RepRap Ltd. user and hero of the open-source 3D printing movement Adrian Bowyer endeavors to use an electric current to create a 3D printed liquid plastic monomer that will polymerize in just a single scan—and in just a few seconds. If feasible this may be a much faster path to 3D printing objects.
By combining three different innovative techniques Adrian thinks that he may be able to come up with a new innovative 3D printing method. The reverse-CT scan 3D printing technique from University of California (UC), Berkeley and Lawrence Livermore employs a printer projecting scans onto rotating photosensitive resin. The device, aptly named after the Star Trek Replicator, works through computed axial lithography (CAL).
“Basically, you’ve got an off-the-shelf video projector, which I literally brought in from home, and then you plug it into a laptop and use it to project a series of computed images, while a motor turns a cylinder that has a 3D-printing resin in it,” explained Hayden Taylor, assistant professor of mechanical engineering at the UC Berkeley, and senior author of a recently published paper on the technology.
“Obviously there are a lot of subtleties to it — how you formulate the resin, and, above all, how you compute the images that are going to be projected, but the barrier to creating a very simple version of this tool is not that high.”
The open-source electric 3D scanning technique for 3D reconstruction from Spectra offering a seamless technology for medical imaging via electrical conductivity, permittivity, and ‘impedance of a part of the body’ from electrode measurements—transferred via small AC currents.
“This impedance information is then used to create an image reconstruction using techniques like a CATSCAN. By running multiple frequencies through the body cross-section of interest, you can obtain further information on dielectric spectrums of individual materials located between the electrodes,” states the Spectra team. “This multi-dimensional data is perfect for machine learning to delve into and make EIT and even more powerful tool for transforming human health!”

A preliminary scan of lung cross-section by the Spectra system [thanks to the Spectra Crowdfunder page].
Last, Bowyer uses Electropolymerisation as a coating procedure and one that is conducive for small areas, applying an electrochemical coating.
“The polymerization solution contains the monomer, solvent, and the supporting electrolyte. This method can be further divided into potentiodynamic, galvanostatic, and potentiostatic electropolymerization,” state the researchers studying the process in their recent paper.
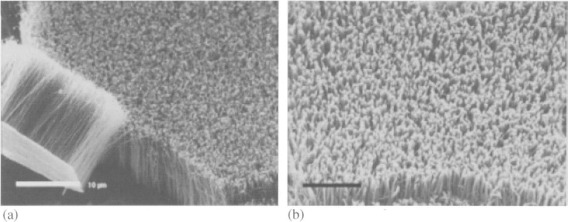
Nanowires made on a surface by electropolymerisation; scale bar is 10 μm [thanks to the Science Direct article on electropolymerisation].
Combining these three concepts, Bowyer plans to use a bath of monomer that will polymerize with an electric current, with the system programmed ‘using the reverse of the Spectra system.’ Ultimately, the liquid monomer would be inside a cylindrical bath with an array of electrodes spanning the whole area. A controller would be used to electrify the monomer enough to solidify it and turn into what would feasibly be like a 3D print—but produced by a machine with no moving parts and created in mere seconds.
“The entire machine could, of course, be printed in a conventional two-filament RepRap if one filament were conducting,” states Bowyer.
“Finally, and very speculatively, an even more ambitious possibility would be to move from organic chemistry to inorganic, and to replace the bath of monomer with an electrolyte such as copper acetate or copper sulphate. It might then be possible to cause the copper to precipitate at any location in 3D space if the pattern of electric currents through the liquid could be got right.”
RepRap Ltd. continues to be a dynamic force in 3D printing, behind projects such as sensory wearables and more, along with other users who continue to explore conductivity within 3D printing from creating supercapacitors to smart materials and sensors, as well as items like composites and more.
What do you think of this news? Let us know your thoughts! Join the discussion of this and other 3D printing topics at 3DPrintBoard.com.
[Source / Images: RepRapLtd.]Subscribe to Our Email Newsletter
Stay up-to-date on all the latest news from the 3D printing industry and receive information and offers from third party vendors.
Print Services
Upload your 3D Models and get them printed quickly and efficiently.
You May Also Like
3D Printing News Briefs, July 2, 2025: Copper Alloys, Defense Manufacturing, & More
We’re starting off with metals in today’s 3D Printing News Briefs, as Farsoon has unveiled a large-scale AM solution for copper alloys, and Meltio used its wire-laser metal solution to...
3DPOD 260: John Hart on VulcanForms, MIT, Desktop Metal and More
John Hart is a Professor at MIT; he´s also the director of the Laboratory for Manufacturing and Productivity as well as the director of the Center for Advanced Production Technologies....
3D Printing News Briefs, June 28, 2025: Defense Accelerator, Surgical Models, & More
In this weekend’s 3D Printing News Briefs, 3YOURMIND was selected to join an EU Defense Accelerator, and PTC has announced model-based definition (MBD) capabilities within Onshape. Finally, a study out...
EOS in India: AM’s Rising Star
EOS is doubling down on India. With a growing base of aerospace startups, new government policies, and a massive engineering workforce, India is quickly becoming one of the most important...