Since the inception of the Industrialization and Digitalization of Additive Manufacturing (IDAM) project in March 2019, progress has been made: partners have been creating the promised digitalized AM pilot lines, and working on the three established phases of pre-printing, printing, and post-printing for automotive applications.
Funded by the German Federal Ministry of Education and Research (BMBF), the 20-million-euro initiative consists of the following 12 partners:
- Aconity GmbH, Herzogenrath
- BMW Group
- Concept Reply GmbH, Munich
- Fraunhofer Institute for Laser Technology ILT, Aachen
- GKN Powder Metallurgy, Radevormwald
- Myrenne GmbH, Roetgen
- Intec GmbH – Ingenieurbüro für Automatisierungstechnik, Bad Neuenahr-Ahrweiler
- Kinexon Industries GmbH, Munich
- Chair for Digital Additive Production DAP, RWTH Aachen, Aachen
- Technical University of Munich, Chair of Metal Forming and Casting, Munich
- Schmitz Spezialmaschinenbau GmbH, Rheinbreitbach
- Volkmann GmbH, Soest
Marking the halfway point for the project, the partners are heavily focused on constructing digital standards and the IoT overview for a comprehensive digital architecture. Most are either small to medium-sized business, committed to furthering progress with metallic 3D printing in the automotive industry.
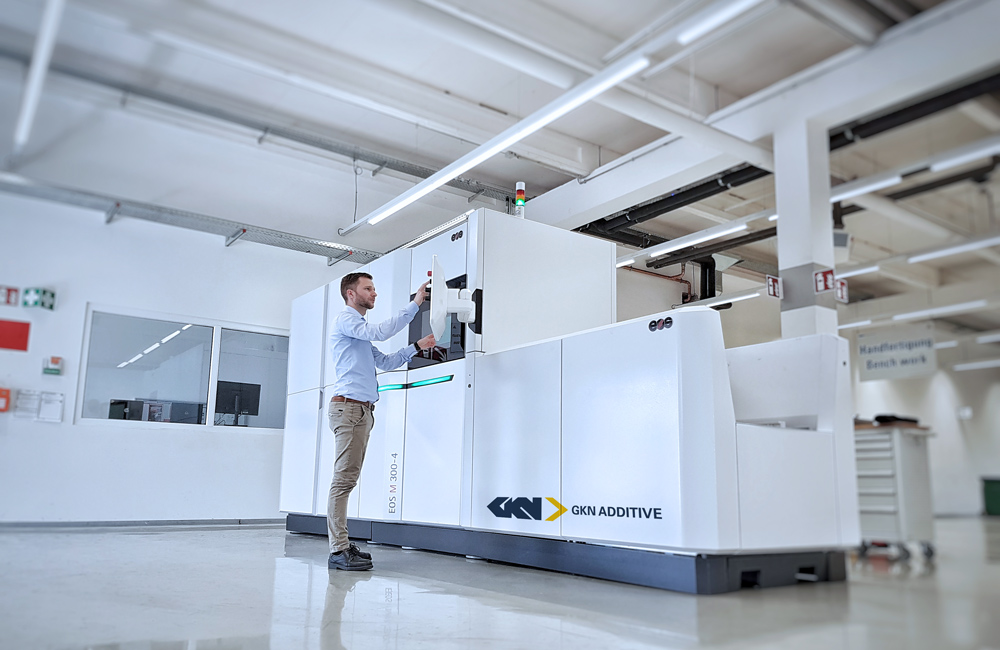
GKN Powder Metallurgy is currently validating a recently acquired EOS M300-4 quad-laser system, testing out multi-laser exposure strategies and pushing the system’s productivity (Image: GKN Powder Metallurgy)
Their goal is to consider the whole additive manufacturing process, integrating process chain modules, and creating a stable process for serial volume production. Pilot lines are being set up at the GKN Powder Metallurgy factory in Bonn, and also at BMW in Munich.
Laser powder bed fusion (LBPF) systems present a range of obstacles (from limited automation to its cost-prohibitive nature), making it difficult to establish the required reliability and versatility needed within the digital architecture, but at the Bonn site, the GKN PM team is testing out new strategies on an EOS M300-4 quad-laser system installed in May. GKN PM is also creating a new metal powder, DP 600, meant for industrial parts in automotive applications—allowing for mechanical properties to be adjusted with heat. The new powder offers the following:
- 13% elongation rate, as-built
- Up to 22 % elongation rate, with heat treatment
- Tensile strength of 950 MPA, as built
- Tensile strength up to 700 MPA, with heat treatment
The partners are testing concepts used in the pilot line modules, and expecting to have them all on site by the beginning of next year. The partners will be able to test and qualify systems, parts, and processes over the next year as they look toward the prototyping chapter—with the ultimate goal of fabricating more than 10,000 automotive parts annually.
The pilot line should not only be open-source, but also easily customized for any LPBF system. To decrease costs further, the use of water atomized powders will be explored in further experiments.
GKN continues to function as a “bridge” between project members, considering strategies that may be either academic or application centered. Find out more about BMW’s involvement in the project here, as well as the opening of their Additive Manufacturing campus here.
[Source: GKN Powder Metallurgy]Subscribe to Our Email Newsletter
Stay up-to-date on all the latest news from the 3D printing industry and receive information and offers from third party vendors.
You May Also Like
Model No. Deploys Titan Pellet 3D Printers for Sustainable Furniture Production
Over the years, many designers have tried to create 3D printed polymer furniture. Early pioneers like Janne Kyttanen, Materialise’s MGX, and Joris Laarman have led the way with 3D printed...
3D Printing News Unpeeled: Recycling PLA, More Efficient Atomizing
Filamentive hopes to recycle your PLA if you’re in the UK and order over £500 worth of filament. Their partner 3D Printing Waste (3DPW) will turn the PLA into injection...
Lighting the Way with Potato Starch: Sustainable Polish ECO Lamps Use 3D Printing
Lighting that meets the essence of nature: this is the reality brought to life by ECO Lamps, which introduces a fresh perspective to sustainable lighting design using potato starch. These...
3D Printing News Unpeeled: 3D Printed Construction Standard, Sand Wall & Self Heating Microfluidics
ISO/ASTM Standard 52939:2023 has been released and it sets standards for QA for 3D Printed polymer, composite and cement buildings. This is most welcome since 3D printed construction is a...