Colombian-based 3D printer manufacturer Fused Form has introduced a new large-format pellet extrusion 3D printing system. The FF Pellet 600+ is the first commercially available industrial pellet printer manufactured in the country, and like its international counterparts, it lowers material costs and production time while also expanding the variety of plastics that can be printed. Expecting to accelerate the adoption of large-format industrial additive manufacturing (AM) in Latin America, company Co-Founders Lissy Rodríguez and Juan Camilo Blanco have developed a competitively priced platform with an automatic pellet feeder, stable nozzle flow, and increased print speeds.
Fused Form has designed a large-dimension, versatile 3D printer with an automatic feeder pellet tank that relies on sensors to ensure pellets are continuously fed into the machine. The powerful extruder works with any plastic pellets as well as recycled material, making it potentially sustainable. Moreover, for big and fast prints, the extruder uses a nozzle of up to 1.2 mm in diameter and smaller nozzles for higher-quality prints. Thanks to its large build size, the FF Pellet 600+ can reach print volumes of up to 600 cubic millimeters without having to worry about printing multiple parts, which would require post-printing assembly and would take weeks instead of days to finish.
The first multi-material FF Pellet 600+ 3D printer made its way to the Department of Mechanical Engineering at the University of Wisconsin-Madison (UW-Madison), where polymer engineering expert Tim Osswald is leading a team of graduate students in AM research at the university’s Polymer Engineering Center (PEC). One of the oldest and most renowned polymer engineering research and educational programs in the United States, the UW-Madison PEC is Co-directed by Osswald, the university’s Kuo K. and Cindy F. Wang Professor of Mechanical Engineering.
Many local and international companies have their roots in plastics undergraduate and graduate education at UW–Madison, where faculty wrote a number of the accepted textbooks in use worldwide on polymer engineering; Osswald alone has authored over 12 books. Every semester, more than 100 students uniquely knowledgeable in plastics graduate from the Department of Mechanical Engineering. In addition to conducting basic polymer research, the PEC works with dozens of businesses, big and small, on materials testing and product development and uses Fused Form printers at its AM lab, along with a wide range of machines from several 3D printer manufacturers.
Thanks to the exclusive extrusion system of the new FF Pellet 600+, users can print materials in large sizes without having to purchase filament, which is basically a product of plastic pellets getting re-melted and extruded into another shape. This represents a great advantage for the industry. According to Rodríguez, customers can buy the pellets directly from wholesalers, a significant saving of between 10 and 20 times the filament cost in Colombia. Then, the pellet granules are fed into a barrel with three heat zones. Inside of this barrel, a pneumatic motor drives the pellets through to be extruded by the nozzle.
“We can drastically increase the printing flow with the FF Pellet 600+, capable of printing larger parts three times faster than with filament printers. Whether PLA, ABS, or other polymer feedstock, the pellet printer allows a larger variety of material choices, including customized multi-materials,” Rodríguez told 3DPrint.com. “So far, we have seen a great interest from local furniture and automotive businesses as well as research institutions worldwide, but we believe that just about any company that needs to print large industrial-grade parts can use our pellet extruder.”
Competitively priced at $17,000, the platform could be an excellent choice for companies that can’t afford large pellet printers in the $50,000s or more. Although the industrial 3D printing market has grown in Latin America, many businesses, especially startups, are still weighed down by smaller budgets and rely mainly on imported devices and materials. The region may appear promising in terms of AM adoption, but there are still several limitations that hold it back, including a complex bureaucracy, high costs, and limited tax incentives for local manufacturers.
Fused Form is one of the pioneering AM companies in Colombia and has been producing printers for ten years, from fused filament fabrication (FFF) desktop systems to large industrial machines. However, Rodríguez suggested that the region has been a bit of a challenge since it is more primary-resource intensive, focused mainly on agricultural commodities exports, and not so much on manufactured goods and technological innovation. Moreover, most 3D printers in the region are imported from the U.S. or Europe, making companies like Fused Form one of the local market disruptors.
“Colombia and Chile are at the forefront of 3D printing in Latin America, both in 3D printer adoption and development,” said Blanco. “Unfortunately, in Latin America, 3D printing is not rooted in product development, and that is something we are currently working on with a lot of companies, helping promote the technology to accelerate manufacturing in our local industries. We see great potential for our products in countries that are showing interest in investing in AM technology, like Ecuador and Peru, mainly due to the low cost of our pellet machine and the similarities in the language and culture, which are usually an entry barrier for big corporations.”
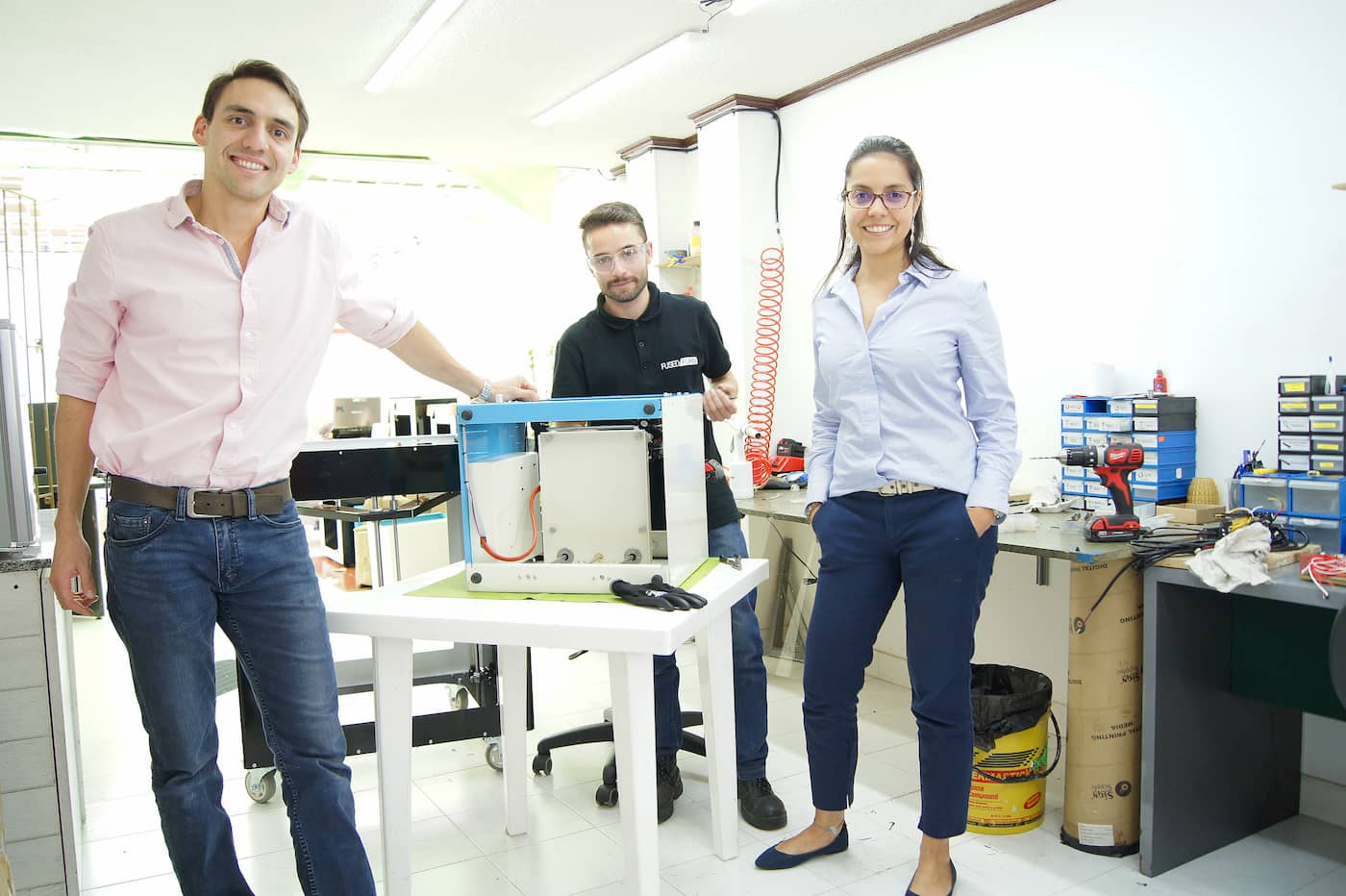
Fused Form co-founders Lissy Rodríguez and Juan Camilo Blanco in Colombia. Image courtesy of Fused Form.
Looking forward to a time when Latin America catches up with developed nations, Rodríguez and Blanco continue to expand their business by incorporating new machine options that appeal to their solid customer base. The company’s strategy is to continue selling 30% of its product line to other countries, including Italy, Spain, Switzerland, and the United States. The FF Pellet 600+ is the sixth 3D printer the duo has designed, and they have high hopes that it will do well in the growing market for pellet extrusion systems.
Subscribe to Our Email Newsletter
Stay up-to-date on all the latest news from the 3D printing industry and receive information and offers from third party vendors.
Print Services
Upload your 3D Models and get them printed quickly and efficiently.
You May Also Like
Reinventing Reindustrialization: Why NAVWAR Project Manager Spencer Koroly Invented a Made-in-America 3D Printer
It has become virtually impossible to regularly follow additive manufacturing (AM) industry news and not stumble across the term “defense industrial base” (DIB), a concept encompassing all the many diverse...
Inside The Barnes Global Advisors’ Vision for a Stronger AM Ecosystem
As additive manufacturing (AM) continues to revolutionize the industrial landscape, Pittsburgh-based consultancy The Barnes Global Advisors (TBGA) is helping shape what that future looks like. As the largest independent AM...
Ruggedized: How USMC Innovation Officer Matt Pine Navigates 3D Printing in the Military
Disclaimer: Matt Pine’s views are not the views of the Department of Defense nor the U.S. Marine Corps Throughout this decade thus far, the military’s adoption of additive manufacturing (AM)...
U.S. Congress Calls Out 3D Printing in Proposal for Commercial Reserve Manufacturing Network
Last week, the U.S. House of Representatives’ Appropriations Committee moved the FY 2026 defense bill forward to the House floor. Included in the legislation is a $131 million proposal for...