Andrew Finkle recently presented a thesis to the University of Waterloo, exploring the potential for more effective materials. In ‘Cellulosic Nanocomposites for Advanced Manufacturing: An Exploration of Advanced Materials in Electrospinning and Additive Manufacturing,’ Finkle continues the trend in refining techniques and additives for better performance.
This study centers around polymer nanocomposites; however, today researchers and manufacturers around the world are engaged in research using additives to create other unique materials too like composite hydrogels, bronze PLA, and composite SLS—all in hopes of accentuating specific projects which may require different mechanical properties or distinct features related to functionality.
In terms of hardware and techniques, Finkle examines both electrospinning and fused filament fabrication (FFF) for use with thermoplastic nanocomposites in the production of electrospun fiber mats and 3D printed parts. The new filaments developed in this study contain reinforcements like nanocrystalline cellulose (NCC), meant to improve mechanical properties over traditional methods.
Typical morphology of electrospun polyamide-6 nanofibers observed with scanning electron microscope [4].
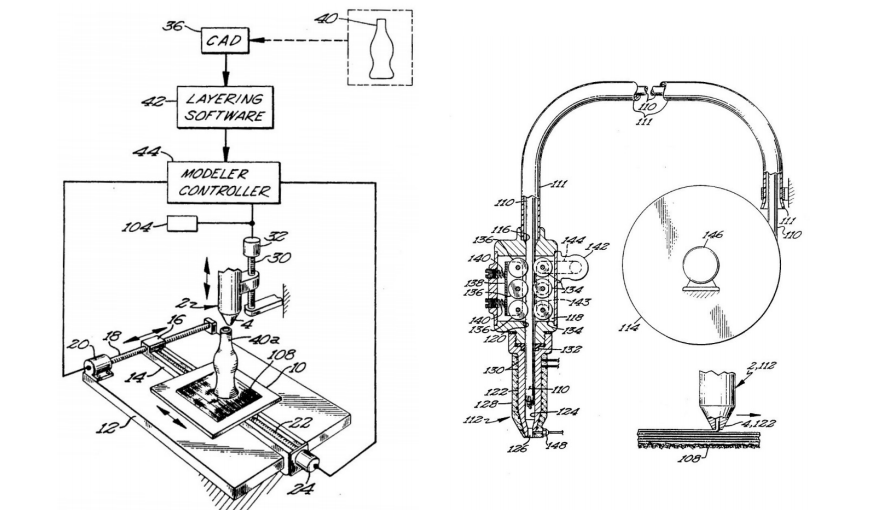
Schematic diagrams of fused deposition modeling (FDM) of thermoplastics from the patent “Apparatus and method for creating three-dimensional objects” by S. Crump including an FDM i) 3D printer and ii) extrusion head [8]
- Heat resistance
- Impact strength
- Rigidity
- Toughness
“The typical NCC whisker is on the order of 10 nm by 200 nm comprised of many cellulose β-glucan chains tightly bound together to form a very strong crystalline material,” explained Finkle. “The theoretical strength of NCC is on the order 9 of stainless steel and carbon nanotubes but unlike these inorganic reinforcements, is made from renewable and biocompatible sources.
“The high strength makes this nanoparticle a great candidate for incorporation into composites and more specifically electrospun nanofibers.”
Electrospun mat morphology was based on the following:
- Fiber diameter
- Bead diameter
- Bead density
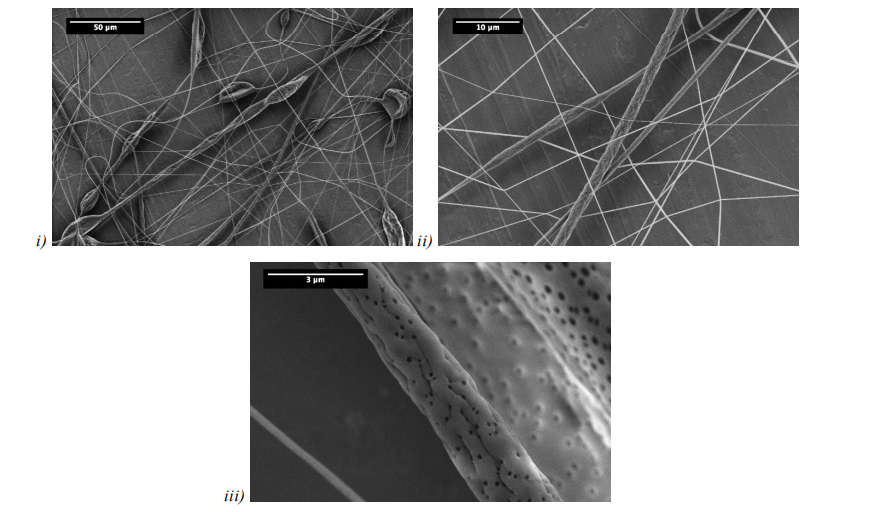
SEM micrographs of 15 wt-% PC nanofibers electrospun using chloroform. Fibers i) and ii) were electrospun using Vapp = 20 kV and iii) using Vapp = 15 kV over a gap distance of 15 cm.
“The formulation parameters chosen to explore within the DOEs are the polymer concentration in the solution, the concentration of additives (NCC). The processing parameters chosen to explore within each DOE included the applied voltage, Voltage, and gap distance, Gap Distance. Between the DOEs two other formulation parameters were explored,” explained Finkle.
“This included the solvent the polycarbonate solution was made in either a 60/40 (w/w) THF/DMF mixture or chloroform, both good solvents for PC. The second variable introduced between DOEs with the same solvent was 2-wt.-% of NCC (or DDSA-modified NCC, cNCC) in the solid mass (not including solvent).”

Standard order of experiments for a 23 full factorial DOE including the treatment shorthand notation and coded factor levels; high (1), center (0), and low (-1)
Design of experiments (DOEs) were investigated in terms of response to model fiber diameters in terms of:
- Function of the PC concentration
- NCC concentration
- Applied voltage
- Gap distance
Center-point measurements evaluated curvatures in the model, and solution properties were noted.

full factorial DOE#1, including the three different factors tested (coded a, b, and c) with their low (-1), high (+1), and center point (0) values
“For most of the experimentation, this involved: following a schedule, often electrospinning as soon as possible following sample preparation; minimizing any error in formulation and mixing of solutions; repeatable collection of nanofiber mats, as well as sample collection, preparation, and imaging of experimental specimens,” concluded Finkle.
“Although controlled as best as possible, some anomalies have still appeared. In particular, the center point replicates of DOE#4 – DDSA-modified Nanocrystalline Cellulose (cNCC) + Chloroform observed in Figure 4.30 show significant variance even though the experimental conditions were identical. This demonstrates that not only that electrospinning in volatile solvents like chloroform at room temperature is difficult to control, but that all possible variables for electrospinning must be considered carefully to achieve desired results.”
What do you think of this news? Let us know your thoughts! Join the discussion of this and other 3D printing topics at 3DPrintBoard.com.
[Source / Images: ‘Cellulosic Nanocomposites for Advanced Manufacturing: An Exploration of Advanced Materials in Electrospinning and Additive Manufacturing’]Subscribe to Our Email Newsletter
Stay up-to-date on all the latest news from the 3D printing industry and receive information and offers from third party vendors.
Print Services
Upload your 3D Models and get them printed quickly and efficiently.
You May Also Like
Reinventing Reindustrialization: Why NAVWAR Project Manager Spencer Koroly Invented a Made-in-America 3D Printer
It has become virtually impossible to regularly follow additive manufacturing (AM) industry news and not stumble across the term “defense industrial base” (DIB), a concept encompassing all the many diverse...
Inside The Barnes Global Advisors’ Vision for a Stronger AM Ecosystem
As additive manufacturing (AM) continues to revolutionize the industrial landscape, Pittsburgh-based consultancy The Barnes Global Advisors (TBGA) is helping shape what that future looks like. As the largest independent AM...
Ruggedized: How USMC Innovation Officer Matt Pine Navigates 3D Printing in the Military
Disclaimer: Matt Pine’s views are not the views of the Department of Defense nor the U.S. Marine Corps Throughout this decade thus far, the military’s adoption of additive manufacturing (AM)...
U.S. Congress Calls Out 3D Printing in Proposal for Commercial Reserve Manufacturing Network
Last week, the U.S. House of Representatives’ Appropriations Committee moved the FY 2026 defense bill forward to the House floor. Included in the legislation is a $131 million proposal for...