In the recently published ‘Fracture Behavior of Bio-Inspired Functionally Graded Soft-Hard Composites Made by Multi-Material 3D Printing: The Case of Colinear Cracks,’ researchers from Delft University of Technology (TU Delft) further explore the impacts of functional gradients in materials related to numerous technical applications, like aerospace or medicine.
In this study, the research team focuses on testing both stepwise and continuous gradients, pointing out that FGMs serve as ‘multi-phase’ composites which are supposed to fulfill mechanical, thermal, electrical requirements, and more. While FGMS can be applied to multiple disciplines, they are also used in the following:
- Thermal barrier coatings
- Piezoelectric devices
- Thermoelectric devices
- Non-uniform pressurized cylinders
- Dental implants
- Biocompatible graded hydrogels
- Soft robotics
- Tissue engineering scaffolds
FGMs are also seen in nature in hard tissue like bone and teeth and are used to advantage in modern applications as hard-soft interfaces can be eliminated—helping to avoid cracks, delamination, and harm to structural integrity.
“The concept of functional gradients is, therefore, one of the design motifs that has its roots in nature and can be implemented in the design of advanced functional materials with properties not achievable using homogenous materials,” stated the researchers.
FGMs also allow for better performance overall, the ability to customize materials for necessary applications, and promote greater longevity in products. As additive manufacturing continues to progress, there is much greater potential for creating FGMs that are both complex, as well as ‘precisely controlled.’
“During the last few years, advanced multi-material additive manufacturing techniques that allow for controlling the deposited material at the voxel level (i.e., length scales in the range of a few tens of micrometers) have been emerging through material jetting processes,” explain the researchers. “Using these emergent techniques, one can precisely control the spatial distribution of mechanical properties in three dimensions at very small scales.”
While it is known that FGMs cause the potential for stress, cracking, and more, the research team explains that it is important to understand FGM fracture behavior in 3D. They created fracture mechanics models to determine fracture modes and crack orientations, emphasizing the hard to soft stage. Ten samples were 3D printed for tensile testing, and divided into the following groups:
- Abrupt hard–soft connections without a gradient
- Three variations of stepwise graded structures (5-steps, 10-steps, 15-steps)
- Continuously graded structures with two different gradient functions, namely sigmoid and linear functions

A schematic view of a single-edge notched tensile specimen with an initial crack colinear with the gradient direction (a) for non-graded (b) and graded (c,d) specimens. The transition zone between hard and soft phases had two gradient functions, namely, (i) step-wise (5 steps, 10 steps, and 15 steps) and (ii) continuous (sigmoid and linear). A schematic drawing showing the different gradient functions is presented in Figure S1 of the supplementary document. The size of the transition length between the hard and soft phases was also varied. Three levels were considered for the transition lengths, namely 5%, 25%, and 50% of the width (W) of the specimen. The design matrix is presented in (e). The white and black pixels respectively represent the hard and soft phases. The geometrical parameters were L=75 mm, W=75 mm, L0=100 mm, and a0=15 mm
Specimens were created using an Objet350 Connex3TM 3D printer, with VeroMagentaTM for hardness, and Agilus30TM Black for the soft phase.
Stress-strain was the same for all samples, with curves comprised of force being linearly increased during stretching, and then an abrupt decrease in force upon brittle fracture. During the second phase, force was sustained until the end, resulting in breakage at that point.
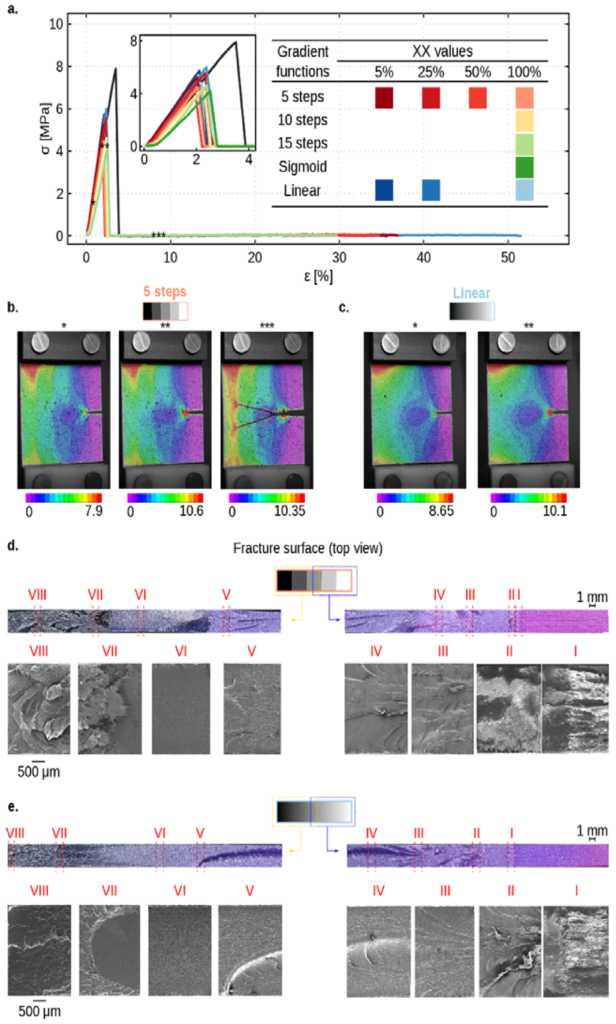
(a) Typical stress–strain curves of specimens with graded or non-graded interfaces. The inset shows a magnified view of the stress–strain curves until 4% strain. Full-field strain measurement using digital image correlation (DIC) of specimens with five steps (b) and linear (c) transition functions. DIC images show von Mises strain before maximum load (*), at the maximum load (**), and after maximum load (***). Digital microscopy images (200× magnifications) and the corresponding scanning electron microscopy (SEM) (35,000× magnifications) analyses of the fracture surface of the specimens with five steps and linear transition function are presented in sub-figures (d) and (e), respectively. The SEM images show the zoomed-in images of eight regions of structures. The scale bars for the digital microscopy images are on top of the corresponding images and underneath the SEM images. The hard phase is in white pixels, while the soft phase is in black. The size of the transition length was 100%W for the specimens in subfigures (b–e).
“We found that, unlike fracture in other directions, the fracture properties (e.g., fracture strain) that are measured for the cracks that are colinear to the gradient direction appear to improve when the material gradient is non-continuous,” concluded the researchers. “FGMs with a continuous gradient, on the other hand, showed slightly higher stiffness and fracture energies.
“This suggests that the type of gradient function (i.e., continuous or non-continuous) may affect the fracture behavior of FGMs differently, depending on the orientation of the crack with respect to the gradient direction. More importantly, in addition to the type of gradient functions, the length of the transition zone between the hard and soft phases is the most critical parameter influencing the fracture resistance of FGMs to crack growth that needs to be included in the design of these advanced materials.”
As users use 3D printing increasingly more to create functional parts over prototypes, researchers and manufacturers delve further into strength testing of materials, whether testing with carbon, seeking rigidity without breakage, innovating with shape memory, and more.
What do you think of this news? Let us know your thoughts! Join the discussion of this and other 3D printing topics at 3DPrintBoard.com.
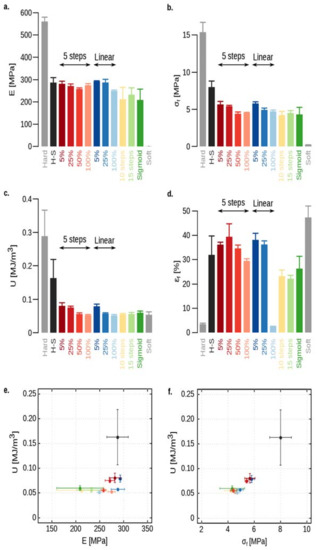
Bar-plots for the comparison of the mechanical properties of the specimens in ten groups, which include elastic stiffness (a), fracture stress (b), fracture energy (c), and final strain (d). The statistical parameters of the calculated fracture properties are summarized in Table S2 of the supplementary document. An ANOVA analysis and a post-hoc Tukey honestly significant difference (HSD) test were used to determine whether there was a significant difference between different groups. The comparison tables are presented in Tables S3–S6 of the supplementary document. The Ashby plots compare the fracture energy with elastic stiffness (e) and fracture stress (f). The plots show the mean and standard deviations for each data point. The fracture properties of the monolithic hard and soft specimens are adopted from [30].
Subscribe to Our Email Newsletter
Stay up-to-date on all the latest news from the 3D printing industry and receive information and offers from third party vendors.
Print Services
Upload your 3D Models and get them printed quickly and efficiently.
You May Also Like
3D Printing News Briefs, July 2, 2025: Copper Alloys, Defense Manufacturing, & More
We’re starting off with metals in today’s 3D Printing News Briefs, as Farsoon has unveiled a large-scale AM solution for copper alloys, and Meltio used its wire-laser metal solution to...
3DPOD 260: John Hart on VulcanForms, MIT, Desktop Metal and More
John Hart is a Professor at MIT; he´s also the director of the Laboratory for Manufacturing and Productivity as well as the director of the Center for Advanced Production Technologies....
3D Printing News Briefs, June 28, 2025: Defense Accelerator, Surgical Models, & More
In this weekend’s 3D Printing News Briefs, 3YOURMIND was selected to join an EU Defense Accelerator, and PTC has announced model-based definition (MBD) capabilities within Onshape. Finally, a study out...
EOS in India: AM’s Rising Star
EOS is doubling down on India. With a growing base of aerospace startups, new government policies, and a massive engineering workforce, India is quickly becoming one of the most important...