Rochester Institute of Technology: Effects of Annealing & Isostatic Pressure on 3D Printed Nylon Parts
In submitting ‘Annealing of Fused Filament Fabricated Nylon 6 with Elevated Isostatic Pressure’ as a thesis for a Master of Science degree at Rochester Institute of Technology, Anthony G. Tantillo explores the effects of pressure on 3D printed parts. This study also explored the benefits of raising printing parameters such as temperature, annealing parts to improve properties like tensile strength.
While realizing the benefits of 3D printing, a technology that has been progressing since the 1980s, Tantillo is also realistic about ongoing challenges in fabrication such as layer adhesion and more, to include:
- Lower density than bulk polymer values
- Poor strength metrics
- High point stresses
- 2D inaccuracies from intended models
“Correcting these negatives will expand upon the field of traditional manufacturing and allow 3DP to become a reliable means to end-product goals,” states Tantillo.
Investigating FDM 3D printing as it is one of the most popular routes—along with the use of common materials like ABS and PLA, Tantillo points out that this method is beneficial for users due to low print times and a wide range of materials available; however, there are other issues specific to FDM printing too such as a lack of resolution, accuracy, and isotropic strength. Such challenges may not affect users as much when they are focused on printing prototypes but must be addressed when moving forward to fabricate functional parts.
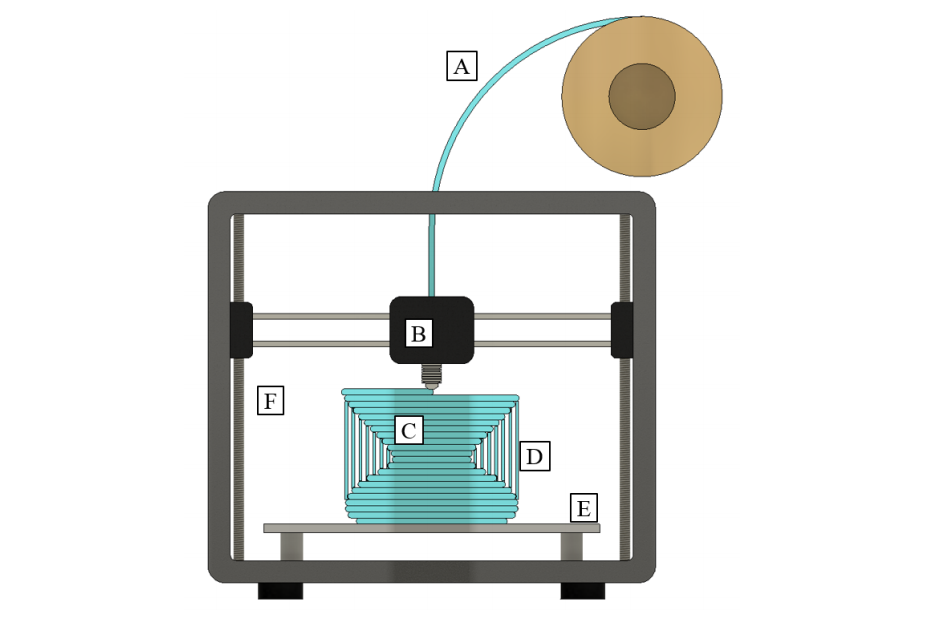
Schematic of a gantry style FFF 3D printer and its constituent parts. As depicted, the hotend carriage moves in all linear directions: X,Y, and Z. (A) Filament feedstock (B) Filament extruder and hot end carriage (C) Printed model (D) Support material (E) Build plate (F) Build volume.
“This process also has the inherent problem of introducing voids between extruded roads. This is due to elliptical road cross sections not being well suited for packing efficiency. These interior voids lead to a lowered part strength when compared to the bulk material,” states Tantillo.
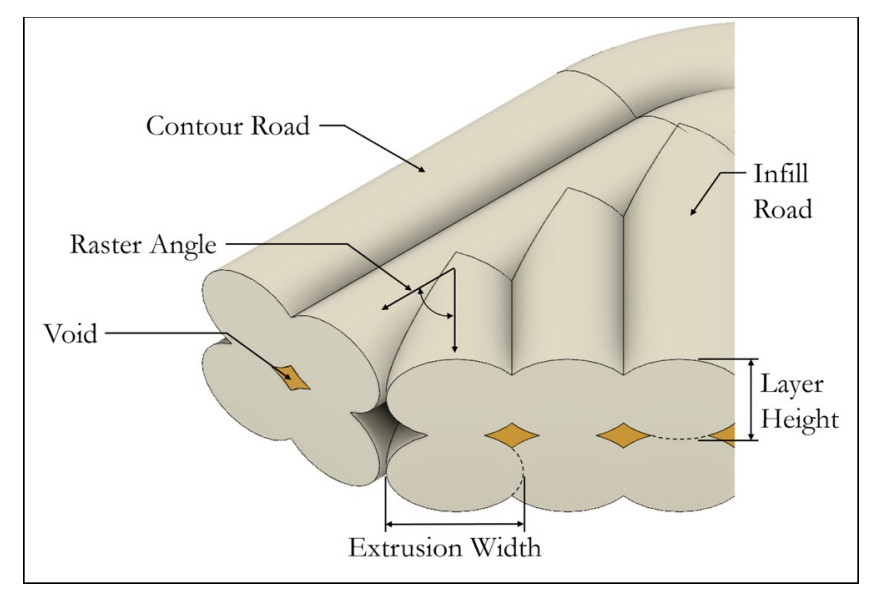
Section view of a FFF printed part showing the commonly varied process parameters. This part is shown with a fully dense infill pattern at a 45° angle. Dashed lines are added to the roads to show printed width and height before necking.
In this study, the focus was on 3D printing with a thermoplastic: polyamide 6 (PA6, Nylon 6), known for its uses within the engineering community due to high impact and tensile strength. As a nylon, however, PA6 may lead to adhesion issues and warpage and is quick to break down due to water absorption.
“Although a challenge to use, PA6 is desirable due to its prevalence in manufacturing today,” states Tantillo.
Annealing is a process often used with plastics to adjust their shape or structure for better performance. In 3D printing, annealing may be used to increase strength. While not using high temperatures, the process does rely on heat over ‘a longer time span’ to strengthen polymers. Slow heating and slow cooling allow polymer chains to fall into order, yielding improved packing efficiency and higher crystallinity with greater density—resulting in greater tensile strength but also brittleness.
In studying how isostatic pressure during annealing affects parts, the researchers used an Intamsys Funmat HT 3D printer with Markforged Tough Nylon 6.
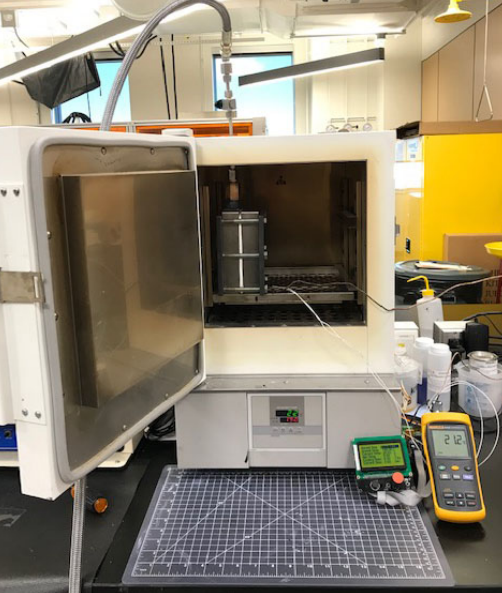
Setup of the furnace with the pressure chamber inside. The Arduino LCD panel and Fluke logger are set to the right of the furnace. The pressure hose is connected to the pump, not in the picture.
3D printing parameters for the study were set for success in fabrication with the ultimate part strength. While Tantillo experienced numerous initial failures—mainly because of warping—he discarded those samples and continued refining the process, along with making a compression chamber consisting of the following parts:
- Chamber and clamping plates
- Packing/gasket material
- Pressure fittings
- Pump
Tantillo was surprised to find that the actual pressure tests did not align with strength increases shown in pre-study results.
“Although it was shown that the crystallinity of the parts increased with annealing, the typical increase in yield strength did not accompany it,” concluded Tantillo. “Similarly, with high applied pressure, the internal voids were significantly affected, but did not seem to affect part yield strength. The modulus for all parts did however increase for all tensile bars and some flexural bars. The impact energy was greatly affected by the annealing and decreased for all tested parts under all conditions. It was shown that applied pressure and heat is a viable method for compaction of internal voids in FFF parts, but not for increased part performance.
“The brittle fracture mode was only evident in one set of part and parts performed over as-printed ones. This is all to say that applied pressure as done in this thesis is not a viable post-processing method for strengthening FFF parts. More care needs to be taken to account for the way pressure is applied to the surface of the part and the environment it is held in.”

Temperature data for all of the eight runs done. The linear portion of the cooldown turns to exponential, but only after Tg (dashed line).
Studies regarding FDM 3D printing, as well as annealing, are expansive, from continued work in improving tensile strength to reducing warpage with other materials, studying the effects of annealing in bioprinting, and more.
What do you think of this news? Let us know your thoughts! Join the discussion of this and other 3D printing topics at 3DPrintBoard.com.
[Source / Images: ‘Annealing of Fused Filament Fabricated Nylon 6 with Elevated Isostatic Pressure’]Subscribe to Our Email Newsletter
Stay up-to-date on all the latest news from the 3D printing industry and receive information and offers from third party vendors.
Print Services
Upload your 3D Models and get them printed quickly and efficiently.
You May Also Like
U.S. Navy Lab Uses 3D Printing to Reduce Tooling Lead Time By Over 90%
The F-35 Lightning II Joint Program Office (JPO), responsible for life-cycle management of the key fifth-generation joint strike fighter (JSF) system used by the U.S., its allies, and its partners,...
Etsy Design Rule Change Reduces Selection of 3D Printed Goods
Online marketplace Etsy has implemented a rule change requiring all 3D printed goods on the site to be original designs. The update to the site’s Creativity Standards states, ¨Items produced using...
Honeywell Qualifies 6K Additive’s Nickel 718 for 3D Printed Aerospace & Defense Parts
6K Additive is renowned for manufacturing sustainable additive manufacturing (AM) powder, and offers a wide portfolio of premium metal and alloy powders that include titanium, copper, stainless steel, and nickel,...
MetalWorm Sells WAAM Systems to Research Institutes in Brazil and Malaysia
Turkish WAAM firm MetalWorm has sold a system in Malaysia and another in Brazil. This is an excellent example of a few emerging trends in additive. Firstly, WAAM was experimented...