If your mind hasn’t been blown enough with 3D printing, bioprinting, and the potential for everything from 3D printed homes, cars, and even organs—get ready to be awed even further as researchers streamline multimaterial and multi-dimensional manufacturing for users around the world. Researchers J.J. Schwartz and A.J. Boydston detail their new technique further in ‘Multimaterial actinic spatial control 3D and 4D printing.’
The researchers explain that while multi-material 3D printing is already in use, with progressive hardware being touted as having the capabilities, it certainly isn’t easy. Leave it to a couple of brilliant chemists, however, to come up with a completely new idea that allows for an all-in-one process where nothing must be stopped or exchanged to switch over to a new material or color. Schwartz and Boydston point out that previously such an exercise was performed through hybrid manufacturing—using more than type of process for creating a product:
“For example, a molded component may be modified by some form of AM technique to give a hybrid part comprised of different materials, or an AM technique could be adapted to allow for incorporation of nontraditional components, such as electronics,” state the researchers.
After much study, the researchers discovered improved printability with epoxy-functionalized polyhedral oligomeric silsesquioxane (ePOSS) – to be used with resins such as IBoA-PEGDA/EPOX-ePOSS (IBoA-1), BA-HDDA/EPOX-ePOSS (BA-1) and HEA/EPOX-ePOSS (HEA-2).

a) Percent by weight of total monomers b) Weight percent based on weight of total monomers c) Stock HEA solution contains 9 wt % oligo(ethylene glycol) diacrylates as determined by GC-MS (40) d) Estimate reflects commercial composition of e) POSS, which is reported to contain 30% EPOX by weight e) Triarylsulfonium salts obtained commercially as a 50% solution (by wt) in propylene carbonate and used as-received.
Curing times overall were shorter in using white light and HEA/Irgacure, rather than UV light and EPOX/TAS combinations:
“To compensate for this difference, we screened varied ratios of the components and found that a 3:7 ratio of the acrylate- versus epoxide- monomers provided serviceable cure times (<120 s) using our custom visible and 365-nm UV projector sources. Incorporation of ePOSS in the IBoA-1 and HEA-2 system enabled a 1:1 ratio of radical to cationic components. Additionally, we used 0.4 wt % of the Irgacure 819 initiator versus 2.5–4 wt % of the TAS.”
“We anticipate that higher intensity of UV light or increased initiator efficiency could be successful in future iterations,” state the researchers.
The researchers go on to explain that in curing with UV light, they found that samples exhibited peak resonance comparable to acrylate and epoxide polymerization. And most importantly:
“These results signified the general ability to dictate the chemical compositions of parts printed from a single vat using simple wavelength control.”
They completed production by sending one series of images through a DLP projector, and the other into a customized UV projection system. Inspired by success, the researchers decided to plunge forward into making larger samples with more complex geometries, preparing 4-pillar specimens with the HEA-1 MASC formulation, and more ‘homogeneous specimens’ created with UV (or visible) light.
As they experimented further with MASC-DLP formulations, the researchers also began looking into 4D printing as specimens were able to swell and morph.
“As expected, specimens that were printed with visible light to give predominantly HEA or BA compositions swelled in aqueous and organic solvents, respectively (Supplementary Table 2). In contrast, specimens printed with UV light to incorporate EPOX showed considerably less volumetric swelling. Specimens printed with sequential UV and visible light resulted in intermediate swelling ratios.”
They experimented with how UV light would function in creating 4D samples, creating a star fish first using the HEA-1 MASC system, and examining the swelling process. The starfish arms curled consistently in several samples, but more so when they used the BA-1 MASC system, with the acrylate parts swelling more in toluene.
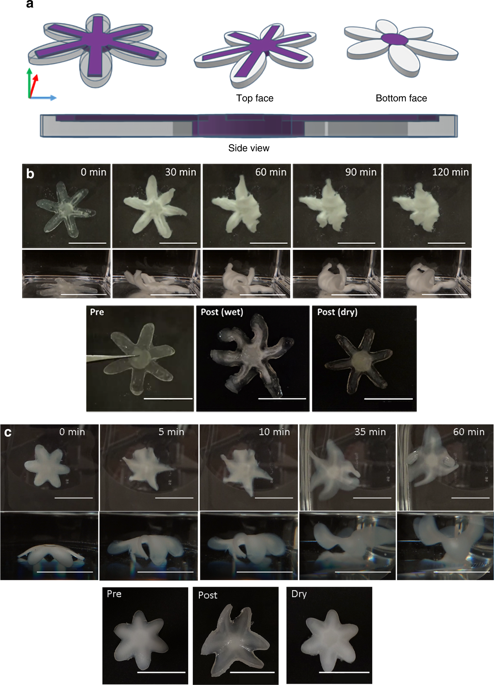
Time-lapse photos of swelling induced actuation in printed sea stars. a CAD models of multimaterial sea star. Tip-to-tip length = 38 mm, core diameter = 9 mm, inlaid beams within each arm = 13 mm. Purple corresponds to UV irradiation and white/transparent corresponds to visible light irradiation. b Swelling results of a sea star in water printed using the HEA-1 MASC formulation. Scale bars = 25 mm. c Swelling results of a sea star in toluene printed using the BA-1 MASC formulation. Scale bars = 25 mm
Further applications for this simplified multi-material 3D printing could include patient-specific medical devices like prosthetics, along with further progress in tissue engineering and the creation of 3D printed organs in the lab.
“This is a first step toward an expanded capability that we hope empowers designers, artists, engineers, and scientists to push the limits of AM materials combinations,” concluded the researchers. “Although these first demonstrations focused on a select combination of materials, expansion toward including the literal and figurative spectrum of photochemical reactivity could unlock numerous possibilities for multimaterial AM.”
What do you think of this news? Let us know your thoughts! Join the discussion of this and other 3D printing topics at 3DPrintBoard.com.
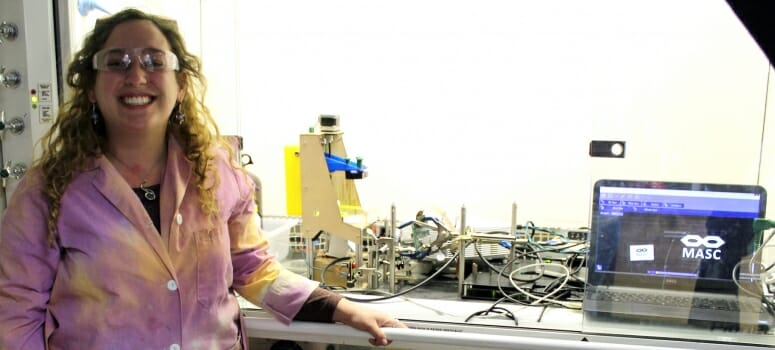
Graduate student Johanna Schwartz next to the multimaterial printing setup that she built. Photo courtesy of A.J. Boydston and Johanna Schwartz.
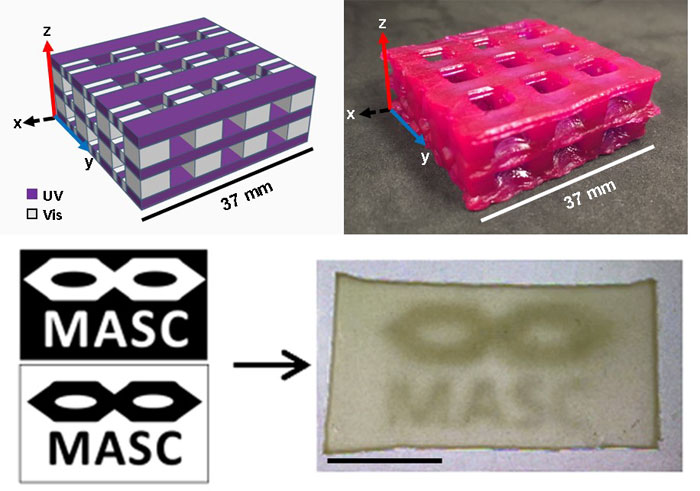
The top images show the digital design and its printed form. Purple corresponds to ultraviolet-cured stiff epoxide regions, whereas the gray regions are visible-light-cured acrylate regions that are soft and compliant. At the bottom, the logo for the 3D-printing group, MASC, is turned into a printed object composed of both stiff, opaque regions and soft, transparent regions. Photo courtesy of A.J. Boydston and Johanna Schwartz.
Subscribe to Our Email Newsletter
Stay up-to-date on all the latest news from the 3D printing industry and receive information and offers from third party vendors.
Print Services
Upload your 3D Models and get them printed quickly and efficiently.
You May Also Like
U.S. Navy Lab Uses 3D Printing to Reduce Tooling Lead Time By Over 90%
The F-35 Lightning II Joint Program Office (JPO), responsible for life-cycle management of the key fifth-generation joint strike fighter (JSF) system used by the U.S., its allies, and its partners,...
Etsy Design Rule Change Reduces Selection of 3D Printed Goods
Online marketplace Etsy has implemented a rule change requiring all 3D printed goods on the site to be original designs. The update to the site’s Creativity Standards states, ¨Items produced using...
Honeywell Qualifies 6K Additive’s Nickel 718 for 3D Printed Aerospace & Defense Parts
6K Additive is renowned for manufacturing sustainable additive manufacturing (AM) powder, and offers a wide portfolio of premium metal and alloy powders that include titanium, copper, stainless steel, and nickel,...
MetalWorm Sells WAAM Systems to Research Institutes in Brazil and Malaysia
Turkish WAAM firm MetalWorm has sold a system in Malaysia and another in Brazil. This is an excellent example of a few emerging trends in additive. Firstly, WAAM was experimented...