In the last few years, the private space industry has created a cost-competitive ecosystem as the boundaries of space exploration expand. While a growing number of private firms are heavily engaged in space launches and spaceflight, others are working “behind the scenes” to develop processes, applications, and technologies that will enhance access to space for government agencies and private companies. In Albuquerque, New Mexico, a startup is pioneering game-changing, disruptive technologies, additive manufacturing (AM) processes, and nanomaterials for space, aerospace, and defense applications, including survivable coatings and mirrors, seeker telescopes, and windows for high energy lasers (HELs).
Founded in 2016 by engineer William Goodman, Goodman Technologies (GT) relies on 3D printing processes and laminate composites to produce parts from one inch to one meter for the most extreme environments on- and off-Earth, like space, nuclear, and cryogenic- temperatures. 3DPrint.com spoke with Goodman about how AM technologies can help create critical space parts, the future of nanostructures, and the role of startups in the commercialization of space.
There have been remarkable innovations in space technologies in recent years, so much so that within a decade, the space industry has turned to AM for launch vehicles and satellite parts traveling to low Earth orbit (LEO) and higher orbits, like geostationary (GEO) and Cislunar. Unquestionably, the space industry is growing, and private investment in space startups has skyrocketed while collaborations with 3D printing manufacturers are expanding.
Goodman believes the new space community is in a stage of emergence with many astonishing parallels to the Gold Rush and Transcontinental Railroad that span roughly twenty years, starting in the mid-1840s when entire ecosystems were developed to support the overlapping mining and transportation industries. The new space ecosystem is growing every day as exploration, manufacturing, natural resource management and harvesting, transportation, lodging, and other applications lead many entrepreneurs to create startups that will help this industry grow, he explained.
Manufacturing spacecraft remained pretty much the same for many decades. However, as demands increase and the planned crewed missions to the Moon, Mars, and beyond seem closer than ever before, space developments are continually being disrupted. Today, GT uses aspects of robocasting, also known as robotic material extrusion, an AM technique analogous to Direct Ink Writing, to print custom-engineered nanopastes, which then undergo serial curing, joining, and pyrolysis or infiltration steps to create complex monolithic 3D structures.
“We are doing this through hardware and software modification and customization of Delta-style clay printers. With this and our proprietary Z-process, we can produce optical substrates for mirrors and structures for telescopes, armor, and thermal protection systems that are technical ceramic nanocomposites.”
GT has won dozens of government contracts in armor, shielding, and CubeSats, by working in nanocomposites, particularly ceramic-based, low-Z, low atomic number of materials for the space radiation environments as well as high-temperature materials for things like thermal protection systems, leading edges, hypersonics, optical systems, and satellites. Since its inception, the company has engaged in some of the most exciting research developments for government agencies, such as using its patent-pending disruptive nanoceramic materials to provide solutions for deep cryogenic temperatures, nuclear and space effects environments challenges, including space structures, space optical and optical/radio frequency systems, shielding, armor, and thermal protection.
By far, Goodman said the most challenging project was making the world’s largest optical substrates in silicon carbide for two highly competitive NASA Phase II projects. His team created three grades of materials over a two and a half-year span before finally deciding to use a patent-pending electrical conductive nanoceramic composite silicon carbide material using novel processes. After hundreds of experiments, the company managed to prove the feasibility of 3D printed silicon carbide composites for ultra-lightweight mirrors and structures for large space optics and laser communications telescopes (lasercoms), which are of interest to several NASA centers, like the Jet Propulsion Laboratory (JPL), and are planned for use in Cislunar, deep-space and planetary missions with orbiter-landers.
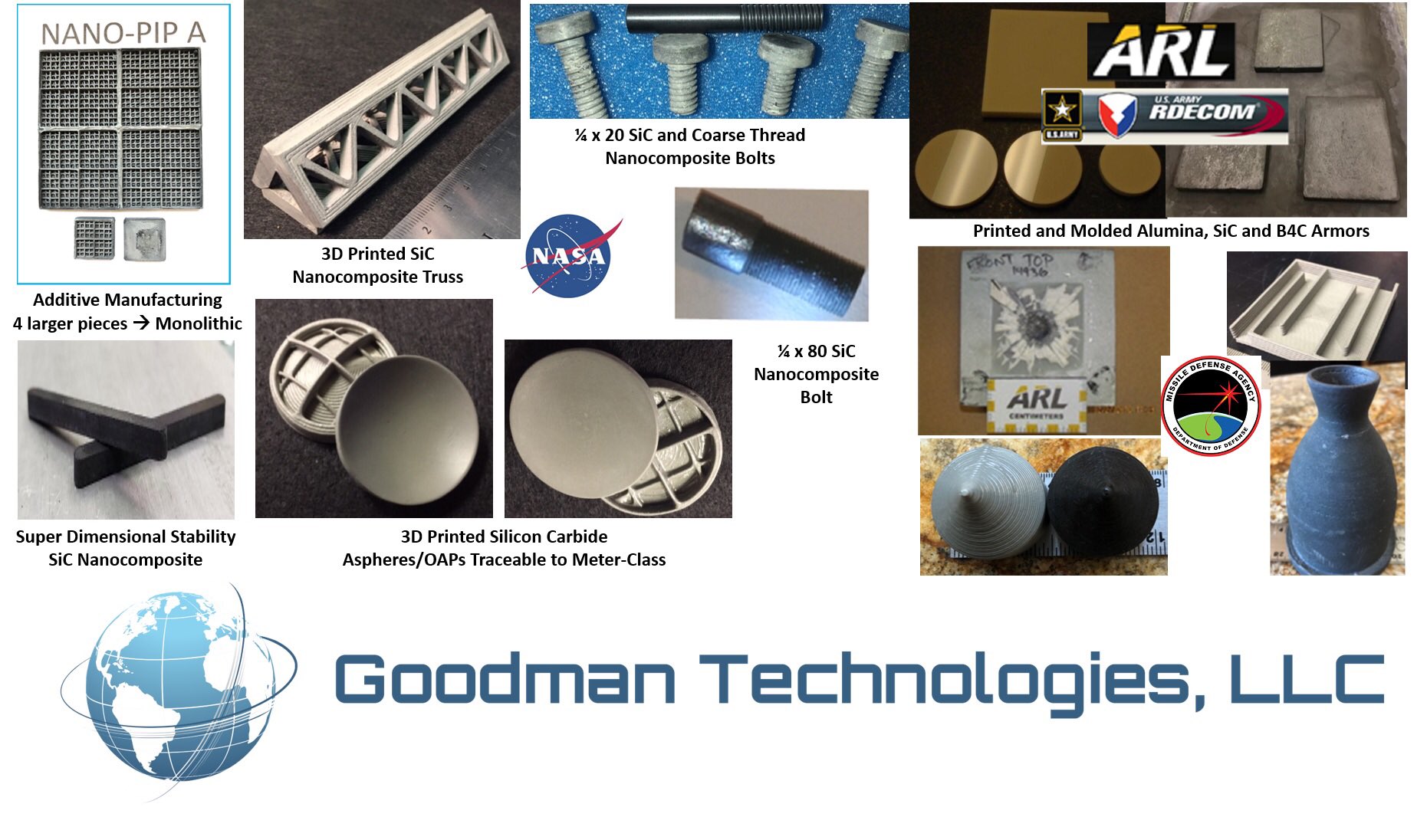
A few of Goodman Technologies’ components for space applications. Image courtesy of Goodman Technologies.
Although pioneering disruptive materials for harsh environments is challenging, the executive says nanocomposites created by his company are multifunctional, which means they are lightweight, dimensionally stable, and radiation tolerant. As a result, they can serve as structure, radiation shielding, and thermal heat pipe for space systems, which translates to lower mass and cost to orbit. For example, the mirrors for space surveillance systems that GT created for LEO had to survive high energy electrons, an exoatmospheric manmade radiation event, while also going in and out of light and darkness multiple times a day. But it’s not an easy process; it usually takes several years of design, analysis, numerous different types of ground tests, and spaceflights to fully qualify mirrors and optical coating.
Beyond a passion for entrepreneurship and coaching fellow space enthusiasts who want to create startups, Goodman is an engineer at heart, with over 30 years of experience developing lightweight, dimensionally stable mirrors and optical instrument systems for NASA and the U.S. Department of Defense (DoD).
“I wanted to dovetail off of this experience and use new nanomaterials and emergent manufacturing processes to create all-new material systems with never before seen properties.”
Now that his company is becoming well known within the space industry, Goodman is wondering about the future of 3D printing in space applications and the next development that could change space exploration for future generations: “Looking forward, I believe that the shielding required to survive space radiation outside of the magnetosphere will be key.” In fact, the useful career lives of astronauts are currently determined by the total dose of radiation they receive. However, outside Earth’s magnetic field, cosmic rays would bombard our bodies and even damage our DNA, increasing the risk of cancer and other illnesses. That is why developing nanotechnology for shields is one of Goodman’s priorities.
As for 3D printing, he expects in-space additive manufacturing to be the pivoting point to revolutionize space exploration. “3D printing in space will be prevalent because, for example, in the case of mirrors for NASA observatories, you need only one-sixth of the mass of the material to manufacture the mirrors and structures on orbit than you would on Earth. That extra mass is only there to survive launch loads. Likewise, using off-Earth natural resources like regolith, on the Moon and Mars will allow the manufacture of shielded structures to extend the career lives of future ‘Extra Terrestrials.’”
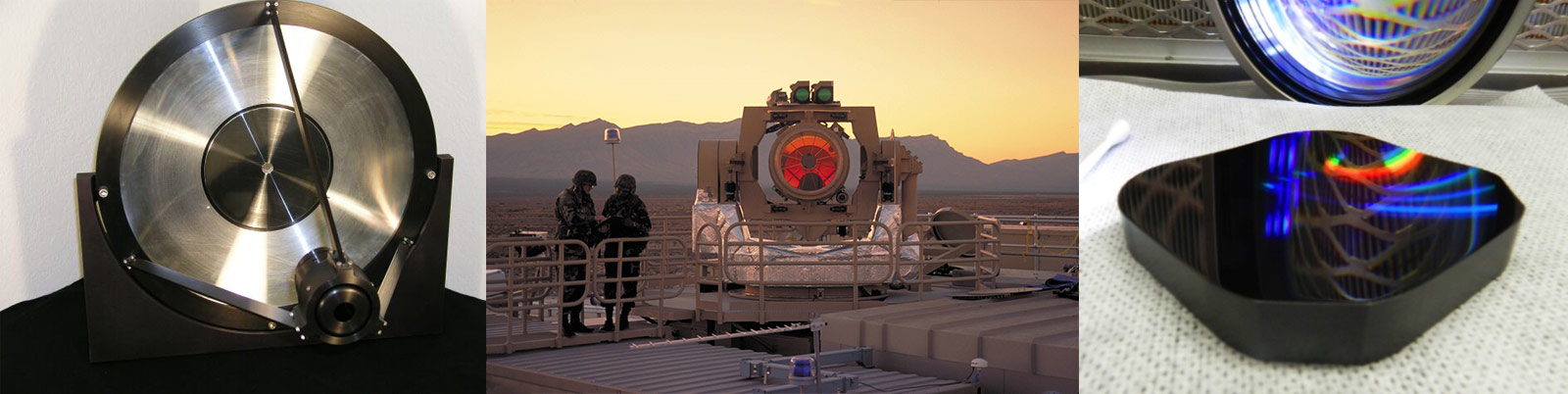
Goodman Technologies creates optical systems for NASA and other agencies. Image courtesy of Goodman Technologies.
For now, however, one of the main challenges to unlock the full potential of 3D printing in space is money, says Goodman. He believes that GT and other businesses have perfectly useful technology for in-space manufacturing right now. Still, the investment required to build the manufacturing factories does not match the timing for the marketplace from the perspective of investors’ exit. For example, it would cost $30 million for GT to develop a small factory on-orbit, says the expert. “The New Space market is being funded by governments around the globe, institutional investors, billionaires, and even crowdfunding. A new dedicated group of space investors is emerging right now, and GT is talking to a few entities about this undertaking.”
Hopefully, we will hear more about GT’s futuristic and innovative 3D printing factory off-Earth. But for right now, Goodman continues to focus on revolutionizing space technologies and is currently developing GT Nano, an investor-ready spin-off company described as a “factory of the future” dedicated to the manufacture of nanocomposites and nanoforested materials that is intended to go public.
Subscribe to Our Email Newsletter
Stay up-to-date on all the latest news from the 3D printing industry and receive information and offers from third party vendors.
Print Services
Upload your 3D Models and get them printed quickly and efficiently.
You May Also Like
The Market and Industry Potential of Multi-Material 3D and 4D Printing in Additive Electronics
Additive manufacturing leverages computer-based software to create components for products by depositing either dielectric or conductive materials, layer by layer, into different geometric shapes. Since its birth in the 1980s,...
3DPOD 262: Bio-inspired Design for AM with Dhruv Bhate, Arizona State University
Dhruv Bhate is an associate professor at Arizona State University. There, he looks at structures, materials, and design. Previously, he worked at PADT as well as in the semiconductor and...
3DPOD 261: Tooling and Cooling for AM with Jason Murphy, NXC MFG
Jason Murphy´s NXC MFG (Next Chapter Manufacturing) is not a generalist service; instead, the company specializes in making tooling. Using LPBF and binder jet, the company produces some of the...
3DPOD 260: John Hart on VulcanForms, MIT, Desktop Metal and More
John Hart is a Professor at MIT; he´s also the director of the Laboratory for Manufacturing and Productivity as well as the director of the Center for Advanced Production Technologies....