Chinese researchers are exploring quality issues in 3D printing further, sharing their results in ‘Effects of nozzle-bed distance on the surface quality and mechanical properties of fused filament fabrication parts.’ Issues with distance between the nozzle and print bed have not been delved into extensively until now in relation to quality in FFF printing, but here we find that variances during the production process could have a significant effect on 3D printed prototypes and parts. As the authors point out, appropriate parameters are key to making good parts, with layer thickness usually being the most important setting to consider; however, there are little to no standards in place (as is true for much of 3D printing) for nozzle-bed distance (NBD), and resulting effects on layer thickness.
The researchers set out to examine how NBD affects not only surface quality but also mechanical properties of 3D printed parts. They attained samples fabricated on an FFF 3D printer, using ABS thermoplastic resins. The pellets, with a density of 1.03 g/cm3, were vacuum dried ahead of time.
“Based on pilot experimentations, the extrusion temperature was set at 175-190 °C, the extruder screw speed and traction speed were set at 10.5 rpm and 6.0 rpm, respectively. The diameter of obtained ABS filament was inspected in-situ by a laser diameter measuring instrument (LST-25) with a precision of ± 0.002 mm. The diameter of fabricated filaments was measured to be 1.75 ± 0.035 mm by 20 point along 5m length.”
Printing parameters were set as follows:
- Printing speed was fixed at 30 mm/s
- Object infill 100 percent
- Layer thickness .20 mm
- Nozzle diameter .40 mm
- Nozzle temperature and heat plate set at 230 °C and 100 °C
Further characterization resulted in tensile testing, bending tests, compression tests, and adhesion tests. Surface quality was a center focus in this research too:
“Surface accuracy was measured by Laser Scanning Confocal Microscope (VK-X200K, KEYENCE). The surface quality in this study is expressed with the altitude intercept, which is widely used in the industrial field. To ensure the accuracy of the experiment, the top surface of the samples was analyzed. For each test, five samples were prepared and tested, the obtained average altitude intercept value were presented in this report.”
The authors noted that NBD had a ‘profound effect’ on bonding and surface finish. Larger NBD showed valleys between filaments, indicating less bonding. At .10 mm, the samples demonstrated no gaps, but at .20, there were obvious ridges and valleys.
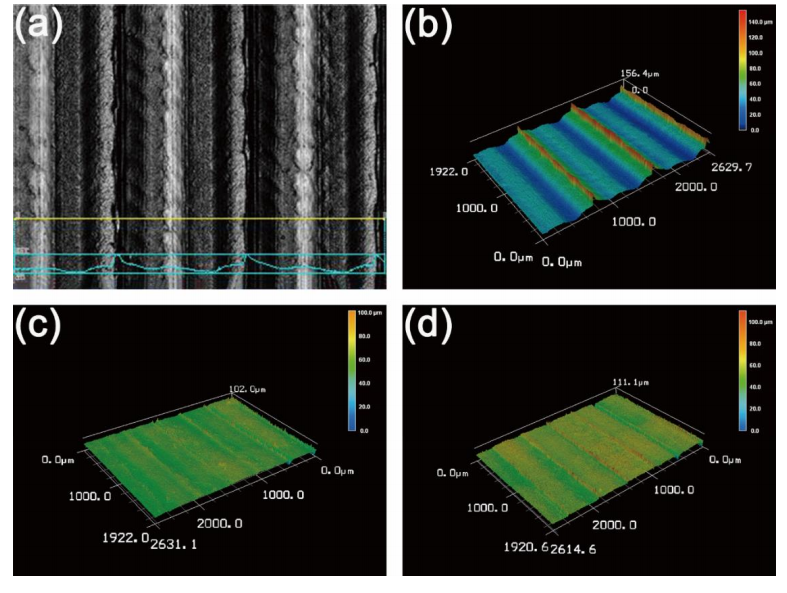
The surface profile of 3D printed samples. (b) (c) (d) 3D surface topography of the samples at NBD of 0.083 mm, 0.10 mm and 0.20 mm, respectively.
“The enhanced heat dissipation at large NBD decreased the force of interfacial bonding from 163.58 N to 100.64 N by 38.48% when NBD increased form 0.10 mm to 0.20 mm. With the nozzle-bed distance increasing, the heat dissipation mechanism also induces the decrease of part mechanical properties, such as tensile, compress and bending strength or modulus due to the porosity increase,” concluded the researchers. “Taking the surface quality and mechanical strength into account, the optimized NBD is found to be 0.10 mm in our study.”
“This research provides valuable insight into the inter-layer bonding process for researchers and 3D printing enthusiasts, helping them to make improved products.”

SEM micrographs of 3D printed samples printed from neat ABS; Cryo-fractured surfaces with NBD of (a) 0.10 mm and (b) 0.20 mm, tensile fractured surfaces with NBD of (c) 0.10 mm and (d) 0.20 mm.
Quality in 3D printing has become an area of intense research today as researchers not only want to experiment with a variety of different types of hardware, software, materials, and different applications, but they also want the end product to be structurally sound, and in many cases one that is functional and offers high performance. There are many details to be considered too, from emissions, to how prints are affected by acoustics, or more obvious issues like extrusion speed. Find out more about how nozzle bed distance affects parts here.
What do you think of this news? Let us know your thoughts! Join the discussion of this and other 3D printing topics at 3DPrintBoard.com.
[Source / Images: Effects of nozzle-bed distance on the surface quality and mechanical properties of fused filament fabrication parts]Subscribe to Our Email Newsletter
Stay up-to-date on all the latest news from the 3D printing industry and receive information and offers from third party vendors.
Print Services
Upload your 3D Models and get them printed quickly and efficiently.
You May Also Like
Havaianas Collaborates with Zellerfeld to Launch 3D Printed Flip-Flops
The shoe of the summer is undoubtedly the flip-flop. Easy on, easy off, your feet won’t get sweaty because there’s not much material, and they’re available in a veritable rainbow...
UCLA Researchers Develop 3D Printed Pen that May Help Detect Parkinson’s Disease
Diagnosing Parkinson’s disease is difficult. Often, early symptoms of the progressive neurological condition may be overlooked, or mistaken for signs of aging. Early diagnosis can help save lives and improve...
Printing Money Episode 30: Q1 2025 Public 3D Printing Earnings Review with Troy Jensen, Cantor Fitzgerald
Printing Money is back with Episode 30, and it’s that quarterly time, so we are happy and thankful to welcome back Troy Jensen (Managing Director, Cantor Fitzgerald) to review the...
Heating Up: 3D Systems’ Scott Green Discusses 3D Printing’s Potential in the Data Center Industry
The relentless rise of NVIDIA, the steadily increasing pledges of major private and public investments in national infrastructure projects around the world, and the general cultural obsession with AI have...