In 2019, a British startup unveiled aesthetically innovative high-end domestic loudspeakers prototyped and produced using 3D Systems’ selective laser sintering (SLS) and DuraForm GF material. The luxurious and tech-forward geometry of the HYLIXA speaker by Node-Audio (Node) promises a “cutting edge” experience that provides high sound quality in a package that doesn’t dominate a room, according to HiFi music experts. For 3D Systems, the distinctive and complex cabinet structure of the product represents a true departure and HiFi industry breakthrough, made possible by using SLS technology.
Node is the vision of two British industrial designers, Ashley May and David Evans. Inspired by the capabilities of additive manufacturing, they set out to deliver products that bring the emotional power of live music into the users’ home. Based in Cambridge, UK, the spiritual home of British HiFi, Node is a hub for audio research and innovation, claiming to challenge the current state-of-the-art in the pursuit of absolute musical purity. Node’s founders May and Evans consider their product as stunning acoustic sculptures that convey distinctly human feel that can also be considered an investment in emotional enjoyment for years. But most of all, they believe in taking advantage of the additive process to devise a high-value, high-performance product that is unique in a global HiFi system market that is expected to increase 28% in the next five years, as per a report by Research & Markets.
With access to a 3D Systems SLS 3D printer in their production facility at the ARCC Campus amidst the Cambridgeshire countryside, the duo set out to reconnect people with a new breed of HiFi system. Far from the traditional monolithic archetypical speaker boxes mounted within an enclosure that had largely disappeared in the early 2000s, the HYLIXA loudspeaker produces audio quality that the creators say rivals a live experience, with beautiful, sculptural aesthetics, thanks to 3D printing processes.
“It was like a fresh start for us as designers,” said Evans. “We’ve always known how to design things so they could be manufactured in a particular way, whereas this sort of threw everything out the window and opened up our imaginations to what was possible.”
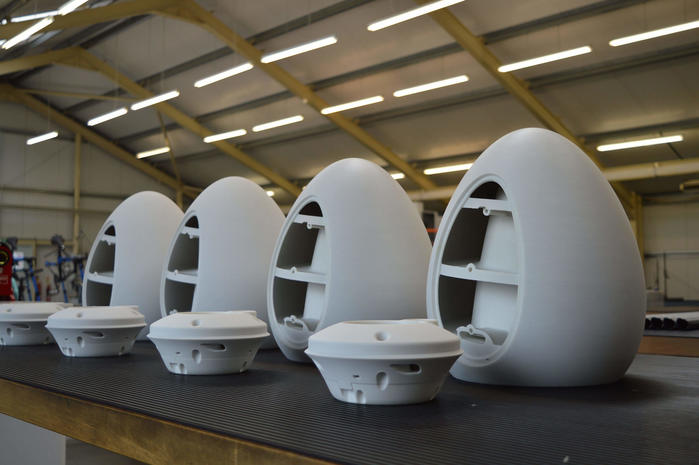
The team at Node maximizes each SLS build by nesting other components within the cabinet. (Image courtesy of Node-Audio)
3D Systems reported that the development process began with 3D designs from Evans and May that then ran through specialized 3D audio simulation software to inform the next iteration. Later on, as the simulation output began to confirm the next-level sound the team was after, they began to prototype and refine further, until finally arriving at Node’s flagship product, HYLIXA.

Node-Audio uses 3D printing to differentiate itself from the HiFi system market. (Image courtesy of Node-Audio)
Production and prototyping for the HYLIXA speakers are done using the 3D Systems sPro 60 SLS printer, with each of the two speakers in the set printed separately within the printer’s 381x330x460 mm build volume. Evans explained the team maximizes each build by nesting the other components within the speaker cabinet so that the cabinet and front baffle components are printed as a single unified part in DuraForm GF, a glass-filled engineering plastic that delivers a surface finish that is machinable and paintable and takes 45 hours to make. As the primary display piece of the speakers, Node puts the HYLIXA cabinets through a methodical post-processing regimen to remove the un-sintered powder, and prepare the surfaces for whatever finishing the customer requests.
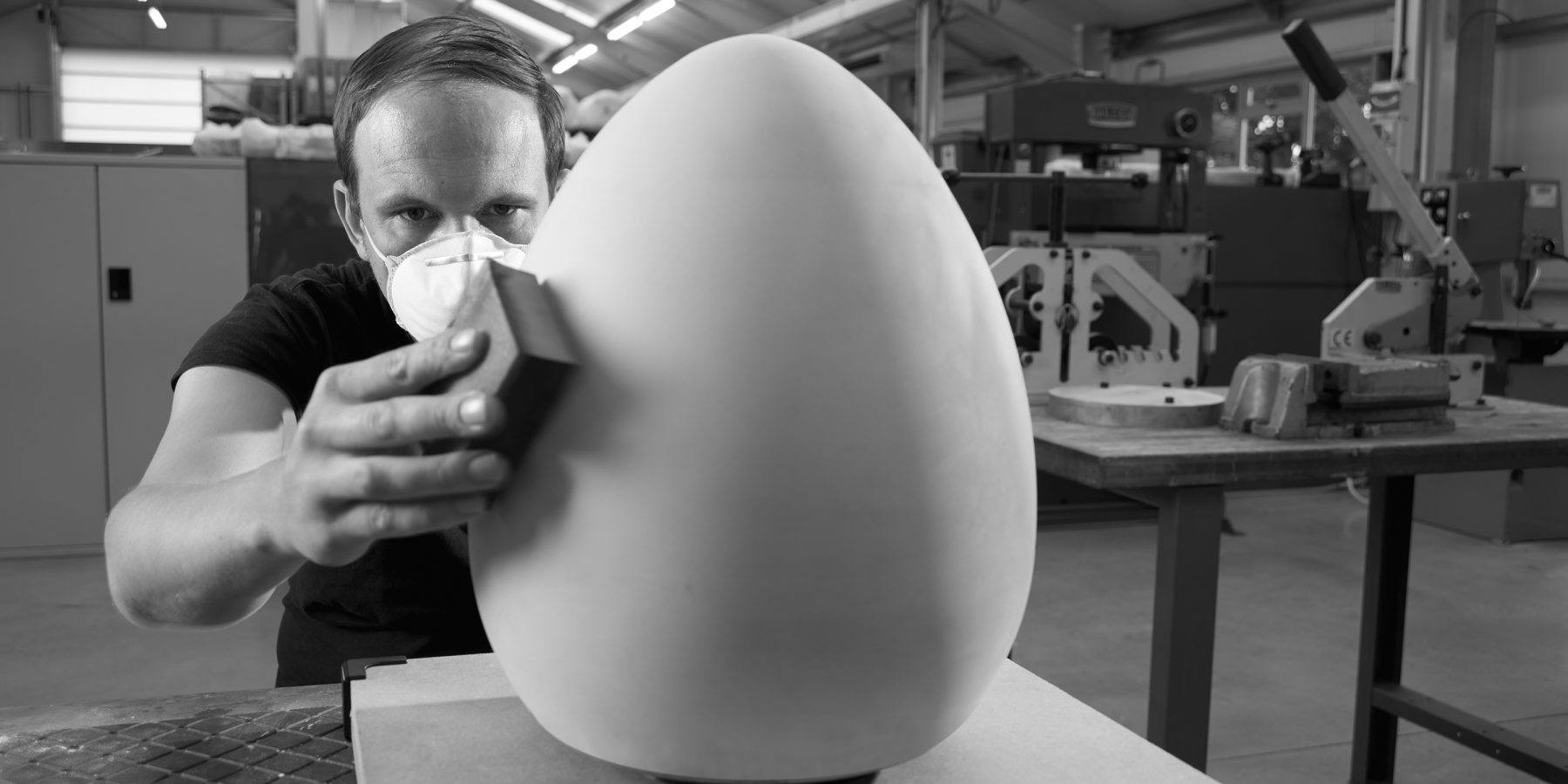
Providing the finishing touches to the 3D printed loudspeaker, post-processing at the lab. (Image courtesy of Node-Audio)
“We learned through the prototyping process that DuraForm GF actually worked very well acoustically. It has almost a ceramic-like quality to the touch, which helped us both structurally and sonically. As designers, we could freely exploit SLS production to create the internal structure, but also design something that looked as beautiful as it sounds,” indicated Evans. “Every component that we 3D printed, we’ve done for a reason. We’ve used the technology to benefit the product in one way or another, and pushed to take everything to the absolute limit.”
By leveraging the laser sintering technique, Evans and May claim to have devised the world’s first ‘helical bass’ enclosure. This internal helix acts as a waveguide to enhance bass performance, without compromising the acoustics in other areas. The patent-pending helical transmission line spirals for 1.6 meters around a conical cabinet interior. This line is fed by a dedicated bass driver and releases the sound through a circular vent around the mid and the tweeter. Because the rounded cabinet is designed and manufactured as a single piece, there are no edges to produce diffraction (a disruption to sound precision).

HYLIXA speakers feature a helical transmission line that spirals for 1.6 meters around the cabinet interior. (Image courtesy of Node-Audio)
At £30,000 (approximately $39,000) per set, the HYLIXA has a competitive edge thanks to 3D printing, embodying the kind of luxury that loudspeaker customers expect, from beautiful designs to high sound quality. But most of all, the SLS technology allows the designers to create complex cabinet geometry which would not be possible using more traditional manufacturing techniques. The creators suggest that by replicating the sonic signature of a human head, voices sound startlingly convincing, “as if the artist was in the room.” Moreover, reviews on many HiFi music gear sites have recognized HYLIXA as an aesthetically unique compact system and sonic treat.
For now, the product can be experienced at several British locations and in Tokyo, Japan, but after having earned credibility within the industry, Node-Audio is looking to grow. Part of the expansion involves new plans which are “very top secret” at the moment, but one thing is for sure, the designers remain committed to using 3D printing processes as an integral part of the company’s strategy to differentiate itself and do things that have never been done before.
Subscribe to Our Email Newsletter
Stay up-to-date on all the latest news from the 3D printing industry and receive information and offers from third party vendors.
Print Services
Upload your 3D Models and get them printed quickly and efficiently.
You May Also Like
Reinventing Reindustrialization: Why NAVWAR Project Manager Spencer Koroly Invented a Made-in-America 3D Printer
It has become virtually impossible to regularly follow additive manufacturing (AM) industry news and not stumble across the term “defense industrial base” (DIB), a concept encompassing all the many diverse...
Inside The Barnes Global Advisors’ Vision for a Stronger AM Ecosystem
As additive manufacturing (AM) continues to revolutionize the industrial landscape, Pittsburgh-based consultancy The Barnes Global Advisors (TBGA) is helping shape what that future looks like. As the largest independent AM...
Ruggedized: How USMC Innovation Officer Matt Pine Navigates 3D Printing in the Military
Disclaimer: Matt Pine’s views are not the views of the Department of Defense nor the U.S. Marine Corps Throughout this decade thus far, the military’s adoption of additive manufacturing (AM)...
U.S. Congress Calls Out 3D Printing in Proposal for Commercial Reserve Manufacturing Network
Last week, the U.S. House of Representatives’ Appropriations Committee moved the FY 2026 defense bill forward to the House floor. Included in the legislation is a $131 million proposal for...