Additive construction is taking off much more quickly than this author had anticipated. We’ve seen an increasing number of “firsts”, from the “first” 3D printed building in Germany to the “first” commercially available 3D printed home in the U.S. More importantly, the practicality of additive construction is beginning to show, with some projects demonstrating the utility, cost, and efficiency of 3D printing certain elements, such as wind turbine bases, over traditional construction techniques.
Along with this momentum, there has been one claim continually made by additive construction firms that has yet to be addressed concretely. Can 3D printing architectural elements, walls or entire buildings actually solve the global housing crisis? A quick internet search will give you countless articles from mainstream outlets answering this question with an implicit “yes.”
However, many of these articles don’t actually ask anyone with on-the-ground knowledge of the housing crisis. For the most part, they allow the companies whom they’ve interviewed, such as Mighty Buildings, New Story or ICON, to give their technological vision of solving the problem of affordable housing. We decided to try another approach.
Peter Cohen is the Co-director at the Council of Community Housing Organizations (CCHO) in San Francisco, a coalition of 22 organizations that develop and advocate for affordable housing in the Bay Area. Cohen agreed to speak to us to give us his perspective on 3D printing as a potential solution to a problem faced by 1.2 billion people on the planet: lack of adequate housing.
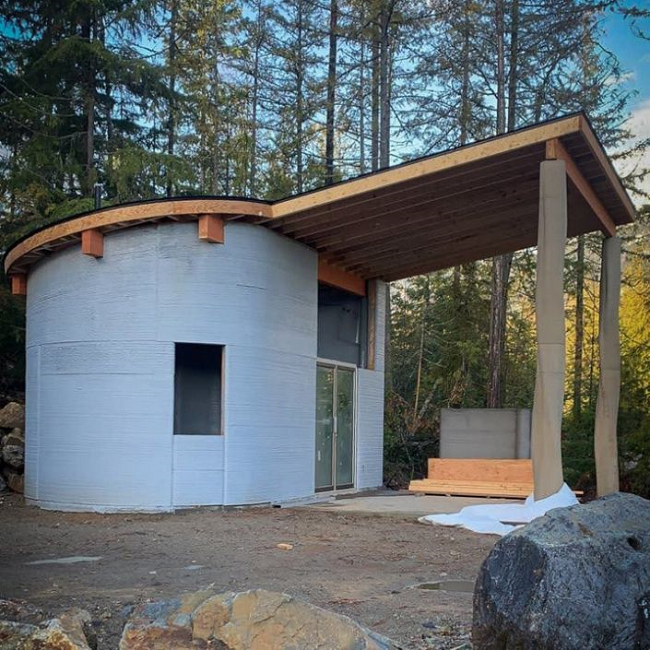
According to Cohen, in his association’s roughly 40-year existence, new solutions regularly come along with a goal of being the magic nail to the matter of housing affordability. In the case of additive construction as one of those new ideas, this technology is actually a construction solution to what is more of a policy problem, particularly in California.
The broader issue is the housing market as a whole, which directs finance capital away from public or nonprofit affordable projects and toward high-end private housing markets. Most finance capital for housing development is concentrated at the top end, where the money’s made. This also typically means highly concentrated in urban areas, particularly lower-cost real estate areas that can be gentrified and turned into high-value real estate. In turn, the public sector, including government and non-profits, are left to fill the housing access gap which is ever widening, but lack the funding to properly address it.
“It’s just a lack of sufficient capital to spread that peanut butter around to ensure that housing is being produced for folks across the entire income spectrum. Construction itself is not going to answer that. It’s more of—I would call the focus on construction technology as kind of working around the edges. What’s really the issue is the staggering disparity of income and debt distribution that’s just polarized everything—and housing production, housing access, is no different,” Cohen said.
Though technology itself likely won’t be able to provide low-cost homes to everyone because it doesn’t address the funding issue, Cohen did reflect that 3D printing could play a role in the housing market. Specifically, he offered that new technologies—whether that’s additive construction or, more simply, pre-fabricated construction—could be used for in-fill of geographically unique pieces of land via accessory dwelling units (ADUs).

While the private sector neglects the suburbs and lower density locations, non-profits can usually only afford to execute projects that leverage economies of scale, meaning over 40 units, to make public investments worthwhile. This leaves a gap for smaller projects in lower density areas where ADUs or other small dwellings could be located and sold at a lower cost than larger homes.
If you have lived in California, you may have already noticed this trend: small units or “tiny homes” are constructed on residential lots to give landowners additional income through renting these new dwellings. If you’ve followed 3D printing for some time, you are already beginning to sense the possibilities.
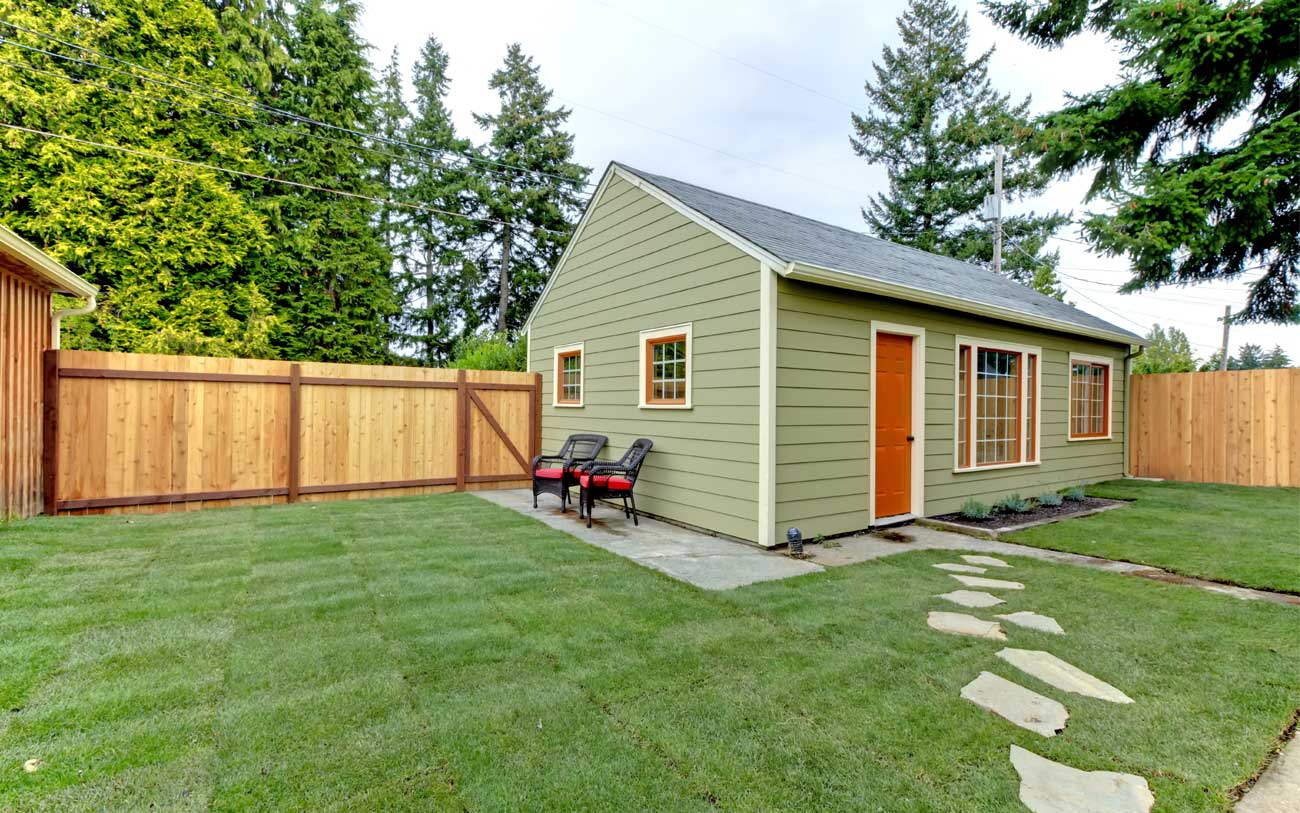
Additive manufacturing is particularly suited to one-off, custom parts with unique geometries, but, so far, can’t manage to produce large volumes at scale. Mass manufacturing always beats out 3D printing when it comes to massive quantities of items.
For construction, we could see a similar application for our technology. If there’s the proper space (or even if it simply involves off-site production of modular architectural elements), a 3D printer could build ADUs on geographically unique lots more affordably than possible with traditional techniques.
“There’s a tremendous opportunity for small-scale construction, putting these ADUs—which is a big thing now—on a small sliver of land where maybe the zoning allows it to have two or three or four units on that lot,” Cohen said. “That’s different from a big affordable housing project. I just don’t see that as being a workable solution.”
At the moment, these types of ADU-style projects at the public level seem to represent political talking points or imaginative ideas but are not yet field tested for viability. However, they have gained attention from the media and political energy. Cohen could imagine a possible public-private partnership, non-profits, or new private market endeavors enabling this sort of project. ADUs could be a way to sustain moderate-income homeowners, generating income or defraying debt, while adding to the housing stock.
In our industry, we’ve seen a wide array of clever businesses spring up that use our unique technical capabilities to fill gaps in the market. Most often, they fulfill high-end applications, such as rocket or race car parts, but if it is the most economical technology available, 3D printing is may be up to the task.
Perhaps we shouldn’t be asking whether or not additive construction is more affordable than building a traditional home, but more affordable than building a tiny home. If so, then one can easily imagine a developer working with an additive construction firm to work with land owners to quickly erect ADUs, with all splitting the profit and, in the process, creating homes that may not be as inexpensive as public housing but is much more affordable than traditional single-family homes.
“I think there’s a real appetite out there from the mom and pops of the world, but nobody’s quite figured out how to systematize yet. It would require helping those mom and pop homeowners feel less intimidated by the whole process and give them a smooth path— presenting a very plug and play ready solution. ‘Take a look at our showroom floor. If you’d like one of those in your backyard, here’s how the permitting process works. It’s all been smoothed out by the city. And here are some contractors who have kind of developed a specialty in this boutique industry’.”
The ultimate “north star” solution to the housing crisis, according to Cohen, is to de-commodify housing. If we were to be objective about it, the entire real estate market is one geared toward profit, which is not in alignment with society’s purported goal of affordable homes.
“Asking the real estate market to de-commodify housing is kind of like asking the oil industry to switch to renewables: it ain’t going to happen anytime soon, you know?”
But as a significant incremental step toward that, the most efficient way to provide housing to everyone would be to simply grab up unused buildings and provide apartments to those who previously couldn’t afford it—a tactic that a state-based governmental system would easily allow for. However, in market-driven societies, a slower and more piecemeal solution is most likely the answer.
CCHO attempts to pursue an “acquisition and preservation” strategy, along with larger scale affordable housing production, in which empty buildings, such as hotels, are taken off the speculation market, refurbished and repurposed into affordable housing. At the same time, it fights the policy battles necessary to make this process possible.
Most recently, this meant a three-year political campaign in San Francisco that resulted in a policy, called the Community Opportunity to Purchase Act, that gives nonprofit organizations, such as the Small Sites Program, the first right to purchase apartment buildings when they come up for sale on the market. These groups don’t get a discount and have to pay fair market price, but they do have the first opportunity to grab those sites before they become game on the open market. San Francisco has become the first city in California to adopt that policy, with only several other municipalities in the country adopting that policy.
This is an important step toward de-commodifying housing until members of U.S. society at large are, one, ready to reprioritize aid toward the less fortunate and, two, have the power to make those priorities into political realities.
Subscribe to Our Email Newsletter
Stay up-to-date on all the latest news from the 3D printing industry and receive information and offers from third party vendors.
You May Also Like
Gorilla Sports GE’s First 3D Printed Titanium Cast
How do you help a gorilla with a broken arm? Sounds like the start of a bad joke a zookeeper might tell, but it’s an actual dilemma recently faced by...
Nylon 3D Printed Parts Made More Functional with Coatings & Colors
Parts 3D printed from polyamide (PA, Nylon) 12 using powder bed fusion (PBF) are a mainstay in the additive manufacturing (AM) industry. While post-finishing processes have improved the porosity of...
$25M to Back Sintavia’s Largest Expansion of Metal 3D Printing Capacity Since 2019
Sintavia, the digital manufacturing company specializing in mission-critical parts for strategic sectors, announced a $25 million investment to increase its production capacity, the largest expansion to its operations since 2019....
Velo3D Initiates Public Offering in a Bid to Strengthen Financial Foundations and Drive Future Growth
Velo3D (NYSE: VLD) has been among a number of publicly traded 3D printing firms that have attempted to weather the current macroeconomic climate. After posting a challenging financial report for 2023,...