Researchers from Laboratoire de thermique et énergie de Nantes uncover some of the challenges in 3D printing versus thermoplastic injection, releasing the findings of their recent study in ‘Heat Transfer and Adhesion Study for the FFF Additive Manufacturing Process.’
Mechanical properties are often the topic of study today—from researching helpful additives to studying the influences of color, to issues with porosity, and far more—as users attempt to improve the functionality of parts. Adhesion between layers is a common problem, usually leading to further examination of technique and materials. In this study, the researchers focused on heat exchanges in an attempt to improve 3D printing.
Temperature remains one of the most important settings for users, leading to good quality and performance in printed parts—or in other unfortunate cases, major structural issues.
“To find precisely the limit of this optimal processing area, the thermal history needs to be predicted accurately,” stated the researchers.
With a better understanding of thermal factors, users may be able to avoid macro-porosities and adhesion problems. During FFF 3D printing, the following heat transfers occur:
- Heat from the extruder
- Convection cooling of filament
- Exchanges between filaments
- Heat from the support plates
- Radiative losses
- Heat from exothermal crystallization for semi-crystalline polymers
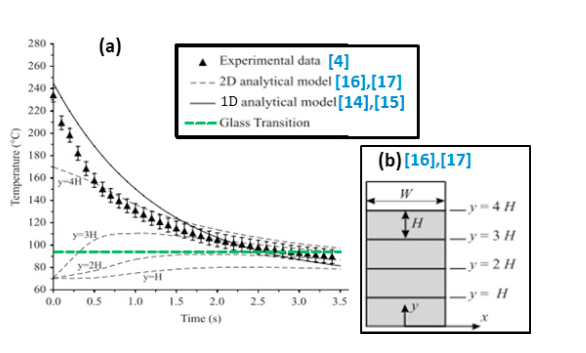
(a) Comparison of the heat transfer model existing in the literature of FFF process and (b) geometry for the 2D analytical model. Adapted from [7]

Experimental bench showing the heated chamber for 3D printing of high temperature polymers and the infrared camera for temperature measurements.
Before printing, the authors customized the 3D printer in their lab, modifying the hardware so it would be able to attain the proper temperatures of up to 400°C.
“The extruder was changed, for a full-metal unit, with a water-cooling closed circuit system. A closed insulated chamber maintains the part in a 200°C atmosphere. It does not block the three translation moving system of the 3D printer inside the chamber. Electronics and mechanical parts are kept outside the chamber. This heating chamber is mandatory for printing polymers like PEKK,” said the researchers.

Experimental set-up. A single filament wall was 3D printed. The pyrometer measures the temperature from the side in situ.
The other specimen was a basic structure 3D printed with both ABS and PEKK, in the form of a 60×2.2×50 mm wall. For ABS, the researchers took qualitative measurements with a pyrometer, with quantitative measurements taken for both ABS and PEKK.
“Because of the poor knowledge of the rheological properties, the calculated degree of healing was found to be equal to 1 very quickly for ABS. However, this is the opposite for PEKK material, which reaches only a degree of healing of 0.45 after the cooling-down of the filament,” concluded the researchers.
“The bench was designed to handle high temperature and future work will consist in studying deposition of PEKK more precisely, and also for carbon fibers reinforced PEKK with different process parameters. The short-term perspectives are to use the model with the thermo-dependent thermal properties, which were characterized in the LTeN laboratory on PEKK polymer.”
What do you think of this news? Let us know your thoughts! Join the discussion of this and other 3D printing topics at 3DPrintBoard.com.
[Source / Images: ‘Heat Transfer and Adhesion Study for the FFF Additive Manufacturing Process’]
Subscribe to Our Email Newsletter
Stay up-to-date on all the latest news from the 3D printing industry and receive information and offers from third party vendors.
Print Services
Upload your 3D Models and get them printed quickly and efficiently.
You May Also Like
The Market and Industry Potential of Multi-Material 3D and 4D Printing in Additive Electronics
Additive manufacturing leverages computer-based software to create components for products by depositing either dielectric or conductive materials, layer by layer, into different geometric shapes. Since its birth in the 1980s,...
3DPOD 262: Bio-inspired Design for AM with Dhruv Bhate, Arizona State University
Dhruv Bhate is an associate professor at Arizona State University. There, he looks at structures, materials, and design. Previously, he worked at PADT as well as in the semiconductor and...
3DPOD 261: Tooling and Cooling for AM with Jason Murphy, NXC MFG
Jason Murphy´s NXC MFG (Next Chapter Manufacturing) is not a generalist service; instead, the company specializes in making tooling. Using LPBF and binder jet, the company produces some of the...
3DPOD 260: John Hart on VulcanForms, MIT, Desktop Metal and More
John Hart is a Professor at MIT; he´s also the director of the Laboratory for Manufacturing and Productivity as well as the director of the Center for Advanced Production Technologies....