In the recently published ‘Additive Manufacturing of Information Carriers Based on Shape Memory Polyester Urethane’ Dilip Chalissery, Thorsten Pretsch, Sarah Staub, and Heiko Andrä explored more in the 4D printing realm.
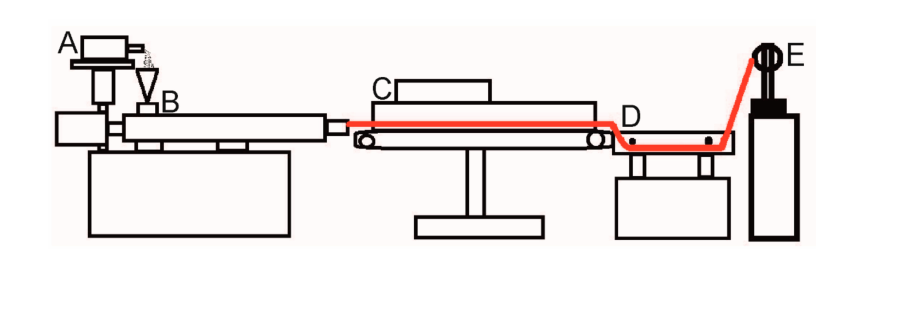
Technical drawing of an extrusion line as used for the production of PEU filaments: Material feeding system (A), twin screw extruder (B), conveyor belt (C), water bath (D), and filament winding machine (E). The extrudate is drawn in red.
Shape memory polymers are becoming more and more useful today as they can respond to their environment, whether in terms of temperature or moisture and can be 3D printed in complex geometries. For this research, thermoresponsive polyurethane-based SMPs are printed using FDM (also called FFF) 3D printing, which has been relatively rare in research so far. The team created two sample designs for their study: one in the form of a QR code reading Fraunhofer IAP, and the other a cylindrical granulate grain.
An Ultimaker 3 was used for fabrication, with samples heated to 100 ◦C and then cooled to −100 ◦C, with the process repeated twice. The QR code was represented in three different types:
- Type 1 – The substrate was printed with non-dyed PEU using a 400 µm nozzle and a target layer thickness of 180 µm.
- Type 2 – the substrate was printed with non-dyed PEU using a 400 µm nozzle. Again, a target layer thickness of 180 µm was selected for the substrate, but the elevation was built with red PEU employing a 400 µm nozzle.
- Type 3 – the substrate was also printed with non-dyed PEU using a 400 µm nozzle, but this time a reduced target layer thickness of 15 µm was selected.
“For all experiments, heating and cooling rates of 3 ◦C·min−1 were selected and the holding time at the highest and lowest temperature was set to 10 min. The storage modulus (E´), loss factor (tan δ) and the glass transition temperature (Tg) were determined for the second heating. The phase transition behavior of the PEU was also studied by differential scanning calorimetry (DSC) using a Q100 DSC from TA Instruments (New Castle, DE, USA),” explained the authors.
The researchers offered a comprehensive study, examining the following:
- Thermal properties
- Print quality
- Programming and characterization of SMPs
While some inaccuracies were found in the 3D prints, the QR codes were functional and as they triggered the shape memory, it deformed correctly, along with providing machine readability as required. The authors stated that shape memory properties were so good, they went on to wonder if they could endure even stronger deformations—with the sample proving so in a stable manner.
The QR codes were significantly light in weight, and they found a good balance in build rate and print resolution with FFF 3D printing, thus making it a ‘promising technology’ for fabrication of SMPs in innovative new shapes.
“The main advantages of the new manufacturing process for QR code carriers are that polymer extrusion can be easily controlled, a significantly lower amount of base material is needed, facilitating the fabrication of very thin layers with a thickness below 10 µm, and the use of solvents can be avoided,” concluded the researchers.
“All these aspects emphasize that the novel production process for QR code carriers is not only attractive for research purposes, but also from an economic point of view, not least because the material could be qualified for processing with a commercially available 3D printer. Therefore, FFF could turn out as an enabling technology to realize applications for SMPs in fields like counterfeit-proof marking of goods at risk of plagiarism and supervision of cold chains.”

Type 2 QR code carrier: Permanent shape after 3D printing (a), the temporary shape as obtained after programming (Fmax = 25 N) (b), and the recovered shape after heating to 60 ◦C (c). To visualize shape recoverability, the image of the permanent shape was converted to black-and-white and superimposed with a transparency of 60% on the image of the recovered shape (d). The result of a mathematical calculation comparing the permanent shape with the recovered shape: congruent areas (green color) and incongruent areas (red color) (e).
Shape memory polymers have been used today for making soft actuators, 4D structures from silicone materials, metamaterials, and more. What do you think of this news? Let us know your thoughts! Join the discussion of this and other 3D printing topics at 3DPrintBoard.com.

Type 2 QR code carrier as investigated by light and confocal microscopy including an evaluation of print quality: Top view and inset exhibiting a randomly selected cuboid (a), surface topography of the cuboid and its surrounding (b), superposition with a virtual QR code having a transparency of 60% (c), result of a mathematic calculation to determine the congruence of the virtual QR code with the physical print object: consistent print areas (green color) and irregularly filled areas (red color) (d), side view of a cut through the cuboid and the substrate (e), and the evolution of layer thickness Z with regard to the cuboid and its surrounding (f).
Subscribe to Our Email Newsletter
Stay up-to-date on all the latest news from the 3D printing industry and receive information and offers from third party vendors.
Print Services
Upload your 3D Models and get them printed quickly and efficiently.
You May Also Like
Reinventing Reindustrialization: Why NAVWAR Project Manager Spencer Koroly Invented a Made-in-America 3D Printer
It has become virtually impossible to regularly follow additive manufacturing (AM) industry news and not stumble across the term “defense industrial base” (DIB), a concept encompassing all the many diverse...
Inside The Barnes Global Advisors’ Vision for a Stronger AM Ecosystem
As additive manufacturing (AM) continues to revolutionize the industrial landscape, Pittsburgh-based consultancy The Barnes Global Advisors (TBGA) is helping shape what that future looks like. As the largest independent AM...
Ruggedized: How USMC Innovation Officer Matt Pine Navigates 3D Printing in the Military
Disclaimer: Matt Pine’s views are not the views of the Department of Defense nor the U.S. Marine Corps Throughout this decade thus far, the military’s adoption of additive manufacturing (AM)...
U.S. Congress Calls Out 3D Printing in Proposal for Commercial Reserve Manufacturing Network
Last week, the U.S. House of Representatives’ Appropriations Committee moved the FY 2026 defense bill forward to the House floor. Included in the legislation is a $131 million proposal for...