Supported by Innovate UK, the Manufacturing Technology Centre (MTC) works to speed up industrial growth in the UK by creating and embedding future skills and developing and proving manufacturing processes, such as 3D printing. The latter is specifically what the National Centre for Additive Manufacturing (NCAM), part of the MTC, focuses on, and its DRAMA research project spent the last three years setting up a stronger AM supply chain for aerospace. But the NCAM also supports automotive and motorsports AM applications: a perfect example of this can be found in the recent work its Coventry team has done to help Oxford Brookes Racing (OBR), the Oxford Brookes University‘s formula student racing team, reach its 2020 all-electric goal.
OBR is one of the top UK formula student racing (FSUK) teams, and has worked with the MTC on a number of projects before. So the team knew that its NCAM would be the perfect partner to help them take things to the next level.
“After a long and successful history of combustion entries in the formula student competition, OBR is making the shift to electric for the 2020 season. With a new team structure and a class 2 project to serve as a R&D platform, OBR aims to develop a platform to not only take on the top FS teams in the world, but to also serve as a test bed of innovation for electric vehicles and controls software,” the OBR website states.
The goal was to see if additive manufacturing could be used to fabricate a complex part that connects the brake mounts, suspension link, and wheel, while also containing the car’s electric motor gearbox.
“Our team was aiming not only to develop a platform to take on the other top Formula Student teams in the world, but to also serve as a test bed for innovation in electric vehicles and controls software,” OBR’s Charles Boileve said. “It has also given us an opportunity to be on the forefront of not only performance, but also the industry by gaining both the knowledge and hands-on experience working with electric vehicles.”
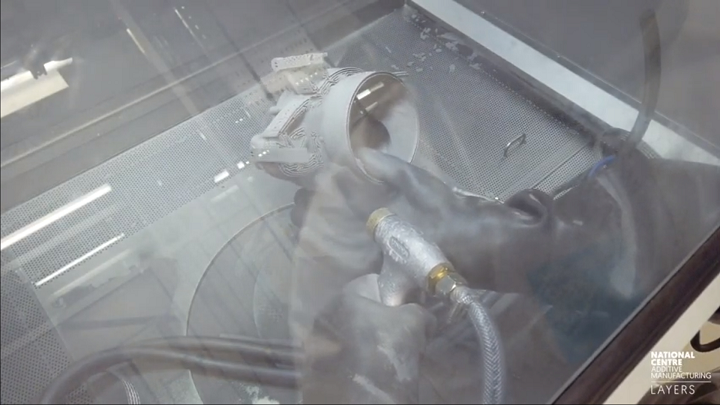
OBR’s part produced in Ti64Al4V on an Arcam EBM Q20plus. (Photo: National Center Additive Manufacturing)
NCAM’s recently installed metal additive manufacturing facility is home to a variety of metal AM technologies, and the center is particularly good at helping clients determine the best technology for whatever application on which they happen to be working. In this case, it turned out to be the GE Additive Arcam Q20plus, an electron beam melting (EBM) system.
“The collaboration case study project enabled demonstration of the full AM end‑to-manufacturing process; from a conception idea to design for AM, manufacture, inspection and post processing machining,” stated Ruaridh Mitchinson, product development leader at NCAM. “The most exciting thing was working closely with MTC Design for Additive and process engineering experts to fully explore the EBM AM process capability, as well as disseminating the knowledge to Oxford Brookes racing team.”
Once it was decided that EBM would be the most appropriate technology, NCAM senior research engineer Emmanuel Muzangaza helped the OBR team develop and complete the critical part for its electric racecar.
“We’re here to help wherever we can. In fact, the OBR team already had a strong concept and design for additive in mind, which was about 90% there,” Mitchinson added. “Our team was able to add our deep additive expertise, offer guidance and add that remaining 10% in order to get the project up and running.”
According to SmarTech Analysis, EBM technology had “huge growth levels for the first nine months” of 2019, the majority of which “was tied to GE Additive, the only significant commercial provider of the technology.”
“Electron beam melting for metals has been a relatively niche market for many years by comparison to laser technologies, and while laser systems will still command the majority share of industry revenues for the foreseeable future, it appears that the EBM segment is ripe for growth,” SmarTech continued.
The OBR team chose EBM technology instead of other additive methods for several reasons, including increased design freedom that makes it possible to densely nest all of the larger parts without any swelling, and to create very few, or no, supports for less money. The process, which takes place at high temperatures in a vacuum, can rapidly print dimensionally accurate, stress-relieved parts using its high-powered electron beam, and results in components that feature material properties comparable to those of wrought material.
The high temperatures of EBM allow parts to be produced with minimal stress, and even none at all, and it’s also cost-effective, as it allows users to print with crack-prone, reactive materials, like the Ti6Al4V (titanium) alloy, for less money. Additionally, the Arcam Q20plus comes with a Powder Recovery Station (PRS), which means any extracted powder can possibly be reused for future prints.

OBR part with supports removed, prior to post-processing. (Photo: National Center Additive Manufacturing)
The part the team created was based on a 4WD in-hub motor configuration with AMK AC servo motors, which was paired to a compact epicyclic gearbox that could produce more than 300 N-m of torque per wheel. A 600V, 6.6 kW-hr battery pack with lithium cobalt oxide (LCO) pouch cells, featuring a peak output of over 130 kW, is used to supply energy to the component, and an open controls platform is used to manage it all, which, as a GE Additive press release states, is “ideal for implementing torque vectoring and advanced vehicle controls to unleash the full performance potential of an electric race car.”
As with all things in 2020, COVID-19 taketh away, and does not giveth anything, so the OBR20 team did not get to show off its new electric racecar on the track in the FSUK season. But, over 80 teams did participate in a virtual competition a few months ago, and OBR20 placed third in Virtual Dynamics and fifth in Statics. If these two had been scored together, like they would have been at the real event, OBR20 would have placed second a third year running.
“While we hit a bump in the road this year, we continued to better ourselves as engineers – by pushing ahead and looking forward,” Boileve said. “The electric revolution is still coming, so we will be striving for perfection as a team, and remain committed to our vision of building a multi-year legacy.”
Subscribe to Our Email Newsletter
Stay up-to-date on all the latest news from the 3D printing industry and receive information and offers from third party vendors.
Print Services
Upload your 3D Models and get them printed quickly and efficiently.
You May Also Like
Johns Hopkins University Researchers Develop HyFAM Technology
Two scientists from Johns Hopkins University, Nathan C. Brown and Jochen Mueller, have developed a hybrid manufacturing technology they call HyFam, or Hybrid Formative Additive Manufacturing. Their work on this technology...
3D Printing G-Code Gets an Upgrade: T-Code
Good old G-Code still manages many 3D printers, great and small. Just like the STL, it’s a standard that enables collaboration while also holding the additive manufacturing (AM) industry back....
AM Rewind: The Biggest News and Trends of 2024
After a sluggish 2023, driven by persistent inflation and geopolitical tensions, 2024 has seen some recovery. Economic growth climbed from about 2.8 percent in 2023 to a modest 3.2 percent...
Metal Wire 3D Printer OEM ValCUN Announces Plans for 2025 Expansion
ValCUN, a Belgian original equipment manufacturer (OEM) of wire-based metal additive manufacturing (AM) hardware, has announced that the company has entered the next phase of its growth trajectory, making key...