3D technologies by Belgian company Materialise (MTLS) have long been used for applications in the healthcare field, from splints and surgical guides to implants, and this summer it received important CE Marking Certification for most of its personalized orthopedic and cranio-maxillofacial (CMF) products. Recently, the company’s technology was definitely put to the test during an extremely major surgery, but with help from Materialise, the world’s first simultaneous double hand and face transplant was a success.
The company helped by 3D printing medical tools, like personalized guides, and using 3D imaging to develop a surgical plan ahead of the procedure, which was performed at NYU Langone Health in Manhattan.
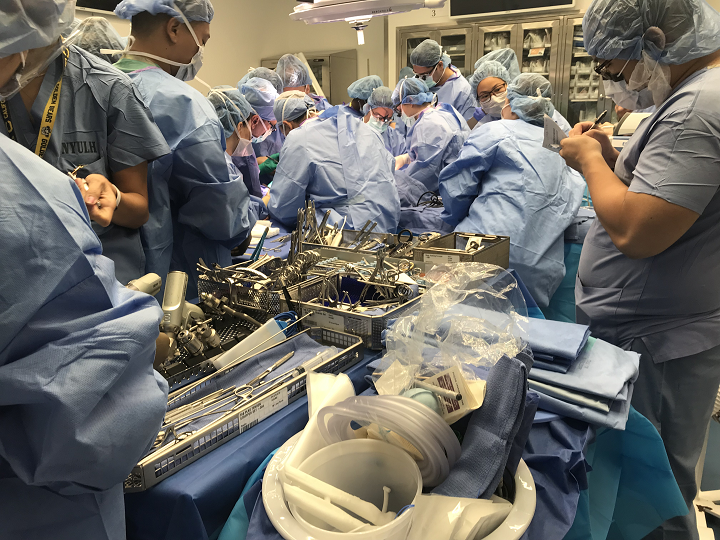
“Image-based planning and medical 3D printing have completely revolutionized personalized patient care by providing surgeons with detailed insights and an additional level of confidence before entering the operation room. As a result, leading hospitals are adopting 3D planning and printing services as part of their medical practices because they create a level of predictability that would be impossible to achieve without the use of 3D technologies,” stated Bryan Crutchfield, Materialise’s Vice President and General Manager – North America.
The patient, only 22 years old, had suffered really bad injuries to both arms and his face from burn wounds he got in a car accident. The soft tissue in these body parts was severely damaged as a result, which made it hard for him to have a normal life. For over a year, Materialise clinical engineers and NYU Langone surgeons prepared for the operation, practicing in a lab in order to perfect the surgical plan ahead of time.
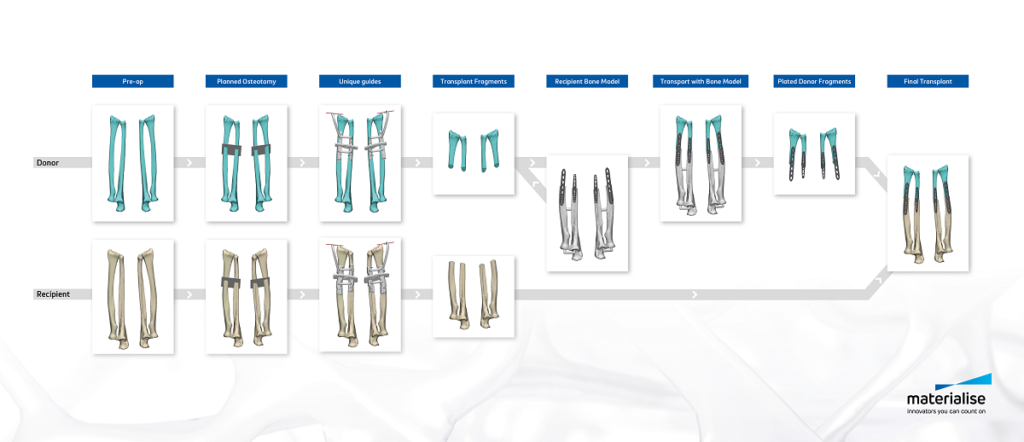
More and more these days, we’re seeing personalized 3D printed surgical tools, like the ones Materialise developed for this surgery, being used to improve accuracy and speed in the operating room. 3D technology is also extremely helpful in terms of surgical planning, which was definitely the case here.
During the long months of planning ahead of the surgery, the Materialise engineers used CT scans to make an onscreen 3D model of the patient’s hands and face in order to create a surgical plan. This way, the clinical engineers and surgeons can gain a better understanding of the patient’s bone structure, which helps them figure out what to tackle first in the operation, and plan out the rest of the surgery. A 3D anatomical model is also helpful in that the doctors are able to visualize a number of different medical scenarios that could occur, and virtually choose and position implants, which means they can prepare for both the best and the worst-case scenarios.
Once the team decided on the final surgical plan, Materialise 3D printed a variety of implements that would be used during the historic transplant surgery, including anatomical models, surgical guides, and other tools. The company’s platform consists of specialized services and software that pave the way for certified medical 3D printing in both research and clinical environments.
“Complex transplant surgery like this brings together a large team of specialists and presents new and unique challenges. This demands careful planning and makes timing, efficiency and accuracy absolutely critical,” explained Dr. Eduardo D. Rodriguez, the Helen L. Kimmel Professor of Reconstructive Plastic Surgery and chair of the Hansjörg Wyss Department of Plastic Surgery at NYU Langone. “Virtually planning the surgery in 3D and creating 3D printed, patient-specific tools offers additional insights in the pre-operative phase and increased levels of speed and accuracy during a time-critical surgery.”

Once the team, which was led by Dr. Rodriguez, found an acceptable donor for the surgery, they had just 24 hours to get started on this first-of-its-kind operation, the goal of which was to give the young patient a better quality of life and improved appearance and function.
The 17-person surgical team used a system of drilling and cutting guides, 3D printed by Materialise and personalized to the patient’s own anatomy, to reposition and fasten the bone fragments; the guides also helped accurately position the various medical tools used in the surgery, which decreased the amount of time the patient was on the operating table.

Materialise also 3D printed identification tags, which could be sterilized, for blood vessels and nerves, as well as 3D printed models used during transport of the donor, and 3D printed splints, which helped the surgeons place the donor hands in the best position during reconstruction of the patient’s soft tissue.
Thanks to the surgical team’s hard work, and with Materialise’s help, the double hand and face transplant was a successful surgery.
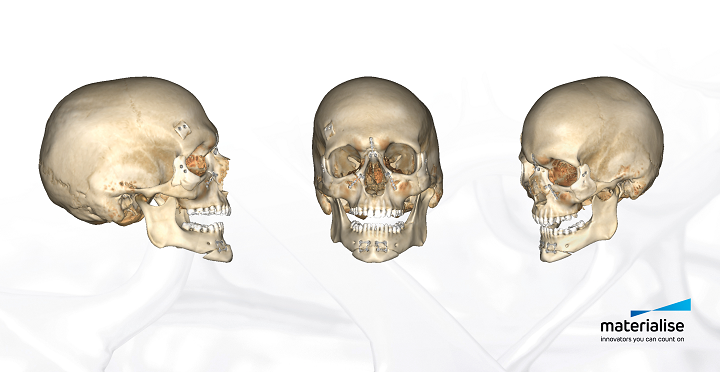
(Source/Images: Materialise)
Subscribe to Our Email Newsletter
Stay up-to-date on all the latest news from the 3D printing industry and receive information and offers from third party vendors.
Print Services
Upload your 3D Models and get them printed quickly and efficiently.
You May Also Like
Reinventing Reindustrialization: Why NAVWAR Project Manager Spencer Koroly Invented a Made-in-America 3D Printer
It has become virtually impossible to regularly follow additive manufacturing (AM) industry news and not stumble across the term “defense industrial base” (DIB), a concept encompassing all the many diverse...
Inside The Barnes Global Advisors’ Vision for a Stronger AM Ecosystem
As additive manufacturing (AM) continues to revolutionize the industrial landscape, Pittsburgh-based consultancy The Barnes Global Advisors (TBGA) is helping shape what that future looks like. As the largest independent AM...
Ruggedized: How USMC Innovation Officer Matt Pine Navigates 3D Printing in the Military
Disclaimer: Matt Pine’s views are not the views of the Department of Defense nor the U.S. Marine Corps Throughout this decade thus far, the military’s adoption of additive manufacturing (AM)...
U.S. Congress Calls Out 3D Printing in Proposal for Commercial Reserve Manufacturing Network
Last week, the U.S. House of Representatives’ Appropriations Committee moved the FY 2026 defense bill forward to the House floor. Included in the legislation is a $131 million proposal for...