If you look at that crooked row of teeth one morning, the thought might occur that you could really use some invisible aligners. One of the earliest killer apps in 3D printing, this alternative to metal braces has proliferated wildly. Medgadget anticipates the global invisible aligners market to reach $8.2 billion by 2026.
As a method for producing patient-specific models on which these aligners are thermoformed, 3D printing continues to play a critical part in this segment, with SmarTech Analysis projecting a $317.3M revenue opportunity by 2028 for additive manufacturing (AM) and clear aligners. The Additive Manufacturing in Dentistry 2019: An Opportunity Analysis and Ten-year Forecast report covers this topic quite extensively, but this author thought it might be useful for those considering the use of invisible aligners to better understand the technology behind it and the options available on the market.
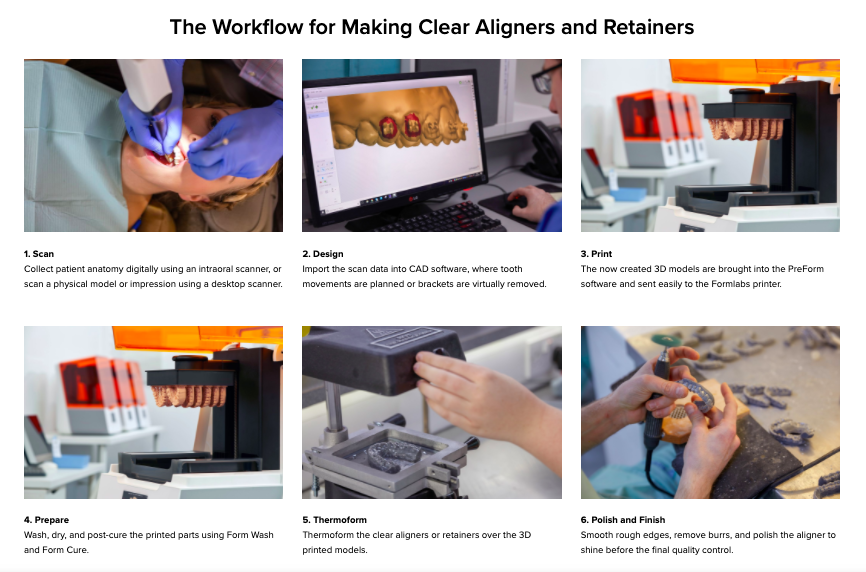
Screenshot from Formlabs’ website.
The production of dental aligners involves the use of specialty to develop a stepwise series of 30-40 designs meant to adjust a patient’s teeth based on scan data. The resulting models are then 3D printed and the actual aligners are made by thermoforming biocompatible plastic over the models. 3D printing is ideal for this purpose due to the high numbers of patient-specific models must be made. The future presents the increasing possibility of directly printed clear aligners, but, for the moment, AM serves as an indirect manufacturing tool.
Producing 220,000 clear aligners per day, Align Technologies, manufacturer of the Invisalign brand, pioneered the use of 3D Systems’ stereolithography (SLA) for this process. Its largest competitor is ClearCorrect, but the expiration of Align patents, the emergence of teledentistry, and the proliferation of 3D printing is changing the overall landscape. As the company’s patents have expired, there are a growing number of competitors. Consumers are now able to obtain clear aligners directly using at-home impression kits, while smaller dental and orthodontist businesses can use in-office 3D printers to create dental aligners.
With traditional clear aligners, not only do consumers have to see an orthodontist, but Invisalign packages can reach up to $9,500 in cost. This compares to direct-to-consumer products from companies such as Smile Direct Club, Candid and byte, which offer products that cost closer to $2,500. One site that reviews dental aligners describes Candid as the pickiest and costliest of the three and byte as the fastest and least expensive. Smile Direct is the most established.
What they make up for in time and cost may be paid for in terms of expert medical care. Without visiting a professional, who may perform dental and jaw x-rays for specifically tailored treatment, underlying dental issues may go unnoticed, according to experts from the Herman Ostrow School of Dentistry at the University of Southern California. For this reason, direct-to-consumer aligners are reserved for milder cases of teeth straightening. Even aligners that require an orthodontist, such as those from Invisalign, cannot tackle the same dental issues as braces, which can cost upward of $13,000.
Smile Direct Club is the largest direct-to-consumer aligner manufacturer, which makes it interesting in its own right, but is also notable for its use of HP’s Multi Jet Fusion technology for the production of thermoforming molds. This is in contrast to vat photopolymerization processes, like SLA and digital light processing, and material jetting, the two otherwise dominant technologies used to produce patient-specific thermoforming molds.
Vat photopolymerization systems range in cost from $3,000 to nearly $1 million and vary greatly in terms of throughput. Some machines, like those from Prodways, offer large batch production compared to desktop machines, from companies like Formlabs, provide small batch manufacturing more affordably. MJF, and potentially high-speed sintering, open up production runs of over 2,000 molds per machine daily. Whereas vat photopolymerization likely requires the greatest amount of post-processing, fast-production DLP machines from Carbon, EnvisionTEC, Carima and 3D Systems all open up the possibility of scalable, high throughput workflows. Material jetting technology is also used for the production of thermoforming molds, but to a lesser degree than the others.
As the technology progresses, however, we may see dental aligners become faster to make and more affordable. This is not only because numerous companies are developing software optimization and automation solutions for processing aligners with 3D-printed molds, but also directly printed aligners will likely emerge on the market.
The aforementioned SmarTech report points out that evidence can be found in the release of EnvisionTEC’s E-Ortholign material, which is meant for directly 3D printing “first aligners.” These are interim devices for patients after their brackets have been removed, but before thermoformed aligners can be made. Some orthodontists are using materials designed for bite splints to 3D print aligners directly. Once the right materials, software, workflows and FDA approval are achieved, directly printed aligners will likely become commercial.
If the existing businesses, which have already founded this indirect methodology for manufacturing aligners via thermoforming, are able to see a benefit to directly 3D printing aligners, then we may see the dental market upended once more. In the meantime, if you’re interested in something a little cruder, you can always try to make your own, like Amos Dudley did.
Subscribe to Our Email Newsletter
Stay up-to-date on all the latest news from the 3D printing industry and receive information and offers from third party vendors.
Print Services
Upload your 3D Models and get them printed quickly and efficiently.
You May Also Like
Making Space: Stratasys Global Director of Aerospace & Defense Conrad Smith Discusses the Space Supply Chain Council
Of all the many verticals that have been significant additive manufacturing (AM) adopters, few have been more deeply influenced by the incorporation of AM into their workflows than the space...
EOS in India: AM’s Rising Star
EOS is doubling down on India. With a growing base of aerospace startups, new government policies, and a massive engineering workforce, India is quickly becoming one of the most important...
PostProcess CEO on Why the “Dirty Little Secret” of 3D Printing Can’t Be Ignored Anymore
If you’ve ever peeked behind the scenes of a 3D printing lab, you might have caught a glimpse of the post-processing room; maybe it’s messy, maybe hidden behind a mysterious...
Stratasys & Automation Intelligence Open North American Tooling Center in Flint
Stratasys has opened the North American Stratasys Tooling Center (NASTC) in Flint, Michigan, together with automation integrator and software firm Automation Intelligence. Stratasys wants the new center to help reduce...