The role of composites continues to grow for 3D printing users engaged in a wide range of projects. In ‘Development of Thermal Resistant FDM Printed Blends. The Preparation of GPET/PC Blends and Evaluation of Material Performance,’ authors Jacek Andrzewski and Lidia Marciniak-Podsadna tackle the ongoing worldwide topic of improving materials for FDM 3D printing.
Andrzewski and Marciniak-Podsadna focus on the development of polymers with a base of polyethylene terephthalate copolymer/polycarbonate (GPET/PC). Polycarbonates are popular in applications like automotive, electronics, machine building, and more, divided into styrene polymers like acrylonitrile-butadiene-styrene (ABS) and acrylonitrile-styrene-acrylate (ASA), and thermoplastic polyesters from which materials like polyethylene terephthalate homopolymer (PET) and polybutylene terephthalate PBT are derived.
In evaluating the potential for performance in FDM 3D printing, the authors considered thermomechanical resistance to be the most important detail in testing—in comparison to many other studies centered around polycarbonate viscosity.
“The viscosity of materials intended for fused deposition modeling (FDM) printing is also one of the important parameters that can constitute a field for modification. Due to high viscosity of PC the plasticizing temperature can reach even 300 °C or more,” explained the researchers. “However, the main issue regarding the printing of PC-based materials is the warping tendency. The PC glass transition temperature (Tg ≈ 150 °C) is the reason for the negative phenomena during the printing process; the effects are shrinkage and deformation of models, therefore the use of a heated chamber during the process is necessary.
“Apart from the difficulties related to PC printing, its high thermomechanical resistance has great advantages in the context of applications.”
The researchers used a ZAMAK EH16D co-rotating twin-screw extruder, with an operating speed of 100 rpm. Dried pellets were extruded with a 3 mm die nozzle and temperature of 260 °C. Samples were then fabricated on a Prusa i3 MK3 printer, at 100 percent infill density, with a 0.4 mm brass nozzle.

The results of the mechanical test for static tensile and flexural method and notched Izod impact resistance test.
“Due to high viscosity of the pure PC filament, even at 285 °C, smooth printing was impossible, therefore the pure PC samples were prepared by injection molding,” stated the researchers. “Cubic samples with a side length of 50 mm were prepared to assess the accuracy of the printed model geometry.”
The GPET/PC (25/75) sample was the only one to exhibit substantial impact strength. The highest stiffness in composite samples was displayed in GPET/PC (50/50) samples. The GPET/PC (25/75) sample was the only one to show ‘significant double impact strength.’ And of noted interest was the PET/PC (50/50) blend, exhibiting the highest E module and strength.
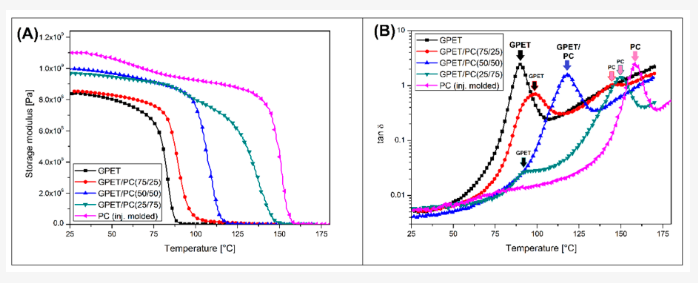
The results of the dynamic mechanical thermal analysis for polyethylene terephthalate copolymer/polycarbonate (GPET/PC) blends. (A) storage modulus thermograms and (B) tan δ curves.
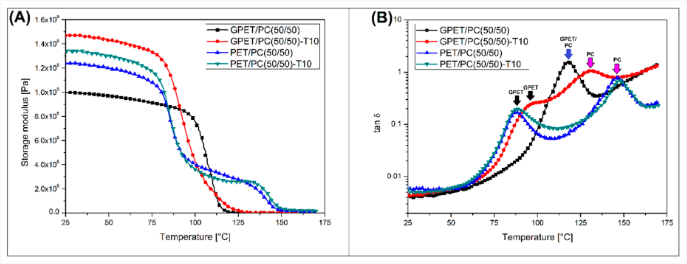
Storage modulus (A) and tan δ (B) plots for composite samples. The graphs compare the results for GPET/PC(50/50)-T10 and PET/PC(50/50)-T10 samples reinforced with 10% of talc, plots are combined with thermograms for unreinforced blends.
“Considering the balance of the mechanical, thermal and rheological properties of the prepared materials, the GPET/PC(50/50) blends were characterized by the best properties,” concluded the researchers.
“The thermal resistance of the PET/PC(50/50) samples was even higher, however, given the intended use as 3D printing materials, the addition of the PET phase significantly worsens the tendencies to shrinkage and deformation of printed models. The addition of talc particles strongly increases the stiffness of the GPET based blend, while the properties of the PET/PC(50/50)-T10 composites changed only slightly. The miscibility of GPET/PC systems, which in practice means that there is no need to use compatibilizers or reactive processing for blends of this type, is a noteworthy phenomenon. The properties of miscible blends are usually directly proportional to the content of individual polymers, according to the rule of mixture.”

Comparison of the 3D scans and real sample deformation for different types of GPET/PC. (A) pure GPET sample, (B) GPET/PC(75/25) sample, (C) GPET/PC(50/50) sample and (D) GPET/PC(25/75) sample.
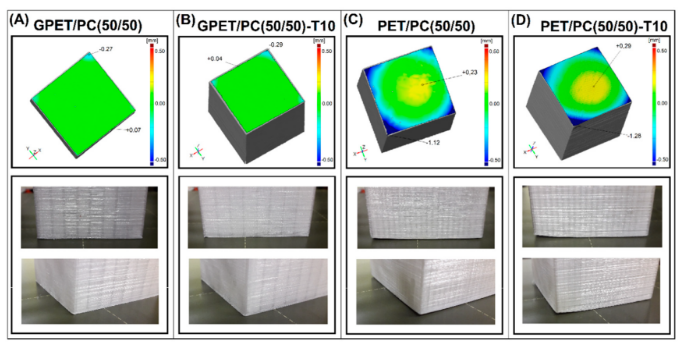
Comparison of the 3D scans and real sample deformation for 50/50% blends and composites. (A,B) GPET based materials and (C,D) PET-based samples.
Users everywhere continue to refine the process of FDM 3D printing, but also seek a variety of different materials, working with a variety of additives to create metal matrix composites, self-sensing composite fibers, nanocomposites, and a long list of other materials. What do you think of this news? Let us know your thoughts! Join the discussion of this and other 3D printing topics at 3DPrintBoard.com.
[Source / Images: ‘Development of Thermal Resistant FDM Printed Blends. The Preparation of GPET/PC Blends and Evaluation of Material Performance’]Subscribe to Our Email Newsletter
Stay up-to-date on all the latest news from the 3D printing industry and receive information and offers from third party vendors.
Print Services
Upload your 3D Models and get them printed quickly and efficiently.
You May Also Like
Making Space: Stratasys Global Director of Aerospace & Defense Conrad Smith Discusses the Space Supply Chain Council
Of all the many verticals that have been significant additive manufacturing (AM) adopters, few have been more deeply influenced by the incorporation of AM into their workflows than the space...
EOS in India: AM’s Rising Star
EOS is doubling down on India. With a growing base of aerospace startups, new government policies, and a massive engineering workforce, India is quickly becoming one of the most important...
PostProcess CEO on Why the “Dirty Little Secret” of 3D Printing Can’t Be Ignored Anymore
If you’ve ever peeked behind the scenes of a 3D printing lab, you might have caught a glimpse of the post-processing room; maybe it’s messy, maybe hidden behind a mysterious...
Stratasys & Automation Intelligence Open North American Tooling Center in Flint
Stratasys has opened the North American Stratasys Tooling Center (NASTC) in Flint, Michigan, together with automation integrator and software firm Automation Intelligence. Stratasys wants the new center to help reduce...