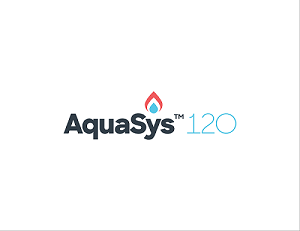
A new material has been developed that is ideal for use as a general-purpose water-soluble support for additive manufacturing (3D printing). Its thermal stability and robust adhesion characteristics make it an ideal support system for a wide array of build materials.
Most manufacturers understand how 3D printing enables them to produce stronger, lighter parts and systems. Although many different materials can be used to create 3D-printed models, thermoplastics like acrylonitrile butadiene styrene (ABS), polylactic acid (PLA) and polycarbonate (PC) are the most commonly used.
Complex thermoplastic parts and structures have bridges or overhangs that require support during printing. Since these support structures are not part of the model, they need to be removed after printing. This post-processing step is important, because it affects the printed part’s final surface finish, strength and color. However, it can be tedious, require the use of harmful chemicals, damage the model’s surface and reduce productivity. That’s why it’s critical to select the right material for 3D printing support structures.
BREAKAWAY VS. SOLUBLE SUPPORT STRUCTURES
Two basic categories of materials are available for support structures: breakaway and soluble. Breakaway support structures are often constructed from a material that is similar to the printed object. After printing, the support is removed by trimming, mechanical breakage, or abrasion.
All of these steps add work, and therefore time and cost, to each piece. In addition, removing the 3D printing support structures can leave blemishes on the model surface or break off part of the model along with the structure. Also, removing breakaway supports is generally more difficult when working with high-temperature materials.
Alternatively, soluble support materials can be removed by placing them in water or a solvent after printing. Using solvents is undesirable because they are generally volatile organic compounds that are unfriendly to printers and the environment. But water-soluble support materials can also be tricky to work with. For example, polyvinyl alcohol (PVA) absorbs water vapor from the air, doesn’t stick very well to print surfaces, and is temperature sensitive, which can cause jams. Also, water-soluble support materials have been exceptionally challenging to develop.
DEVELOPMENT CHALLENGES OF SOLUBLE SUPPORTS
Developing water-soluble supports is challenging for many reasons. First, there are a limited number of commercially available resins that are truly water-soluble. Many water-soluble polymers are very brittle, which prevents their conversion to filament. In addition, plasticizing using traditional additives often inhibits thermal stability and adhesion, which severely limits their use in 3D printing.
The first generation of soluble supports had a variety of issues. Some used harmful chemicals or highly acidic or highly basic solutions. Although some of these are still widely used, resin technology has advanced, and there are now a plethora of soluble support materials on the commercial market including:
• Highly proprietary resins (Stratasys SR30, SR35, SR100, etc.)
• Resins based on commonly available PVA or polyvinylpyrrolidone (PVP)
• Cellulosics like hydropropyl methylcellulose (HPMC)
• Exotic polybutenediol vinyl alcohol (BVOH)
Yet none of these products is ideal for filament because they are not thermally stable. Now there is a better material option.
WATER-SOLUBLE RESINS THAT ARE TOUGH ENOUGH FOR FILAMENT
Infinite Material Solutions recently developed a composite material that is both water-soluble and thermally stable. This “outside the box” resin is formulated from a naturally occurring carbohydrate blended with a polymer that is flexible, tough and water-soluble. The new material (branded AquaSys™ 120) is unique because it is tough enough to be used as support filament.
This formulation is surprising because many pure carbohydrates and water-soluble polymers are far too brittle to form a usable filament. Over the years, formulators have made many attempts to plasticize water-soluble resins so they could be converted to filament. However, adding plasticizers often dramatically reduces the thermal stability of the base resin. Also, plasticizers can inhibit the adhesion between materials, severely limiting their use for 3D printing. AquaSys 120 uses a highly complex process to produce 1.75 mm and 2.85 mm diameter filament that can be used successfully for a variety of 3D printing platforms and materials.
MATERIAL BENEFITS AND COMPATIBILITY
The individual components of this new material are widely used in industry for a variety of applications ranging from packaging and drug delivery to cosmetics and personal care products. The material is hydrophilic, biocompatible, biodegradable, nontoxic, and noncarcinogenic, based on information available for all the individual components.
This new filament material can be used for the most common 3D printing technologies including fused filament fabrication and direct material extrusion. It is also compatible with a broad range of materials including polypropylene and hydrophilic and hydrophobic polymers. It shows excellent thermal stability and other advantages over traditional PVA that make it a more versatile, robust, and environmentally friendly material for support filaments.
These advantages include:
• Dissolves in water much faster than pure PVA
• Can be printed with a wider range of materials
• Has enhanced adhesion properties
• Is more quickly biodegraded than PVA
THERMAL STABILITY AT MUCH HIGHER TEMPERATURES
A leading brand of PVA filament prints at 215-225 ºC and a maximum build plate temperature of 60 ºC. Alternatively, AquaSys 120 filament prints at 240-245 ºC and a maximum build plate temperature of 130 ºC.
ADHESION CHARACTERISTICS
Being able to build materials that can adhere to soluble supports, or vice versa, is of critical importance to achieving a successful 3D print. Poor adhesion between adjacent layers of support and build materials causes sloughing off and print failures.
The new material was engineered with enhanced adhesion properties to address this problem. It is compatible with a wide range of both hydrophobic and hydrophilic materials used in filament-driven 3D printing platforms and continues to be used with new build materials.
To date it, AquaSys 120 has been successfully printed with polyamides (nylon), co-polyester (CPE), acrylonitrile butadiene styrene (ABS), thermoplastic polyurethane (TPU), polycarbonate (PC), and polyolefins like polypropylene (PP). This offers a significant advantage over traditional PVA filament, which has limited adhesion to CPE, ABS, TPU, PC, and PP.
DISSOLUTION
In head-to-head dissolution trials of identically printed parts, the new filament material dissolved twice as fast as a leading brand of PVA at room temperature (22 ºC) and over six times faster at elevated temperatures (80 ºC). Figure 1 shows its dissolution kinetics versus PVA. Unlike PVA, which can form gels prior to dissolution and especially at elevated temperatures, the new material dissolves cleanly with no gelation at temperatures >35 ºC.
DISPOSAL AND BIODEGRADABILITY
The new composite material is based on a naturally occurring carbohydrate that is very rapidly mineralized in the environment. Mineralization of this carbohydrate component can take several hours or days. The remaining components of the material biodegrade more slowly, but like PVA, they are considered to be ultimately biodegradable based on respirometric mineralization tests using acclimated sludge from wastewater treatment facilities.
A new water-soluble support material is now available that solves a number of challenging issues in additive manufacturing. This carbohydrate composite capitalizes on the unusual thermal stability and outstanding water solubility of a naturally occurring saccharide blended with a flexible and tough water-soluble polymer. This unique material provides advanced adhesion to a wide variety of build materials, a broad processing window and improved aqueous dissolution performance without the use of solvents or harsh chemicals.
By: Nathan W. Ockwig, Gavriel DePrenger-Gottfried, Brandon Cernohous, Philip J. Brunner, Jeffrey J. Cernohous
Subscribe to Our Email Newsletter
Stay up-to-date on all the latest news from the 3D printing industry and receive information and offers from third party vendors.
Print Services
Upload your 3D Models and get them printed quickly and efficiently.
You May Also Like
Heating Up: 3D Systems’ Scott Green Discusses 3D Printing’s Potential in the Data Center Industry
The relentless rise of NVIDIA, the steadily increasing pledges of major private and public investments in national infrastructure projects around the world, and the general cultural obsession with AI have...
Formlabs Teams Up with DMG MORI in Japan
In late June, Nick Graham, Chief Revenue Officer at Formlabs, announced on LinkedIn that the company had partnered with DMG MORI, one of the world’s leading machine tool companies, to...
EOS in India: AM’s Rising Star
EOS is doubling down on India. With a growing base of aerospace startups, new government policies, and a massive engineering workforce, India is quickly becoming one of the most important...
3D Printing News Briefs, June 25, 2025: R&D Materials, 3D Printed Veneers, & More
In today’s 3D Printing News Briefs, 3DXTECH has launched a program that gives customers early access to experimental materials, and the first Lithoz CeraFab Multi 2M30 in the Czech Republic...