the 3D printing industry and receive information and offers from third party vendors.
Print Services
Upload your 3D Models and get them printed quickly and efficiently.
You May Also Like
Reinventing Reindustrialization: Why NAVWAR Project Manager Spencer Koroly Invented a Made-in-America 3D Printer
It has become virtually impossible to regularly follow additive manufacturing (AM) industry news and not stumble across the term “defense industrial base” (DIB), a concept encompassing all the many diverse...
Inside The Barnes Global Advisors’ Vision for a Stronger AM Ecosystem
As additive manufacturing (AM) continues to revolutionize the industrial landscape, Pittsburgh-based consultancy The Barnes Global Advisors (TBGA) is helping shape what that future looks like. As the largest independent AM...
Ruggedized: How USMC Innovation Officer Matt Pine Navigates 3D Printing in the Military
Disclaimer: Matt Pine’s views are not the views of the Department of Defense nor the U.S. Marine Corps Throughout this decade thus far, the military’s adoption of additive manufacturing (AM)...
U.S. Congress Calls Out 3D Printing in Proposal for Commercial Reserve Manufacturing Network
Last week, the U.S. House of Representatives’ Appropriations Committee moved the FY 2026 defense bill forward to the House floor. Included in the legislation is a $131 million proposal for...