Gas metal arc welding (GMAW) additive manufacturing is a more affordable metal technology, with a high deposition rate for potentially fabricating medium and large components. Van Thao Le, with Le Quy Don Technical University in Vietnam, has published a paper, titled “A preliminary study on gas metal arc welding-based additive manufacturing of metal parts,” that centers around investigating the mechanical properties and internal quality of components 3D printed using a GMAW robot.
GMAW-based technology is better for manufacturing metal parts with large dimensions than gas tungsten arc welding (GTAW) and plasma arc welding (PAW) methods because of its higher deposition rate. It’s important to achieve high internal quality of GMAW-printed parts, which is why it’s necessary to gain a better understanding of their microstructures – particularly when the component will be used in a load-bearing condition. This technology is consistently used in Vietnam because of its lower cost, so manufacturers should know all they can about the method in order to attain good results.
“Therefore, the objective of this study is to investigate the internal quality of thin-walled parts manufactured by the GMAW-based AM process. The results obtained in this study allow us to demonstrate the feasibility of using the GMAW robot for manufacturing or repairing/remanufacturing of metal components according to the AM principle,” the author wrote.

Figure 1. (a) Schema of the GMAW-based AM system, (b) built thin-walled sample, (c) positions for cutting the specimens, & (d) five zones for observing microstructures and measuring the hardness on a cut surface of the specimen.
An industrial GMAW robot built a thin-walled component using the wire arc additive manufacturing (WAAM) process, out of mild steel copper-coated welding wire on a low-carbon steel substrate plate. The 6-axis robot used a welding torch to deposit layers from the substrate, and you can see the welding process parameters in the table below.
“The distance between the GMAW torch and the workpiece was 12 mm. The deposition was conducted at room temperature and without preheating the substrate,” Le explained. “Once the deposition of a welding layer was finished, the welding torch is retracted to the beginning point for the deposition of the next layer with a dwell time of 60 seconds. The dwell time used between two successive layers aims at cooling down the workpiece and transferring accumulated heat to the environment.”
A wire-cut electrical discharge machining (EDM) machine was used to cut two groups of tensile specimens from the thin-walled sample, so that the author could measure the built material’s hardness, using a digital microhardness tester, get a closer look at its microstructures with an optical microscope, and test the tensile properties.
“Before cutting these specimens, two side surfaces of the built thin wall were machined to obtain an effective width of the built thin-walled materials,” Le wrote.
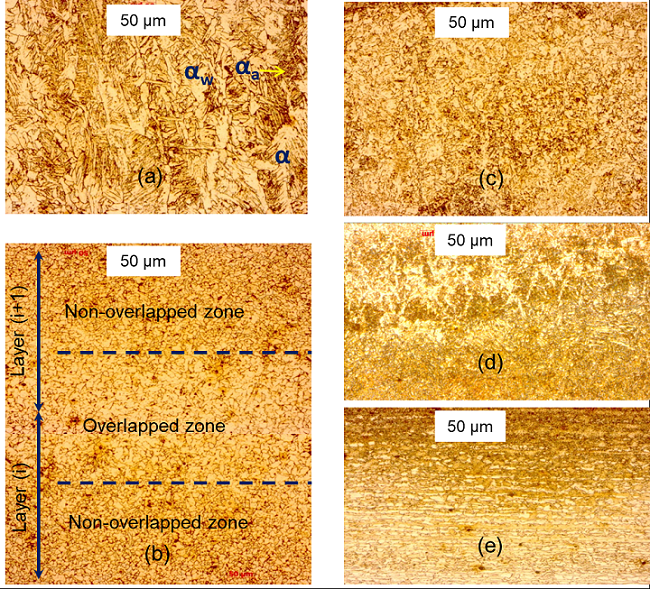
Figure 3. Microstructures of built materials observed in five zones: (a) upper zone, (b) middle zone, (c) lower zone, (d) heat-affected zone (HAZ), and (e) substrate zone.
The specimen’s microstructure was observed in five different zones. The upper zone, which features three types of ferrite grains and a high variation of thermal and high-cooling rates, has “lamellar structures with primary austenite dendrites” that distribute perpendicular to the substrate. The middle zone has two types of grains, and mostly features “the granular structure of ferrites with small regions of pearlites at grain boundaries.” The microstructures found in the lower zone, which has a slower cooling rate than the upper, are made of “equiaxed grains of ferrite, in which thin lamellae are distributed and coexisting with thin strips of pearlite.” These grains are finer than the ones in the middle zone, because the value of thermal shock is higher here.
In the heat-affected zone (HAZ), the microstructures transfrom from austenite to martensite, while the substrate zone features ferrite/perlite banded microstructures – the total opposite of the middle zone’s “homogenous distribution of phases.”
The above table shows the hardness (HV) measurement in the five zones. The upper zone had the highest HV, while the middle had the lowest, and the HAZ’s value was slightly lower than the substrate zone.
Specimens were tested on a tensile machine, and Le also figured the engineering strain-stress curves.

Figure 4 . Tensile tests with two specimens TSv1 and TSh1: (a) Installation of the specimen on the tensile test machine, (b) the broken specimens after the tensile tests, and (d) the engineering stress-strain curves.
“The hardness (ranged between 164±3.46 HV to 192±3.81 HV), yield strength (YS offset of 0.2% ranged from 340±2 to 349.67±1.53 ), and ultimate tensile strength (UTS ranged from 429±1 to 477±2 ) of the GMAW-based AM-built components were comparable to those of wrought mild steel,” he explained.
“There is also a significant difference in terms of YS and UTS between the vertical and horizontal specimens due to non-uniform microstructures of built materials. Moreover, the mechanical properties of the thin-walled component built by the GMAW-based AM process are comparable with those of parts manufactured by traditional processes such as forging and machining.”
This study found that the metal components built by GMAW-based robotic AM have “adequate and good mechanical properties for real applications.” Le concluded that it is feasible to use a GMAW robot to 3D print parts that can be used in industrial applications.
Discuss this research and other 3D printing topics at 3DPrintBoard.com or share your thoughts in the Facebook comments below.
Subscribe to Our Email Newsletter
Stay up-to-date on all the latest news from the 3D printing industry and receive information and offers from third party vendors.
Print Services
Upload your 3D Models and get them printed quickly and efficiently.
You May Also Like
Could 3D Printing for Biocomputing Make Wetware Aware?
As an AI arms race consumes ever more electricity, and every ChatGPT search query costs $0.36, the search for new ways of computing has intensified. One answer could be in better...
Bambu Lab Launches Software to Manage 3D Printer Fleets—No Cloud Needed
Bambu Lab has introduced a new software tool, Bambu Farm Manager, designed to help users manage large fleets of 3D printers over a local network, without relying on the cloud....
Consolidation in AM: How 2025 Is Shaping the Industry’s New Normal
The first half of 2025 has been marked by a clear shift in the additive manufacturing (AM) industry. Companies are no longer just focused on developing new tech by themselves....
3D Printing News Briefs, July 2, 2025: Copper Alloys, Defense Manufacturing, & More
We’re starting off with metals in today’s 3D Printing News Briefs, as Farsoon has unveiled a large-scale AM solution for copper alloys, and Meltio used its wire-laser metal solution to...