3D printing has made significant impacts in nearly every industry, and on every scale too. This includes markets many may not have considered, unless they had a need for products like earbuds, hearing aids, or other communication devices fitted to the ear. Now, UK-headquartered ACS Custom is using additive manufacturing to improve production processes and further cater to customers seeking customized items related to hearing.
With the 3D Systems Figure 4 direction digital solution, ACS is taking advantage of the classic benefits 3D printing has to offer—mainly with speed in getting products to market, allowing them to remain competitive and increase efficiency. The custom solution includes:
- Figure 4 PRO-BLK 10 3D printing resin
- Figure 4 Standalone 3D printing system
- 3D Sprint software
- Application engineering services
Not only has ACS Custom been using Figure 4 for two years now, 3D Systems designed the 100% digital workflow solution exclusively for their unique applications. They have been able to increase production substantially, and are now able to offer their customers high-quality products—and access to complete customized articles—with “unparalleled surface finish.” New workflow through digital production has allowed for the following improvements:
- 4X increase in capacity
- 2X increase in efficiency
- Reduction of material usage by 50%
- Reduction of labor cost by 80% for one part
“Through collaboration with 3D Systems’ team, we’ve been able to maximize the technology’s role in our business and have elevated our company to a whole new level,” said Andy Shiach, the managing director of ACS Custom.
3D Systems’ Figure 4 PRO-BLK 10 material figures in predominantly to the workflow solution. As a photopolymer with thermoplastic characteristics, PRO-BLK 10 allows for greater industrial speed, precision, strength, and durability—surpassing the quality and production of more conventional methods like injection molding.
“This material has unique and compelling properties that represent significant improvements in first-time print yield, heat deflection, UV stability, durability, flexibility, and impact strength, while also enabling new biocompatible and direct digital production workflows such as the one designed for ACS,” states a recent press release sent to 3DPrint.com.
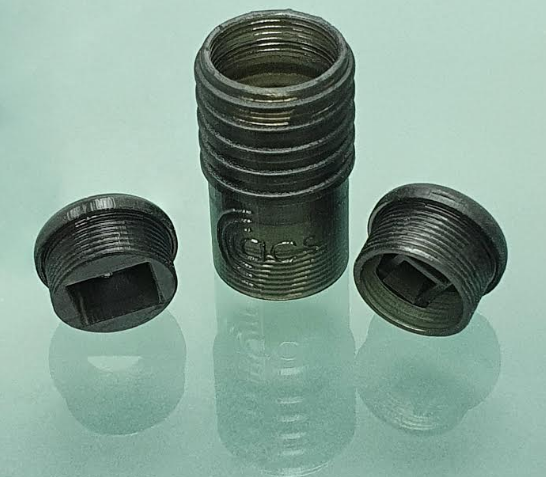
ACS produces this two pin comms adaptor for in-ear communication headsets using 3D Systems’ Figure 4 Direct Digital Production solution. The part comprises a central body and two end caps – one houses a 3.5mm stereo socket, the other includes spring contacts to work with the two pin connector from the radio. A very fine pitch metric thread is printed into the parts and they are functional without any special post-processing or thread cutting required. (Image courtesy of ACS Custom)
PRO-BLK 10 is biocompatible in terms of ISO10993-5 and ISO10993-10 standards, able to provide better sound and quality in hearing devices that will last a long time for the user.
ACS is using the 3D Systems’ Figure 4 Standalone 3D printer with 3D Sprint Software, enjoying speeds of up to 62 mm/hr at 50 micron layer thickness. ACS Custom is also 3D printing for eggshell casting, fabricating very thin walls to make molds that can then be injected with silicone, using Figure 4 EGGSHELL-AMB 10 material. After injection, the mold is cracked and peeled just like an eggshell—with the silicone part inside ready for post processing.
“3D Systems’ customer-centric solutions approach to innovation underlies everything we do—from understanding the customer workflow and application through to complete solution development,” said Scott Anderson, VP & segment leader for manufacturing & prototyping, 3D Systems.
“This highly market-driven approach allows our team the opportunity to engage unique applications for each customer and deliver solutions that propel their innovation and customer value to the next level. Our collaboration with ACS Custom showcases how the Figure 4 solution (hardware, software, and materials) enables direct and indirect digital production to increase efficiency, capacity, and flexibility, while concurrently offering superior end-part quality. This reinforces how additive manufacturing solutions can truly drive competitive advantage.”
While the direct production of hearing device parts may be limited to the small comms adapter pins above, ACS’s strategy is representative of a larger trend occurring in the field of audio electronics manufacturing. Relevant to this case is the story of Node Audio, which is also using the Figure 4 for production, specifically unique speaker components that can only be made with 3D printing. However, perhaps even more closely related is MoonDrop, a Chinese company that is using 3D printing to produce high-end, custom, in-ear monitors for professional audio engineers and luxury customers.
[Source / Images: 3D Systems]Subscribe to Our Email Newsletter
Stay up-to-date on all the latest news from the 3D printing industry and receive information and offers from third party vendors.
Print Services
Upload your 3D Models and get them printed quickly and efficiently.
You May Also Like
Making Space: Stratasys Global Director of Aerospace & Defense Conrad Smith Discusses the Space Supply Chain Council
Of all the many verticals that have been significant additive manufacturing (AM) adopters, few have been more deeply influenced by the incorporation of AM into their workflows than the space...
EOS in India: AM’s Rising Star
EOS is doubling down on India. With a growing base of aerospace startups, new government policies, and a massive engineering workforce, India is quickly becoming one of the most important...
PostProcess CEO on Why the “Dirty Little Secret” of 3D Printing Can’t Be Ignored Anymore
If you’ve ever peeked behind the scenes of a 3D printing lab, you might have caught a glimpse of the post-processing room; maybe it’s messy, maybe hidden behind a mysterious...
Stratasys & Automation Intelligence Open North American Tooling Center in Flint
Stratasys has opened the North American Stratasys Tooling Center (NASTC) in Flint, Michigan, together with automation integrator and software firm Automation Intelligence. Stratasys wants the new center to help reduce...