Many scientists have been inspired by the movements of fish, and paired the concept with 3D printing for interesting experiments. Researchers Zhiyong Tang, Xiufeng Shao, Jianze Huang, Jinyuan Yao, and Guifu Ding from Shanghai Jiao Tong University used 3D printing to create a novel micropump that’s actuated by vibrating micropaddles (MPs) to manipulate fluid. Where did they get the idea? From the natural phenomenon of fish moving forward by swinging their fins or body, of course.
The team published a paper, titled “Manipulating fluid with vibrating 3D-printed paddles for applications in micropump,” on their work, which introduces moving MPs into a 3D printed micropump in order to move fluid. The paper investigates the MP-driven pump through analysis, computations, and experiments.

Evolution of the MP-driven micropump: (a) Fish with fins; (b) Dragon boat; (c) V shape MP-driven micropump without valve.
“This paper presents a novel working mechanism of a micropump using micropaddles (MPs) to actively manipulate fluid based on 3D printing technology. The novel working principle is systematically discussed using analysis, computation and experiment methods,” the team wrote.
Micropumps have many applications, from drug delivery and biochemical sensing to environmental monitoring, molecular separation, and microelectronics cooling. There are two main kinds: a mechanical micropump has a physical actuator, while a non-mechanical one drives microfluids by transforming non-mechanical energy into kinetic movement. The team’s novel micropump is based on vibrating paddles.
“Most mechanical displacement-type micropumps greatly depend on a vibrating diaphragm actuated by piezoelectric, electrostatic, electromagnetic, or shape memory alloy to fill and pressurize the chamber periodically to manipulate microfluid,” the researchers explained. “These mechanical micropumps output microfluid only by deforming the whole chamber and fail to control fluid locally, thereby restricting precise manipulation and system integration.”

Schematics of two 3D printable prototype devices: (a) Printing anti-model by FDM; (b) Manufacturing paddle-driven pump by rolling-over process; (c) Encapsulating vibrating source with silica gel pump; (d) Optical picture of the device; (e) Integral modeling pump by Polyjet; (f) Encapsulating vibrating source; (g) Side view of the fabricated pump; (h) Optical photo of the integrated molding pump.
The researchers created a theoretical model in order to research parameters, like vibration amplitude and frequency and MP shape and size, that can drive microfluids. They used two different 3D printing techniques in order to simplify the process of fabricating the prototype pump. A Flashforge Dreamer, and a “rolling-over process,” were used to create a prototype pump’s anti-model, complete with an open chamber, while an integrated molding valveless pump with paddles and a circular inlet and outlet was 3D printed on a Stratasys J750.
“The method that combined 3D printing and rolling-over process offered convenience to observe the experiment phenomena and research the working mechanism in the following experiments. Silica gel was considered an ideal, highly tensile material to replicate 3D structures at a low cost and with suitable flexibility,” the researchers explained.
“Combining FDM printing technology and the rolling-over process, the materials that could not be directly printed could be used to form complex 3D structures or devices.”
Epoxy resin was used to affix the micromotor, which moved in a horizontal circumference, on the bottom membrane of the first pump, so that the flow rate of the pump, with eight vibrating paddles, could be directly tested. This prototype pump integrated a lab-on-a-chip (LOC) system with several functions and executed a dyeing experiment “to validate the directional driving capability intuitively,” while the second used the weighing method to test flux.
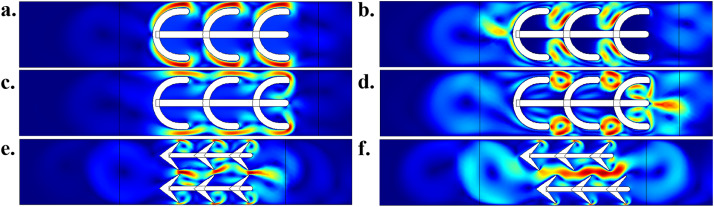
Simulation results of the flow pattern driven by U, VA and VM MPs when vibrating at 50 Hz and 100 μm: (a–d) Fluid state driven by U-shaped MPS in a period; (e) Fluid state driven by VA MPS at 0.5T; (f) Fluid state driven by VS MPS at 0.5T.
Finite element analysis (FEA) and mathematical modeling helped show the working principle, and “crucial parameters,” of the 3D printed micropumps driven by MPs, including the fact that the pumps were able to deliver fluid in a specified direction, and output different flow rates, once some of these parameters were changed. A high-speed camera was used to observe “the working process” of the micropaddles.
Most of the micromotor’s energy went towards increasing vibration amplitude, but this parameter was fairly “volatile” when the motor was installed on a different device, so the researchers decided on a standard for the paddle tip’s displacement along the channel direction as they set the amplitude. The camera was also used during an experiment that measured the paddle’s vertical displacement, which showed that “the vibration amplitude continued to increase with enhanced working voltage.”
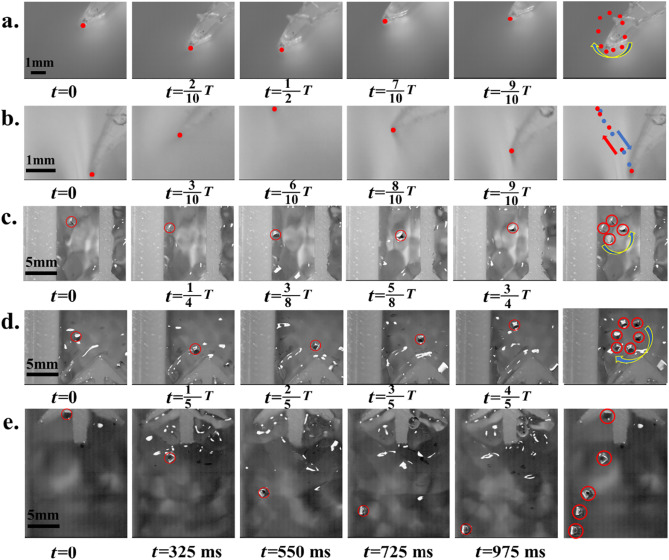
Images of the tracking path of vibrating paddles and vortexes from high speed camera: (a) Trajectory of V shape paddle in a period when vibrating at 150 Hz in air; (b) Moving trail of V shape paddle in a cycle when vibrating at 150 Hz in water; (c) Route of vortex between two paddles demonstrated by a floating Al grain; (d) Route of vortex behind paddles; (e) Moving path of working fluid in front of paddle.
“All prototype pumps maintained the same increasing trend with the driving voltage, thereby indicating improved fluid manipulation ability. Although a few abnormal points resulted from the size factor and the influence of the actual environment, most testing results showed nearly the same output capability relationship with the numerical simulation results,” the researchers stated.
They found that the micropaddle-driven pump, when vibrating at 162 Hz and powered at 9 V, was able to attain a high flow rate of 127.9 mL/min, and that the driving capability was affected by either alternating the structural distribution or optimizing the structure. These findings and more, like fluid morphology and revolving direction, “were consistent with the simulation results, thereby indicating that the simulations produced reliable results.”
“The other two demonstration experiments, namely, dyeing test and detecting acid-base reaction, proved the pump’s ability to manipulate fluid directionally and control flow order,” the researchers concluded. “Searching for a more reasonable vibration source and reducing device size are needed for further study.”
Discuss this and other 3D printing topics at 3DPrintBoard.com or share your thoughts below.
Subscribe to Our Email Newsletter
Stay up-to-date on all the latest news from the 3D printing industry and receive information and offers from third party vendors.
Print Services
Upload your 3D Models and get them printed quickly and efficiently.
You May Also Like
Heating Up: 3D Systems’ Scott Green Discusses 3D Printing’s Potential in the Data Center Industry
The relentless rise of NVIDIA, the steadily increasing pledges of major private and public investments in national infrastructure projects around the world, and the general cultural obsession with AI have...
Formlabs Teams Up with DMG MORI in Japan
In late June, Nick Graham, Chief Revenue Officer at Formlabs, announced on LinkedIn that the company had partnered with DMG MORI, one of the world’s leading machine tool companies, to...
EOS in India: AM’s Rising Star
EOS is doubling down on India. With a growing base of aerospace startups, new government policies, and a massive engineering workforce, India is quickly becoming one of the most important...
3D Printing News Briefs, June 25, 2025: R&D Materials, 3D Printed Veneers, & More
In today’s 3D Printing News Briefs, 3DXTECH has launched a program that gives customers early access to experimental materials, and the first Lithoz CeraFab Multi 2M30 in the Czech Republic...