Researchers from Poland’s Silesian University of Technology are getting in on the recycling action via 3D printing, and the title of their recently published paper certainly grabs the attention, whether you are a tech buff or not. ‘The Use of Shredded Car Windscreen Waste as Reinforcement of Thermoplastic Composites for 3D (FDM) Printing,’ authored by Piotr Olesik, Mateusz Koziol, Daria Konik, and Jakub Jała, outlines their recent experimentation with shredded windscreen glass in FDM 3D printing.
Recycling of glass laminate in the auto industry can be an expensive venture if it is required that polyvinyl butyral (PVB) be removed. Methods involving turning waste glass into ceramic pellets or using it in making silicon carbide have been investigated but also, but in the end, much of this automotive glass waste is just tossed into landfills. Because of that burden on the environment, the researchers stress the need to improve the process.
Considering the amount of filament going into 3D printers today as the technology has hit the mainstream with continued, accelerated momentum, finding more recycled materials to put into the hardware makes perfect sense. And while shredded car glass may not have been on the minds of many innovators yet, the authors see this automotive material as having surprising potential for creating strong filament—despite the minimal exploration of 3D printing with glass composites so far. The same goes for filaments made from low density polyethylene (LDPE), which is a cheap plastic with high chemical resistance and flexibility.
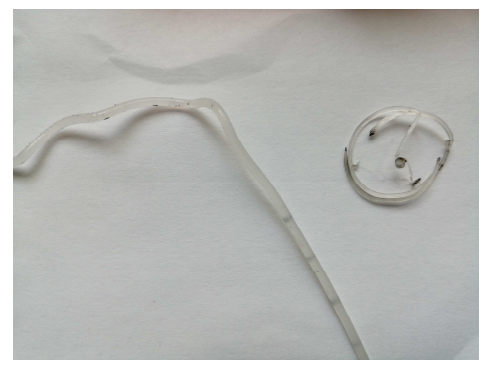
Behavior of neat LDPE print and filament during printing at rates above 1 mm/s – visibly deformed filament and unsuccessful vestigial printout
In beginning their study, the researchers were able to obtain glass powder from ground windscreen glass waste to create a composite for 3D printing filament by adding low density polyethylene (LDPE). The powder still contained the PVB (polyvinyl butyral), however, which is a necessary component to safety glass as a binding resin that adds strength but also some degree of flexibility. By keeping it in the mix they were also able to eliminate the added expense of removal.
The filament for FDM printing was created through extrusion winding, and open-air cooling—resulting in 1.45±0.05 mm material, and a reduction in filament strength as the glass content increased. The researchers set to work in assessing the potential of the materials, with printing temperature ‘selected experimentally’ during multiple trials (with the best print results set at 250°C and table temperature of 90°C).
“During printing, an unfavorable effect of filament bending was observed in the printer, below the supplying roller. This effect occurred during printing at a supply speed of more than 1 mm/s. Special additional printing tests with supply rates below 1 mm/s were carried out. This made the printing possible, and it showed the evident superiority of the composites over the neat LDPE.”
The researchers were able to solve the problem by stiffening the line between the rollers, but this required customized inserts. Overall, they noted LDPE printing as having potential in FDM 3D printing, but only at low printing speeds (with the inserts).
“The addition of shredded car windscreen glass slightly (but clearly) improves the behavior of the LDPE filament during the printing process, significantly improves the quality of the obtained printouts, and especially reduces shrinkage during cooling,” concluded the researchers. “The amount of 30% by weight of glass should be rather treated as the minimum amount to obtain the desired effects.”
“Further work on the use of LDPE in FDM printing should focus on the possibility of accelerating the printing rate by making design changes in printers (larger supply nozzles), or ensuring adequate stiffness of the material itself – e.g. by creating custom blends (with polypropylene or polystyrene) and, obviously, by producing composites with hard components.”
While much of the technology realm is wonderfully unpredictable, one thing is for certain, 3D printers around the world are getting a constant workout with an infinite supply of new materials for new ideas. Researchers in China have been inspired by origami to create 4D metamaterials, the Swiss have been experimenting with Multi-Metal Electrohydrodynamic Redox 3D Printing, and others are looking into fabrication with glass-ceramics at the nanoscale. Find out more now about the uses of recycled auto glass in 3D printing here. What do you think of this news? Let us know your thoughts! Join the discussion of this and other 3D printing topics at 3DPrintBoard.com.
[Source / Images:‘The Use of Shredded Car Windscreen Waste as Reinforcement of Thermoplastic Composites for 3D (FDM) Printing,’]Subscribe to Our Email Newsletter
Stay up-to-date on all the latest news from the 3D printing industry and receive information and offers from third party vendors.
Print Services
Upload your 3D Models and get them printed quickly and efficiently.
You May Also Like
U.S. Navy Lab Uses 3D Printing to Reduce Tooling Lead Time By Over 90%
The F-35 Lightning II Joint Program Office (JPO), responsible for life-cycle management of the key fifth-generation joint strike fighter (JSF) system used by the U.S., its allies, and its partners,...
Etsy Design Rule Change Reduces Selection of 3D Printed Goods
Online marketplace Etsy has implemented a rule change requiring all 3D printed goods on the site to be original designs. The update to the site’s Creativity Standards states, ¨Items produced using...
Honeywell Qualifies 6K Additive’s Nickel 718 for 3D Printed Aerospace & Defense Parts
6K Additive is renowned for manufacturing sustainable additive manufacturing (AM) powder, and offers a wide portfolio of premium metal and alloy powders that include titanium, copper, stainless steel, and nickel,...
MetalWorm Sells WAAM Systems to Research Institutes in Brazil and Malaysia
Turkish WAAM firm MetalWorm has sold a system in Malaysia and another in Brazil. This is an excellent example of a few emerging trends in additive. Firstly, WAAM was experimented...