While disaster has not yet befallen my humble family, there is no shortage of emergencies globally and the COVID-19 pandemic has demonstrated just how useful even desktop 3D printing can be during disaster situations. Provided with the opportunity to review an Ultimaker S3 3D printer and several unique filaments, I thought I’d explore the 3D printing of simple goods that might be useful during emergency situations to get an idea for just how useful a desktop 3D printer might be.
In a previous article, I reviewed the Ultimaker S3 and described most of the items I printed. To learn more about how these machines have actually been used for emergency situations, I spoke to Jeremy Evers, an Application Design Engineer with Ultimaker. As it turns out, Evers and the rest of the world were impacted by an emergency situation of pandemic proportions, with 3D printing often presenting itself as a novel solution to many global supply chain issues.
Evers noted that, as 3D printing was introduced to produce supplies in the critically hit Lombardi region of Italy, he took note of the ways that this technology could help.
“I remember there was a point in time when everybody needed to stay indoors. Nobody was allowed to go grocery shopping or do whatever outside. The same was true for me. I was still traveling in February, giving workshops, inspiring people with 3D printing and then, all of a sudden, I was also locked inside,” Evers said. “We also really saw these scenes from Italy, where 3D printing was enabling the production of certain parts that were not able to be produced on time or there were difficulties with supply as the amount of people in the hospitals were increasing.”
In response, Ultimaker launched an initiative to connect people, businesses and organizations with their local service providers to obtain supplies more quickly via 3D printing. As we have seen, face shields became an easy way for 3D printer owners to help fulfill a critical need even with desktop systems. In addition to designing new types of face shields that might be more ergonomic, faster to print, or made with no assembly required, Evers took note of Ultimaker users developing new stacking strategies making it possible to 3D print 48 face shield brackets in a single print.
As an application engineer, Evers typically assists customers in obtaining the best results with their prints, including CAD modeling and providing printing parameters. As demand for supplies peaked during the pandemic, he lent this expertise to help those creating personal protection equipment and other goods to achieve the best possible products.
“When they had an idea, I helped them by approaching the task with a 3D printing mindset, asking ‘How feasible is this design to be made with 3D printing technology? Would I make changes to the design to a certain extent to make it more printable? How can we minimize the amount of support material?’ Evers explained. “I would also help with Cura optimizations to, of course, produce designs as fast as possible, but also to make the parts as reliable as possible.”
Ultimaker’s machines are open to third-party materials, making it possible to print with a wide variety of materials. As noted in our review, introducing new materials to the S3 is as simple as downloading a material profile via the Ultimaker Marketplace. As a part of his work, Evers has an eye on the industry to see what materials are available and how they might serve particular applications. In terms of 3D printing face shield brackets and other items, materials began to play an important role.

A member of the Ultimaker community 3D printing face shield brackets on an Ultimaker S5 3D printer. Image courtesy of DrCeeVee on the Ultimaker forums.
“What I’ve seen is that certain people start with material that is easy to print. They want fast results with PLA, but then they get feedback from people to make them more ergonomic,” Evers said. “They might change the shape. At some point you need to change more than just the shape. So, you can think of different kinds of materials. So, you saw people using TPU, a flexible, rubber-like material that bends around your head. But then, you might think about it from an ecological point of view. After a few hours of use of a face shield, it might get thrown away for medical safety reasons. So, people also began to explore antimicrobial filaments, with copper particles in it killing bacteria. And because of this open system, it’s really easy for users to experiment with different kinds of materials and see what’s best suitable for their application.”
Outside of the pandemic, desktop systems have been used in a crunch for what might be deemed a business emergency. Evers relayed an anecdote describing an operator from a long-time customer who took notice of the company’s Ultimaker printers and, when faced with the need for a critical part, was able to turn to 3D printing in a crunch. When a hook needed for automatically picking up boxes proved to be too short for a run, he designed a longer replacement in CAD and printed it on the fly so that, by the time the night shift took over the job, they had the right tool for the job.
“This was an emergency situation for the customer because the operation line was constantly stopping because it was jammed, since the wrong part was not really fulfilling its proper function,” Evers said.
There are, naturally, limitations with 3D printing. For instance, Z-axis strength for most technologies prevents the production of structurally critical parts. In both well-equipped local operations and a massive response to a global problem, such as the COVID-19 outbreak, multiple manufacturing technologies can be deployed to address supply needs. In the case of the pandemic, we saw laser cutters used to make the shields that would be attached to face mask brackets.
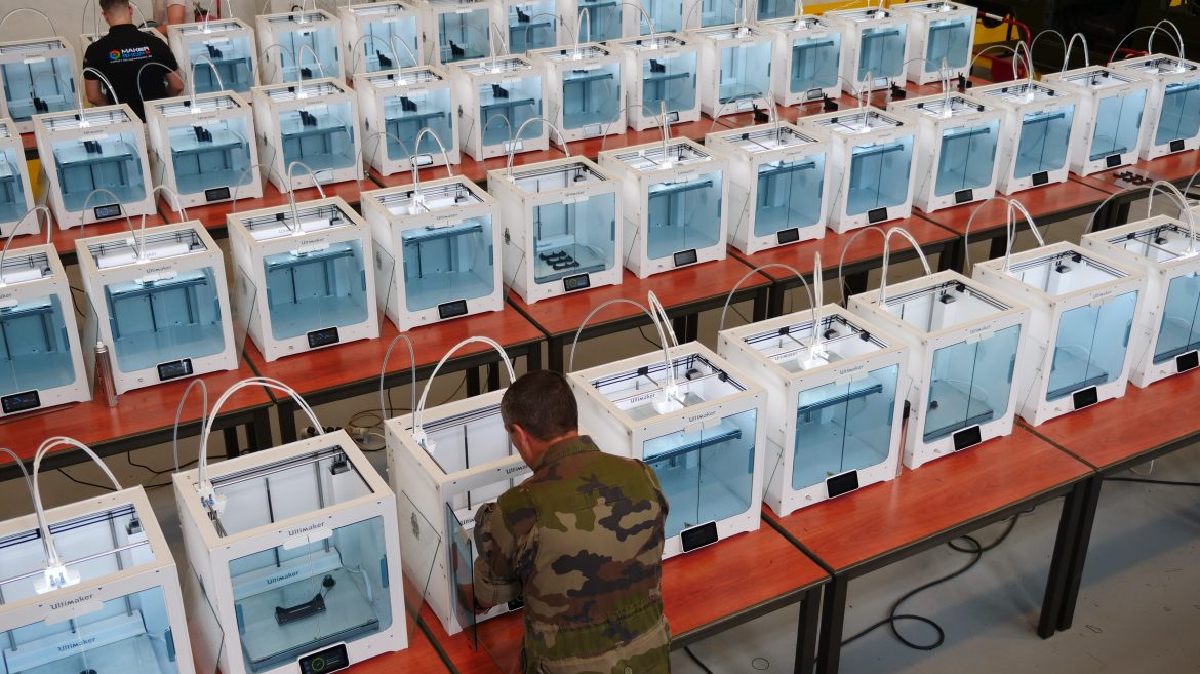
Amid the pandemic, the French Army established a 50-printer Ultimaker farm to 3D print spare parts.
In addition to emergencies, there are obviously numerous examples in which this is the case. 3D printing has been used in indirect production to make molds, jigs and fixtures, positives for investment casting or as end parts that become part of an assembly made with traditionally made components. Evers noted the possibilities of such strategies for emergency applications.
“I think in emergency situations you really need to be creative with the technology you have at hand. You can create molds and then, based on your requirements, you can cast it in metal or even in silicon. You can fill it with different kinds of additives to create better properties,” Evers said.
Particularly worth noting in the case of emergency production of parts is the proprietary nature of those items. As Michigan Technological University’s Joshua Pearce argues, in order to properly respond to an emergency such as the COVID-19 pandemic, it is necessary for companies to make their goods open source, thus enabling engineers and emergency responders to produce replicas on the fly.
“Open source is, of course, of great use during the emergency situations. If you’re not limited to the functionalities of the machine, you can upgrade certain parts,” Evers said. “If you need a bigger application, you can rebuild it. You change some parameters. Maybe you have the material, which you normally injection mold with pellets, but you want to use it for 3D printing, you could modify the printer in that way, as well.”
Subscribe to Our Email Newsletter
Stay up-to-date on all the latest news from the 3D printing industry and receive information and offers from third party vendors.
Print Services
Upload your 3D Models and get them printed quickly and efficiently.
You May Also Like
Making 3D Printing Personal: How Faraz Faruqi Is Rethinking Digital Design at MIT CSAIL
What if your 3D printer could think more like an intelligent assistant, able to reason through a design idea, ask questions, and deliver something that works exactly the way the...
Reinventing Reindustrialization: Why NAVWAR Project Manager Spencer Koroly Invented a Made-in-America 3D Printer
It has become virtually impossible to regularly follow additive manufacturing (AM) industry news and not stumble across the term “defense industrial base” (DIB), a concept encompassing all the many diverse...
Heating Up: 3D Systems’ Scott Green Discusses 3D Printing’s Potential in the Data Center Industry
The relentless rise of NVIDIA, the steadily increasing pledges of major private and public investments in national infrastructure projects around the world, and the general cultural obsession with AI have...
Formlabs Teams Up with DMG MORI in Japan
In late June, Nick Graham, Chief Revenue Officer at Formlabs, announced on LinkedIn that the company had partnered with DMG MORI, one of the world’s leading machine tool companies, to...