Four partners are collaborating on MultiPROmobil, an NRW Leitmarkt Project focused on the creation of innovative laser tools that are not only capable of handling multiple functions during production but may also have the potential to transform previous obstacles in designing electric vehicles. The project has been ongoing since November 2018, targeting small- to medium-sized companies.
Coordinated overall by the Fraunhofer Institute for Laser Technology ILT, other companies involved in the project are:
- Bergmann & Steffen GmbH
- CAE Innovative Engineering GmbH
- Laser Processing and Consulting Centre (LBBZ GmbH)
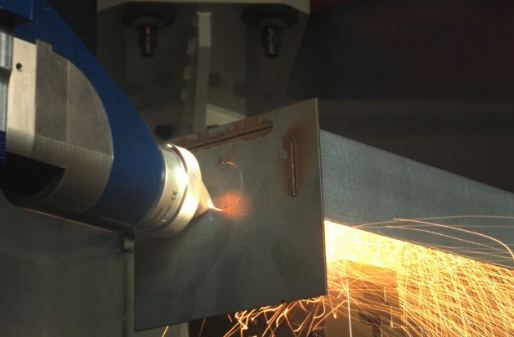
Multifunctional laser processing head that can already cut and weld innovative sheet metal assemblies. Now, additional additive manufacturing steps are added.
The MultiPROmobil partners have been immersed in creating a balance between flexibility and productivity in developing concepts that rely on hybrid construction with the lightweight parts that technology such as 3D printing, additive manufacturing, and robotics can deliver—along with complex electromobility. In their latest press release, the Fraunhofer ILT team points out that fast-changing products and fluctuation in batch size are required to bring these concepts to fruition.
“In volatile markets, laser technology combined with digitalization is a predestined enabler for cost-effective production,” explains Dr. Dirk Petring, group leader for Macro Joining and Cutting at Fraunhofer ILT and coordinator of the joint project “Multifunctional robot technology with a universal laser tool for separating, joining and additive manufacturing processes in semi-bionic lightweight e-mobility – MultiPROmobil.”
In developing a multi-functional laser processing head and robot for sheet metal production, the group is using a combi-head from Laserfact GmbH, meant to assist in cutting and welding functionality as well as ‘additively generating structures.’ A current goal in the project is to modify the combi-head for streamlined execution of three different processes at once during manufacturing, without having to switch out nozzles, and eventually the team will further develop semi-bionic vehicle structures with a laser—with plans to use several robots at once in ‘highly flexible manufacturing cells.’
“As the first application example, the triangular control arm of an electric vehicle will be optimally designed and cut, then welded and reinforced with additive structures in the multifunctional laser robot cell, all without a single tool change, states the latest press release from Fraunhofer ILT. “Of particular importance here is the flexibility of the clamping technology developed by Bergman & Steffen GmbH. In the future, several multifunctional robots are to be used in highly flexible manufacturing cells, depending on the size of the assembly and the required cycle time.”
Upon completion of the project, the partners expect to see the following benefits:
- Engineering efficiency increased
- Startup times reduced by around 30 percent
- Unit cost reduction
- Less resource consumption
“With agile, laser-based manufacturing, process chains for the production of sheet metal assemblies can be made very flexible and scalable so that they can be gradually introduced into electromobility applications,” explains Dr. Petring.
This project will run for three years. While coordination is provided by Fraunhofer ILT, funding is provided by the European Regional Development Fund (ERDF) and the State of North Rhine-Westphalia. Find out more about the MultiPROmobil project at the LASER World of PHOTONICS later this month.
Visitors can learn more about MultiPROmobil, and other current developments at the joint Fraunhofer booth 431, in Hall A2 at the event in Munich from June 24-27, 2019. If you just can’t wait that long, you can read about other projects we have followed regarding the progressive use of robotics, from research into applications for soft robotics to industrial uses for making furniture, as well as simulation programs in medicine and assistance in building space stations.
What do you think of this news? Let us know your thoughts! Join the discussion of this and other 3D printing topics at 3DPrintBoard.com.
[Source / Images: Fraunhofer Institute for Laser Technology ILT]Subscribe to Our Email Newsletter
Stay up-to-date on all the latest news from the 3D printing industry and receive information and offers from third party vendors.
Print Services
Upload your 3D Models and get them printed quickly and efficiently.
You May Also Like
Making Space: Stratasys Global Director of Aerospace & Defense Conrad Smith Discusses the Space Supply Chain Council
Of all the many verticals that have been significant additive manufacturing (AM) adopters, few have been more deeply influenced by the incorporation of AM into their workflows than the space...
EOS in India: AM’s Rising Star
EOS is doubling down on India. With a growing base of aerospace startups, new government policies, and a massive engineering workforce, India is quickly becoming one of the most important...
PostProcess CEO on Why the “Dirty Little Secret” of 3D Printing Can’t Be Ignored Anymore
If you’ve ever peeked behind the scenes of a 3D printing lab, you might have caught a glimpse of the post-processing room; maybe it’s messy, maybe hidden behind a mysterious...
Stratasys & Automation Intelligence Open North American Tooling Center in Flint
Stratasys has opened the North American Stratasys Tooling Center (NASTC) in Flint, Michigan, together with automation integrator and software firm Automation Intelligence. Stratasys wants the new center to help reduce...