In the next decades, the space economy will drive advances in innovation, technology, and manufacturing. In 2020, space leaders like Aerojet Rocketdyne, Made In Space, and SpaceX hit new milestones in off-Earth exploration that will lead to long-term economic benefits. The global space industry is already expected to generate $1.1 trillion or more in 2040, up from the current $350 billion. Furthermore, the production of space vehicles, such as rockets, off-orbit stations, capsules, satellites, rovers, and more, is booming due to the pressing need to develop more space infrastructure as part of plans for space exploration and to improve connectivity on Earth.
Critical to empowering the space economy is developing new space engine technology, and one company is getting ready for the upcoming space race. In 2015, Colorado-based startup Ursa Major Technologies put together an expert team of designers and engineers to realize its vision of providing the emerging microsatellite and nanosatellite launch market with innovative propulsion solutions. Its products are intended to be used by aerospace startups looking to outsource their engine production rather than make them on-site.
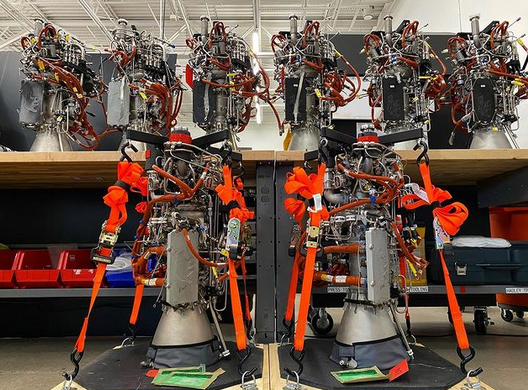
Ursa Major Tech produced dozens of Hadley engines in 2020 at its Colorado development site. Image courtesy of Ursa Major Tech via Instagram.
To optimize the unique part creation of its engines for launch and hypersonic applications, Ursa Major leverages additive manufacturing (AM) processes. The startup has focused its attention on cutting-edge 3D printing techniques that could help create and power a new generation of space vehicles from the outset. Company founder and former Propulsion Engineer at SpaceX and Blue Origin, Joe Laurienti, turned to AM technology, simulation, and 3D design software by ANSYS to modernize the development of staged combustion engines.
The company successfully designed and built two liquid oxygen and kerosene combustion engine models, Hadley and Ripley, and is currently working on a third engine called Samus. Through internally developed materials and processes, Ursa Major additively manufactures 80% of its engines. Hadley, a 5,000 pound-force engine capable of launching orbital and suborbital vehicles, is part of the Air Force Research Laboratory (AFRL)’s X-60A program. Launch services provider Generation Orbit is developing the X-60A air-launched rocket designed for hypersonic flight research under an AFRL Small Business Innovation Research (SBIR) contract. In 2020, Generation Orbit completed the X-60A integrated vehicle propulsion system ground test campaign in Jacksonville, Florida. The test runs included both cold flow and hot-fire testing with Ursa Major’s Hadley liquid rocket engine.

Ursa Major Tech’s Hadley engine pre burners made with 3D printing technology. Image courtesy of Ursa Major Tech via Facebook.
The startup was also one of seven companies to receive an SBIR Phase II contract from the U.S. Department of Defense of up to $750,000 to jump-start a prototype during a 2019 open innovation call held on Inaugural Hypersonics Pitch Day. As part of its mission, Ursa Major is partnering with several startups to prove they can disrupt the launcher vertical integration trend and encourage space vehicle manufacturers to outsource propulsion. It has struck an agreement with American aerospace company Stratolaunch, which has begun construction on a prototype hypersonic vehicle designed to launch from the world’s biggest airplane. In late October 2020, Stratolaunch said the Ursa Major rocket engine tests that will power the vehicle to speeds above Mach 5 were complete.
Newcomer Phantom Space has also turned to Ursa Major for its engines. Founded by early SpaceX team member and Co-founder of Vector Launch, Jim Cantrell, Phantom Space is a new space transportation provider that will focus on micro-satellite, small satellites, and propulsion systems launch services. The company has arranged to use Ursa Major’s engines to power its first rocket, which at about four feet in diameter and roughly 50 feet in length is being designed to carry 1,000 pounds into orbit. According to the Arizona Daily Star media site, Phantom’s first rocket will use seven Ursa Major engines for liftoff, with one engine for the second stage, noting that the liquid oxygen and kerosene-fueled engines have already been qualified for flight.

Senior Propulsion Development Engineer Jacey Coniff is working on installing sense line tubing for test stand instrumentation. Image courtesy of Ursa Major Tech/Kaitlin K Walsh.
At its Berthoud, Colorado site, the Ursa Major team designs, engineers, and assembles the engines on-site before testing them. The company has produced dozens of propulsion systems throughout the last two years, predominantly using direct metal laser sintering (DMLS) 3D printing technology. In 2020, the company expanded its test facilities with the grand opening of the UB01 control center and activated its second test stand, where an upgraded version of the Hadley engine ran for thousands of seconds during the second quarter of 2020. The company is working on expansion plans for its Berthoud campus to unify all of its sites into one in 2021.⠀
To keep up with its engine serial production target, the team is also working on the Ripley engine, which varies from Hadley. It is a 35,000-pound engine that provides a boost propulsion solution for vehicles intended for space orbit. Also leveraging 3D printing and staged combustion, Ripley delivers industry-leading performance and power at a price point set to change the space launch industry, suggested the company. Although still not revealed, the high-energy propulsion Samus engine is a 50,000-pound liquid hydrogen engine expected to be ideal for medium and heavy class space-launch applications.

The Ursa Major Tech logo and part number are printed on the side of the Hadley engine’s main thrust chamber, which is 3D printed. Image courtesy of Ursa Major Tech/Kaitlin K Walsh.
In December 2020, Laurienti managed to secure $25.3 million in new funding to aid the campus expansion and accelerate product development. Overall, the company has managed to raise more than $48.8 million in funding over six rounds from investors like Space Angels, the country’s leading source of capital for early-stage space ventures like SpaceX, Made In Space, and Oxford Space Systems. As well as Alsop Louie Partners, Dolby Family Ventures, Alpha Edison, and leading space investor Dylan Taylor.

Hot fire testing an engine at Ursa Major Tech’s Colorado site. Image courtesy of Ursa Major Tech via Facebook.
Even though many space companies are developing their own propulsion systems in-house, a growing number of smallsat launch startups are looking for reasonably-priced engines that can perform well. Here, Ursa Major could find a thriving market. In the last five years, the company has gained momentum thanks to big-time contracts with the U.S. Department of Defense and a steady sale of engines to launcher startups. Entrepreneurs like Laurienti are transforming the space industry by foreseeing future demands and continuously incorporating 3D printing technologies into rocket engine manufacturing. As more companies become important players in the off-Earth ecosystem, the historically staggering cost of access to space will continue to decrease, revolutionizing space activity like never before.
Subscribe to Our Email Newsletter
Stay up-to-date on all the latest news from the 3D printing industry and receive information and offers from third party vendors.
Print Services
Upload your 3D Models and get them printed quickly and efficiently.
You May Also Like
U.S. Navy Lab Uses 3D Printing to Reduce Tooling Lead Time By Over 90%
The F-35 Lightning II Joint Program Office (JPO), responsible for life-cycle management of the key fifth-generation joint strike fighter (JSF) system used by the U.S., its allies, and its partners,...
Etsy Design Rule Change Reduces Selection of 3D Printed Goods
Online marketplace Etsy has implemented a rule change requiring all 3D printed goods on the site to be original designs. The update to the site’s Creativity Standards states, ¨Items produced using...
Honeywell Qualifies 6K Additive’s Nickel 718 for 3D Printed Aerospace & Defense Parts
6K Additive is renowned for manufacturing sustainable additive manufacturing (AM) powder, and offers a wide portfolio of premium metal and alloy powders that include titanium, copper, stainless steel, and nickel,...
MetalWorm Sells WAAM Systems to Research Institutes in Brazil and Malaysia
Turkish WAAM firm MetalWorm has sold a system in Malaysia and another in Brazil. This is an excellent example of a few emerging trends in additive. Firstly, WAAM was experimented...