Now that we’ve looked at how 3D printing is being applied to bicycle production, what technologies can be used for what components, who is likely to rely on 3D printing, and what drivers there would be for the industry, we need to ask: why use 3D printing at all?
Or to frame it better yet: What unique things can 3D printing do for a bike company and its customers? A lot of individuals turn to 3D printing for the fun or excitement. But, when 3D printing succeeds in fundamentally disrupting an industry, there are always advantages for manufacturers and their customers. We’ve already shown you some key business drivers that could lead to broad spectrum 3D printing adoption. But, can we foresee any marketable improvements to bicycles that 3D printing and 3D printing alone can do?
Mass Customization
In this case, the most obvious use for the technology is in mass customization. Mass customization allows a customer to choose a style or easily produce something that conforms to their body, which can increase their affect for it or its utility, while getting the manufacturer a higher profit for the item. Mass customization in bicycles will be the most impactful on these fronts:
- Frame geometry
- Crankshaft and other motion-related geometry
- Handlebars and grips
- Optically customized items
- Seats
- Safety gear and helmets
Frame geometry could be customized by printing an entirely custom frame or by making customized lugs for use with custom-cut tubes. This can in a relatively inexpensive way manufacture custom frames in which the size and geometry is adapted to the user very specifically. This could be done with other technologies or by hand to a certain extent. But, the automated design and calculation coupled with automated manufacturing could make 3D printing the easiest way to perform this well and repeatedly.
Crankshafts, pedals, and even gears could be entirely and completely customized to the individual rider, as well. Your motion and body could be used to make individual geometries for these components, in such a way that the entire motion of the vehicle is made optimally for just you not everyone. There could be a Mary Cruise gear, a Mary accelerate-to-sprint gear, a Mary full-sprint gear, all optimized to her and her riding style. You could even optimize groupsets for a single stage or part of a race.
Using Twikit in combination with HP Multi Jet Fusion polypropelyene or TPU, you could make customized handlebars and grips just for you. Based on a 3D scan, you could create an optimal grip for your hand. Different grips could be made for different rider positions in various portions of a run to optimize your experience.
You could put your signature, drawing, shape, favorite item on top of your bike. Or your shifter could come with your logo on it or your frame could have your decal on it. Customized optical components are to be used in automobiles. May they also find widespread applications in bicycles?
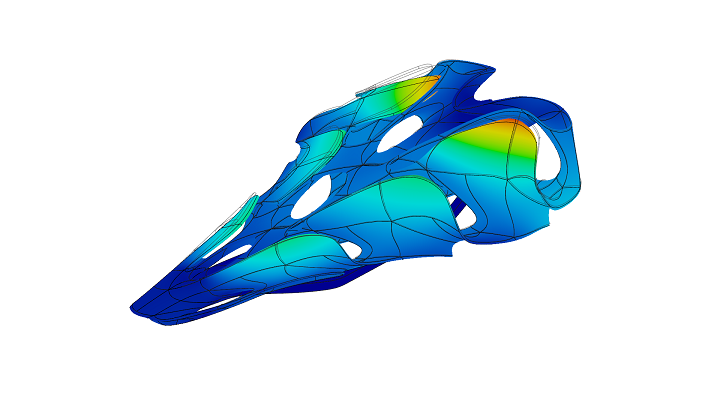
Nyxo bike saddle displacement
If you’ve ever ridden for long duration, you’ll realize that the seat is crucial. Mass-customized seats have been attempted by Specialized and others, but no breakthrough components have been offered to consumers at scale as of yet. Ideally, we could make a gradient seat or a saddle that has variable density at every point. A 3D scan could be the basis of a seat made just for you. For large multi-day races, like the Giro and Vuelta, professional teams could even make new saddles for every day of the stage to disperse weight and potential blisters and make riders more comfortable across many weeks of touring.
Light-weighting
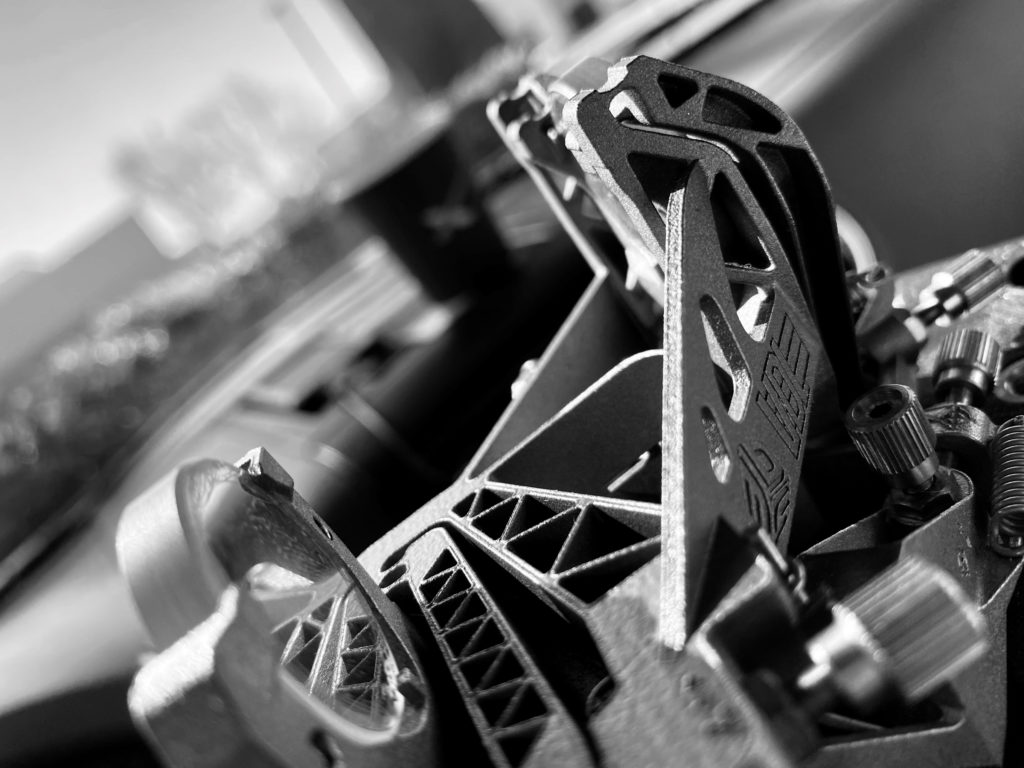
Lightweighting semiconductor components and advanced motion mechanisms reduces inertia and improves lithography and wafer processing machine speed and uptime. (Part courtesy of VDL)
Uniquely 3D printing could be used to lightweight almost any component of the bike. We could redesign every individual component and reduce its weight by 20 to 50 percent to specifically produce a lighter part or region of a bike, or the bicycle as a whole.
Dampening
With specifically designed components, vibrations, feedback, “road noise”, shocks, uneven surfaces and more can be dampened. Bicycles can be made to be much more comfortable and one could ride them longer with more comfort. Energy from riders could also be directed and used more effectively. These components can also be integrated into existing ones: e.g., a seat post or handlebars that dampens vibration. This is a relatively new area to which to apply additive, but it would make for a huge leap forward in rider comfort.
New Suspension Components
RockShox and other components have been improving rides for a long time now. Domin is working on automotive hydraulic suspension parts for Aston and others that could also be used to create higher comfort on bicycles in a low-weight, low-mass package using 3D printed hydraulics.
Completely New Derraileur or Other Groupset Parts

Examples of amorphous demo parts fabricated in an EOS system [Image: Exmet AB]
So, perhaps it would be a bit optimistic to ask them to take to new materials. But, 3D printed bulk metallic glass components could mean completely lubricant free gearboxes that are ultralight and maintenance-free, as well as high-performance. Companies such as Heraeus and Exmet are focusing their attention elsewhere, but the performance improvement would be significant.
Subscribe to Our Email Newsletter
Stay up-to-date on all the latest news from the 3D printing industry and receive information and offers from third party vendors.
You May Also Like
3D Printing Unpeeled: Biofuel Waste to Filament & Sustainable Photopolymers
I can’t ever remember a day with so many potentially high impact news stories have come out. In one story, we all know that there are problems with the safety...
Finnair Hires AM Craft to 3D Print Plastic Parts for Aircraft Interiors
Riga-based AM Craft, a supplier specialized in 3D printing aviation components and certified under EASA Part 21G, announced a significant achievement today. The company will assist in upgrading Finnair’s A320...
3DPOD Episode 198: High Speed Sintering with Neil Hopkinson, VP of AM at Stratasys
Neil Hopkinson, a pioneering 3D printing researcher, played a pivotal role in developing a body of research that is widely utilized today. He also invented High Speed Sintering (HSS), also...
3D Printing Webinar and Event Roundup: May 12, 2024
Webinars and events are picking up in the AM industry this week! ASTM International continues its Professional Certificate Course and Stratasys continues its advanced in-person trainings, while 3D Systems is...