Authors Chanyeol Yoo, Samuel Lensgraf, Samuel Lensgraf, Lee M. Clemon, and Ramgopal Mettu detail their research for improvements in FDM 3D printing, outlined in the recently published ‘Toward Optimal FDM Toolpath Planning with Monte Carlo Tree Search.’
Most toolpath planning in FDM 3D printing consists of input models sliced into layers; however, this can lead to a lack of efficiency in motion at times, especially when the extruder may still be moving but not actually printing. In this study, the researchers set out to compute an efficient and optimal toolpath via a new algorithm using the Monte Carlo Tree Search (MCTS).
“A powerful general-purpose method for navigating large search spaces that is guaranteed to converge to the optimal solution,” the MCTS was analyzed within this study regarding its ability to improve searches.
“To our knowledge, this is the first algorithm for toolpath planning with any guarantees on global optimality,” stated the researchers.
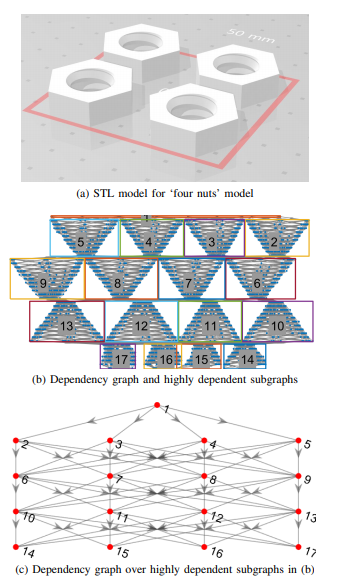
Example model of ‘four nuts’ (a) image, (b) labelled dependency graph, and (c) clustered dependency graph from (b)
Previously MCTS has been useful for solving problems in robotics applications, yielding the desired, greater efficiency in toolpath planning.
“Monte Carlo tree search algorithm is based on biased search algorithm for finding an optimal solution asymptotically. Starting at an initial condition, a tree grows at every iteration. The algorithm finds the next best node in a tree to expand using upper confidence bound (UCB), where UCB balances between exploitation and exploration. Intuitively, the node with higher likelihood of finding a better solution will be selected. Once a node is selected for expansion, one or a number of complete sequences is randomly generated from the node until reaching the end (e.g., end of time horizon),” explained the authors.
“In order to make our algorithm efficient, we also introduce a novel clustering algorithm on the dependency graph for the input model.”

An example illustrating clustering algorithm in Alg. 1. (1) 16 raw contours are clustered into three highly dependent subgraphs (HDS) as shown in (b).
With a dataset comprised of 75 models, use of the MCTS method did demonstrate ‘substantial reduction’ in wasted motion. The authors noted that MCTS performance was like that of their current local search toolpath planner, but overall made it easier for them to investigate difficult in planning with some models.

‘Four nuts’ model. Toolpath for building the part by (a)(d) typical layerwise planner, (b)(e) local search from [6], and (c)(f) proposed MCTS, with red indicating non-printing motion. The solution toolpath for each method is shown in red. Extrusionless distances (in mm) are 16737, 12220 and 11057, respectively.
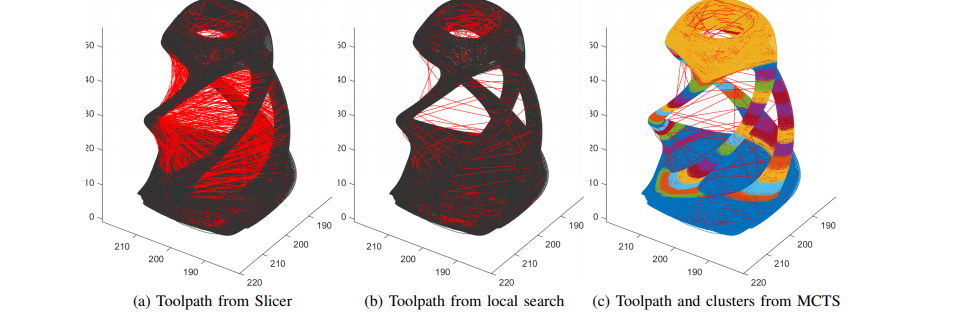
‘Twisty’ model. Toolpath for building the part by (a) typical layerwise planner, (b) local search from [6], and (c) proposed MCTS, with red indicating
non-printing motion. Solution toolpath for each method is shown in red. Extrusionless distances (in mm) are 25021, 11423 and 11306, respectively.
“A natural question is why one would use MCTS over local search for a given model. Using our empirical studies, it appears that the output of the clustering step and subsequent composition of HDS components of the dependency graph provide guidance as to whether MCTS can achieve convergence,” concluded the researchers.
“As we saw in our empirical analysis if there enough HDS components with respect to the size of the dependency graph then it is highly likely that MCTS will converge to an optimal toolpath. If the number of HDS components is too large, or the average size is too small, then MCTS will have difficulty exploring the toolpath space and may perform worse than local search.”
Researchers around the world continue to study ways to refine and use FDM 3D printing, from experimenting with new materials to fabricating innovative medical devices. What do you think of this news? Let us know your thoughts! Join the discussion of this and other 3D printing topics at 3DPrintBoard.com.
[Source / Image: ‘Toward Optimal FDM Toolpath Planning with Monte Carlo Tree Search’]Subscribe to Our Email Newsletter
Stay up-to-date on all the latest news from the 3D printing industry and receive information and offers from third party vendors.
Print Services
Upload your 3D Models and get them printed quickly and efficiently.
You May Also Like
The Market and Industry Potential of Multi-Material 3D and 4D Printing in Additive Electronics
Additive manufacturing leverages computer-based software to create components for products by depositing either dielectric or conductive materials, layer by layer, into different geometric shapes. Since its birth in the 1980s,...
3DPOD 262: Bio-inspired Design for AM with Dhruv Bhate, Arizona State University
Dhruv Bhate is an associate professor at Arizona State University. There, he looks at structures, materials, and design. Previously, he worked at PADT as well as in the semiconductor and...
3DPOD 261: Tooling and Cooling for AM with Jason Murphy, NXC MFG
Jason Murphy´s NXC MFG (Next Chapter Manufacturing) is not a generalist service; instead, the company specializes in making tooling. Using LPBF and binder jet, the company produces some of the...
3DPOD 260: John Hart on VulcanForms, MIT, Desktop Metal and More
John Hart is a Professor at MIT; he´s also the director of the Laboratory for Manufacturing and Productivity as well as the director of the Center for Advanced Production Technologies....