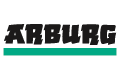
In addition to prototyping, ARBURG Plastic Freeforming (APF) with the Freeformer is particularly suitable for the industrial additive manufacturing of functional components. This offers the advantage of supporting the processing of plastic granules in the same form in which they are used in conventional injection molding. These include biocompatible, resorbable, sterilisable and FDA-approved original materials. This opens up a range of new possibilities, both in the field of medical technology as well as for use within the human body
The market for additive manufacturing is growing rapidly and offers an interesting production technology solution to complement injection molding. With its know-how in plastics processing spanning decades as well as the Freeformers, Arburg provides both experts and newcomers with innovative solutions for industrial additive manufacturing.
Functional components for medical technology
APF with the Freeformer is an “open system” that provides the user with access to Arburg’s material database as well as allowing them to process their own original plastics and optimize the process control themselves. Alternatively, they can access Arburg’s database. The APF process offers freedom in terms of materials. For medical technology, the Freeformer has manufactured, for example, resorbable implants such as cranial, cheek, and finger bones made from medical PLLA (Purasorb PL18, Resomer LR 708) using additive methods.
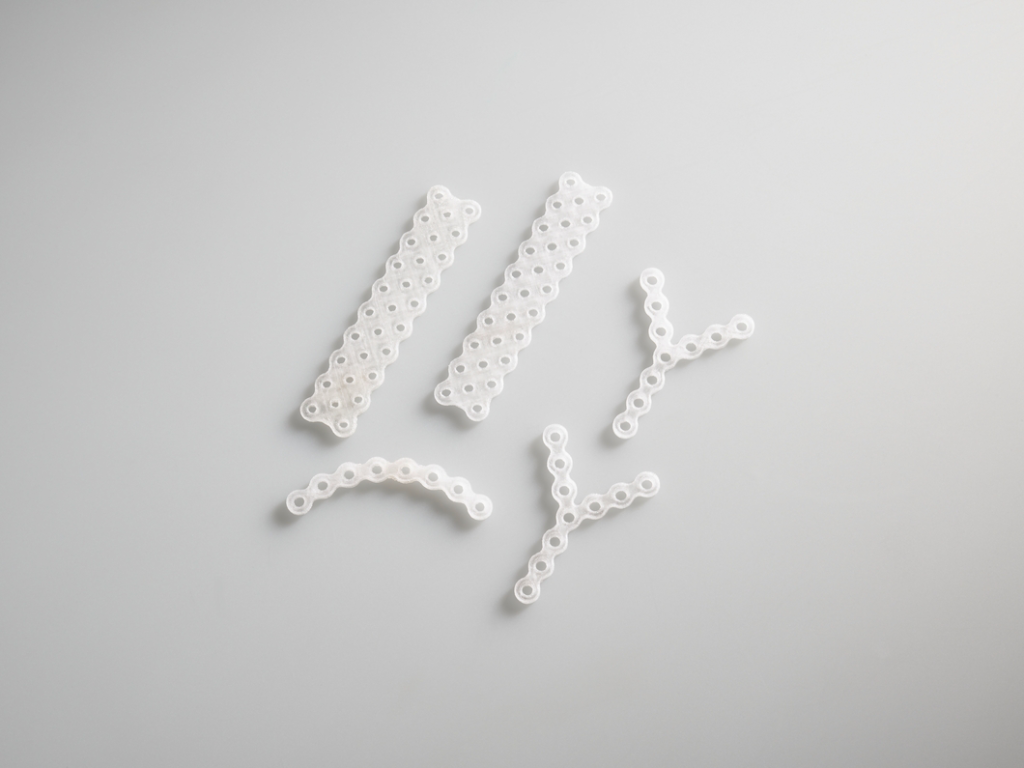
Resorbable materials such as soft breast implants and plate implants that resemble bone with a honeycomb structure are replaced with the body’s own tissue and absorbed of their own accord after a certain time.
A prime example is the processing of Resomer LR 706 (a composite made from poly L-lactide-co-D,L-lactide and ß-TCP) by the company Evonik to create implant plates intended for direct application in the body to help repair fractures. The polymer composite imitates imitates human bone and contains 30 percent ceramic additives (ß-TCP), making the resulting component more stable and adding calcium as a means of promoting bone formation. The advantage of these implants is clear: they do not need to be surgically removed when healing is complete. What’s more, permanent implants can also be made, for instance, from PCU (bionates) using the APF process. These are especially suitable for use in the spinal column.
Applications for functional components produced using high-quality additive methods are increasingly being found outside of the body too. The process is also predestined for medical devices and aids. Arburg has also introduced the processing of medically approved SEBS (Cawiton PR13576) with a hardness of 28 Shore A. The very soft material is thick and tear-resistant and can be used, for example, to produce functional respiratory masks.
Hard/soft combinations and fibre reinforcement
Equipped with three discharge units, the Freeformer 300-3X can produce complex and resilient functional components in a hard/soft combination made from qualified standard plastics and a support material using an additive method.
The Freeformer 300-4X has a fourth rotary axis and a fibre feed unit. These features now make it possible to manufacture long-fibre reinforced components.
Unique processing of medical TPE
Soft materials such as FDA-approved TPE Medalist MD 12130H (hardness 32 Shore A) can currently only be processed using the Freeformer, creating components such as sealed bellows and heart valves.
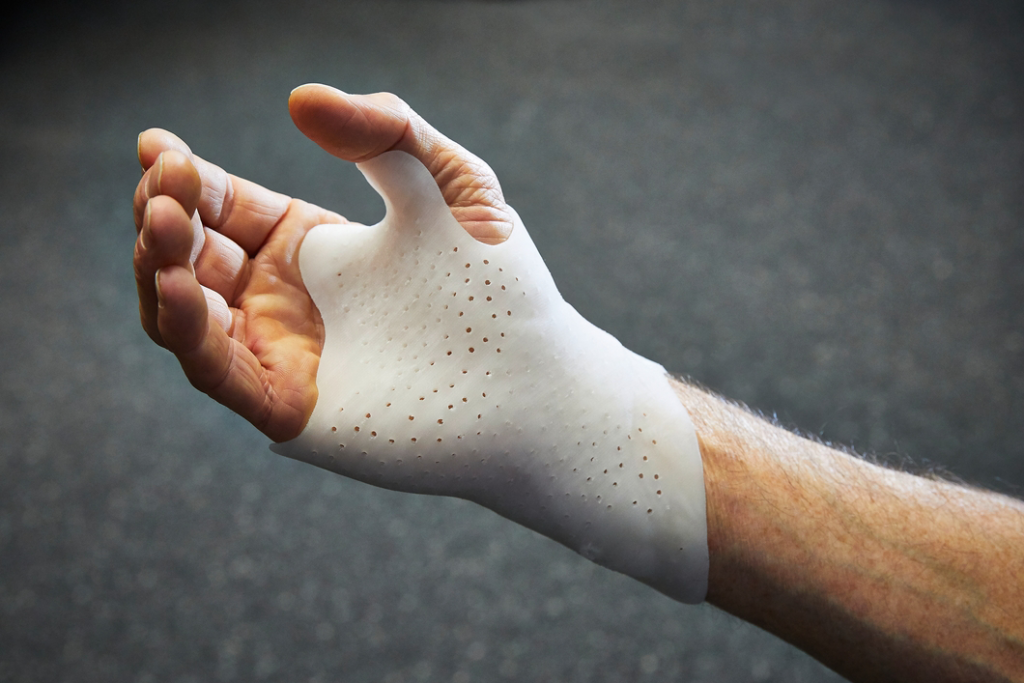
The medical material TPE Medalist MD 12130H (hardness 32 Shore A) is suitable, for example, for producing flexible, customised hand orthoses.
The APF process makes it possible to change the filling level of the component in a targeted manner while maintaining the same parameters and thereby vary the mechanical properties. In the case of TPE, for example, this results in different Shore hardnesses. Different material densities can also be realised within a component, as Arburg demonstrated by means of a test sample with honeycomb structures.
Martin Neff, head of the plastic freeforming department at Arburg, will explore other applications in the field of medical technology, including flexible and electrically conductive strain gauges, tablets with customised active ingredient quantities, and hand orthoses made from medical TPE or using fibre reinforcement in his talk at the AMS (11 February 2020, 10.35 a.m.).
Freeformer is suitable for clean room use
All Freeformers are perfectly suited to use in clean rooms. They produce very few emissions, are dust-free, and have a build chamber that is usually made from stainless steel. An optional robot interface makes it possible to automate the additive manufacturing process and integrate the Freeformer into IT-networked production lines. Process quality can be documented reliably, and components can be clearly traced as and when required. Data transfer is carried out via the OPC UA communication protocol.
Conclusion
The APF process with the Freeformer is particularly suitable for additive manufacturing in the field of medical technology. Geometric freedom, combined with material freedom will enable completely new plastic applications to be achieved, including use within the human body. The Freeformer is in great demand for the additive manufacturing of individual orthoses, implants made from biocompatible standard granulates and used as aids for surgical preparation.
Martin Neff, the Head of Plastic Freeforming at Arburg will speak at Additive Manufacturing Strategies, Boston on February 11th at 11:40.
Images
ARBURG_147538 Freeformer 300-3X.jpg
Equipped with three discharge units, the Freeformer 300-3X can produce complex and resilient functional components in a hard/soft combination made from qualified standard plastics and a support material using an additive method.
ARBURG_ 170477 Freeformer breast / 170475 bone implants.jpg
Resorbable materials such as soft breast implants and plate implants that resemble bone with a honeycomb structure are replaced with the body’s own tissue and absorbed of their own accord after a certain time.
ARBURG 170489 hand orthosis TPE.jpg
The medical material TPE Medalist MD 12130H (hardness 32 Shore A) is suitable, for example, for producing flexible, customised hand orthoses.
ARBURG_165965 Freeformer Wabenstruktur.jpg
Using the APF process, the component density can be specifically influenced. TPE Medalist MD 12130H (hardness 32 Shore A) is suitable for the production of flexible honeycomb structures.
Subscribe to Our Email Newsletter
Stay up-to-date on all the latest news from the 3D printing industry and receive information and offers from third party vendors.
Print Services
Upload your 3D Models and get them printed quickly and efficiently.
You May Also Like
Heating Up: 3D Systems’ Scott Green Discusses 3D Printing’s Potential in the Data Center Industry
The relentless rise of NVIDIA, the steadily increasing pledges of major private and public investments in national infrastructure projects around the world, and the general cultural obsession with AI have...
Formlabs Teams Up with DMG MORI in Japan
In late June, Nick Graham, Chief Revenue Officer at Formlabs, announced on LinkedIn that the company had partnered with DMG MORI, one of the world’s leading machine tool companies, to...
EOS in India: AM’s Rising Star
EOS is doubling down on India. With a growing base of aerospace startups, new government policies, and a massive engineering workforce, India is quickly becoming one of the most important...
3D Printing News Briefs, June 25, 2025: R&D Materials, 3D Printed Veneers, & More
In today’s 3D Printing News Briefs, 3DXTECH has launched a program that gives customers early access to experimental materials, and the first Lithoz CeraFab Multi 2M30 in the Czech Republic...