Researchers from Canada and India are delving further into the science of materials in 3D printing, outlining their findings in the recently published ‘Microstructural evolution and mechanical behavior of nickel aluminum bronze Cu-9Al-4Fe-4Ni-1Mn fabricated through wire-arc additive manufacturing.’

TEM-Bright field micrograph showing Fe3Al precipitate (κII that is not associated with NiAl lamellae) by an arrow with corresponding CBED pattern taken at [001¯] zone axis.
NAB is strengthened because of its additives, and offers the ‘outstanding advantage’ of being able to transform during solidification:
“The absorption of aluminum from the matrix by κ-phases extends the apparent range of the α-field. As a result, under equilibrium conditions, no eutectoid formation occurs and β is not retained below 600 °C unless the aluminum content goes beyond 11%, compared to 9.5% in the Cu-Al binary system. The precipitation of κ-phases in the α-matrix increases the mechanical strength considerably without a significant reduction in ductility.”
Historically, parts made from NAB are expensive to produce, leaving manufacturers to weld parts in maintenance and repair—rather than just making them again. This is not a perfect system by any means, however, as NAB alloys are vulnerable to serious issues like porosity, cracking, and distortion. These problems stem from high thermal conductivity and expansion.
Researchers have tried the following to strengthen mechanical properties:
- Heat treatment
- Changes in composition
- Plastic deformation
- Friction stir processing
- Nickel ion implantation
- Thermal diffusion of Ni coating
- Laser surface melting
- Laser surface alloying
“The limitation with surface modifying treatments is that they can only improve the corrosion resistance and mechanical properties of the surface layer instead of the bulk material. Heat treatment and plastic deformation techniques such as FSP have some limitations and are hard to use to process heavy castings such as ship propellers,” explained the researchers.
“Overall, NABs are metallurgically complex alloys in which small variations in the compositions can result in the formation of markedly different microstructures, which can, in turn, result in significant variations in seawater corrosion resistance.”
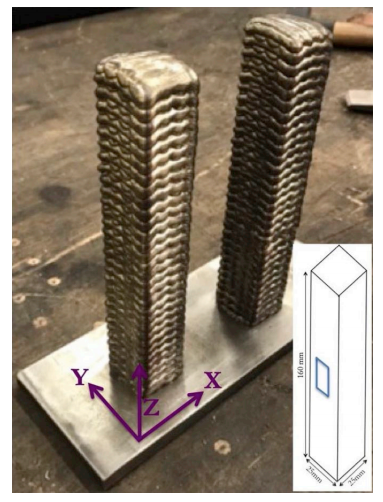
Photograph of nickel aluminum bronze square bars produced by WAAM. Inset shows the dimensions (not to scale; side: 25 mm and height: 160 mm) of the schematic bar. Blue rectangular box in the inset shows the location of the sample used for microstructural characterization. (For interpretation of the references to color in this figure legend, the reader is referred to the web version of this article.)
In this study, however, the researchers point out that additive manufacturing offers ‘superior’ results, and especially with more recent forays into wire-arc additive manufacturing (WAAM)—a technique using a wire instead of atomized powder.
Industrial users can produce large parts with WAAM, also enjoying:
- Full density
- High deposition rate
- High material utilization
- Low equipment cost
For WAAM-NAB samples in this study, the researchers used GTarc 60-5 WAAM equipment, featuring gas-metal arc welding (GMAW). Cast samples were created too. Mechanical properties were evaluated, and overall there were tests performed on up to five samples as the team worked to ‘confirm repeatability of the tests.’
Ultimately, the researchers decided that WAAM techniques are effective in use with the NAB alloy if low temperatures are used. Samples demonstrated ‘excellent layer bonding,’ with no defects, and reheating resulted in no ‘detrimental’ microstructural changes.

(a) Low and (b) high magnification optical micrographs at the location of fracture in a WAAM tensile specimen. No preferential cracking along layer interface or HAZ bands.
“Heat treatments in the range of 500–600 °C may result in increasing the volume fraction of fine-κIV precipitates, which may increase the strength levels of WAAM-NAB,” concluded the researchers.
“Overall, the prospects of WAAM to produce NAB seem very bright and it can significantly widen the scope and applicability of additive manufacturing to produce NAB parts and components, mainly for the marine industry. Further work towards the effect of various heat treatments on microstructure, mechanical properties, and corrosion resistance would be highly beneficial.”
The use of wire-arc continues to be of interest to researchers and manufacturers interested in trying new techniques that include 3D printing with metal, integration with robotics, and further exploration.
What do you think of this news? Let us know your thoughts; join the discussion of this and other 3D printing topics at 3DPrintBoard.com.
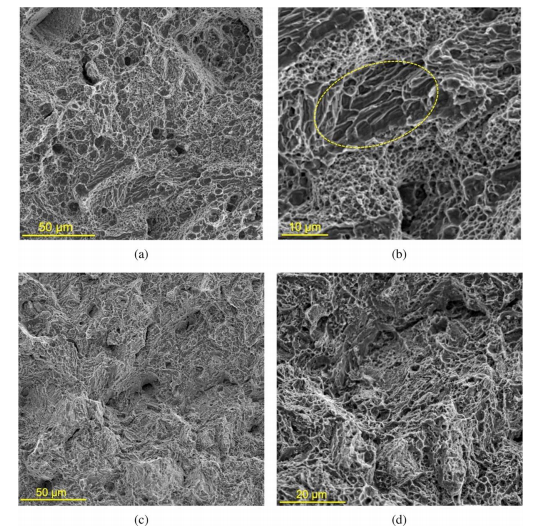
SEM fractographs of (a and b): Cast, and (c and d): WAAM samples. Encircled region in (b) shows flat fracture features due to the presence of coarse intermetallic phase.
Subscribe to Our Email Newsletter
Stay up-to-date on all the latest news from the 3D printing industry and receive information and offers from third party vendors.
Print Services
Upload your 3D Models and get them printed quickly and efficiently.
You May Also Like
3D Printing News Briefs, June 28, 2025: Defense Accelerator, Surgical Models, & More
In this weekend’s 3D Printing News Briefs, 3YOURMIND was selected to join an EU Defense Accelerator, and PTC has announced model-based definition (MBD) capabilities within Onshape. Finally, a study out...
3D Printing News Briefs, June 7, 2025: Digital Inventory, Thermal Management Solutions, & More
In this weekend’s 3D Printing News Briefs, UK-based 3D printing bureau 3D People responds to global instability, and AEWIN chose Fabric8Labs’ technology for advanced thermal management solutions. We’ll end with...
Low-Cost Binocular Indirect Ophthalmoscope Made with CAD Software & Bambu Lab X1C
3D printing is increasingly used in the fabrication of diagnostic equipment, including ophthalmology, which is a medical specialty that deals with the diagnosis and treatment of eye conditions and diseases....
3D Printing News Briefs, May 17, 2025: Color-Changing Materials, Humanoid Robot, & More
We’re covering research innovations in today’s 3D Printing News Briefs! First, Penn Engineering developed 3D printed materials that change color under stress, and UC Berkeley researchers created an open source,...