In 2019, Stratasys (NASDAQ: SSYS) released its Digital Anatomy solution, which combined three materials and custom software inside GrabCAD with its full-color, multimaterial J750 printer for the purposes of turning 3D scans into realistic 3D printed anatomical models for training and surgical planning. The Digital Anatomy materials are optimized to look and feel like bone and tissue, and mimic the mechanical properties of actual human tissue very closely, so the solution is a great option for functional models. Now, the company announced that it has upgraded the J750 Digital Anatomy printer to give it more advanced bone capabilities for super-realistic models and simulations.
The bone models that Digital Anatomy is now capable of fabricating offer more than just a startlingly lifelike appearance: they are actually biomechanically accurate, and this is a fact that’s been verified by clinical research studies. Because of the solution’s software upgrade, the J750 is able to realistically mimic porous bone structures, ligaments, and fibrotic tissue, so medical professionals can print models that actually behave like real human bone.
“We believe that better preparation leads to better clinical outcomes. The mechanical properties of bone are so fundamental to the ability of our skeletons to support movement, provide protection for our vital organs and ultimately affect our quality of life. Being able to 3D print models that are biomechanically accurate and unique to each patient is critical to that preparation,” Vice President Osnat Philipp, the leader of the global healthcare team at Stratasys, explained in a press release.
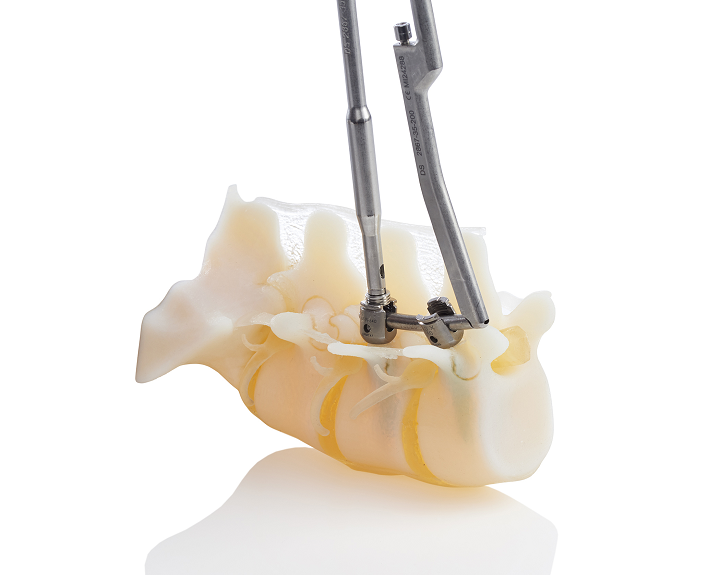
The Digital Anatomy 3D printer from Stratasys enables physicians to practice inserting screws for orthopedic applications with biomechanical realism similar to a human anatomy.
Most traditional bone models are less than optimal, as human bone is hard to get and costs a lot of money, and it’s difficult to find bone with the specific pathology characteristics that researchers need, such as various ages or bones with tumors. Human bone from cadavers has been used in the past, in addition to off-the-shelf manufactured models, and both of these options are not patient-specific. That’s why researchers in the medical industry have been turning to 3D printed bone models, but these are not all created equal. Stratasys says that its Digital Anatomy bone models offer extremely realistic haptic feedback when surgeons are sawing the model or inserting a screw into one, and they are also patient-specific, as “each model can be created from an actual patient scan.”
When Stratasys first introduced its Digital Anatomy solution, the main focus was to use its software, and new GelMatrix and TissueMatrix materials, to create realistic soft cardiology tissues, like blood vessels and hearts, rather than hard bone. The resulting anatomical models helped medical device trainers conduct testing, gave medical professionals a realistic training device, and helped surgeons prepare for operations in advance. What’s changed with this new software enhancement is that all of these can continue to occur, but for orthopedic applications now.
A doctor at a Florida children’s hospital said that realistic 3D printed skull and spine models, like the ones enabled by the J750 Digital Anatomy, give doctors a better training tool for practicing cutting and drilling bones.
“The opportunities seem endless to me because doctors can ‘operate’ before they operate. It’s going to decrease surgical time, it’s going to decrease morbidity and mortality, and help us decrease anesthesia time, which is better for brain development,” she said.
The J750 Digital Anatomy system is obviously an important part of the solution, but the software really kicks things up a notch, featuring over 100 sophisticated presets resulting from years of testing by leading hospitals and academic medical centers all over the globe. Stratasys says that physicians can print long bones with different amounts of marrow, or ensure a solid contrast between general bones and denser skull bones. Vertebrae joints can be 3D printed with different levels of stiffness, material combinations can be printed at the voxel level for correct biomechanical properties, and it’s even possible to print intervertebral discs normally or degenerated.
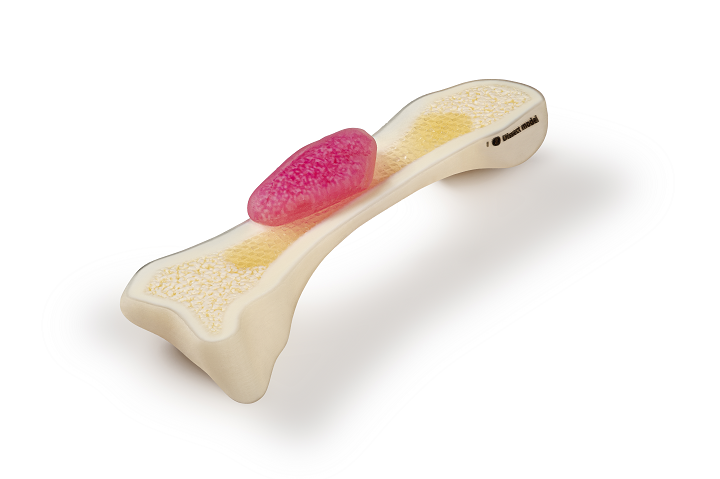
The Digital Anatomy 3D printer can also produce accurate models of patient bones down to the voxel level, including marrow, and even lets doctors include features like tumors.
A clinical evaluation of bone model characteristics 3D printed on the J750 Digital Anatomy printer was completed this year by researchers at Tel Aviv University‘s Computational Mechanics and Experimental Biomechanics Lab, with a focus on the accuracy of screw pull-out force and driving torque with both cancellous and cortical screws. The team concluded that the pull-out force of orthopedic screws used with the Stratasys 3D printed models featured a haptic response similar to what they’d see with human cadaver bone. Another 2020 study, by a team at Israel’s Technion Institute of Technology’s Materials Science and Engineering Laboratory, compared the mechanical accuracy of cadaver spines with that of 3D printed spine models. These researchers demonstrated that the range of motion offered by the 3D printed lumber vertebrae models, compared to previously published research on human spines, was indeed accurate.
In the report “Additive Manufacturing In Orthopedics: Markets for 3D Printed Medical Implants,” published in 2019, SmarTech Analysis states that orthopedics is “one of AM’s key driving segments,” and that likely has not changed much in the last year. So it was a smart move by Stratasys to focus on upgrading the part of its Digital Anatomy solution that focuses on 3D printed bone models.
(Source/Images: Stratasys)
Subscribe to Our Email Newsletter
Stay up-to-date on all the latest news from the 3D printing industry and receive information and offers from third party vendors.
Print Services
Upload your 3D Models and get them printed quickly and efficiently.
You May Also Like
Reinventing Reindustrialization: Why NAVWAR Project Manager Spencer Koroly Invented a Made-in-America 3D Printer
It has become virtually impossible to regularly follow additive manufacturing (AM) industry news and not stumble across the term “defense industrial base” (DIB), a concept encompassing all the many diverse...
Inside The Barnes Global Advisors’ Vision for a Stronger AM Ecosystem
As additive manufacturing (AM) continues to revolutionize the industrial landscape, Pittsburgh-based consultancy The Barnes Global Advisors (TBGA) is helping shape what that future looks like. As the largest independent AM...
Ruggedized: How USMC Innovation Officer Matt Pine Navigates 3D Printing in the Military
Disclaimer: Matt Pine’s views are not the views of the Department of Defense nor the U.S. Marine Corps Throughout this decade thus far, the military’s adoption of additive manufacturing (AM)...
U.S. Congress Calls Out 3D Printing in Proposal for Commercial Reserve Manufacturing Network
Last week, the U.S. House of Representatives’ Appropriations Committee moved the FY 2026 defense bill forward to the House floor. Included in the legislation is a $131 million proposal for...