As part of the Artemis Generation, a team of undergraduate students from ten U.S. colleges and universities has designed and tested the world’s first 3D printed rocket pad for lunar missions. The reusable subscale prototype rocket landing and launch pad was 3D printed using a cement-based material and a gantry print system developed by revolutionary construction company ICON at a Texas Military Department location in Camp Swift. The novel concept could enable safe and reusable landing and launch required for sustainable lunar exploration.
3D printed in October 2020, the Lunar PAD, short for Lunar Plume Alleviation Device, is 20 feet in diameter and over 1.6 feet tall. Its petal-like channel design was created to solve the problems caused when the force of an engine’s powerful exhaust meets the dusty lunar surface, known to cause a wide range of issues. The carefully outlined central cone, channel dividers, and exit vents help disperse a rocket’s exhaust upward and outward, minimizing the amount of dust lofted during launch and landing.
The PAD consists of essentially two layers: a “roof” where a rocket launches from or lands on, and a series of channels below to safely redirect the exhaust. Slits in the roof allow exhaust from rockets to travel into the carefully designed channels that direct the exhaust flow to the edge of the launch pad, where it exits through specialized vents. The central cone and dividers support the rocket and pad roof’s weight, while a wall surrounds the structure, capturing any lunar dust particles that become mobilized during a launch or landing.
It took ICON’s crew seven hours to print the exterior shell and internal framework of the launch pad and 14 hours to print the infills, including the thick “roof” or deck of the pad that the rocket sits on. For the task, the team relied on the company’s proprietary Vulcan industrial construction 3D printer—a gantry-based platform operated through an integrated tablet that enables users to intuitively and easily monitor and control the machine—along with its unique Lavacrete material to precisely pour the concrete that fills the formwork.
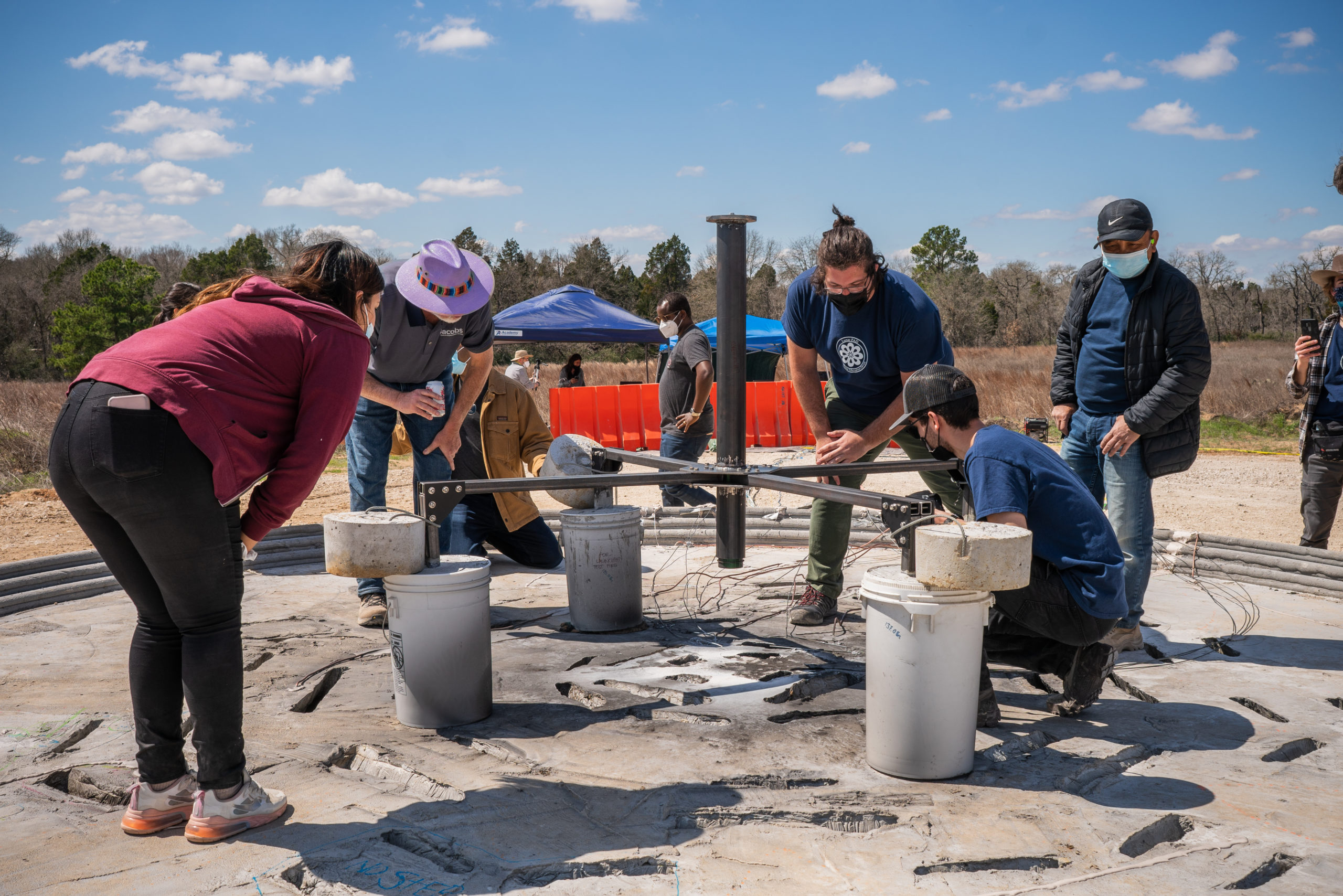
Students build a subscale prototype of a reusable lunar launch and landing pad at Camp Swift in Bastrop, Texas, in October 2020. Image courtesy of ICON.
The vision of a landing pad solution was conceived by the students during the 2019 NASA Proposal Writing and Evaluation Experience (NPWEE), a 12-week training course crafted by NASA’s Marshall Space Flight Center Chief Technologist John Dankanich. As part of the Lucy Student Pipeline Accelerator and Competency Enabler (L’SPACE) Academy, the course helped expand and diversify the pool of high-quality, selectable proposals for new concepts and technologies that meet NASA’s needs.
The team won, allowing them to present to Marshall experts in June 2020 at a virtual Design Readiness Review and to secure funding to print and test a subscale version of the pad. Later, they submitted a paper on the Lunar PAD concept in January 2021 at the American Institute of Aeronautics and Astronautics‘ 2021 SciTech Forum, suggesting that their idea relies on in-situ resource utilization (ISRU) methods and technologies to minimize launch mass and enable previously unimagined structures.
“The proposal addressed a technology pain point, as the project enables a safe and reusable landing pad required for sustainable lunar exploration. The team worked many hundreds of hours, engaged NASA subject matter experts, and went from concept formulation to a preliminary design. They then turned that design into reality with the subscale construction, all in a few short months,” said Dankanich.

An internal view of the subscale, 3D printed lunar launch, and landing pad created with ICON’s Vulcan system. Image courtesy of ICON.
Continuing its mission to create off-world construction, ICON helped the students build the pad prototype. One of the leaders advancing construction technologies, ICON has been known to use 3D printing robotics, software, and advanced materials to change the paradigm of home building on Earth and beyond. With a division of the company already dedicated to space constructions and a contract with NASA to begin research and development of a space-based system that could support future exploration of the Moon, ICON has been aiming to 3D print off-Earth for a long time.
This latest project between ICON, NASA, and the Texas Military Department is one of the Austin-based firm’s milestones. To test the Lunar PAD design and its ability to be 3D printed, the team has been working with experts from Marshall’s Moon to Mars Planetary Autonomous Construction Technologies (MMPACT). A project that aims to develop and demonstrate on-demand capabilities to protect astronauts and create infrastructure on the lunar surface via the construction of landing pads, habitats, shelters, roadways, berms, and blast shields using lunar regolith-based materials.

Aerial view of the subscale, 3D printed lunar launch, and landing pad created with ICON’s Vulcan system. Image courtesy of ICON.
In March 2021, MMPACT’s project lead, Mike Fiske, and the Lunar PAD team returned to Camp Swift to see how their prototype would hold up under the extreme high-temperatures and stresses created by a rocket engine. The Sounding Rocketry Team at Texas A&M University assisted with hot-fire testing and the rocket motor fabrication. Based on preliminary analysis and results from instrumentation integrated into the pad during printing to measure temperature, strain, and exhaust flow behavior, the lunar pad performed as designed.
“It has been a pleasure working with these students over the last year and helping to advance the state of the art in the planetary launch and landing pads,” said Fiske, an in-space manufacturing engineer with Jacobs Engineering Group in Marshall’s Space Technology Development Branch. “The results from this project contribute strongly to our future knowledge of lunar launch and landing pads and get us one step closer to lunar infrastructure.”
https://youtu.be/dOKKkV-30dE
This next generation of explorers, dubbed by NASA as the Artemis Generation Students, will ensure that the U.S. continues to lead space exploration and discovery. From NASA’s Artemis Student Challenges to interacting with astronauts, NASA is engaging young minds in space-related endeavors. The results have been successful, more than 12,000 people have applied to join NASA’s Artemis Generation astronauts to help the agency return humans to the moon and reach outward to Mars. Dozens of student teams have built off-world mining robots, fabricate and launch high-power rockets, and even spacesuit user interface technologies. With so many exciting milestones ahead for space travel and exploration, the possibilities for innovative creation are endless, and NASA is taking the lead to thriving in orbit.
Subscribe to Our Email Newsletter
Stay up-to-date on all the latest news from the 3D printing industry and receive information and offers from third party vendors.
Print Services
Upload your 3D Models and get them printed quickly and efficiently.
You May Also Like
3DPOD 260: John Hart on VulcanForms, MIT, Desktop Metal and More
John Hart is a Professor at MIT; he´s also the director of the Laboratory for Manufacturing and Productivity as well as the director of the Center for Advanced Production Technologies....
Making Space: Stratasys Global Director of Aerospace & Defense Conrad Smith Discusses the Space Supply Chain Council
Of all the many verticals that have been significant additive manufacturing (AM) adopters, few have been more deeply influenced by the incorporation of AM into their workflows than the space...
3DPOD 259: AM at Stratasys with Rich Garrity, Chief Business Unit Officer
Rich Garrity is the Chief Business Officer of Stratasys. Rich shares Stratasys´ vision and future with us. We talk about machines, applications, clients, and the market in general. What technologies...
Stratasys & Automation Intelligence Open North American Tooling Center in Flint
Stratasys has opened the North American Stratasys Tooling Center (NASTC) in Flint, Michigan, together with automation integrator and software firm Automation Intelligence. Stratasys wants the new center to help reduce...