The dual pipette was designed and 3D printed to fulfill specific needs in the fluid piping process. These needs were previously met. However the process was time consuming. The combining of the two pipettes into one provides for a speedy and more efficient workflow when processing large amounts of medicine.The need was for two different functions:1.The ability to suction a single fluid mixture into separate reservoirs for individual ejection into separate containers.2.The ability to suction two different fluid mixtures separately and eject them into a single container together.
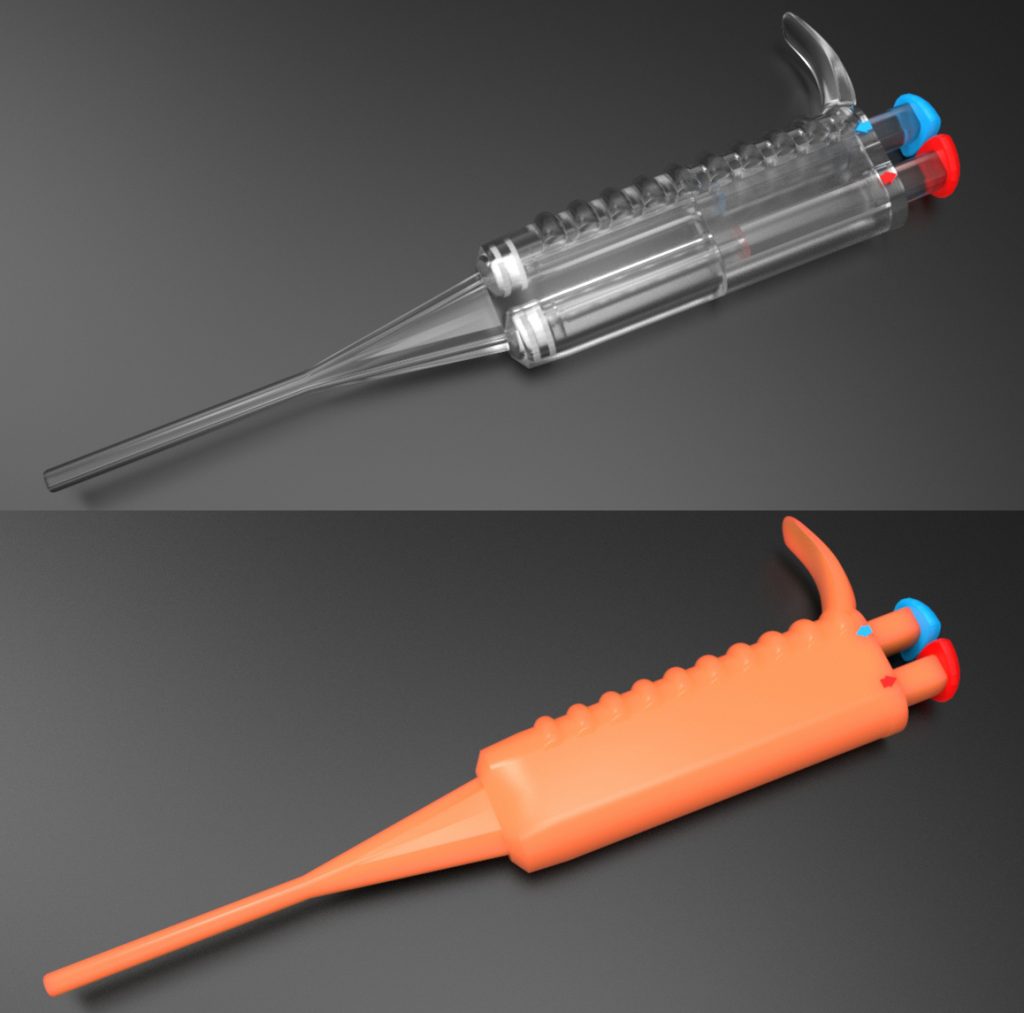
The dual pipette utilizes the same principles of pulsion and suction as a common syringe. The plungers are pulled up to create a vacuum and draw fluid up the spout and pressed down to eject fluid from the spout. The 3D printed plungers are fitted with normal rubber plunger tips to ensure an air-tight seal.
The pipette is a 3d printable, simplistic design. The primary difference is the ability to 3D print this pipette quickly. This means that we’re producing copies without the need for large-scale manufacturing. Reducing production time and availability to technicians by weeks.
A variety of materials have been experimented with. The most suitable 3D printed material for the device will be EnvisionTEC’s E-Shell 200. A liquid photopolymer designed for DLP 3D printers that produces strong, tough, water-resistant ABS like parts with high detail that are Class IIa biocompatible according to ISO 10993/Medical Product Law and are CE certified for use as hearing aid products, otoplastics, and medical devices.
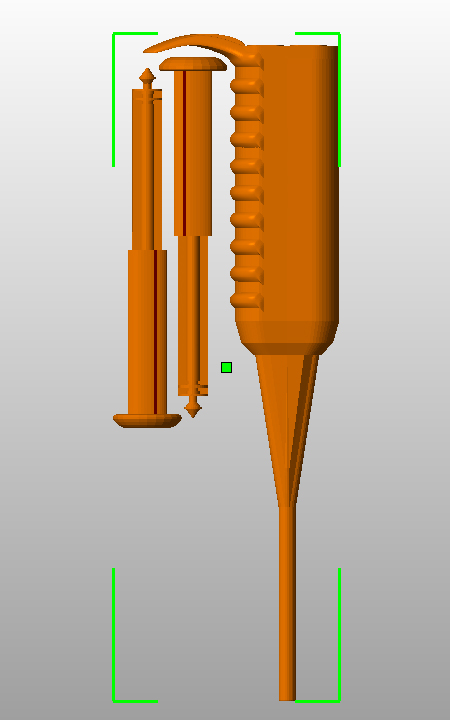
I utilized a variety of 3d CAD design software in the development process. The final design was created in Lightwave 3D. I find a mix of traditional CAD and Polygon based modeling software helps me produce better more ascetic product designs.
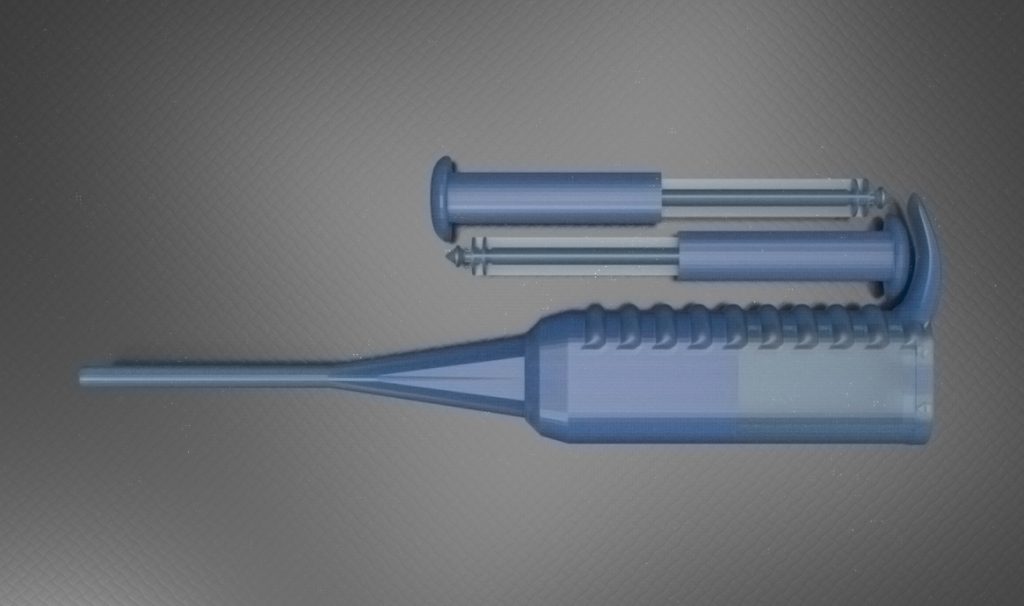
I enjoyed the creation of the dual pipette and consider it a good design because it has succeeded in fulfilling a specific need without otherwise costly measures. The dual pipette design aids in the development of medicines related to many medical treatments including Cerebral palsy.
Subscribe to Our Email Newsletter
Stay up-to-date on all the latest news from the 3D printing industry and receive information and offers from third party vendors.
Print Services
Upload your 3D Models and get them printed quickly and efficiently.
You May Also Like
Heating Up: 3D Systems’ Scott Green Discusses 3D Printing’s Potential in the Data Center Industry
The relentless rise of NVIDIA, the steadily increasing pledges of major private and public investments in national infrastructure projects around the world, and the general cultural obsession with AI have...
Formlabs Teams Up with DMG MORI in Japan
In late June, Nick Graham, Chief Revenue Officer at Formlabs, announced on LinkedIn that the company had partnered with DMG MORI, one of the world’s leading machine tool companies, to...
EOS in India: AM’s Rising Star
EOS is doubling down on India. With a growing base of aerospace startups, new government policies, and a massive engineering workforce, India is quickly becoming one of the most important...
3D Printing News Briefs, June 25, 2025: R&D Materials, 3D Printed Veneers, & More
In today’s 3D Printing News Briefs, 3DXTECH has launched a program that gives customers early access to experimental materials, and the first Lithoz CeraFab Multi 2M30 in the Czech Republic...