US researchers delve further into soft robotics, outlining their findings in the recently published ‘Soft Somatosensitive Actuators via Embedded 3D Printing.’ Developing a new method relying on soft somatosensitive actuators (SSAs) embedded in 3D printed structures, the researchers focus on an effective way to combine conductive features with elastomeric matrices.
Today, 3D printing, soft robotics, and sensors often seem to accompany one another—and in this study, the scientists combined three SSAs within a gripper, allowing them to show proprioceptive and haptic feedback via embedded features such as curvature, inflation, and contact sensors.
“Harnessing the temperature-dependent ionic conductivity of the SSAs’ contact sensors coupled with our free-form fabrication process, we also created SSAs with temperature and deep-versus-fine touch contact sensing, respectively, which have not yet been realized by other soft robotic actuators,” stated the researchers.
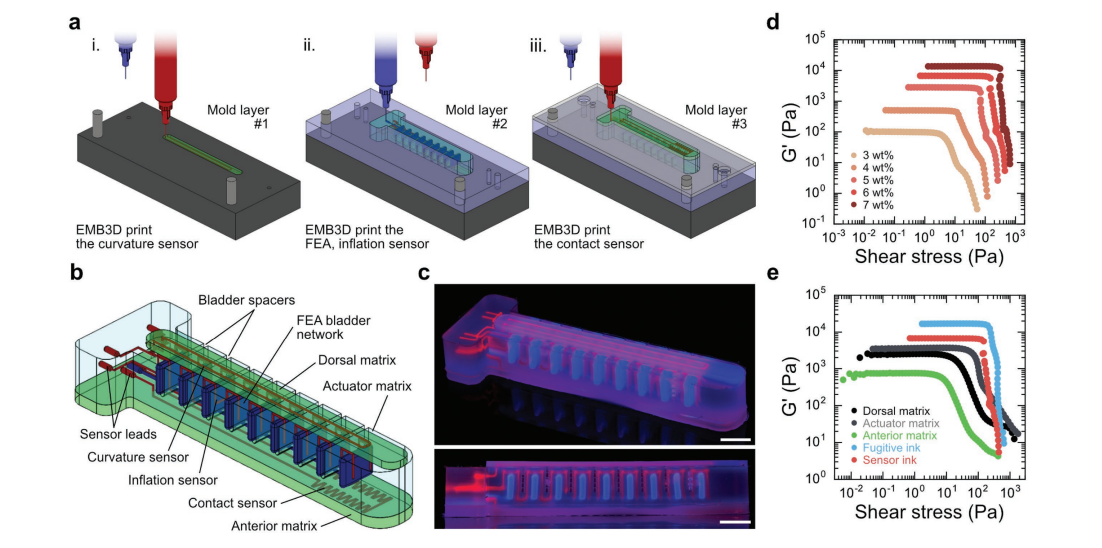
Fabrication of soft somatosensitive actuator (SSA) innervated with multiple soft sensors. a) The curvature sensor is printed within the dorsal matrix (Layer 1); the actuator features and inflation sensor are printed within the actuator matrix (Layer 2); and the contact sensor is printed in the anterior matrix (Layer 3). b) Schematic illustrations and c) images of the final SSA. The images in (c) are taken under black light exposure, and the fugitive (blue) and sensor (red) inks have been fluorescently dyed to facilitate visualization (scale bars are 10 mm). d) Log–log plot of storage modulus, G′, as a function of shear stress for sensor inks composed of 1-ethyl-3-methylimidazolium ethyl sulfate with varying fumed silica content (wt%). e) Log–log plot of G′ as a function of shear stress for all matrix materials and inks used for constructing these SSAs via EMB3D printing.
Conductive inks are printed within three matrices:
- Dorsal
- Actuator
- Anterior matrix
With those materials loaded, the researchers could print the following:
- Curvature sensor in the dorsal matrix
- FEA features (including actuator spacers and bladder network) and inflation sensor in the actuator matrix
- Contact sensor in the anterior matrix
Upon completion of printing and curing, SSAs are removed from their molds. From there, ‘fugitive ink is evacuated,’ leaving behind empty channels for electrical leads to be inserted. Success is based on each elastomeric matrix demonstrating suitable rheological properties. The SSAs must be able to bend correctly, with all sensors able to deform as well as increase when faced with resistance.
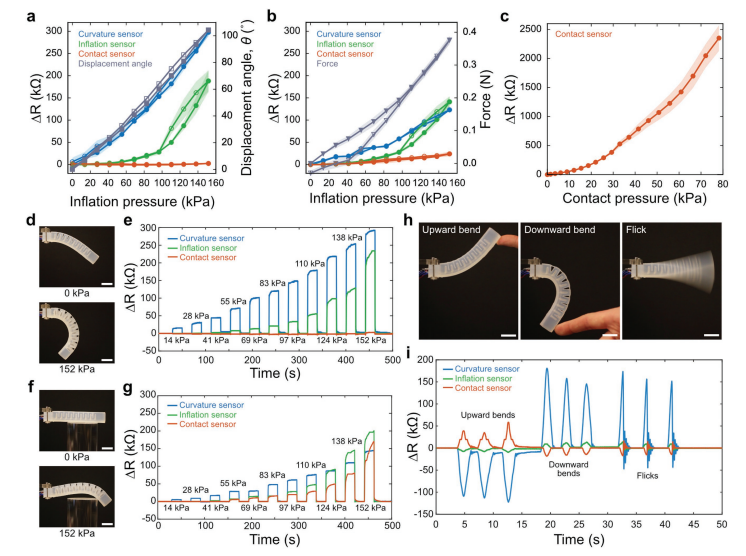
Performance of soft somatosensitive actuators. a) Resistance change, ΔR, for the curvature, inflation, and contact sensors and displacement angle, θ, as a function of inflation pressure during free displacement. b) ΔR for each sensor and force generated as a function of inflation pressure during blocked displacement. c) ΔRcontact as a function of applied contact pressure. For (a)–(c), data points and shaded regions represent mean values and standard deviations, respectively, (n = 3). d) Images of an SSA at 0 kPa (top) and 152 kPa (bottom) during a dynamic free displacement test, in which the SSA experiences periods of no inflation (0 kPa for 20 s) to increasing inflation pressure (held for 20 s) in increments of 14–152 kPa. e) ΔR of each sensor is plotted as a function of time. f) Still images of an SSA inflating against an acrylic rod at 0 kPa (top) and 152 kPa (bottom) during a dynamic blocked displacement test, in which the SSA is actuated via the same inflation sequence as in (d) and (e). g) ΔR for each sensor is plotted as a function of time. h) Upward bend (left), downward bend (middle), and flick-style (right) manipulations carried out on a noninflated SSA. i) ΔR for each sensor is plotted as a function of time for an SSA undergoing a sequence of three upward bends, three downward bends, and three flicks. All scale bars are 20 mm.
Made up of an organic ionic liquid (1-ethyl-3-methylimidazolium ethyl sulfate (EMIM-ES) filled with fumed silica particles), the sensor ink used in this study is a rheology modifier, offering the following benefits:
- Low vapor pressure
- Nonpermeability through elastomeric matrices
- Suitable resistivity for sensing applications
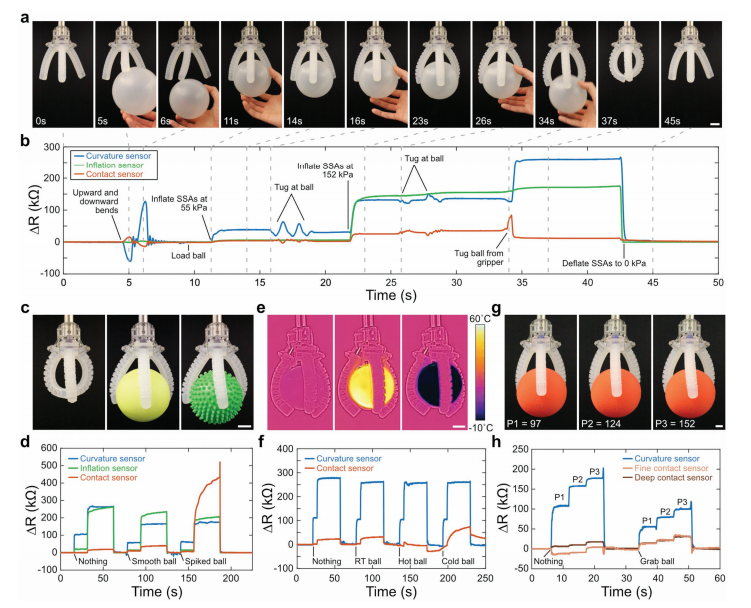
Soft robotic grippers with somatosensory feedback. a) Images of an interaction sequence between a ball and a soft robotic gripper comprised of SSAs (see Movie S5 in the Supporting Information; scale bar is 20 mm). b) ΔR of each sensor as a function of time during the interaction sequence shown in (a). (Note: The noninflated gripper (t = 0 s) had one SSA bent upward (t = 5 s) and downward (t = 6 s) before the ball is inserted into the gripper. The gripper is then inflated to 55 kPa (t = 11 s) to hold the ball (t = 14 s) even when manually tugged (t = 16 s). The inflation pressure is increased to 152 kPa for a stronger grip (t = 23 s). After additional tugging (t = 26s), the ball is removed from the gripper (t = 34 s), which remains inflated at 152 kPa (t = 37 s). The gripper is deflated at t ≈ 43 s.) c) Still images show the gripper holding nothing (left), a smooth ball (middle), and a spiked ball (right) (see Movie S6 in the Supporting Information; scale bar is 20 mm). d) ΔR for each sensor is plotted as a function of time. e) Thermal images of a gripper holding a room temperature (RT) ball, a hot ball (≈60 °C), and a cold ball (≈0 °C) (see Movie S7 in the Supporting Information; scale bar is 20 mm). f) ΔRcurvature and ΔRcontact plotted as a function of time. g) Still images showing a gripper comprised of SSAs with embedded fine and deep contact sensors holding a foam ball at 97 kPa (P1), 124 kPa (P2), and 152 kPa (P3) (see Movie S9 in the Supporting Information; scale bar is 10 mm). h) The ΔRcurvature, ΔRfine, and ΔRdeep are plotted as a function of time for the sequence shown in (g).
“Each sensor consists of a resistive strain gauge whose electrical resistance is given by R = ρL/A, where ρ is the resistivity, L is the length, and A is the cross-sectional area of the printed ionogel features,” explained the researchers. “The change in resistance, ΔR, during operation is given by ΔR = R − R0, where R0 is the initial resistance.”
As the three SSAs were combined in creating the soft robotic gripper for this study, the researchers noted that as the device was used to reach out for various balls, each SSA inflated—and all in an identical manner, with sensory feedback received from the center SSA.
“We clearly observe the kinesthetic nature of the inflation sensor by removing the ball from the inflated gripper, as ΔRinflation remains somewhat constant. R for all sensors returned to ≈R0 once the SSAs were deflated,” explained the researchers.
In experimenting with temperature, they noted the following:
“When grabbing the RT ball at 165 kPa, ΔRcontact is ≈9 kΩ greater than that for when the gripper holds nothing at 165 kPa. When grabbing the hot ball, ΔRcontact decreases noticeably, even becoming negative, due to the local increase in the contact sensor’s conductivity where the distal meander made contact with the ball. Finally, when grabbing the cold ball, a clear increase in ΔRcontact is observed that exceeds the value of ΔRcontact for the same ball held at RT. When the gripper releases the hot and cold balls, ΔRcontact does not immediately return to the value of 0 kΩ measured at RT.”
Ultimately, the team realized that for this sample, the SSAs were not capable of handling contact pressure and temperature of objects in a ‘straightforward’ way, leading them to note that for the future they would need to create additional sensors with different materials, or incorporate machine learning methods.
They created fine and deep contact sensors too, made up of different receptive fields—like fingers. During experimentation, the research team arranged for a soft foam ball to be ‘grabbed’ during three different levels of inflation.
“For each inflation pressure, ΔRfine is negative or ≈0 kΩ when the gripper grabs nothing and increases noticeably when grabbing the ball. The deep contact sensor is less sensitive, but ΔRdeep is still ≈8, 10, and 12 kΩ greater when grabbing the ball at P1, P2, and P3, respectively, than when grabbing nothing,” stated the researchers.
In conclusion, the authors state that their study represents a ‘foundational advance’ to be used for applications such as soft robotics, wearable, and haptic devices. This is an area of study being pursued by researchers around the world, tackling projects to include 3D printed biomimetic devices, 4D printed soft robotics, new metamaterials, and a variety of different sensors.
What do you think of this news? Let us know your thoughts; join the discussion of this and other 3D printing topics at 3DPrintBoard.com.
[Source / Images: ‘Soft Somatosensitive Actuators via Embedded 3D Printing’]Subscribe to Our Email Newsletter
Stay up-to-date on all the latest news from the 3D printing industry and receive information and offers from third party vendors.
Print Services
Upload your 3D Models and get them printed quickly and efficiently.
You May Also Like
3D Printing News Briefs, July 2, 2025: Copper Alloys, Defense Manufacturing, & More
We’re starting off with metals in today’s 3D Printing News Briefs, as Farsoon has unveiled a large-scale AM solution for copper alloys, and Meltio used its wire-laser metal solution to...
3DPOD 260: John Hart on VulcanForms, MIT, Desktop Metal and More
John Hart is a Professor at MIT; he´s also the director of the Laboratory for Manufacturing and Productivity as well as the director of the Center for Advanced Production Technologies....
3D Printing News Briefs, June 28, 2025: Defense Accelerator, Surgical Models, & More
In this weekend’s 3D Printing News Briefs, 3YOURMIND was selected to join an EU Defense Accelerator, and PTC has announced model-based definition (MBD) capabilities within Onshape. Finally, a study out...
EOS in India: AM’s Rising Star
EOS is doubling down on India. With a growing base of aerospace startups, new government policies, and a massive engineering workforce, India is quickly becoming one of the most important...