Researchers Jakub Marchewka and Jadwiga Laska from AGH University of Science and Technology in Poland are working to process new material blends for FDM 3D printing in tissue engineering, outlining their results in the recently published ‘Processing of poly-L-lactide and poly(L-lactide-co-trimethylene carbonate) blends by fused filament fabrication and fused granulate fabrication using RepRap 3D printer.’
As materials science becomes a huge topic of study within the 3D printing and additive manufacturing world for a wide range of applications spanning from automotive to aerospace to construction and much more, finding suitable polymers in the medical field for research in areas like tissue engineering continues to be a challenge due to the intrinsic difficulties in sustaining cells.
In this study, Marchewka and Laska are exploring biodegradable polymers like semi-crystalline poly(L-lactide) (PLLA) and amorphous poly(L-lactide-co-trimethylene carbonate) for processing on an open source RepRapPro Tricolour Mendel.
“The form of filament was desired because of its simple application using the standard low-cost 3D printer,” explained the researchers.
Four sample types were created in the form of porous, cylindrical scaffolds (15.15mm in diameter and 1.20mm in height) with porosity of 65%, 55%, 45%, and 35% (35%, 45%, 55%, and 65% infill, respectively). Poronterface software was used with the RepRap printer as the researchers fabricated twenty different runs of each sample type.
PLLA and PLLATMC are both suitable for processing via FDM 3D printing due to:
- Different mechanical properties which allow for creation of a ‘wide range’ of blends
- Thermoplastic qualities
- Commercial availability of medical grade quality
Using both 80:20 PLLA:PLLATMC and 30:70 PLLA:PLLATMC (wt.%) blends, the researchers were able to apply the materials for two separate type of tissues such as bone or cartilage. They noted that ‘thermal properties were similar for both blends.’
To produce the 80:20 PLLA:PLLATMC blend, resulting in a ‘high-quality filament,’ the researchers employed two steps, with granulate as the intermediate. They produced the filament with a diameter of 1.71 ± 0.04 mm, pointing out that the general standard for commercial materials is 1.75 ± 0.05 mm.
For the 30:70 PLLA:PLLATMC blend, however, there was difficulty in creating the desired material due to the blend’s lack of suitable material properties:
“For 80:20 PLLA:PLLATMC blend, the printer was applied in standard configuration using the material in the form of filament. However, for 30:70 PLLA:PLLATMC blend, it was necessary to adapt the device and install an appropriate module to process the granulate.”

3D printer in the standard (a) and modified (b) configuration adapted for the processing of filament or granulate, respectively
The printer was customized for use with the materials with the installation of a new module. The main parts include:
- NEMA 17 stepper motor
- Shaft coupling
- 8 mm diameter screw
- 40 W ceramic heater
- 100 k thermistor
- Aluminum heating block
- 4 mm nozzle
- Insulation
- Two cooling turbine fans
Quality of printing was assessed by resolution, accuracy, precision, and tolerance.
“Detailed characterization of the samples shows that both FFF and FGF could be applied for the preparation of the scaffolds with high quality appropriate for their potential application in tissue engineering,” concluded the researchers. “FFF in comparison with FGF provides the higher precision and accuracy of the method, but the overall procedure is longer.
“In general, FGF is a more versatile method which could be applied to various thermoplastic polymers also with the additives when the brittleness of material makes the preparation of the filament difficult. However, for this method, the slightly worse quality of the product should be taken into consideration with regard to the specific requirements.”
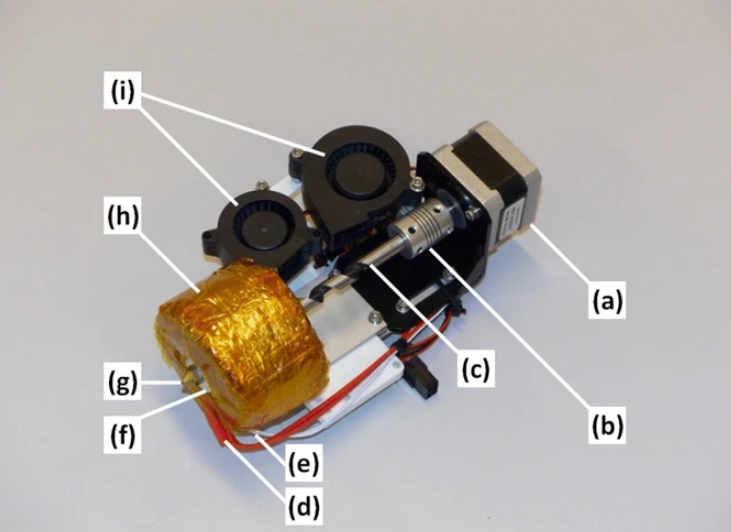
New module applied for the processing of material in the form of granulate (letters indicate the parts referred in the text)
What do you think of this news? Let us know your thoughts! Join the discussion of this and other 3D printing topics at 3DPrintBoard.com.
[Source / Images: ‘Processing of poly-L-lactide and poly(L-lactide-co-trimethylene carbonate) blends by fused filament fabrication and fused granulate fabrication using RepRap 3D printer’]Subscribe to Our Email Newsletter
Stay up-to-date on all the latest news from the 3D printing industry and receive information and offers from third party vendors.
Print Services
Upload your 3D Models and get them printed quickly and efficiently.
You May Also Like
Heating Up: 3D Systems’ Scott Green Discusses 3D Printing’s Potential in the Data Center Industry
The relentless rise of NVIDIA, the steadily increasing pledges of major private and public investments in national infrastructure projects around the world, and the general cultural obsession with AI have...
Formlabs Teams Up with DMG MORI in Japan
In late June, Nick Graham, Chief Revenue Officer at Formlabs, announced on LinkedIn that the company had partnered with DMG MORI, one of the world’s leading machine tool companies, to...
EOS in India: AM’s Rising Star
EOS is doubling down on India. With a growing base of aerospace startups, new government policies, and a massive engineering workforce, India is quickly becoming one of the most important...
3D Printing News Briefs, June 25, 2025: R&D Materials, 3D Printed Veneers, & More
In today’s 3D Printing News Briefs, 3DXTECH has launched a program that gives customers early access to experimental materials, and the first Lithoz CeraFab Multi 2M30 in the Czech Republic...