According to the Centers for Disease Control and Prevention (CDC), malaria is a mosquito-born disease caused by a parasite. While roughly less than 2,000 cases are diagnosed annually in the US, it’s a terrible disease in areas like sub-Saharan Africa. Globally, according to the World Health Organization (WHO), there are over 217 million malaria cases and 435,000 deaths. Malaria eradication programs usually focus on eliminating the small puddles of water that the mosquitoes use to breed, or by using an insecticide to kill larvae or mosquitoes. An issue with the latter approach is that in some cases mosquito populations may become resistant to certain pesticides.
One of the standard methods used to assess resistance in adult mosquito populations is the WHO insecticide susceptibility test (bioassay). Researchers Sean Tomlinson, Henrietta C. Yates, Ambrose Oruni, Harun Njoroge, , , and
“The WHO bioassay kit consists of several acrylic pieces that are assembled into a unit. Parts of the kit commonly break, reducing the capacity of insectaries to carry out resistance profiling. Since there is at present only a single supplier for the test kits, replacement parts can be hard to procure in a timely fashion. Here, we present 3D printable versions for all pieces of the WHO bioassay kit,” the team wrote.
“Using widely available polylactic acid (PLA) filament as a printing material, we were able to design and print functional replacements for each piece of the WHO bioassay kit. We note no significant difference in mortality results obtained from PLA printed tubes and WHO acrylic tubes. Additionally, we observed no degradation of PLA in response to prolonged exposure times of commonly used cleaning solutions.”
The WHO bioassay test consists of mosquitoes held in one of two tubes – one tube is lined with untreated paper, while the other is lined with insecticide-impregnated paper. The tubes are capped with a screen mesh, and the mosquitoes are held inside for an hour. The mortality percentage of the bugs in the insecticide tube, 24 hours post-exposure, is used to measure insecticide susceptibility.
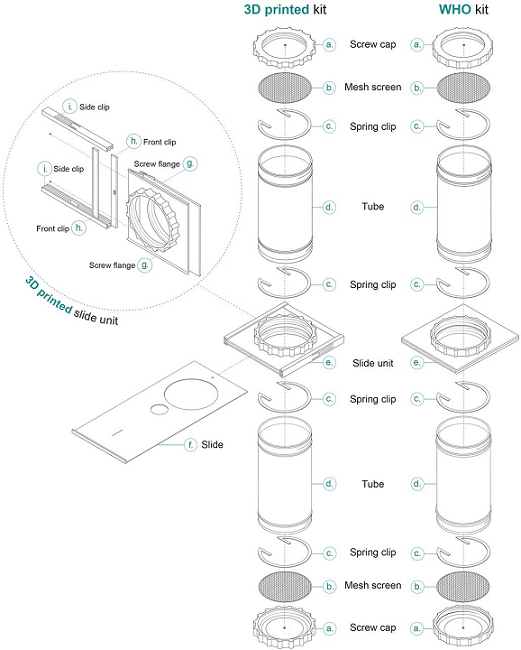
Figure 1. WHO bioassay kit and equivalent 3D printed parts. Cutaway shows the assembly of the 3D printed version of the slide unit. For illustration purposes, the WHO bioassay slide has been omitted but is visually identical to f.
One kit, pictured above, contains two tubes, two mesh screens, two screw caps, four spring clips, one slide unit, and one slide. Some of these components can become damaged, lost, or worn over time, which can cause “a reduced capacity of insectaries to conduct bioassays,” and due to high costs and long shipping times, replacing these parts is not always easy or economically feasible.
“Our designs can be used to produce replacement parts for the WHO bioassay kit in any facility with a 3D printer, which are becoming increasingly widespread,” the team wrote.
“Here, we present 3D printable replacement parts for the WHO bioassay kit which print without the need for tools or glue; and which interface with existing WHO bioassay parts.”
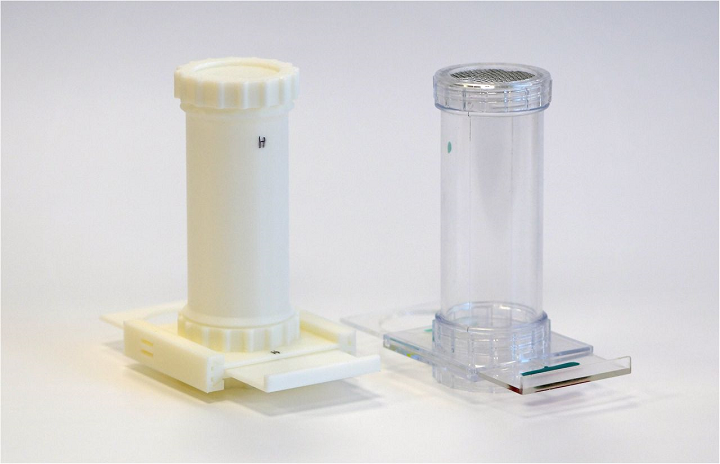
Figure 2. Photo of WHO bioassay component and corresponding 3D printed version. E and H are used to denote the exposure and holding sides, respectively, whereas on the WHO kit a red and green dot is used.
The team created the 3D model files for the components using SketchUp and OpenSCAD, though some parts couldn’t be directly replicated; the existing design was slightly modified for these so that they could be successfully 3D printed. The files were sliced with Ultimaker’s Cura 3.3.1, and the parts were 3D printed, out of white 1.75 mm PLA, on an Original Prusa i3 MK3 and MK3S. The CAD and STL files are available on Github.
The outer geometry of the tube rims was changed from squared to triangular in order to save on plastic usage and reduce print time. The slide unit features an internal section where the gate slides, and the team had to adapt it to become 3D printable. Two halves were created, and they found a way to bond them together.
“We designed a sliding clip method of joining two screw flanges of the slide unit. Two halves of the slide unit are printed with the addition of arrow-like notches on each side; these interface with a sliding lock clip that mechanically locks the two halves together and creates a gap for the gate to slide through,” the researchers explained.
The slide unit was also redesigned to fix the friction nodules, which means that there is some assembly required now; however, this can be done without tools. The team also added a 3 mm border to the CAD version of the mesh screen to make them stronger for handling purposes.

Figure 3. Bioassay results comparing mortality between the WHO bioassay kit and 3D printed kit for Mbita, Kilifi and their combined results. A t-test was used to compare means for each test.
The team used a standard 4% WHO diagnostic dose of DDT insecticide to perform susceptibility tests on two Kenyan laboratory strains of Mbita and Kilifi female mosquitoes; the insect colonies are maintained by the Kenya Medical Research Institute and the Liverpool School of Tropical Medicine. After the 24-hour holding period, they recorded percentage mortality, and found “no significant difference” between the WHO bioassay kits and the 3D printed ones.
They also exposed some of the parts, like mesh screens and screw caps, to four different sucrose solutions often used during the actual bioassay protocol, in order to observe if the PLA degraded.
“After exposure to 10% sucrose, 70% ethanol, 3% Rely+On Virkon (Lanxess) and 5% Decon 90 (Decon Laboratories Ltd.), we observed no signs of degradation of the PLA strength, tensibility, surface colour or size,” they wrote.
The researchers believe that the best use case for their 3D printed parts is as a replacement library for missing or damaged parts of the original WHO bioassay kit. These replacement components join other 3D printing uses, such as membrane feeder aids, blood filters, and diagnostic tools, in helping to learn about, diagnose, fight, and prevent malaria.
Discuss this and other 3D printing topics at 3DPrintBoard.com or share your thoughts below.
Subscribe to Our Email Newsletter
Stay up-to-date on all the latest news from the 3D printing industry and receive information and offers from third party vendors.
Print Services
Upload your 3D Models and get them printed quickly and efficiently.
You May Also Like
Havaianas Collaborates with Zellerfeld to Launch 3D Printed Flip-Flops
The shoe of the summer is undoubtedly the flip-flop. Easy on, easy off, your feet won’t get sweaty because there’s not much material, and they’re available in a veritable rainbow...
UCLA Researchers Develop 3D Printed Pen that May Help Detect Parkinson’s Disease
Diagnosing Parkinson’s disease is difficult. Often, early symptoms of the progressive neurological condition may be overlooked, or mistaken for signs of aging. Early diagnosis can help save lives and improve...
Printing Money Episode 30: Q1 2025 Public 3D Printing Earnings Review with Troy Jensen, Cantor Fitzgerald
Printing Money is back with Episode 30, and it’s that quarterly time, so we are happy and thankful to welcome back Troy Jensen (Managing Director, Cantor Fitzgerald) to review the...
Heating Up: 3D Systems’ Scott Green Discusses 3D Printing’s Potential in the Data Center Industry
The relentless rise of NVIDIA, the steadily increasing pledges of major private and public investments in national infrastructure projects around the world, and the general cultural obsession with AI have...