Advancements in Rhinoplasty: Will Your Nose Job be 3D Printed?
Researchers at Pohang University of Science and Technology (POSTECH) have created a new process for rhinoplasty—more commonly known as the procedure for performing nose jobs. Outlined in ‘Three-dimensional printing of a patient-specific engineered nasal cartilage for augmentative rhinoplasty,’ their method makes use of 3D printing an implant and then bioprinting stem cells to encourage the growth of nasal cartilage and a sustainable structure. Right now taking place in mice, such a procedure would take considerable time to percolate through to humans in a clinical setting. It is a promising path however to patient-specific 3D printed nose augmentations using biological materials. More importantly still, a similar procedure could, at some point in the future, prove potentially fruitful for ears or other cartilage in the body. This is a long ways off but the work is promising.
In exploring traditional rhinoplasty procedures, the researchers share with us two of the most typical types of surgery today, to include the autologous cartilage graft, and the synthetic nasal implant. The first is more organic in nature as surgeons take rib and ear cartilage to support the changes to the nasal region; however, it may be hard to harvest the necessary tissue from the patient, the surgery takes a long time, and may be not be successful overall. With artificial implants, there are risks of inflammation and infection, and ‘manual carving’ is required to shape the implant correctly to the patient’s nose. The research team points out that there is an art to such shaping with a sharp knife, and when done incorrectly or inaccurately, the shape may be off, and the implant may be unstable too.
Enter all the benefits of 3D printing—from better affordability to speed in production to a patient-specific fit—and it would seem that the future is already decided for such procedures. The use of hydrogels in creating scaffolds for developing tissue in the lab is no longer a novelty, but many have not demonstrated the levels of sustainability necessary or the ability to maintain the proper structure for procedures like rhinoplasty. The researcher’s new method includes customization of a nasal implant that is 3D printed and then injected with cells.

Computer-aided design and 3D printing of a patient-customized nasal implant. (a) The process of generating the custom design of the nasal implant model. The difference between the preoperative and postoperative nose geometrical shapes was calculated. A 3D solid model was then generated according to the geometric difference. Finally, an octahedral pattern architecture was designed in the nasal implant model, and a cover mold model was designed based on the nasal implant model. (b) Schematic elucidating the principle of fabricating a 3D construct by the pMSTL system. (c) Photographs of the fabricated PCL nasal implant and OrmoComp cover mold with the patient-specific design (scale bars = 5 mm).
The research was performed on mice, as the scientists implanted the cartilage within subcutaneous regions to evaluate success in the in vivo microenvironment.
“The results confirmed that the engineered nasal cartilage was well retained under in vivo conditions that surrounded it with physical stress,” stated the researchers. “A subcutaneous region was chosen for the implantation of the engineered nasal cartilages in mice to simulate the physical stresses occurring at a location beneath a skin layer.”
“The engineered nasal cartilage was subjected to various mechanical stresses, including skin tension and flexure due to the natural bending motion. During the implantation period, the appearance of the implanted site maintained the augmented shape, without noticeable deformation. After 12 weeks, the engineered nasal cartilages were retrieved, and no damage induced by the physical environment surrounded the implants was observed. In addition, the implants were covered with blood vessels and fully filled with neo-tissues.”
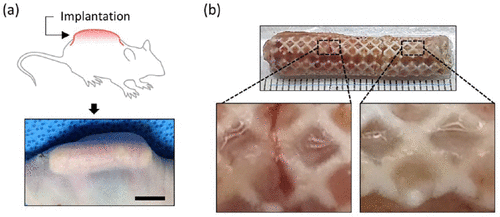
Subcutaneous implantation of the engineered nasal cartilage: (a) schematic and photograph of the construct implanted in a dorsal subcutaneous region (scale bar = 10 mm) and (b) gross image of the retrieved implant after 12 weeks post-implantation. The ruler is graduated in mm.
In discussing their findings further, the research team points out that in Asia, where rhinoplasty is popular, more than 16 percent of patients are currently unhappy with the results of surgery and may desire another procedure to fix the first one. Unhappiness with their appearance is a major issue for patients later, but worse, they may also suffer from rejection of the implant or serious infections.
The researchers are suggesting improved preoperative processes, especially in designing the shape of the implant with facial editing software and then converting it to files for modeling and 3D printing ‘without concern for the surgeon’s proficiency,’ after which the hydrogel is filled with the patient’s cells and injected into the 3D printed nasal implant. The researchers expect that the cells may transform into something like the autologous cartilage while sustaining the proper shape. They explain that the main benefit of the 3D printed implant is in ‘structural accuracy,’ with the hydrogel offering a suitable biochemical environment.
Overall, the entire rhinoplasty procedure should be shorter, more comfortable, and more streamlined for everyone involved.
“We expect that the developed process, which combines computer-aided design, three-dimensional printing, and tissue-derived hydrogel, would be beneficial in generating implants of other types of tissue,” conclude the researchers.
3D printing in medical implants has been ongoing for years now and research and development continue in refining patient-specific care, with 3D printing of organs and tissue as the goal for most scientists hoping to save lives as waiting lists are eliminated, along with patient rejection issues, infection, and more.
3D rhinoplasty models have been created previously to educate both patients and medical professionals, and we have followed discussions regarding the imminence of both ear and nose transplants via bioprinting; in fact, both 3D and 4D printing may play a part together in printing organs for transplant patients. Find out more about the advancements in rhinoplasty here.
What do you think of this news? Let us know your thoughts! Join the discussion of this and other 3D printing topics at 3DPrintBoard.com.

The histological analysis of the implanted engineered nasal cartilages. Representative images obtained after H&E and collagen II staining of the implants retrieved at (a) 6 and (b) 12 weeks (scale bars = 200 μm). The red dotted line and the star symbols indicate the PCL region.
Subscribe to Our Email Newsletter
Stay up-to-date on all the latest news from the 3D printing industry and receive information and offers from third party vendors.
Print Services
Upload your 3D Models and get them printed quickly and efficiently.
You May Also Like
3DPOD 252: What’s Really Happening in Bioprinting, with Mark Skylar-Scott, Stanford University
Mark Skylar-Scott is an experienced bioprinting researcher now working at one of the foremost bioprinting labs in the world at Stanford University. We talk about inexpensive desktop bioprinters and their...
Printing Money Episode 28: Recent M&A and More with Joris Peels, 3DPrint.com
Welcome to Episode 28 of Printing Money. For this one Danny is joined by our own, Joris Peels (Executive Editor, 3DPrint.com). This crossover-pod is indeed quite meta-level but it’s not...
3DPOD 251: 3D Printing for Football Helmets with Kodiak Brush, LIGHT Helmets
Kodiak Brush grew up playing football before working on crash testing. Sometimes someone’s career can seem like it is inexorably building up to one goal. And with Kodiak now making...
3DPOD 250: Dieter Schwarze, Nikon SLM Solutions
Dieter Schwarze is a true 3D printing icon. Here we get the twisting, arduous tale of Dieter’s journey into additive. Starting with inkjet, SLA and lots of other technologies, Dieter´s...