Researchers from King Mongkut’s University of Technology Thonburi in Bangkok, Thailand continue to study the science of materials in 3D printing—a topic that has continued to expand throughout recent years especially as the technology has infiltrated the mainstream and been widely embraced not only just in labs but also a wide range of industries, educational systems, and both offices and homes too on the individual level. Their current research is outlined in the recently published ‘Comparison of Filler Types in Polyactic Acid Composites for 3D Printing Applications.’
Through customization of materials, users today can look forward to greater freedom to innovate in their own work, whether designing prototypes, parts, medical devices, DIY projects in the home, and more. PLA is widely used (along with other standards like ABS) due to its accessibility, affordability, and biodegradable nature as a plant-based material. In this study, the researchers examined a variety of fillers suitable for PLA, assessing which additives would be best for preventing brittleness in parts.
Filler types evaluated in this study included:
- Wood flour (WF)
- Talc (TC)
- Calcium carbonate (CaCO3)
- Microballoon (MB)
- Silicon dioxide (SiO2)
Samples were designed in SolidWorks 2014, and then files were imported into Cura 2.6.2. The researchers used FDM 3D printing to manufacture objects for tensile testing.
Dumb-bell shaped samples were tested for Young’s modulus, tensile strength, and elongation at break.
“It was found that the 3D printed parts were completely fabricated and stable in shape during fabrication,” stated the authors in their research paper. “The 3D printed composites were a difference in color and texture which were dependent on the color and physical of fillers. The PLA/TC, PLA/CaCO3, PLA/MB and PLA/SiO2 composites were a whitish, and smooth surface while the PLA/WF composites were brown and rougher surface.”

The 3D printed parts of PLA composites:(a) neat PLA,(b) PLA/WF, (c) PLA/TC, (d) PLA/CaCO3, (e) PLA/MB, and (f) PLA/SiO2
Through adding TC and MB, the researchers were able to decrease brittleness. With the PLA/TC composites, greater elongation and flexural strength were displayed in contrast to neat PLA and other composites.
“The 3D printed PLA/TC composites had greater elongation and flexural strength compared to neat PLA and PLA composites because of the plated of talc that would be terminated the cracks and then it supported the further force. The PLA filled with glass microballoons gave the best impact strength, the reasons being associated with the highest melt flow rate that led to a great fusion and bonding between layers. Moreover, the TC-filled and MBfilled PLA composites were stable in shape during fabrication that was satisfied both in the manufacturing and the tough properties,” concluded the researchers.
“For the thermal properties, the PLA slightly deteriorated Vicat softening point when adding the fillers, except for PLA/MB. Next, we focused on the investigate the properties of PLA filled with glass microballoons for 3D printing application in the tooling holder for CNC machine. Next, we focused on investigating the friction and wear properties of 3D printed parts of PLA filled with glass microballoons for making the tool holder in the milling CNC machine.”
If you are a 3D printing user today you have access to an overwhelming number of different types of software, hardware, and materials. Composites are being studied widely, from silver-nanowire photopolymers to PLA antioxidants, to wood composites, and more.
What do you think of this news? Let us know your thoughts; join the discussion of this and other 3D printing topics at 3DPrintBoard.com.
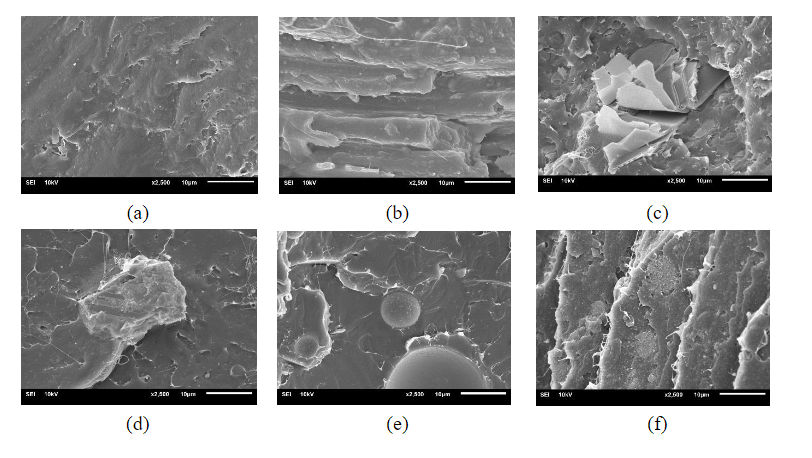
SEM Micrographs of the Fractured Surface of Filament Composites: (a) neat PLA,(b) PLA/WF, (c) PLA/TC, (d) PLA/CaCO3, (e) PLA/MB, and (f) PLA/SiO2
Subscribe to Our Email Newsletter
Stay up-to-date on all the latest news from the 3D printing industry and receive information and offers from third party vendors.
Print Services
Upload your 3D Models and get them printed quickly and efficiently.
You May Also Like
The Dental Additive Manufacturing Market Could Nearly Double by 2033, According to AM Research
According to an AM Research report from 2024, the medical device industry, specifically in dentistry, prosthetics, and audiology, is expected to see significant growth as these segments continue to benefit from...
Heating Up: 3D Systems’ Scott Green Discusses 3D Printing’s Potential in the Data Center Industry
The relentless rise of NVIDIA, the steadily increasing pledges of major private and public investments in national infrastructure projects around the world, and the general cultural obsession with AI have...
AM Research Webinar Explores Continuum’s Sustainable Metal Additive Manufacturing Powders
Metal additive manufacturing (AM) powder supplier Continuum Powders is working to develop solutions that empower industries to reduce waste and optimize their resources. An independent life cycle assessment (LCA) of...
3D Printed Footwear Startup Koobz Lands $7.2M in Seed Round
California-based Koobz is focused on reshoring the U.S. footwear supply chain with advanced manufacturing processes, including 3D printing. The startup just announced that it has added $6 million to its...